If it ain’t broke, don’t fix it.
Reactive maintenance is the world’s oldest approach to maintenance. Also called “run-to-failure,” reactive maintenance refers to maintenance tasks performed after an asset has broken down. The focus is on restoring assets to operating conditions as quickly as possible. According to a Plant Engineering study, 61 percent of manufacturing facilities practice reactive maintenance.
What Is Reactive Maintenance?
Reactive maintenance serves only one purpose—to address problems when they arise. Maintenance activities are triggered by equipment malfunctions, setbacks, and failures. Broken-down machines are either repaired or replaced. For example, do you change a light bulb before it burns out? The most logical thing to do would be to wait for it to burn out and then buy a new bulb. The run-to-failure approach is best suited for non-critical and low-cost pieces of equipment that don’t have a major impact on production or your team’s safety.
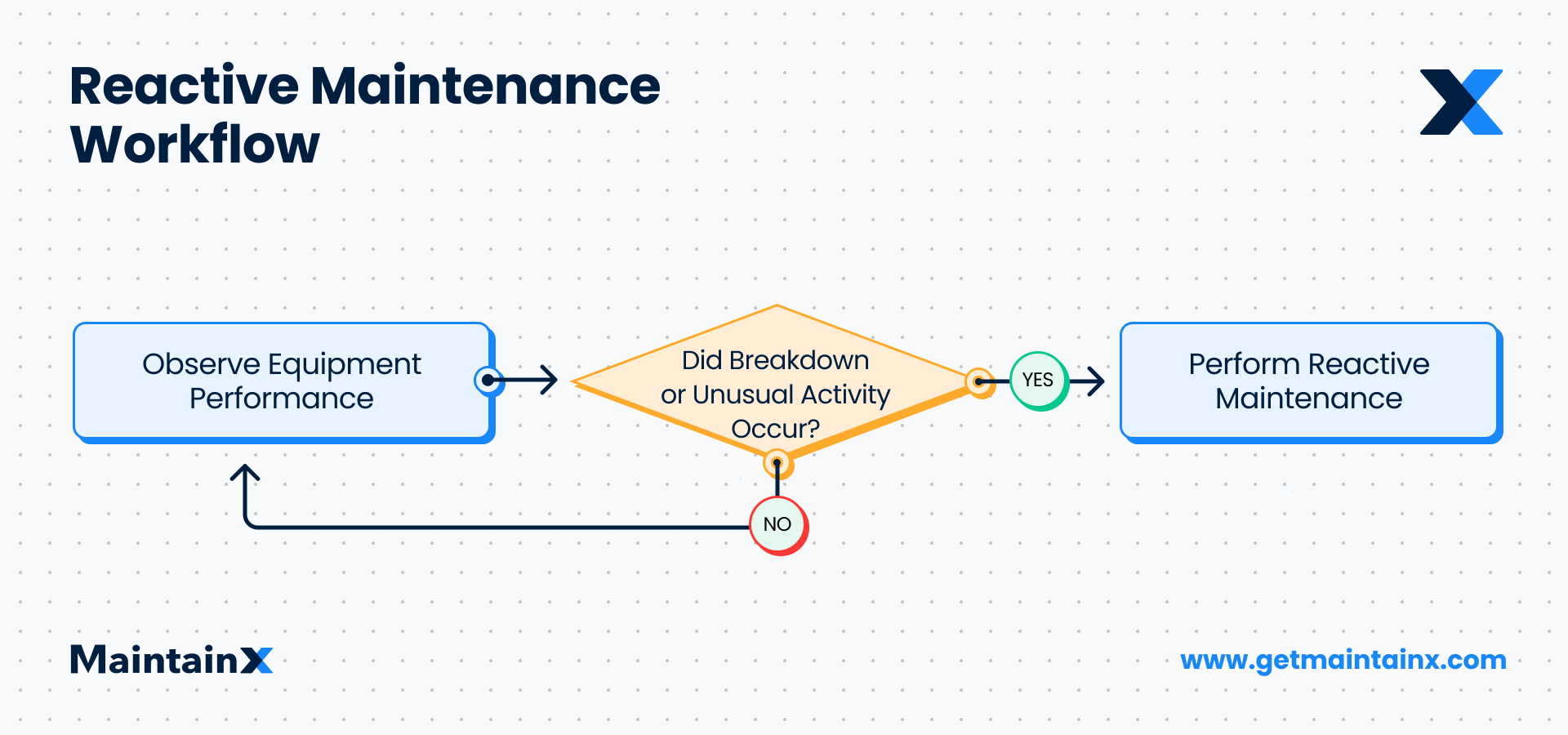
Types of Reactive Maintenance
Reactive maintenance is a maintenance activity undertaken in response to an equipment breakdown. There are two types of reactive maintenance strategies:
Emergency Maintenance
Emergency maintenance refers to maintenance activity that needs to be taken immediately to restore an asset’s operational capacity. It can also be a response to urgent safety requirements that must be addressed. Emergency maintenance activities are always given priority to avoid extended shutdowns and possible losses. Factors such as replacement part availability and repair scope can impact emergency maintenance.
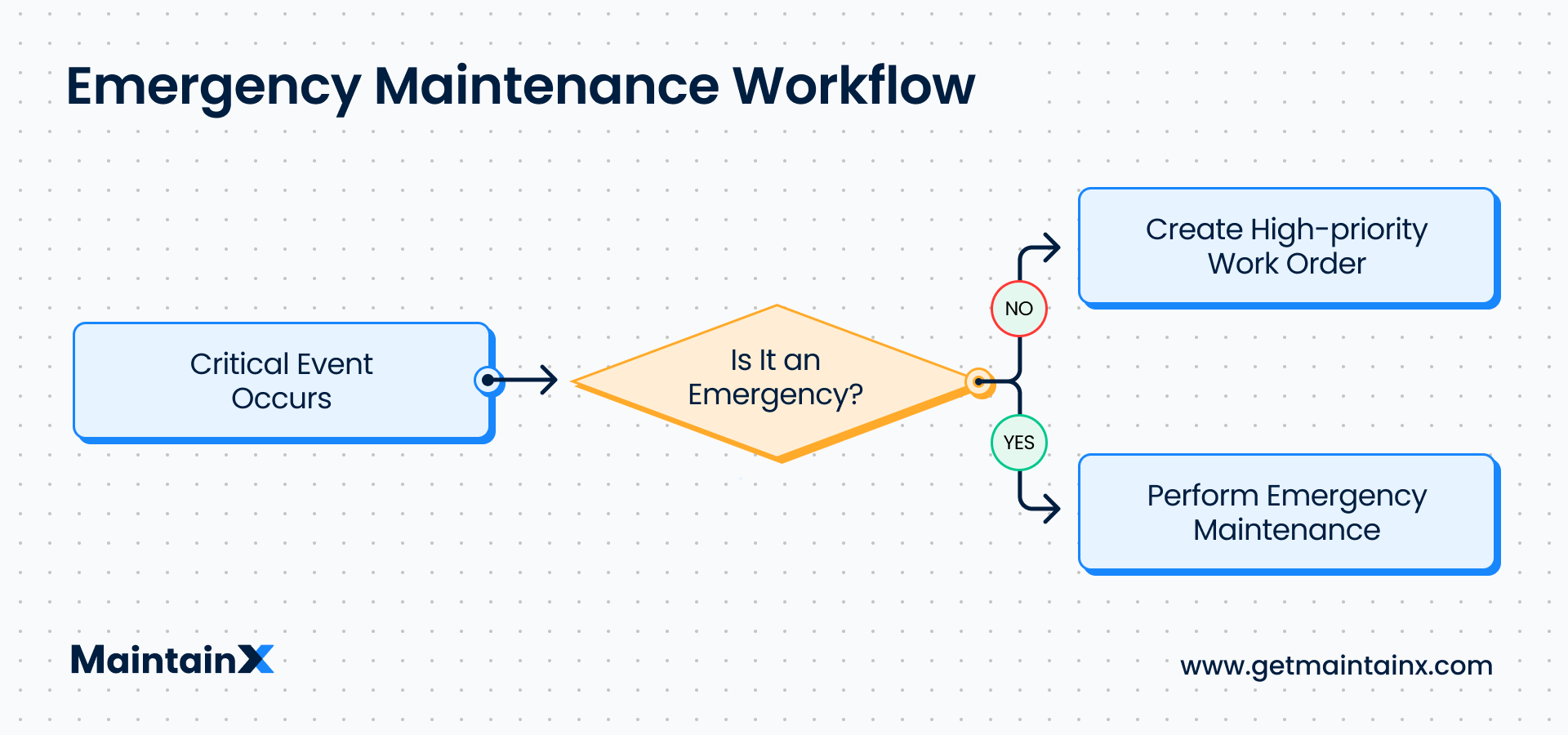
Corrective Maintenance
In some cases, assets can have problems that are yet to escalate into failure. For example, a piece of equipment has started rusting. In such situations where disruption of production is yet to occur, maintenance is performed to restore the asset to its optimal condition. Some people argue that this is proactive maintenance because failure is yet to occur, but any maintenance activity that is a reaction to a situation or a cause falls under reactive maintenance. Corrective maintenance can be performed when the problem is detected or scheduled for later to allow the company to organize resources.
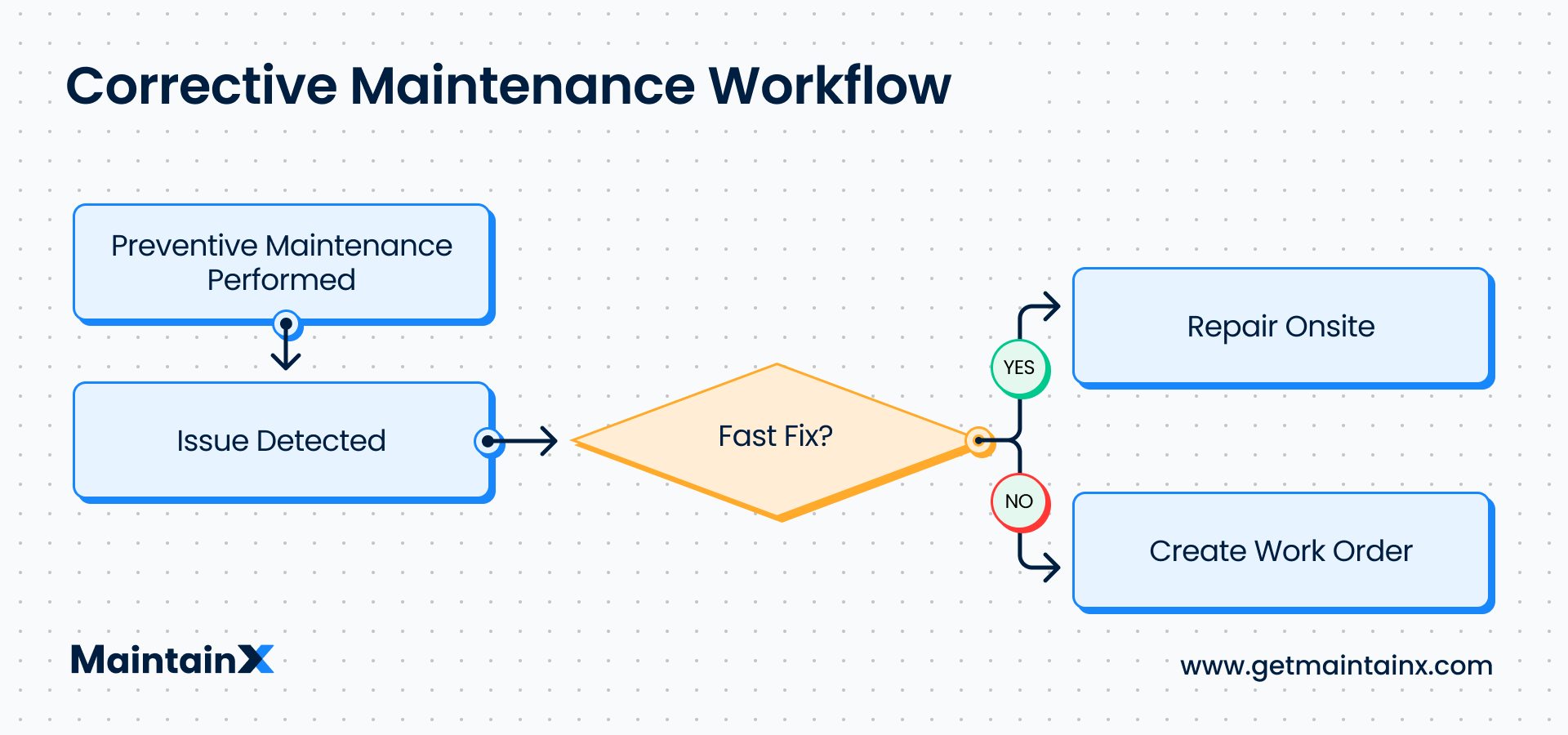
Emergency maintenance is usually more expensive than corrective maintenance because there’s little time to pull together resources. It often forces organizations to outsource maintenance services and pay extra for expedited delivery of replacement parts.
Reactive Maintenance vs. Proactive Maintenance
Taking a purely reactive approach to maintenance is always discouraged. Aberdeen estimates that the manufacturing industry loses an average of $50 billion each year due to unplanned downtime. The International Society of Automation (ISA) says that organizations banking on reactive maintenance stand to lose up to 20 percent of their productive capacity.
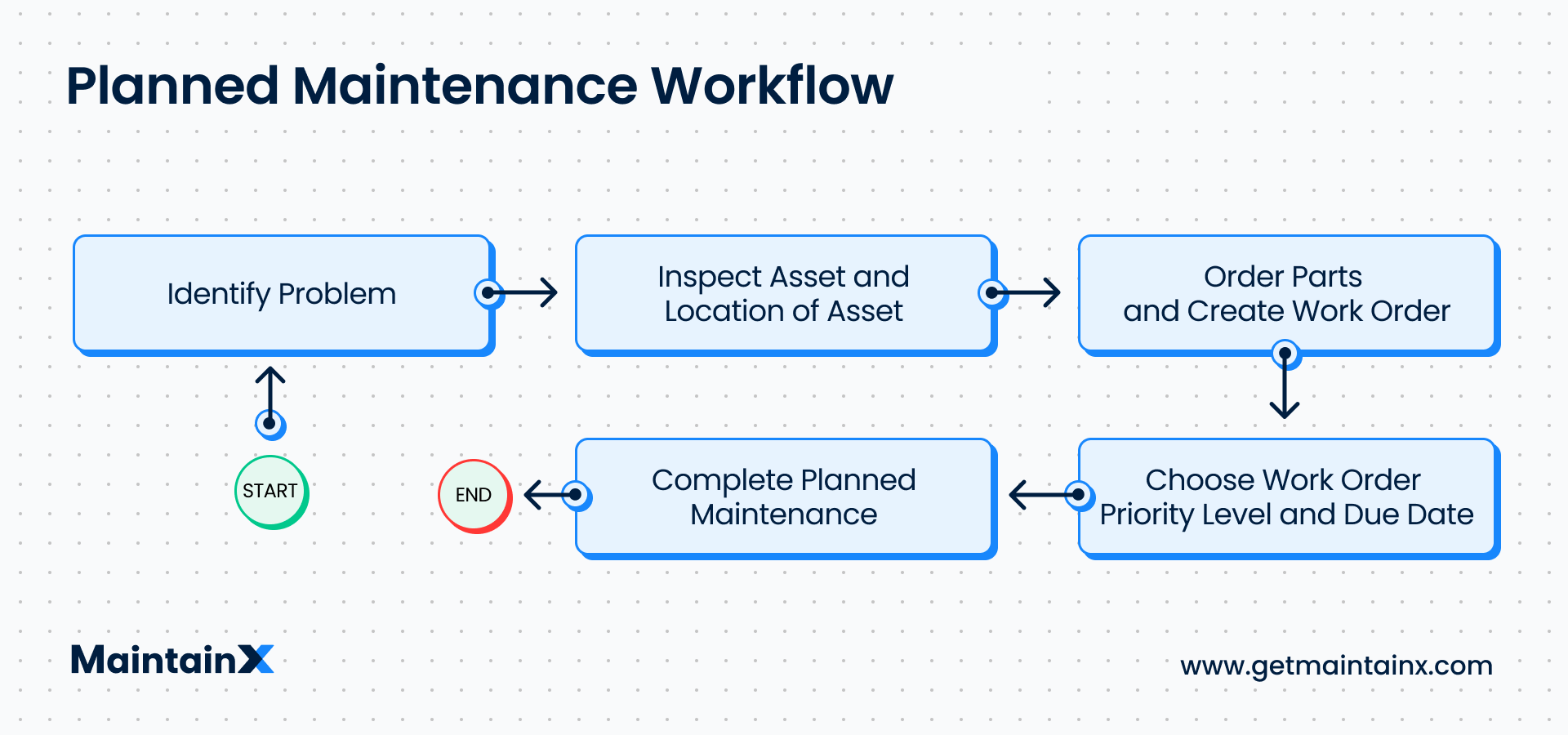
We’ve already defined reactive maintenance as maintenance tasks triggered by equipment malfunctions, setbacks, and failures. Proactive maintenance, on the other hand, refers to a preventive maintenance approach that seeks to anticipate defects and prevent failures before they occur. It plans maintenance activities based on data gathered from Computerized Maintenance Management Systems (CMMS), machine sensors, and condition-based monitoring mechanisms. Maintenance seeks to address the root cause of asset failure. For example, one might measure the vibrations of a rotating machine to determine its condition.
Is One Better Than the Other?
According to Plant Engineering, at least 33 percent of companies want to move from a reactive maintenance approach to a proactive one. However, reactive maintenance always happens based on the finite nature of machinery.
A well-planned and executed proactive maintenance strategy requires an organization to have resources at its disposal. Since the initial costs of moving toward preventive maintenance can be high, experts recommend prioritizing PM for critical assets as a starting point. Reactive maintenance, therefore, will take care of non-critical assets.
Even for reactive maintenance, companies can still plan and schedule maintenance tasks (corrective maintenance). Reactive maintenance is only problematic if it is unplanned (emergency) and impacts production or safety. Experts recommend adopting the 80/20 approach, based somewhat on the Pareto Principle, where 80 percent of maintenance activities are proactive while 20 percent is reactive.
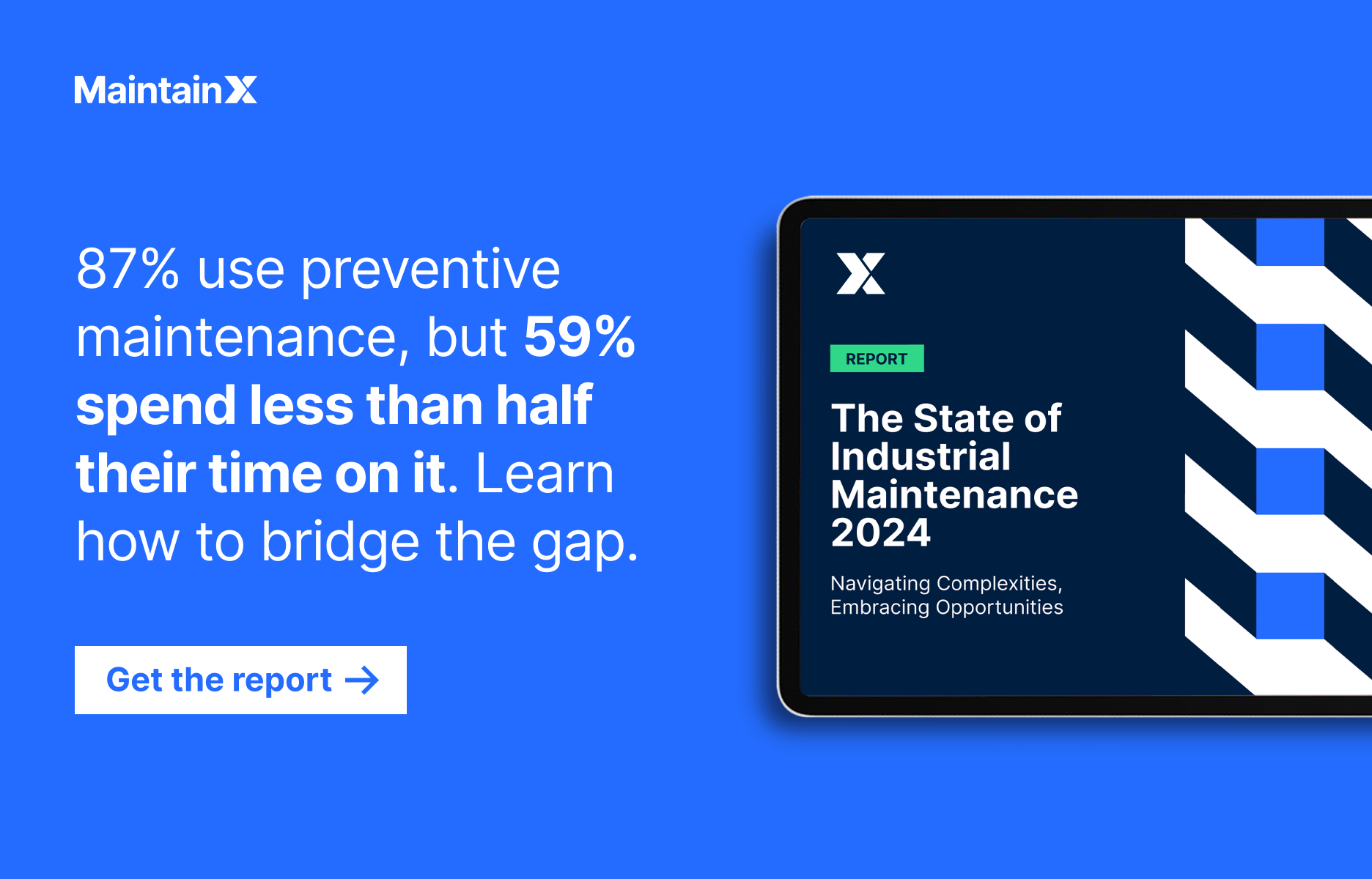
Examples of Reactive Maintenance
Let's look at a few examples of what this looks like in common situations.
1. Car Maintenance
How many times have you seen a car not starting because the battery died and the owner had to jumpstart it and later replace it? Here the driver performed a reactive maintenance task. Another example would be when you take your car for an oil change. The technician may realize that other parts, the headlights, for example, also need servicing. You can decide to have the repairs done at that particular moment or schedule them for another day. However, should your headlines stop working on a dark road at night, you would need to perform emergency maintenance.
2. Road Repair
Roads are installed to last for a long time. However, wear and tear is a common occurrence, especially for roads that experience high traffic. One of the most common problems on our roads is potholes. Fixing potholes on a road can only be done after they occur.
Other examples include fixing broken doors, replacing leaking water pipes, and buying a new HVAC after the current one breaks down. We could go on and on!
Interesting Statistics
Most organizations downplay the importance of maintenance. However, it’s a massive industry worth billions of dollars. Here are a few maintenance statistics:
● Maintenance activities can take up to 40 percent of the total production costs, according to A Comprehensive Approach for Maintenance Performance Measurement.
● The U.S. maintenance industry employs more than 1.3 million people.
● A run-to-failure maintenance approach can cost up to 10 times more than a proactive maintenance plan. Nonetheless, about 80 percent of industrial plant maintenance managers still heavily rely on reactive maintenance.
● According to Plant Engineering, 44 percent of reactive maintenance is usually the result of aging equipment.
Advantages and Disadvantages of Reactive Maintenance
Just as with every other strategy, this type of maintenance strategy has its benefits and drawbacks. See the table below:
Get a CMMS to Run Your Maintenance Workflows
Reactive maintenance addresses problems when they arise. It is best suited to non-critical assets and requires minimal initial costs for maintenance systems. However, it has its limitations, especially when critical assets are concerned. Reactive maintenance can complement proactive maintenance for a reliability-centered maintenance approach to managing assets.
CMMS software allows maintenance teams to create work order templates in advance and assign tasks when maintenance needs arise. The software helps busy managers track, plan, and operationalize maintenance activities and analyze failure data.
See MaintainX in action