Reliability-Centered Maintenance (RCM) is a corporate-level preventative maintenance strategy designed to optimize maintenance programs by establishing safe minimum levels of equipment upkeep.
RCM emphasizes matching individual assets with the maintenance techniques most likely to deliver cost-effective outcomes. The successful implementation of an RCM process enhances reliability, equipment uptime, and company savings.
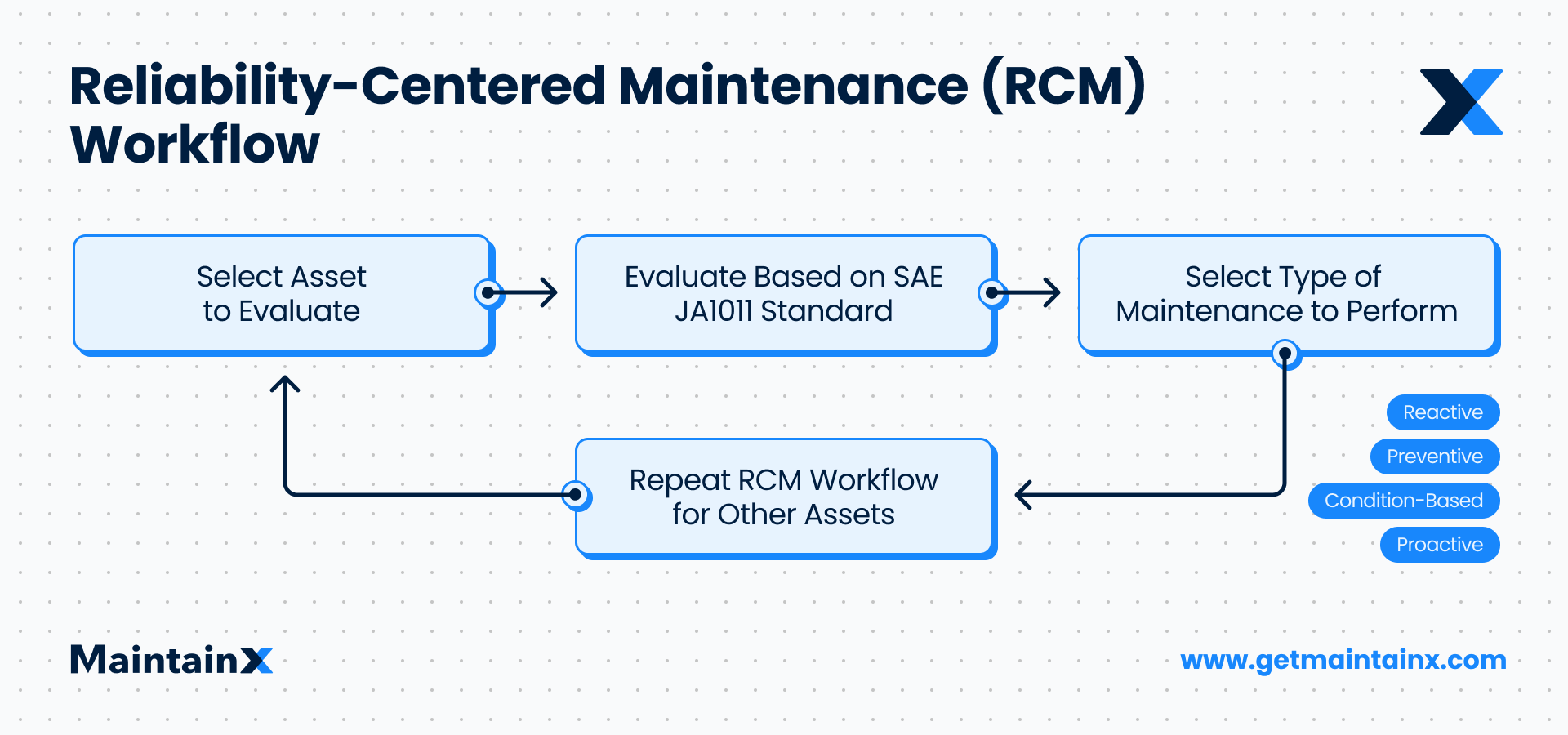
What is reliability-centered maintenance?
Reliability-Centered Maintenance (RCM) is a preventive maintenance approach that focuses on optimizing the reliability of a system or process. At its core, RCM seeks to identify potential failure modes and ways to prevent them before they occur. The goal is to proactively assess the risk associated with any potential failure so maintenance teams can take corrective measures quickly and effectively.
What is the purpose of RCM?
The primary objective of RCM is best understood by analyzing its root words:
Reliability: The quality of performing consistently well.
Maintenance: Ensuring assets continue to function as desired.
Essentially, Reliability-Centered Maintenance (RCM) provides a roadmap to analyze and act upon the root causes of equipment failures—technology, culture, design, and maintenance strategy inefficiencies—in pursuit of affordable asset reliability.
Of course, downtime is inevitable when working with complex pieces of machinery. However, top-tier organizations use RCM to prevent sudden breakdowns that require laborious maintenance, costly outsourcing and lost production time.
Why RCM is important for operations
The importance of RCM is twofold–it helps optimize an organization’s operations by preventing failures from occurring in the first place and reducing unplanned maintenance costs when failures occur.
Through detailed root cause analysis and failure mode identification, RCM enables organizations to develop robust, proactive maintenance plans that address all relevant failure modes for each piece of equipment. This allows for more accurate budgeting for planned activities such as scheduled maintenance, inspections, and testing. Furthermore, using data from past repairs and replacements along with aging equipment models helps form an accurate cost estimate for future repairs or replacements ahead of time.
In addition to cost savings, RCM improves safety by addressing known risks up-front and ensuring teams take corrective measures before machines break down. By monitoring key performance indicators (KPIs), organizations can detect emerging trends early on, allowing them to take corrective action before a failure occurs; this leads to improved reliability and reduced downtime resulting in more significant productivity gains over time. With these benefits in mind, it’s easy to see why reliability-centered maintenance has become a necessary component of effective asset management plans in today’s ever-changing business environment.
The principles of reliability-centered maintenance
The RCM paradigm argues that the less maintenance you perform on an asset, the better. Only perform maintenance when absolutely necessary or when the benefits outweigh the risks and costs. RCM is based on four key objectives:
- Preserve system functions.
- Identify failure modes that can affect system functions.
- Prioritize identified failure modes according to risk and cost projections.
- Select the most effective tasks to control failure modes.
How is RCM different from standard maintenance programs?
RCM recognizes that all facility assets are not of equal importance—from both safety and process standpoints. The decision-making framework seeks to best match equipment needs with available resources for cost-effective reliability.
Translation: Some assets are more integral to daily production goals than others, and assets don’t always fail for the same reasons. Thus, RCM provides a management roadmap for prioritizing, optimizing, and assigning maintenance activities.
According to the O&M Best Practices Guide, Release 3.0, top-performing facilities, on average, divide their maintenance efforts into the following categories based on RCM:
- <10% Reactive Maintenance
- 25% to 35% Preventive Maintenance
- 45% to 55% Predictive Maintenance
Because RCM emphasizes newer predictive maintenance technologies—such as infrared, acoustic (partial discharge and airborne ultrasonic), corona detection, vibration analysis, sound-level measurements, and oil analysis—the process isn’t financially feasible for small-to-medium-sized companies. However, RCM has earned a “government seal of approval.”
United Airlines executives developed the process before catching the attention of the U.S. Department of Defense in 1978. Today the maintenance process is practiced by hundreds of industrial and service organizations around the world.
The requirements of reliability-centered maintenance
Organizational leaders should outline their RCM goals by considering management availability, accessible technologies, and budgetary resources. This somewhat time-consuming process carefully analyzes individual asset management scenarios before assigning corresponding maintenance tasks.
Below are the evaluation criteria for RCM, as described by the Society of Automotive Engineers (SAE). Assess each piece of equipment, organized by phase, by asking:
Decision
- What functions does it perform, and what are the desired performance standards?
- In what ways could the asset fail to fulfill its functions?
- What are the causes of each possible failure scenario?
Analysis
- What happens when each type of failure occurs?
- What consequences would we suffer as a result of each failure?
- How could we predict or prevent each potential failure?
Action
- What should we do if we can’t determine a suitable proactive task?
The final component of RCM is choosing and scheduling appropriate maintenance tasks. A CMMS can schedule, assign, and oversee work orders. As expected, different techniques are suitable for different asset situations. Some machinery may require proactive tasks, including preventive and predictive maintenance. Conversely, reactive maintenance may be the most financially prudent course of action for other low-importance pieces.
Advantages and disadvantages of reliability-centered maintenance
Successfully implementing RCM benefits organizations that can afford it. The framework takes the guesswork out of maintenance prioritization and helps organizations maintain assets in a consistent, structured, and cost-effective manner.
Because RCM heavily relies on predictive maintenance (PdM) technologies, its program advantages and disadvantages mirror those of it. However, RCM allows facilities to match resources to equipment needs more closely while improving reliability and decreasing cost—more than any singular PdM strategy.
RCM advantages
The advantages of reliability-centered maintenance include:
- Cost effectiveness. RCM helps reduce costs by minimizing unnecessary routine maintenance tasks. When combined with preventive maintenance, RCM has been shown to reduce workloads by 70 percent.
- Better teamwork. RCM takes a group approach to maintenance tasks. Communication and cooperation among departments and teams improve when everyone is involved in problem analysis and decision-making.
- Improved asset performance. It also eliminates unnecessary overhauls and, therefore, reduces shutdowns. RCM also helps to diagnose failure more quickly.
- Improved employee motivation. When employees are involved in the application of RCM, they get a better understanding of the assets in their operating contexts. This motivates them to take ownership of maintenance problems and solutions.
- Better safety and environmental integrity. RCM seeks to understand the implications of every failure mode and takes proactive steps to prevent them. Besides limiting failures, the maintenance prioritization process promotes the availability of necessary protective devices.
Here’s an example of RCM’s benefits: The NASA Marshall Flight Center saved more than $300,000 in costs by implementing an RCM strategy that reduced maintenance costs, improved workplace safety, and extended the lifespan of aging assets. The program also enabled the Center to minimize its energy consumption and reduce its environmental impact.
RCM disadvantages
RCM also has its drawbacks. The initial costs of implementing RCM are high. Performing RCM analysis requires maintenence teams to invest significant time, finances, and resources to get started. ROI may be slower than executives prefer.
The second major disadvantage of RCM is that it simultaneously incorporates all of the other types of maintenance strategies, including some of their drawbacks.
For instance, say you choose a run-to-failure approach for a given asset. You simultaneously run the risk of an unplanned failure. For this reason, RCM is sometimes seen as expensive compared to running predictive or preventive maintenance programs alone. However, most experts agree that RCM is more cost-effective in the long run.
How to run a reliability-centered maintenance program
The best way to implement an RCM program–which can be daunting–is to take a logical approach and handle one step at a time. While there are different ways of implementing RCM, these eight basic steps are a great place to start:
Step 1: Select an asset RCM analysis
Choose an asset on which to perform the RCM analysis. What criteria should you use to select the asset? Some factors to consider include how critical the asset is to operations, its repair costs in the past, and its previous preventive maintenance costs.
Step 2: Outline the functions of the system for the selected asset
It’s important to know the functions of the system, including its inputs and outputs, no matter how small. This helps to define the requirements for the maintenance of the system or equipment. For example, the inputs of a conveyor belt are the goods and the mechanical energy that powers the belt.
Step 3: Define the system or equipment failure modes
Understand the different ways in which the system can fail. For example, the conveyor belt may not transport the goods fast enough or completely fail to transport them from one end to the other.
This helps to prioritize maintenance activities based on the potential impact of each failure on the overall performance of the system or equipment. Functional failure is the inability of an asset or system to meet acceptable standards of performance.
Failure Mode and Effects Analysis (FMEA) is the process of assessing the potential causes and impacts of equipment failures. It’s a proactive, data-driven, and team-oriented method for identifying the relative effect of various failure modes on productivity goals.
FMEA is also referred to as failure modes, effects, and criticality analysis (FMECA) and potential failure modes and effects analysis.
Step 4: Assess the consequences of failure
What will happen in the event of a failure? Asset failure can result in safety concerns and poor business performance. It also can affect other equipment. Plant operators, equipment experts, and technicians should work together to identify the root causes of individual asset failure. This process helps determine how to prioritize tasks.
You can organize this process using many methods, including:
- Failure Modes and Effects Analysis (FMEA): This is a method of evaluating the impact of a failure by identifying where and how a process might fail. For example, what would make the conveyor belt slow down or stop working?
- Failure, Mode, Effect, and Criticality Analysis (FMECA): This is the same as FMEA. However, it goes one step further and creates linkages between failure modes, the effects, and the causes of failure.
- Hazard and Operability Studies (HAZOPS): HAZOPS is a systematic examination of processes to identify issues that may result in risks for your personnel and assets. In most cases, it guides the review of standard operating procedures.
- Fault Tree Analysis (FTA): The FTA is a graphic tool used to examine the cause of system-level failure. It employs a top-down deductive analysis of failure.
- Risk-based Inspection (RBI): RBI is a decision-making process used to optimize inspection plans. It’s primarily used to examine industrial equipment, such as piping, pressure vessels, and heat exchangers.
Always prioritize the more critical failure modes for additional analysis. Retain the failure modes that can occur in real-life operating environments.
Step 5: Determine a maintenance strategy for each failure mode
The probability of each failure mode occurring should be assessed, taking into account factors such as the system’s operating environment, maintenance history, and the reliability of its components.
Step 6: Implement the strategy and perform regular reviews
For your RCM program to be effective, you need to implement the maintenance recommendations identified in Step 5. After implementation, regular reviews will help to improve the systems and performance. Whichever maintenance strategy you decide to use for each asset, you will be able to generate additional data that will improve your systems.
Step 7: Determine a maintenance strategy for each failure mode
At this point, select a maintenance strategy for each critical failure mode. It should be both economically and technically feasible. You can use condition-based maintenance (CBM), preventive maintenance, corrective maintenance, or predictive maintenance (PdM). If you are unable to implement a given strategy for a particular failure mode, consider redesigning the system to modify or eliminate the failure mode completely in all your maintenance planning.
Non-critical failure modes can be considered for a run-to-failure maintenance strategy. At this stage, you are looking to answer the question, “What is the principle of an effective maintenance strategy?”
Step 8: Implement the strategy and perform regular reviews
For your RCM program to be effective, you need to implement the maintenance recommendations identified in Step 5. After implementation, regular reviews will help to improve the systems and performance. Whichever maintenance strategy you decide to use for each asset, you will be able to generate additional data that will improve your systems.
Preventive maintenance strategies to use with RCM
Reliability-centered maintenance (RCM) is a strategy that aims to optimize the maintenance of a system or equipment to ensure its reliability and performance. One of the most effective preventive maintenance strategies used with reliability-centered maintenance (RCM) is implementing a preventative maintenance program. This program can involve various activities designed to help identify and anticipate potential problems with equipment or systems before they occur. Thus RCM reduces or eliminates the need for corrective action once a problem has arisen.
Overall, preventive maintenance is essential to any well-rounded reliability-centered maintenance strategy. It enables businesses to catch problems early on before they become major issues requiring costly repairs or replacements. By having regularly scheduled inspections along with predictive maintenance practices such as thermography scans and ultrasound readings when appropriate, organizations can avoid expensive repair costs. More importantly, it ensures high levels of safety at all times for those operating their systems daily.
You can use a range of preventive maintenance strategies within an RCM framework, including the following:
1. Periodic maintenance
Also known as time-based maintenance, this type of preventive maintenance is based on a predetermined schedule. Teams perform maintenance at regular intervals, regardless of the condition of the equipment. Time-based maintenance is typically used for simple, low-risk systems or equipment with a predictable failure rate.
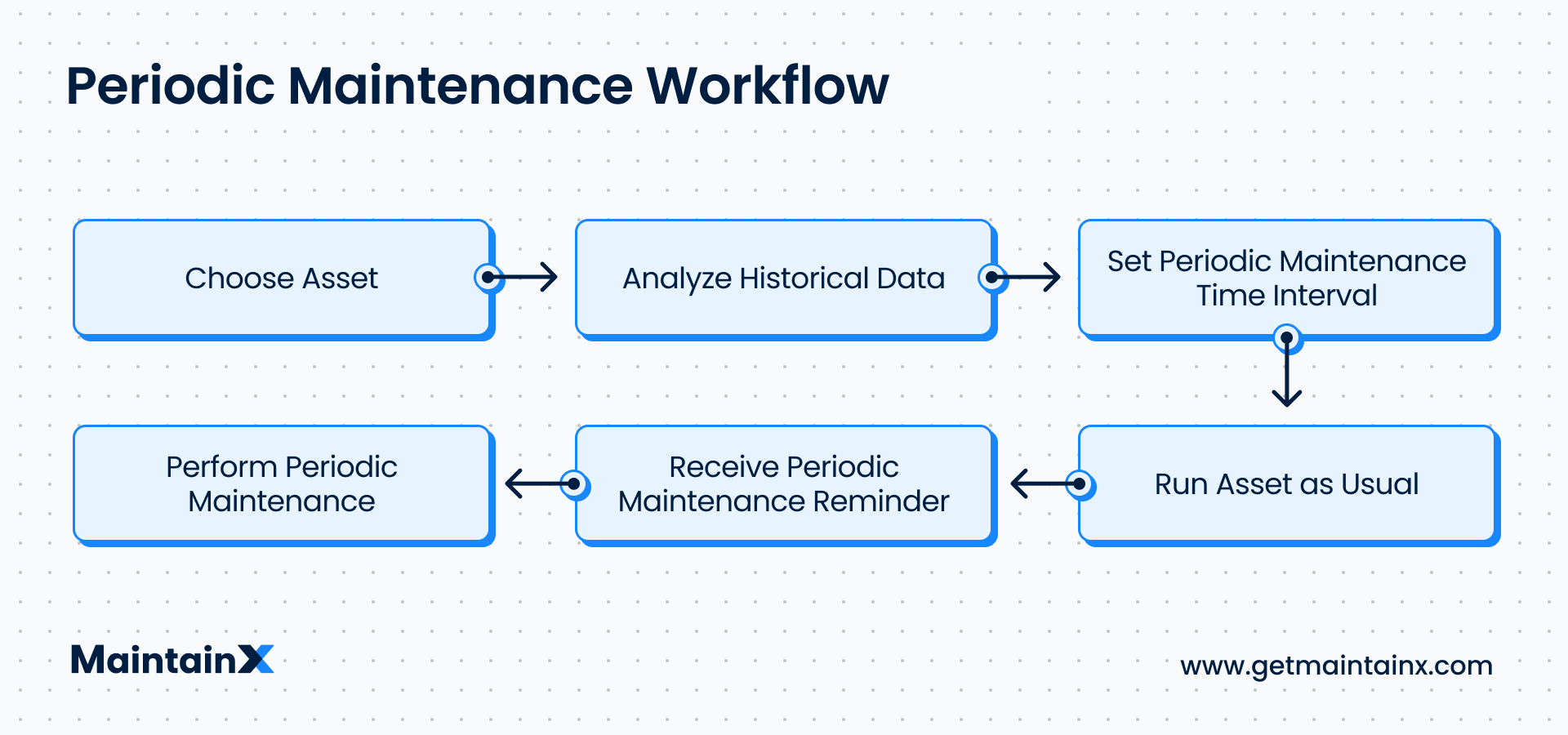
2. Condition-based maintenance
This type of preventive maintenance is based on condition monitoring of the equipment. Teams perform maintenance when certain predefined thresholds or limits are reached. Companies typically use condition-based maintenance for more complex, higher-risk systems or equipment with unpredictable failure rates.
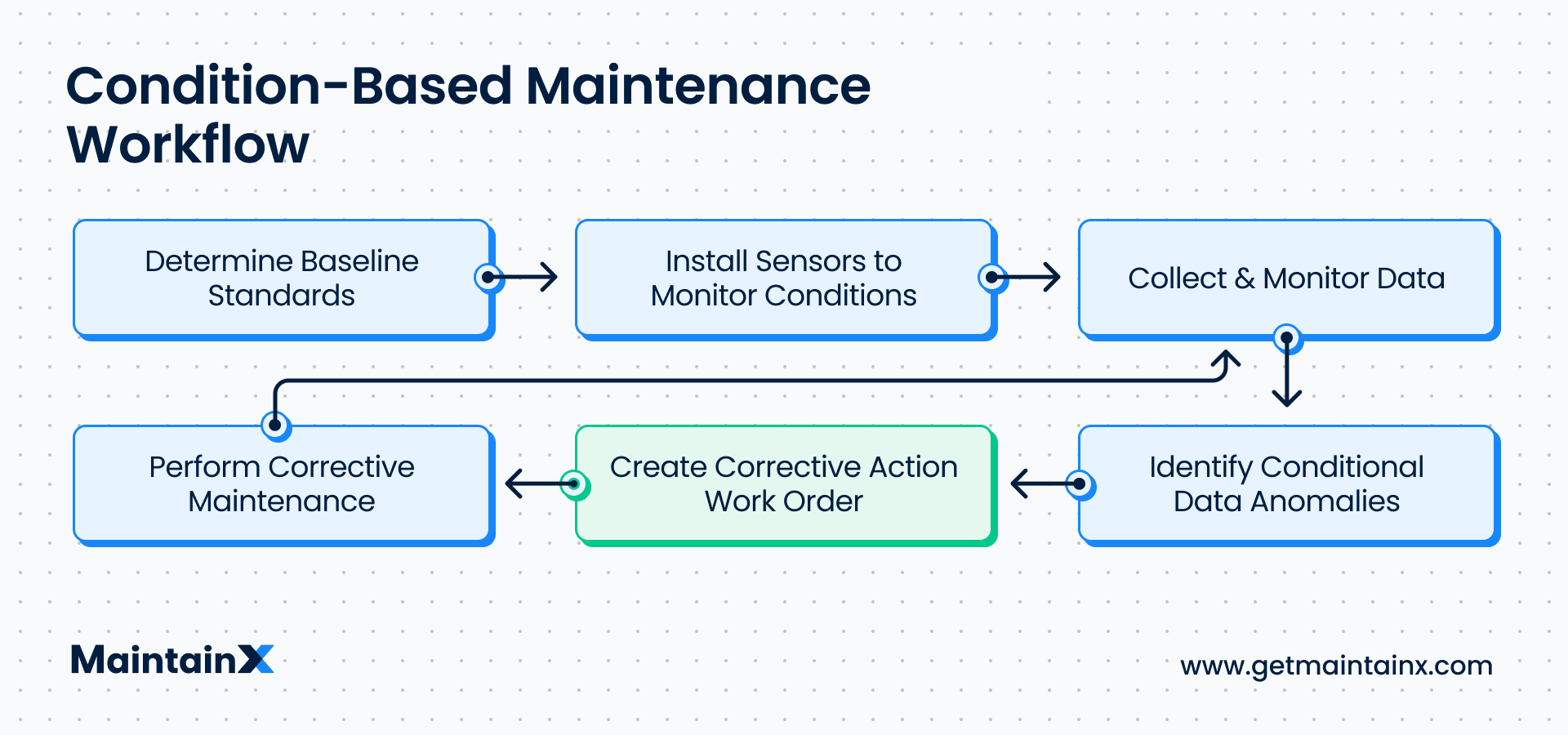
3. Predictive maintenance
This type of preventive maintenance uses monitoring and diagnostic tools to predict when equipment is likely to fail and schedule maintenance accordingly. Companies typically use predictive maintenance for complex, mission-critical systems or equipment with a high failure cost.
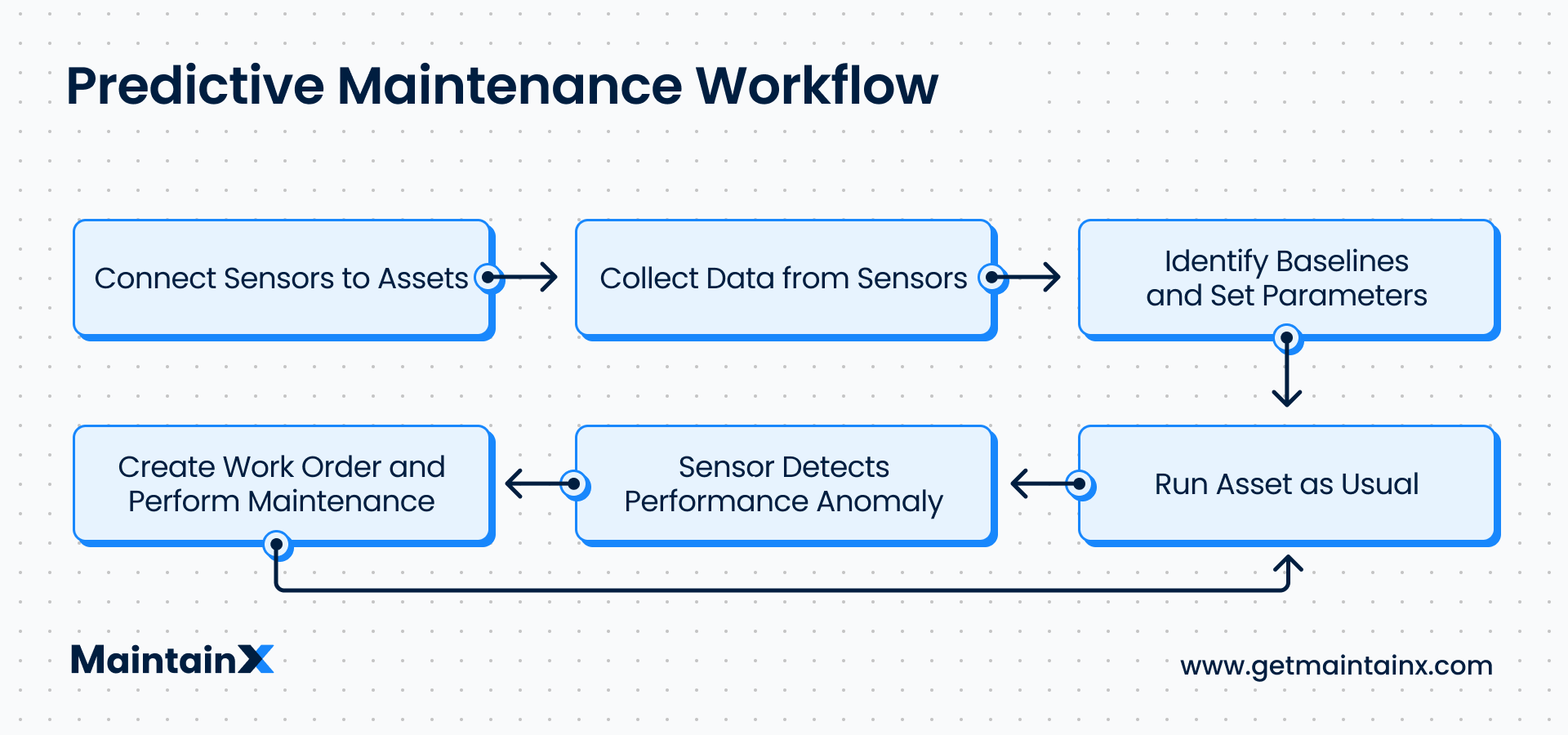
4. Performance-based maintenance
This type of preventive maintenance is based on the performance of the equipment. Teams perform maintenance when specific performance targets are not being met. Companies typically use performance-based maintenance for equipment that critically impacts the system’s overall performance.
5. Risk-based maintenance
This type of preventive maintenance is based on the risk associated with the equipment and is focused on mitigating the most critical risks first. Risk-based maintenance is typically used for systems or equipment with multiple potential failure modes and varying levels of risk.
In addition to these plans, preventative measures undertaken regularly are not part of any formalized plan. Still, they contribute significantly to ensuring the reliability of a system or process. These measures include:
- keeping up with industry standards for safety and quality control
- creating an inventory management system
- implementing best practices for troubleshooting
- conducting regular audits
- raining staff on proper techniques for handling equipment and systems
By taking all these steps into account, organizations can enjoy reliable systems. And, in the process, avoid costly repairs due to unexpected failures or malfunctions.
Examples of RCM across industries
RCM was first established for the aviation industry. However, industries and organizations often use the minimum criteria for RCM processes outlined in technical standard SAE JA1011: Evaluation Criteria for Reliability-Centered Maintenance (RCM) Processes.
The Society of Automotive Engineers (SAE) outlines seven questions in the SAE JA1011 standards that inform the criteria for RCM processes, regardless of industry:
- What are the equipment’s primary function and performance standards?
- What are the possible ways in which it can fail to perform the main function?
- What are the causes of each failure?
- What happens when each failure occurs?
- What are the impacts of each failure on the system?
- How can you prevent or minimize the impact of each failure?
- What actions should you take if failure cannot be prevented?
RCM in technology industry
One example of how manufacturers have successfully implemented and benefited from reliability-centered maintenance is a large-scale technology manufacturer. This company had a range of equipment, from small machines to complex robotics systems. To ensure maximum reliability and minimize downtime, they implemented a reliability-centered maintenance program by thoroughly analyzing the various components of their production machines. They then determined the most likely sources of failure. After making these assessments, they identified which components were most prone to failure. They began implementing preventive maintenance work orders to detect problems early and take corrective action before more serious issues arose. The result was a dramatic decrease in downtime, improved efficiency, and increased customer satisfaction with the quality of their products.
RCM in food industry
A large food processing plant that processes millions of pounds of frozen raw materials daily implemented RCM. Through extensive analysis, they determined which components posed the most significant risk for potential failure or breakdowns. They then designed a proactive system with standard operating procedures that included regular inspections and tests to catch issues before they caused costly delays in production time or product spoilage. As a result of this proactive system, they experienced fewer unexpected shutdowns caused by machinery failures. They also reduced overall costs associated with machine repairs or replacements. This also improved customer satisfaction due to consistently higher quality products being produced.
RCM in automotive industry
An automotive parts manufacturer needed to keep their assembly lines running smoothly despite frequent heavy use and extreme environmental conditions. By conducting periodic inspections on its machinery as well as using predictive analytics techniques, they were able to create maintenance schedules tailored specifically to each particular piece of equipment—not just one generic schedule for all machines across the entire plant. This enabled them to identify potential problems early on. The company took corrective action quickly. No major issues occurred while they prevented unplanned outages due to mechanical breakdowns or malfunctions. Ultimately this led to greater overall equipment effectiveness (OEE), productivity, and cost savings associated with fewer unexpected repairs or replacements down the road.
CMMS and RCM
With CMMS software, manufacturers can easily track and record all information related to the maintenance activities of their assets. This, in turn, helps identify situations that could lead to equipment failure or downtime. In addition, by using RCM as part of their overall maintenance strategy, manufacturers can ensure that all necessary preventive measures are taken to minimize the risk of mechanical breakdowns or downtime.
CMMS software also helps manufacturers keep their equipment running at its peak operating efficiency. By providing detailed data on how each piece of machinery is performing, CMMS software allows manufacturers to identify areas where they can optimize performance and extend the lifespan of their assets. In addition, manufacturers can use this data to identify potential issues before they cause problems and quickly determine when equipment needs to be serviced or upgraded to maintain optimal performance levels.
Overall, RCM, combined with the convenience of CMMS software, provides an effective preventative maintenance strategy for reducing unplanned downtime, improving reliability, and ensuring that all machinery runs at peak efficiency. With an effective preventative plan in place, manufacturers can achieve maximum production rates while keeping operational costs low. As a result, businesses can increase their competitive advantage by eliminating or minimizing mechanical failures. This reduces long-term repair costs associated with emergency maintenance activities.
Let MaintainX run your RCM
Reliability-centered maintenance programs allow organizations to choose the most cost-effective AND reliable maintenance strategy for each asset. RCM programs reduce unnecessary costs, improve safety, and eliminate unnecessary work orders. Larger organizations that can afford to implement advanced periodic maintenance strategies benefit most from RCM’s holistic framework. MaintainX can run your RCM and reduce downtime, increase asset useful life, and help you work smarter, not harder.
Ready to digitize your maintenance program to MaintainX?
See MaintainX in action