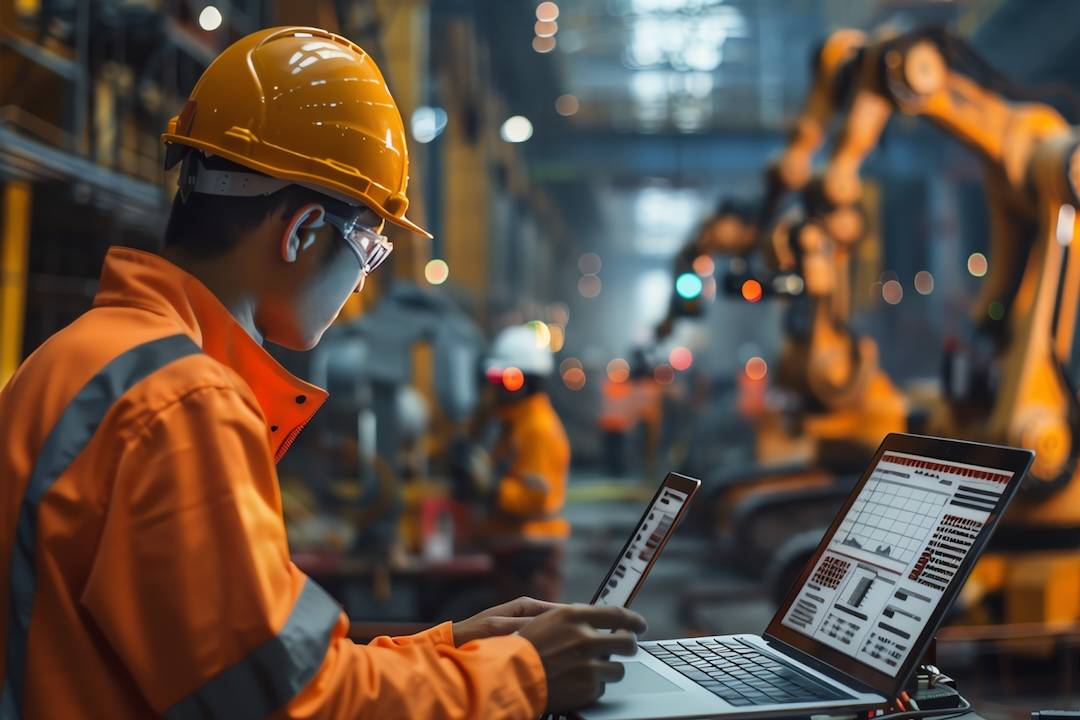
As artificial intelligence (AI) adoption surges across industries, maintenance teams face a pivotal moment. While 92% of companies report significant benefits from AI investments, the path to realizing that value isn't always straightforward. Let's explore what's driving AI adoption in maintenance and what it means for your operations in the coming year.
Why Traditional Maintenance Methods Won't Cut It in 2025
Maintenance teams are dealing with increasingly complex operations, and traditional approaches are struggling to keep pace. A tidal wave of data from multiple sources—work orders, IoT sensors, equipment readings, and maintenance histories—has arrived, making it challenging to extract meaningful insights. Critical information about improving equipment reliability and reducing downtime lies buried within this data, but it is difficult for people to extract. Driving this wave is the doubling of data collection across these sources in the last two years, creating an overwhelming flood of information.
Adding to this complexity, expert technicians are either in short supply or retiring, taking valuable undocumented knowledge with them. In the manufacturing sector alone, 28% of companies expect to lose a quarter of their workforce to retirement in the next five years. Without effective tools to capture and transfer this expertise, organizations risk losing critical operational knowledge.
These challenges are pushing maintenance teams to seek new solutions that enable them to work smarter, not harder, and finally put their mountain of data to productive use.
AI is already delivering results
Today's AI solutions are helping maintenance teams achieve what was previously impossible. Technicians are identifying equipment issues days—even weeks—before they cause downtime, dramatically reducing unexpected repairs and production losses.
The most successful teams are leveraging AI to digitize, centralize, and standardize their maintenance procedures and work orders across all technicians. This standardization drives consistent quality across facilities and shifts while creating a foundation for continuous improvement and scalable operations.
What sets modern AI solutions apart is their ability to capture not just textbook procedures but the real-world expertise of seasoned technicians—including their asset-specific knowledge and site-specific adaptations. This ensures that, as experienced workers retire, their invaluable insights remain accessible to the next generation of maintenance professionals.
What might arrive in 2025
Although it is impossible to predict the future, the next wave of AI innovations promises to transform maintenance operations in even more innovative ways. Imagine your technicians having access to:
- AI assistants that provide expert guidance on demand, as naturally as consulting an experienced colleague.
- Augmented Reality (AR) glasses that overlay visual instructions and step-by-step procedures directly onto equipment.
- Visual diagnostic tools that can identify current and potential equipment faults from a single image.
These capabilities aren't science fiction—they're already proven by adjacent industrial teams and software, like the use of AR within Manufacturing Execution Systems (MES). Some of your colleagues in other departments may already be using them. As these technologies become available for industrial maintenance, they'll enable your teams to work more confidently and efficiently.
Most significantly, AI will help bridge the growing skills gap in maintenance operations. While these are powerful tools, their true value lies in empowering new workers to perform at higher levels. Picture having an AI system that can deliver the insights of a veteran technician to all your staff—available 24/7, 365 days a year. This isn't about replacing human expertise; it's about amplifying it. By making deep technical knowledge more accessible, organizations can build resilience and maintain operational excellence in our increasingly digital world.
Want to learn more about how AI is reshaping maintenance and how to prepare your team for success? Download our comprehensive white paper that explores these trends in detail and provides practical guidance for implementation.
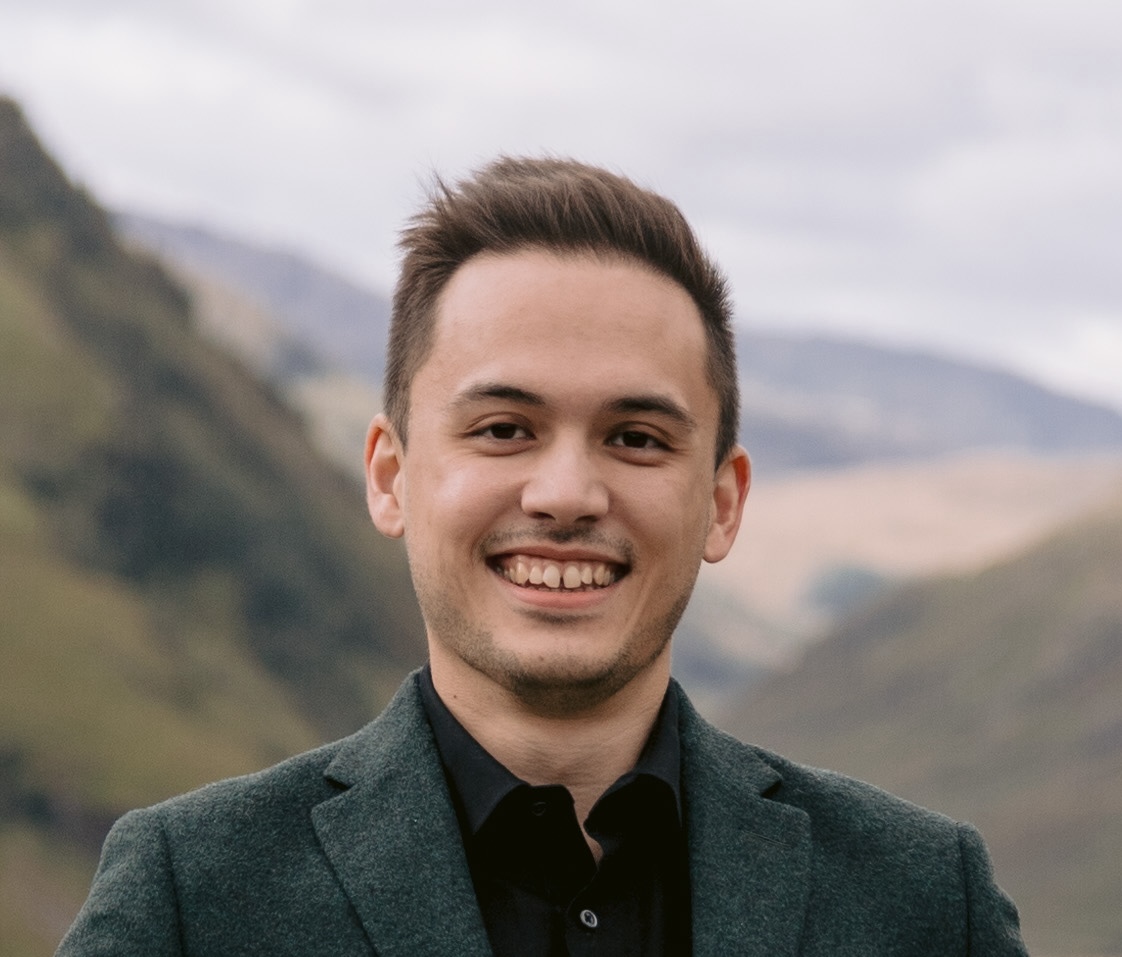
Andrew Benjamin is a Senior Product Marketing Manager at MaintainX with nearly a decade of experience marketing SaaS products. Of late, he’s guided organizations through digital transformation initiatives, and enabled them to harness actionable insights from their data using AI & ML models.