Have you ever fixed a broken dryer, washing machine, or dishwasher? If so, you’ve performed corrective maintenance.
Corrective maintenance is a crucial part of asset management that reduces downtime by fixing issues as soon as possible. With downtime costing, on average, $25,000 per hour, it’s important that facilities do all they can to get downtime under control. In this guide, we explore the different types of corrective maintenance, their advantages and disadvantages, some examples, and how to perform corrective maintenance at the right time.
What is corrective maintenance?
Simply put, corrective maintenance is unscheduled maintenance performed after something has broken. It is a category of maintenance tasks that fixes or repairs equipment failure and can be part of preventive or reactive maintenance. While preventive maintenance work aims to keep assets in good working condition, it can include corrective actions. For example: A technician carrying out a routine inspection notices that part of a larger piece of equipment isn’t working properly. The technician then fixes the part before the equipment breaks down. While this maintenance process is preventive, the actions to get that part working properly are corrective.
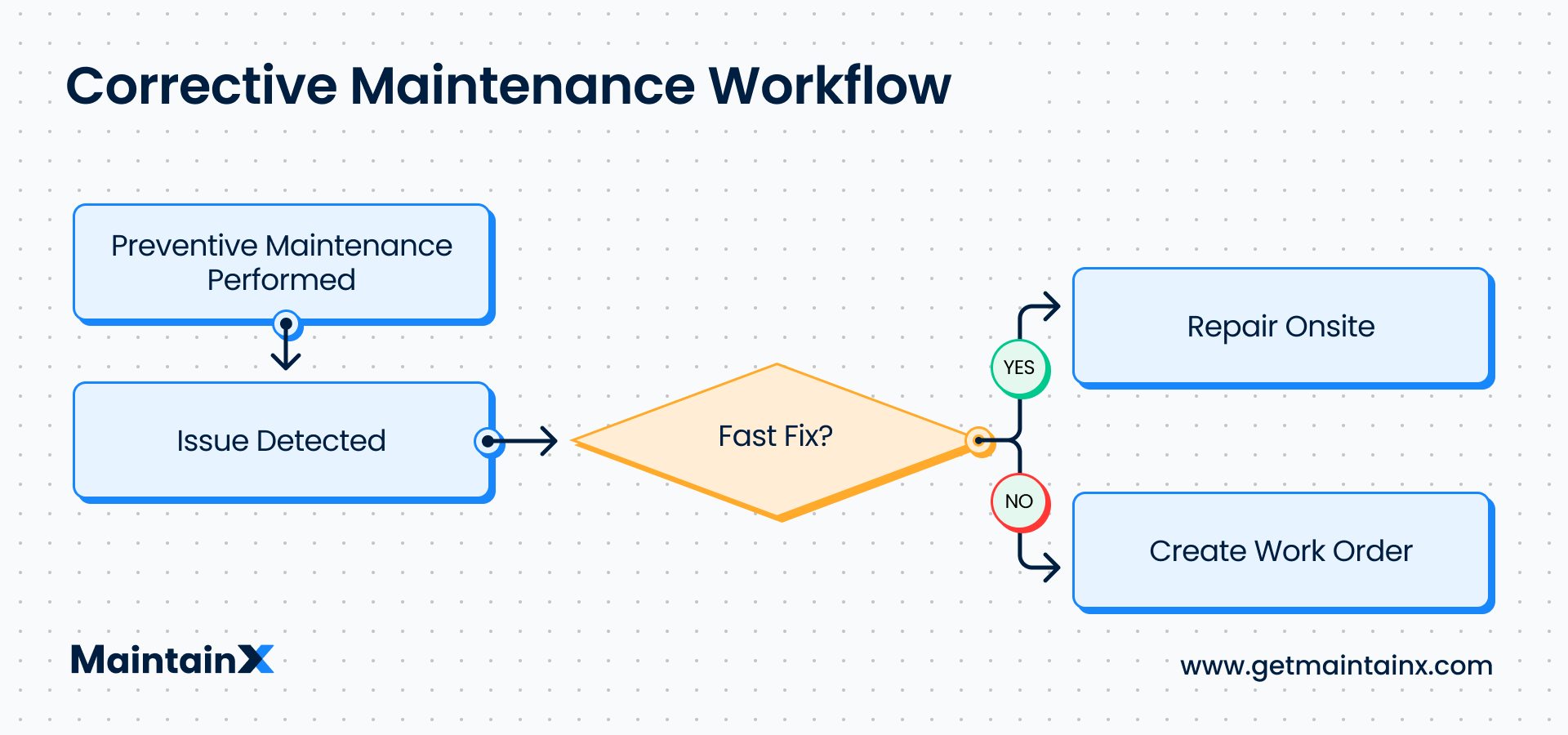
Types of corrective maintenance
Corrective maintenance falls into two major categories: planned and unplanned.
Planned corrective maintenance
Planned corrective maintenance involves performing maintenance work to repair or replace a malfunctioning asset according to a prearranged schedule—before it completely breaks. This kind of scheduled corrective maintenance means you identify the issues or problems first, plan out their repairs, and then carry them out during scheduled downtime.
Unplanned corrective maintenance
Sometimes, an asset fails unexpectedly, and you need to get it back up and running immediately. Unplanned corrective maintenance refers to repairs that technicians perform immediately under such circumstances. Certain assets are critical for safety and production and require you to restore their operational functionality ASAP. This type of corrective maintenance is reactive, time-sensitive, and occurs without prior scheduling.
To understand planned and unplanned corrective maintenance a bit more, let’s explore the instances that require them.
When is corrective maintenance performed?
As we’ve explained, teams can perform corrective maintenance either according to a schedule or on an emergency basis. In practice, this can look like:
- Unexpected breakdowns: When an asset fails unexpectedly, technicians perform corrective maintenance to get it back up and running.
- Performance issues: Here, a piece of equipment hasn’t failed but is performing sub-optimally. Corrective maintenance here focuses on fixing the cause of the malfunction before an actual breakdown occurs.
- Safety issues: Sometimes, pieces of equipment are performing just fine as far as production is concerned, but they show signs of impending malfunctions that can threaten safety.
- Routine inspections: During regular inspections, teams can identify issues and schedule corrective actions.
Examples of corrective maintenance
Here are a few scenarios when this type of maintenance is used:
- Example of unscheduled corrective maintenance: Water companies periodically deal with hard water residue build-up in their pipes. This common occurrence can increase water pressure and lead to burst pipes. When a pipe does burst, water companies must immediately replace it to avoid significant financial losses.
- Example of scheduled corrective maintenance: Dusty HVAC filters negatively affect unit efficiency over time because the system has to work harder. For this reason, facilities often replace air filters monthly.
Corrective maintenance best practices
For effective corrective maintenance, here are some steps to follow.
Create a rapid response plan
By developing a rapid response plan ahead of any actual breakdowns, you ensure that your maintenance team can quickly address those breakdowns when they do happen. This plan should include clear steps for diagnosing issues, accessing necessary tools and spare parts, and deploying skilled technicians. This way, you’ll eliminate any critical downtime spent figuring out how to handle the problem.
Document maintenance and repair SOPs
Implementing standard operating procedures (SOPs) helps ensure that your teams have a step-by-step guide to the corrective actions they need to take. These SOPs will help technicians perform tasks correctly and uniformly, leading to consistent outcomes every time. A Computerized Maintenance Management System (CMMS), particularly one with mobile access, is a useful tool for giving your team access to SOPs wherever they are.
Prioritize maintenance based on criticality
If you have limited resources, one element of managing your resources effectively is determining the criticality of your assets. To do this successfully, assess factors like the impact of equipment failure on production, safety, and costs.
Improving corrective maintenance with a CMMS
Corrective maintenance requires companies to invest in resources that enable their workforce respond effectively to equipment problems. Organizations can avoid major unplanned downtimes—and extend asset life spans— by pairing both unplanned and planned repair actions with realistic preventive maintenance programs. When planning programs, aim for an 80 percent preventive maintenance to 20 percent corrective maintenance ratio.
A CMMS like MaintainX can help you schedule corrective maintenance and react quickly to equipment failures. Here’s how:
Work order management
If you’re dealing with a breakdown that requires emergency corrective maintenance, every second counts. With downtime costs going as high as $500,000 an hour in some facilities, you need to be able to respond quickly. It’s crucial to be able to communicate with staff instantly, share instructions, access data, and monitor progress. Even if you’re scheduling corrective maintenance in advance, you need to be able to manage work orders properly. MaintainX CMMS enables all of these and more with robust work order management features. Assign and track work orders in real time, and ensure your technicians capture the right data every single time using time tracking, signatures, pre-filled templates, required fields, and more.
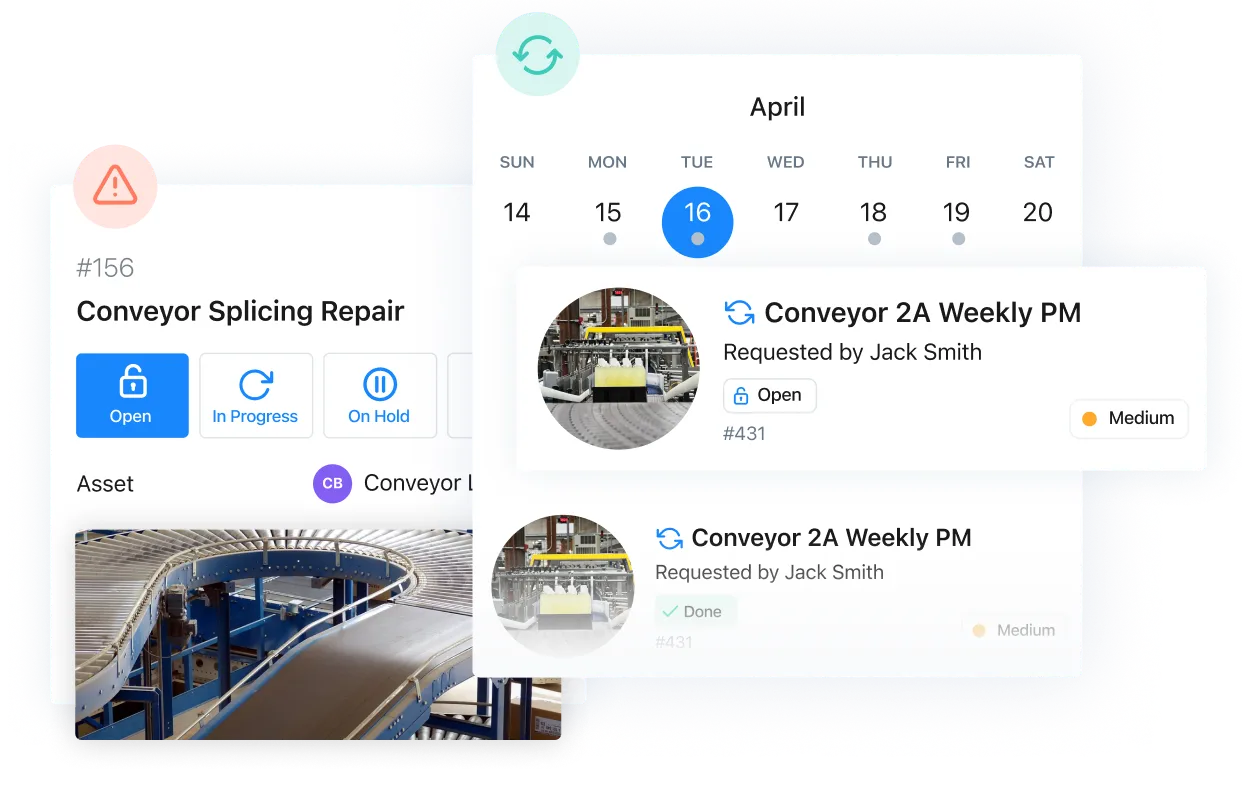
Digital parts inventory
Corrective actions cannot take place without the right parts and tools. Quickly locate parts with digital inventory management features like QR codes and barcodes. Take advantage of automated low-quantity alerts and automatically generated purchase orders to prevent stockouts and eliminate costly rush orders.
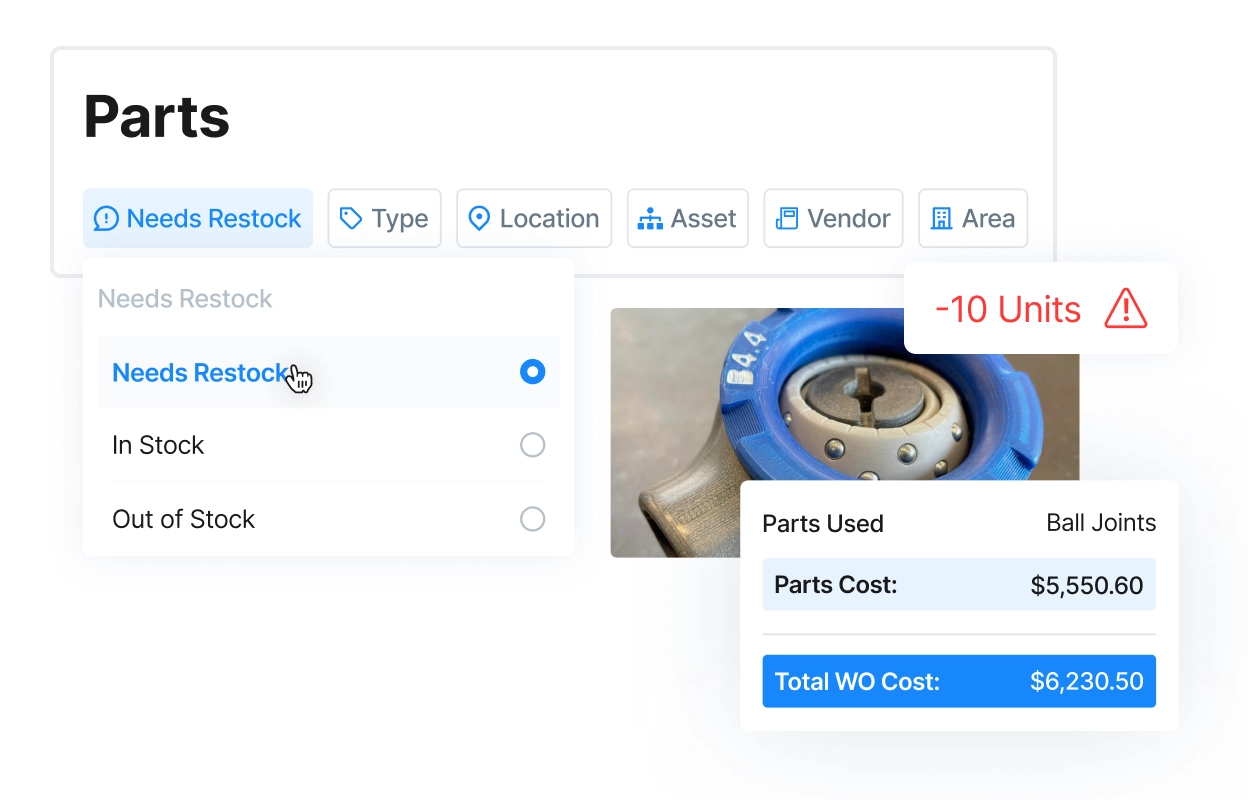
Reporting and analysis
Tracking and analyzing asset performance data helps you determine how well your maintenance efforts are doing. MaintainX reporting tools provide data-driven insights that enable you to make the right decisions about your corrective maintenance. You’ll be able to identify what processes are working and which need rethinking.
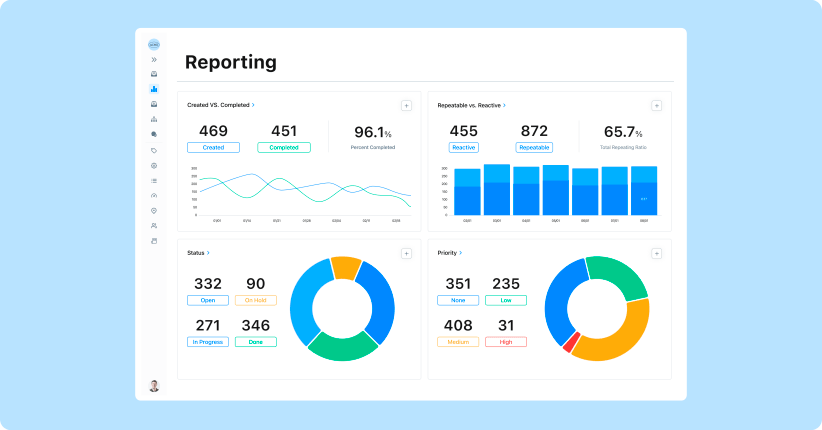
Book a tour with one of our experts and discover how we can help you save time and money by improving and automating your maintenance management!
Frequently Asked Questions
It’s easy to confuse planned corrective maintenance with preventive maintenance (PM). However, there are some clear distinctions between the two maintenance strategies.
Most notably, corrective maintenance focuses on dealing with problems after they occur. On the other hand, PM focuses on reducing the likelihood of problems occurring in the first place. Corrective maintenance is performed at random intervals as assets break, while preventive maintenance is conducted regularly with active inspection measures in place.
Finding the right balance between corrective maintenance and preventive maintenance can be tricky. John Day, operational manager at Alumax of South Carolina, answers this persistent question with The 6–to-1 Maintenance Philosophy. The philosophy dictates that for every six PM tasks a company performs, it may need to complete one corrective task.
This ratio ensures that equipment issues that cannot be predicted with preventive maintenance are handled with planned corrective actions before excessive downtime can occur. While the 6-to-1 Maintenance Philosophy provides a valuable benchmark for equipment service planning, every organization is unique. Nothing substitutes for conducting a thorough asset inventory, tracking individual asset behavior, and fine-tuning a customized preventive maintenance strategy.
As previously mentioned, maintenance can be planned or unscheduled. Unscheduled corrective maintenance refers to actions taken immediately after asset failure occurs. In such instances, the failure is considered critical, and corrective action is needed ASAP.
Planned corrective maintenance, however, refers to actions that are needed but can be deferred to a later date without harm. Deferred maintenance can happen due to limited resources in terms of budget, time, or staff resources. Specific maintenance tasks might also be backlogged because they require outsourced specialty services. Planned corrective maintenance takes place in two forms:
- Run-to-failure maintenance strategy: Here, an asset will be allowed to run until it breaks down. Only then will it be repaired or replaced. The strategy is suitable only for redundant systems and non-critical assets that the company can easily replace or repair cheaply.
- Planned corrective maintenance (part of CBM or preventive maintenance): In this instance, problems identified during preventive and condition-based maintenance inspections are scheduled for maintenance actions.
This type of maintenance is best used in conjunction with a comprehensive PM program. Experts recommend only relying on corrective maintenance when absolutely necessary. Your reliance on it will depend on a number of factors, such as how critical certain assets are to daily operations, the cost of downtime for these assets, and how easily swappable the pieces are in the event of a problem. When in doubt, follow the 80/20 rule: direct 80 percent of your effort toward preventive PM and 20 percent of your attention toward corrective maintenance.
Timely corrective maintenance identifies asset problems before equipment failure occurs. Whether planned or unscheduled, it catches issues before they lead to downtime and unnecessary costs. For example, you can replace worn-out brake pads before they affect the rotors. Replacing the worn-out brake pads (correcting the problem) keeps the rotor from breaking down and grounding the vehicle (downtime).
Based on your maintenance management plan, your maintenance team will initiate corrective maintenance when it notices that an asset is about to break down or that the condition of a given component will affect the overall performance of an asset. Repairs and restoration can be done before downtime occurs. This helps minimize equipment failure and increase the lifespan of individual pieces of equipment.
Unfortunately, unplanned corrective maintenance can halt production lines and cause service interruptions. However, the downtime for correction is minimal compared to total equipment failure. Unscheduled corrective maintenance interruptions are intended to restore assets to optimal performance before failure.
See MaintainX in action