.jpeg)
You’re not imagining it: AI really is everywhere, and the speed of its adoption is unlike anything we’ve seen before. Think of the wave of digital transformation from 2000 to the present—now compress that timescale into just a few years. That’s how fast AI is moving.
It’s no surprise, then, that you can’t open a trade publication without seeing a headline about AI. In 2024 alone, McKinsey reported a dramatic jump in adoption: 72% of organizations were on board, compared to 55% just a year earlier. That number will only keep climbing.
But beyond the numbers, there’s a very clear message: manufacturers need to understand and embrace AI if they want to stay competitive. The question is, how can you leverage AI to improve your operations without simply chasing hype or creating fancy proofs-of-concept that don’t deliver real returns?
Below, I’ll share my 2025 predictions for AI in manufacturing and offer insights into the practical steps teams can take to see immediate (and lasting) results.
Prediction #1: Industries that digitized earlier will springboard ahead
I often tell people: the best time to start capturing frontline data was 20 years ago. A strong historical data foundation is what propels today’s manufacturing teams into the most useful AI applications.
Why? Because AI isn’t just about algorithms; it’s about feeding those algorithms accurate, contextual data. A recent Deloitte survey found that 91% of AI projects fail because of one (or more) of the following issues:
- Data collection and quality
- A lack of worker experience and expertise
- Infrastructure limitations
I see many manufacturers run out and buy off-the-shelf AI products, hoping for quick wins. The output often looks impressive at first glance—but when you look under the hood, the insights either aren’t actionable or they’re completely missing the mark. Meanwhile, teams that have spent years collecting high-quality frontline data have been quietly but steadily building their AI “springboard.” They don’t have these data problems; they’re already seeing tangible ROI right now.
Of course, if you’re reading this and wishing you’d started capturing data two decades ago, know that all is not lost. The second-best time to start is right now. So whether you’re setting up your first mobile CMMS or exploring advanced sensor integrations, focus on building that data foundation. AI tools will come and go, but data remains the common denominator that ensures successful—and sustainable—AI initiatives.
Prediction #2: Getting the basics right will outmatch fancy algorithms every time
I’ve written about what I call The AI Trap. In a nutshell, it’s the all-too-common mistake manufacturing teams make when they rush to adopt AI—often due to fear of missing out—without getting their foundational data and processes in order. They treat AI like an all-knowing, all-seeing magic bullet that can fix everything, which of course it can’t.
Time and again, I’ve seen teams fall into this trap. They end up with AI pilots that look good on a PowerPoint slide but offer no real-world value. This mistake is avoidable if you stay laser-focused on two things:
1. Use AI to drive immediate, practical benefits.
This often starts with seemingly straightforward goals: automating work orders, spotting maintenance issues earlier, or making your frontline teams more efficient. These small wins build momentum and help prove the value of AI to leadership and operators alike.
2. Build the data foundation for the future.
No AI model—no matter how sophisticated—can deliver consistent value without clean, structured data. Too many organizations overlook the “unsexy” work of digitizing and centralizing day-to-day operations. But trust me, it’s essential. The data you collect today will ensure you can maximize every AI breakthrough that comes next.
I’m regularly surprised by how many manufacturers I speak with who still rely on pen-and-paper or siloed spreadsheets for core processes. Yes, digitizing can be daunting, but that investment is what separates AI hype from AI results. In 2025, the teams that obsess over “getting the basics right” will leave the fancy, off-target models in the dust.
Prediction #3: The best decision-making will come from pairing human intelligence and machine data
We often think of AI in purely technological terms—sensors, analytics dashboards, and networked machines. But human expertise is what truly unlocks AI’s potential.
Here’s a simple illustration I offered in a recent article for SmartIndustry:
- A sensor might say a machine is running too hot.
- An experienced operator might note that this machine has always run warmer on humid days and doesn’t need immediate intervention.
In fact, Deloitte’s 2025 Manufacturing Industry Outlook calls out data quality, contextualization, and validation as some of the biggest obstacles to AI implementation. To overcome those, you need people—knowledgeable technicians, engineers, and frontline workers—who can interpret, contextualize, and improve machine-generated outputs.
Real-world examples might include:
- Comprehensive, context-rich maintenance records capturing what actually happened on the floor
- Observations from the line about humidity, temperature, or even shift variances that might affect machine performance
- Quick handoff notes that describe not just the status of a machine, but the quirks the next shift should look out for
Ignore these details, and you’ll end up with an AI that’s only half-informed. Embrace them, and you’ll have a robust foundation for both daily operations and future predictive capabilities.
The future of AI in manufacturing is built one piece at a time
It’s easy to get lost in speculation when thinking about the future of AI. But as we speed toward 2025, here’s my best advice:
1) Identify pragmatic use cases for AI today.
- This might mean standardizing maintenance work across sites using an AI assistant that creates digital procedures in minutes.
- Or it might mean using work order data to generate AI-powered estimates for future jobs
2) Focus on building your data foundation at the frontline.
- If you’re capturing work orders with pen and paper, enabling your frontline workers with a mobile CMMS for real-time data capture will be revolutionary.
- If you’ve already done that for years, the next step could be implementing sensors or advanced analytics to move toward predictive maintenance.
No matter where you are in your journey, 2025 will be the year that separates true AI-driven manufacturing from the also-rans. The compressed wave of AI adoption is here—and moving faster than anything we saw in the early-2000s digital transformation. The best way to make sure you’re on the right side of that wave is to start collecting the right data, avoid “The AI Trap” by focusing on fundamentals, and, above all, never forget the value of human insight.
Because while AI is powerful, it’s the combination of human intelligence and machine data that will carry manufacturing forward into 2025—and beyond. So roll up your sleeves and get started. We’ve got a future to build.
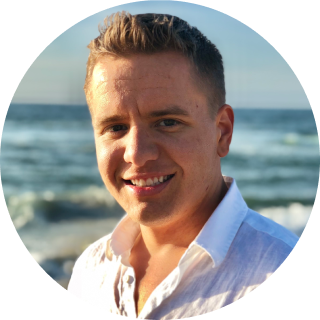
Nick Haase is a co-founder for MaintainX and is responsible for designing and leading the go-to-market strategies. He is a subject-matter expert in emerging CMMS technologies.