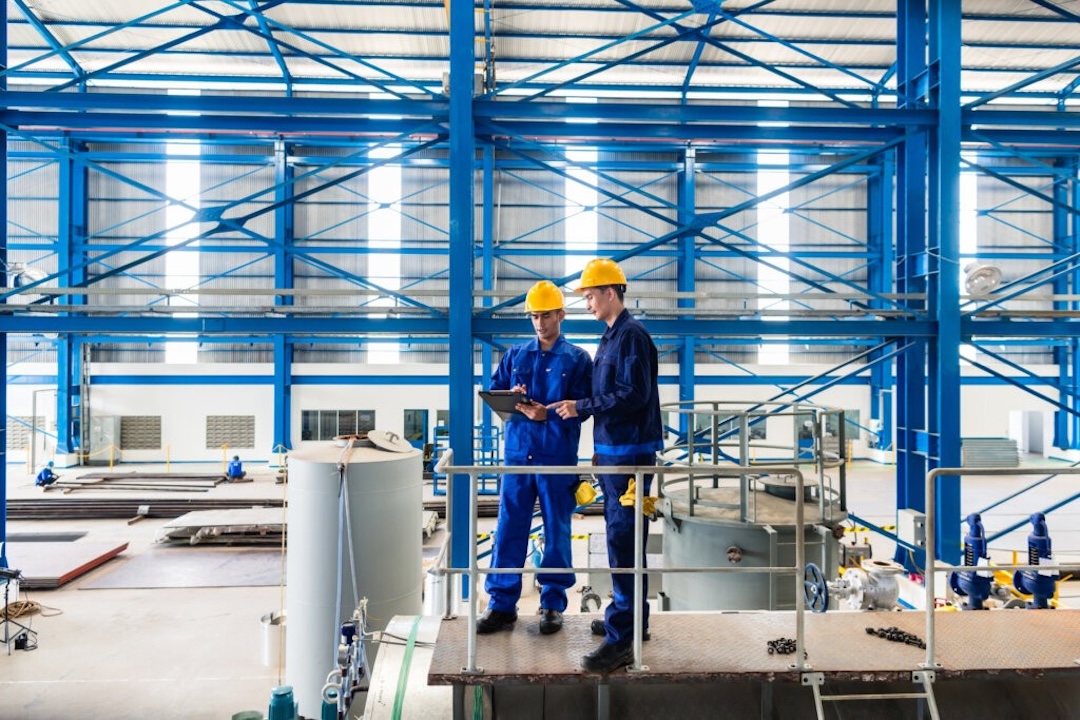
For years, manufacturers have been losing billions of dollars to outdated maintenance practices that do little to prevent unplanned downtime. Deloitte, for example, reports that unplanned downtime costs industrial manufacturers an estimated 50 billion dollars annually. As a result, manufacturers remain on the lookout for new innovations that can improve maintenance efficiency. Artificial Intelligence (AI) is one such example—which is why, according to recent American Manufacturing Resurgence surveys by Xometry, 80% of manufacturing CEOs plan to invest in AI over the next two years.
However, whether AI-powered or otherwise, using new technology is only one step. What makes the real difference is how well these tools work for the people who actually use them: the frontline workers. AI-enabled predictive maintenance, for example, can forecast equipment failure and enable dynamic maintenance planning, but this only works if the data powering the system is accurate. Without reliable data, your team will see unreliable predictions, leading to inconsistent results and wasted efforts.
That’s why it’s critical that teams collect robust, accurate, and consistent data to ensure they are prepared—not simply for predictive maintenance, but for other AI innovations on the horizon. Today’s data paves the way for tomorrow’s innovation, and every day you spend not capturing data reduces your ability to maximize future gains. You’ll be missing out on the opportunity to prepare for future AI use cases that can streamline your processes, boost efficiency, and maximize your productivity.
Creating a foundation for AI innovation
Tech solutions offer the most value when designed with technicians in mind, and AI tools are no different. You can organize all the training sessions you want, but the questions technicians ask themselves remain the same: How does this make my life easier? Does this tool fit naturally into my existing workflows? As a leader, your job is to find user-friendly software that makes sense within your team’s existing workflows so that your team will want to embrace it.
To ensure you create a valuable foundation for AI models, you need software that makes data capture easy for your team. With this data, the models can then learn your facility and equipment's ideal and non-ideal operating conditions. The models can also better learn your ideal maintenance procedures and go further to analyze this data. This analysis can help you identify potential problems and opportunities to improve.
What does capturing this data look like in practice? It means logging maintenance tasks in detail, monitoring inventory and equipment performance, tracking time and procedures used in repairs, and recording contextual environmental conditions for a site's most critical assets and processes. This can often be easier said than done, which is why many teams struggle with inaccurate data at critical times. Let’s consider some of the factors that compromise data quality and leave teams unprepared so you can proactively avoid them.
What leads to poor-quality data?
Problems with missing or inconsistent data aren’t a new or rare phenomenon. Consider an incident at Birch Bay Waterslides earlier when a man sustained an injury going down a slide. When people tried to understand what had happened, it turned out that inspection records were missing, hampering the investigation. This is only one way in which inaccessible or inaccurate data affects operations. Others include:
- Limited integration: If you’re aiming to take your maintenance work to the next level with third-party tools, you can’t do that with incomplete or inaccessible data.
- Difficulty in proving compliance: Searching through large amounts of paper records or spreadsheets in preparation for inspections is an inefficient use of time.
- Tribal knowledge: Without data stored in easily accessible digital systems, you’ll rely on specific individuals for knowledge about specific processes, slowing down your entire workflow.
No organization wants to run into these issues, and many implement digital systems to mitigate these problems. However, many teams can still run into issues due to the following factors:
Lack of mobile access
Because technicians work on the floor, not having the systems with them slows down the data capture process. If they only have access to the desktop system, they’ll capture their inputs using pen-and-paper and then manually add them to the system after they return to their desks. This cumbersome process leads to delays and inaccuracies.
Unintuitive processes
Some industrial software systems have neglected the needs of mobile, deskless workers, whose input is crucial for success. As a result, their workflows are too complicated for frontline workers trying to capture information as quickly as possible. This slows adoption or causes technicians to default to paper or manual-dependent processes.
Lack of comprehensiveness
Even when some systems appear to work just fine, they may only be designed to capture some of the relevant data. Users will end up recording only the data that the system prompts them to. In practice, you’ll end up with a system that records all downtime events, but does not include machine conditions just before or in the weeks leading up to the event, preventing condition-based maintenance analysis.
How can you improve data management?
The great thing is that nobody has to follow the traditional path. Even teams still using pen-and-paper, email, or spreadsheets to organize their maintenance can skip the desktop-only systems and move directly to mobile computerized maintenance management systems (CMMS).
In the past, many organizations had to build in-house solutions, which not only cost a lot but also required continuous work to maintain. Today, several CMMS options exist in the market, offering out-of-the-box solutions like centralized data management, data visualization, pre-built integrations, templates, and robust collaboration tools. These tools help to ensure your teams can capture as much valuable data as they can as quickly as possible.
This doesn't suggest that a CMMS is a magic pill that requires no further effort today. If wrongly implemented, a CMMS can make work even more complicated for frontline technicians. Workers will struggle with too many disconnected and unprioritized alerts, alarms, and work orders across multiple apps and documentation sources, with complex interfaces and long load times. This leaves them with a simple choice: do the work and move on to the next task, or spend 30 minutes figuring out how to accurately record their work, thereby reducing wrench time.
However, as long as you’re using software that makes sense for your team, everything will be a breeze. You’ll have access to intuitive interfaces and workflows, centralized work order management, and streamlined data practices. You’ll see significant savings in downtime, better resource planning, improved safety, and more. But don’t just take our word for it.
A first-hand example
Building materials producer Titan America partnered with MaintainX to establish a reliability-centered maintenance (RCM) program in its Florida plant and drive measurable O&M savings.
A key requirement for Titan was user experience. MaintainX’s intuitive system enabled Titan America’s technicians to easily follow digitized inspection checklists from their mobile devices, enter work order data in real-time, and escalate issues to supervisors via instant messaging within seconds. MaintainX’s ease of use and accessibility helped drive adoption and increase data capture.
In less than a year, Titan America eliminated over 30% of unplanned downtime, but it didn’t stop there: the team is also building a data foundation for AI-enabled predictive maintenance.
Simply put, teams need to act now. Just as proactively adopting preventive maintenance strategies is your best bet to ensure your assets stay in good working condition, you need to be proactive in preparing for innovation. To build AI models that understand your organization’s maintenance needs, you need to start using the best digital maintenance solutions today to enable more efficient solutions for the future.
Step into the future with MaintainX
If you’re looking for a partner on your digital transformation journey, look no further than MaintainX. MaintainX provides robust tools to capture, manage, and access data that is accurate, reliable, and consistent. MaintainX strengthens data capture with tools like:
- Pre-filled templates, required fields, and signatures to ensure technicians capture the correct data every time
- Photos, videos, and voice clips that enable technicians to add useful context to work orders
- Anomaly detection to prevent errors when recording data
Beyond these, however, MaintainX has already made great strides with AI innovation, providing tools to streamline your operations today. Take advantage of:
- AI-powered Procedure Generation to create checklists and SOPs faster
- AI-powered Voice Memos to share more information easier
- AI-powered Smart Time Estimates to plan and schedule tasks
To learn more, book a demo with MaintainX today.
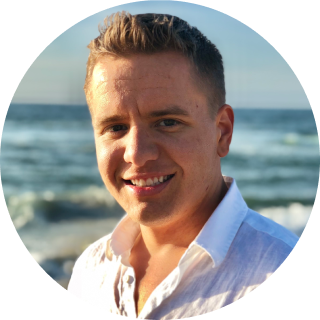
Nick Haase is a co-founder for MaintainX and is responsible for designing and leading the go-to-market strategies. He is a subject-matter expert in emerging CMMS technologies.