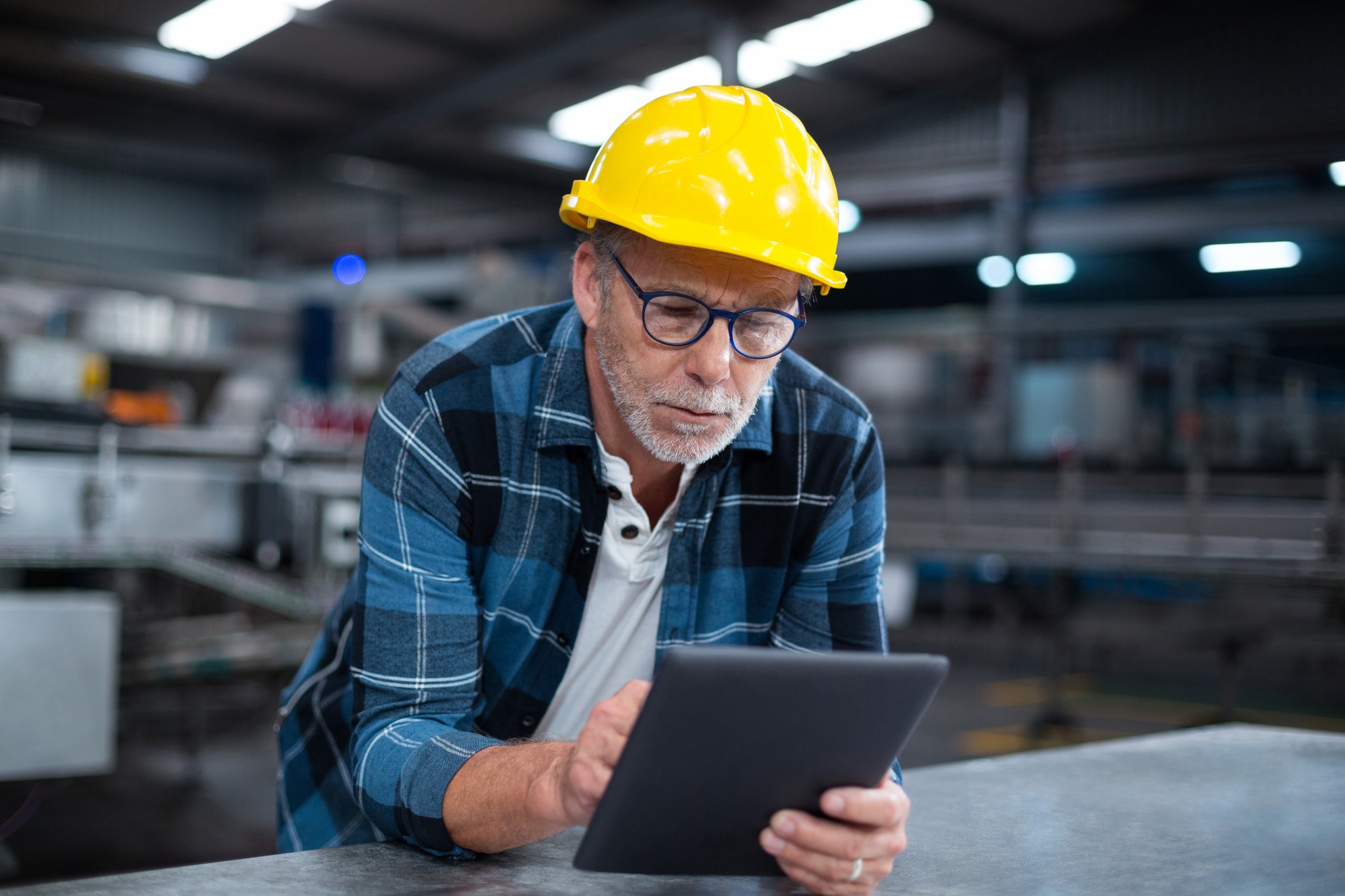
Every hour of unplanned downtime costs companies an average of $125,000. Lost production, emergency repairs, and schedule chaos—it all adds up fast. Think you're immune to a major breakdown? Think again. Even a seemingly minor oversight, like inadequate lubrication, can cripple operations and lead to six-figure losses.
Reactive maintenance is a gamble you can't afford, but preventive maintenance puts you in the driver's seat. Instead of waiting for problems to strike, you'll get ahead of them, safeguarding your machinery and keeping your facility running at peak efficiency. This guide is your blueprint for proactive maintenance success, covering everything from the critical components of preventive maintenance to building a preventive maintenance plan—empowering you to slash costs, maximize uptime, and protect your bottom line.
What is preventive maintenance?
Preventive maintenance is a proactive maintenance strategy for maintaining equipment, machinery, and other assets in optimal condition to prevent failures and breakdowns. It involves regular inspections, servicing, and repairs to address minor issues before they escalate into major problems.
The objective of preventive maintenance is to optimize asset performance and longevity. By proactively addressing minor issues, preventive maintenance eliminates unforeseen downtimes, reduces the frequency and severity of breakdowns, and ensures consistent, efficient operation of equipment and assets.
A key component of preventive maintenance programs is condition monitoring. Condition monitoring evaluates specific machine behavioral indications—temperatures, vibrations, oil levels—to prevent impending failure. For example, maintenance technicians must replace machine bearings after so many hours because they aren’t designed to last forever.
Why companies are prioritizing preventive maintenance
Preventive maintenance offers maintenance teams a level of control over their downtime that is not possible with reactive maintenance. Instead of waiting for assets to break down, companies can strategically plan downtime to perform maintenance on equipment to reduce future breakdowns and unplanned downtime.
This proactive approach can have a dramatic financial impact. According to ABB’s recent Value of Reliability survey, two-thirds of industrial businesses experience unplanned downtime at least once a month, costing the typical business nearly $125,000 per hour globally. Some estimates place the total cost of unplanned downtime at over $50 billion a year.
Costs associated with unplanned downtime include lost production time, repair work, and replacement parts. The potential for material financial impact underscores the need for companies to prioritize asset health with preventive maintenance plans, skilled technicians, and strategic inventory management.
Through planned maintenance, companies can:
- Extend asset lifecycle;
- Maintain uptime;
- Reduce spending on repair work; and
- Avoid expensive rush orders on emergency replacement parts.
Preventive maintenance vs. reactive maintenance
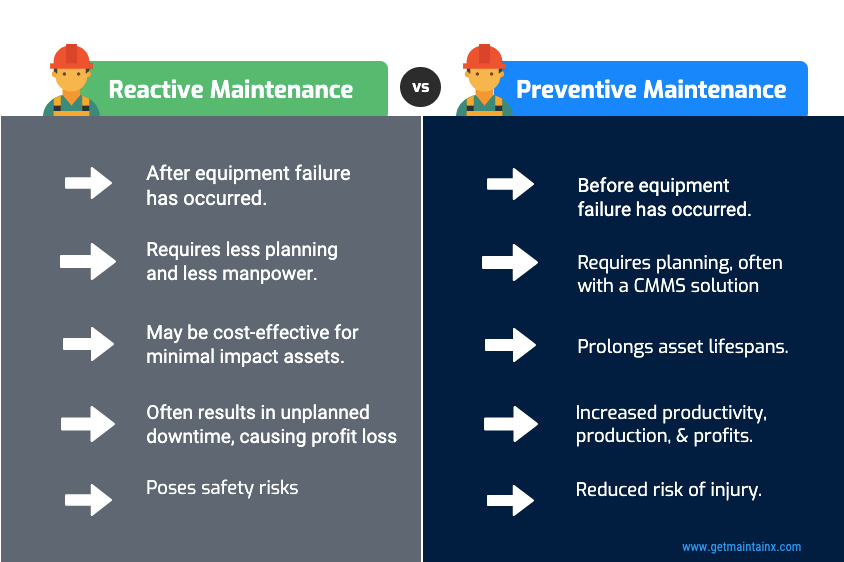
Reactive maintenance is exactly as the name suggests—maintenance work done in response to breakdowns or failures. Also known as run-to-failure maintenance, it entails waiting for minor problems to become big before doing anything about them. According to the Schneider Electric Report, “Predictive Maintenance Strategy for Building Operations: A Better Approach,” 55 percent of U.S. companies exclusively practice reactive maintenance.
On the one hand, the logic might seem obvious. After all, why fix it if it isn’t broken? But when you leave minor issues to fester, they can grow into larger problems that cause significant downtime and production losses.
That being said, reactive maintenance isn’t without its benefits. For one, a reactive strategy requires no upfront spending and is cheaper than other maintenance strategies in the short term. In addition, you’ll save costs on maintenance for non-essential assets. However, the question you should ask yourself is, despite saving that money in the short term, will you spend more in the long run due to unplanned equipment failure?
Click here to learn more about Preventive Maintenance vs. Reactive Maintenance.
The key components of preventive maintenance
An effective preventive maintenance program leverages a broad mix of activities determined by your budget, staff expertise, equipment specifications, regulatory needs, and unique operational goals. And while each preventive maintenance program may vary by organization, team, or facility, the fundamental components remain the same. Here's a breakdown of the key elements of preventive maintenance:
Proper equipment installation
The first step in preventive maintenance is ensuring you properly install the equipment and its parts. A single out-of-place component can negatively impact asset performance and lead to unplanned downtime. Following manufacturer guidelines for installation can mean the difference between a piece of equipment that functions without incident and one that malfunctions on its first day of use.
Regular inspection
Regular inspections involve a thorough visual examination of your equipment to identify signs of wear, damage, or impending problems. Inspections could range from a simple walkthrough with checklists to detailed inspections using tools like borescopes. These inspections are crucial because they allow you to catch and fix minor issues before they escalate into significant breakdowns, saving you time, money, and headaches.
To get these inspections right, develop detailed standard operating procedures tailored to your specific equipment, train your staff on what to look for, and meticulously document all findings (even small ones) with photos when possible to create a baseline for future comparisons.
Routine testing
Routine testing goes beyond visual inspections. Using specialized tools and techniques like vibration analysis, oil analysis, infrared thermography, and various electrical tests, you can better understand your asset’s internal health. By comparing the test results to established performance benchmarks, you can detect hidden wear, internal component degradation, and misalignment that could lead to unexpected breakdowns.
The key to successful testing is choosing the proper tests for your specific assets, establishing accurate baselines when the equipment operates normally, and accurately interpreting the data (which may require specialized expertise).
Scheduled servicing
Another core component of preventive maintenance is the scheduled servicing of assets. Regularly scheduled proactive maintenance tasks like cleaning, lubrication, replacing worn parts, or adjustments extend equipment life, minimize costly failures, and keep equipment running at peak efficiency.
To get it right, strictly adhere to the OEM's guidelines, keep detailed records of all service work performed on each asset, and monitor equipment post-servicing to fine-tune your maintenance schedules as needed.
Calibration
Lastly, calibration is all about ensuring the accuracy of your measuring instruments, such as gauges, sensors, and meters. It involves comparing your devices’ readings to highly accurate reference standards and adjusting them as necessary to improve accuracy. Readings from improperly calibrated tools can lead to product quality issues, equipment damage, safety hazards, and even regulatory non-compliance.
To properly calibrate your instruments, use reference standards that are much more accurate than the device being calibrated, precisely follow the equipment manual's instructions, thoroughly document pre- and post-calibration readings, and adhere to recommended calibration schedules based on device type, usage frequency, and stability.
Quick example of preventive maintenance
A basic example of a preventive maintenance task is regularly changing the oil in a vehicle according to the manufacturer's recommended schedule. Neglecting the recommended oil change can lead to wear and tear on the engine, potentially leading to catastrophic failure.
Large enterprises have even more to lose when ignoring manufacturer recommendations for maintenance. Replacing or fixing critical equipment earlier than budgeted can significantly impact production, costs, and the bottom line.
Through preventive maintenance, organizations can maximize their investments by slowing down excess asset depreciation, deterioration, and malfunction.
Types of preventive maintenance
PM tasks help anticipate and prevent equipment breakdown. Maintenance technicians should perform proactive maintenance procedures on all parts and components that show signs of age-related failure patterns.
No one type of preventive maintenance is better than the other. But no matter which PM plan you choose, stick with manual and manufacturer recommendations when determining the type of PM your equipment needs.
Preventive maintenance falls into four primary categories:
Periodic maintenance
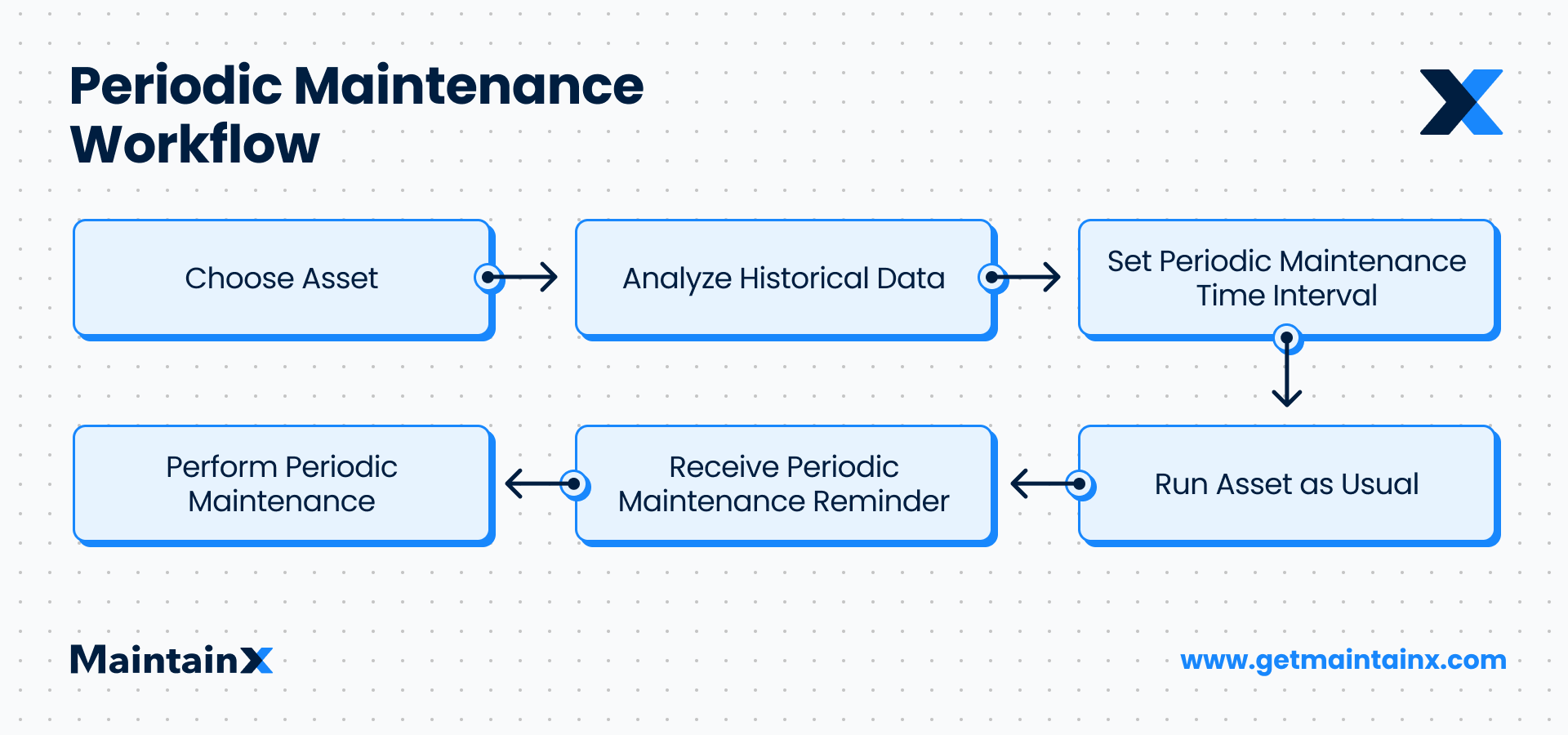
Also known as time-based maintenance, periodic maintenance is regular maintenance work performed at scheduled intervals (i.e., annually, quarterly, monthly, or weekly). Managers should read equipment manuals to determine recommended maintenance schedules. Most manufacturers indicate how often to inspect assets and the average life of each part—for example, performing oil changes on the car’s engine every six months.
Meter-based maintenance
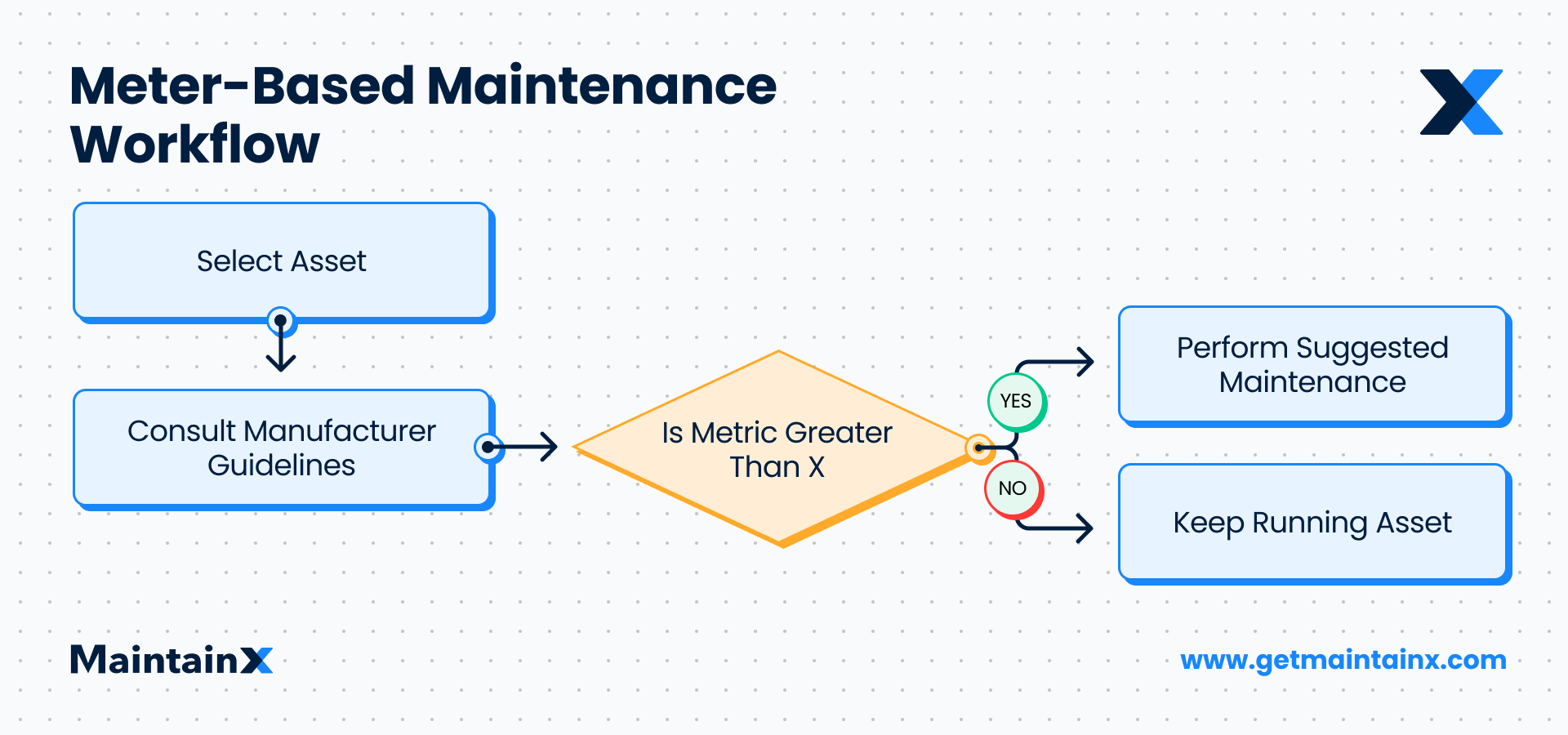
Also called performance-based or usage-based maintenance, this type of preventive maintenance dictates action based on equipment-usage variables or milestones. Preventive maintenance under this approach follows a schedule based on how much use a piece of equipment has experienced. For example, changing a car’s engine oil after every 5,000 miles of driving.
Predictive maintenance
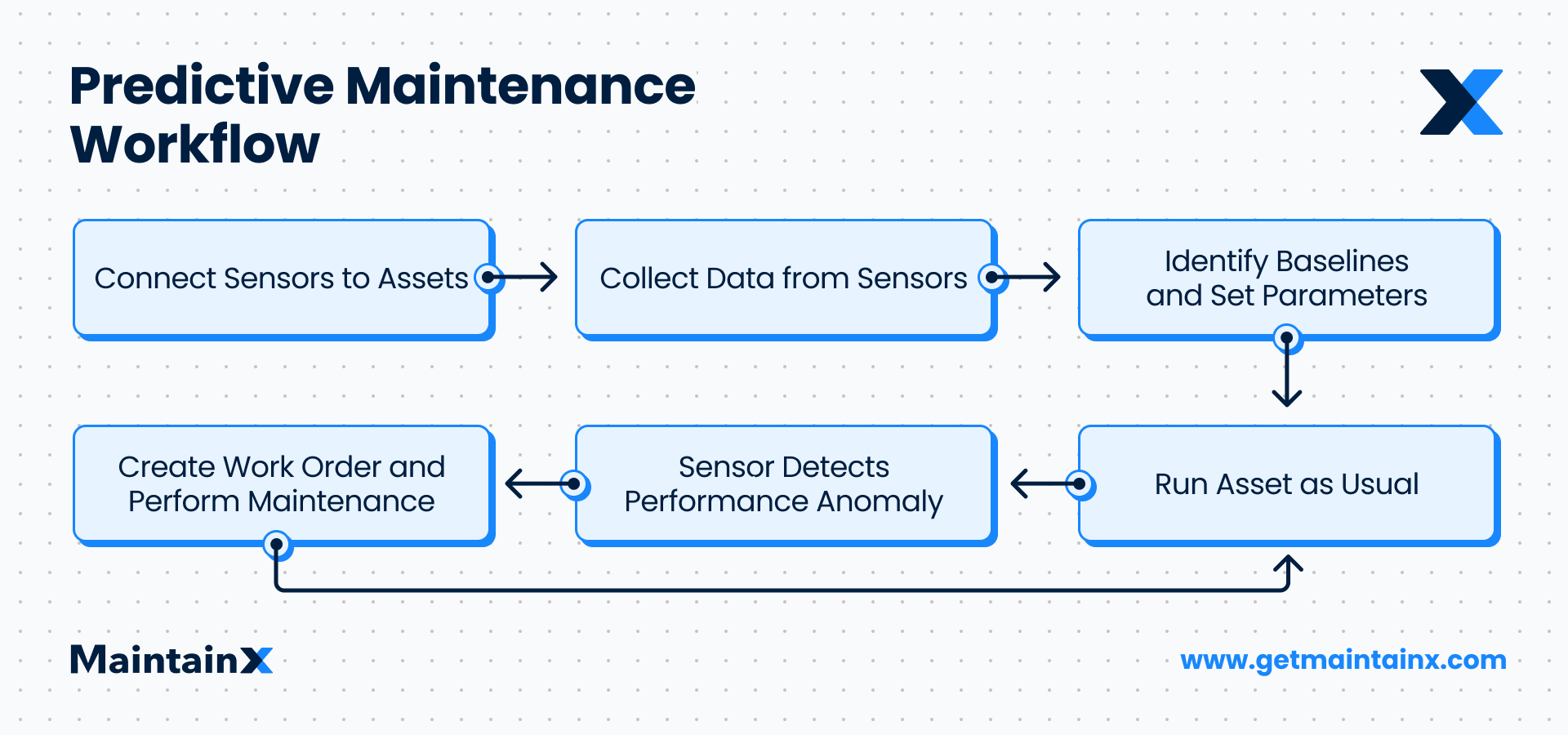
Predictive maintenance (PdM) is an advanced form of preventative maintenance that aims to reduce the number of planned tasks by narrowing the focus to instances where equipment failure is likely. PdM involves analyzing sensor data (such as temperature, vibrations, thermal imagery, etc) related to equipment health. By feeding this sensor data into machine learning algorithms, teams can predict potential failures by comparing an asset’s present behavior with its expected behavior and identifying anomalies.
For example, unusual vibration can indicate excessive wear and tear in a machine’s engine, just as thermal imagery can help point to imminent overheating.
Prescriptive Maintenance
Similar to predictive maintenance, this newer type of maintenance makes decisions based on data. However, prescriptive maintenance uses prescriptive analytics to go beyond predicting failures and explore hypothetical outcomes and how to avoid them.
The smart software collects and analyzes equipment conditions before suggesting specific recommendations designed to prevent equipment failure. For example, instead of simply indicating wear and tear through vibration analysis, prescriptive analytics could go further to specifically recommend either lubrication or a change in parts.
Which type of preventive maintenance is right for you?
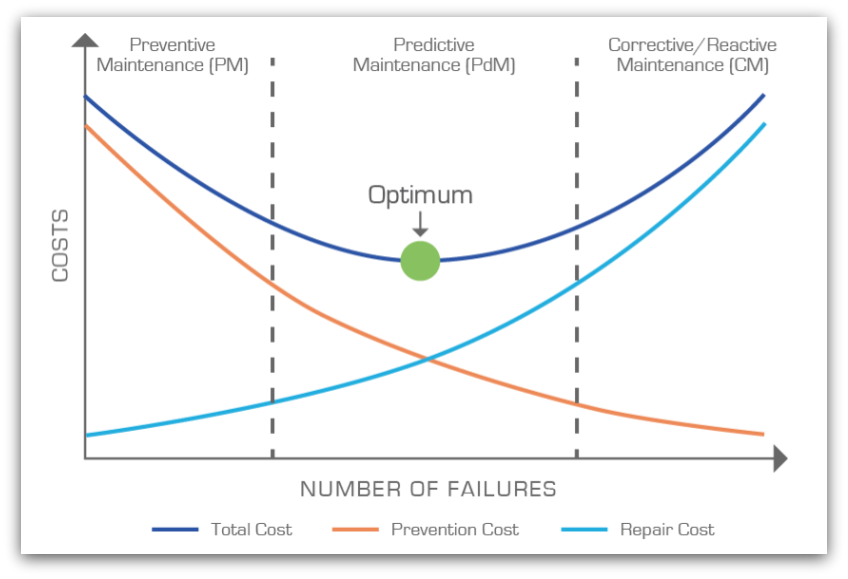
While different preventive maintenance strategies offer unique advantages and disadvantages, most facilities utilize a combination of approaches to optimize asset performance. When developing your preventive maintenance program, consider these key factors:
The assets
Assets' maintenance requirements vary widely, from simple mechanical components to complex electronic systems. Manufacturer guidelines offer invaluable insights into the type of maintenance tasks required (e.g., lubrication, calibration, cleaning), the frequency of these tasks (e.g., daily, weekly, monthly, annually), and special tools or procedures required. Following these recommendations ensures optimal asset performance and helps maintain compliance with industry regulations and safety standards.
Resources
Make sure that you have the resources and budget to support the maintenance strategy you choose. Consider factors like staffing levels, the expertise of your maintenance team, the complexity of your equipment, the cost of the program, and the overall financial impact of potential downtime or repairs before choosing your preventive maintenance program.
Data
Implementing a maintenance strategy is more than just making one choice and sticking to it at all costs. Constantly reviewing and refining your plan based on what's working and what's not is crucial for success. Collect consistent, correct, and comprehensive data to fully understand your preventive maintenance program’s performance. This data-driven approach will help you identify areas for improvement and optimize your maintenance strategy for maximum efficiency and cost savings.
Learn how to choose the right equipment maintenance strategy
Benefits of preventive maintenance
If you’re used to a reactive maintenance strategy, it can be hard to justify the effort required to upgrade to a preventive maintenance strategy—after all, why fix what isn’t broken? However, by sticking with just a reactive approach, you risk missing out on the key benefits of preventive maintenance.
1. Reduced unplanned downtime
Unplanned equipment downtime throws a wrench into any operations. Whether it's a critical asset like a manufacturing machine or an elevator in your building, unexpected equipment failures and breakdowns cause costly delays, frustrations, and potentially even safety risks. Preventive maintenance is your shield against these disruptions. By proactively fixing problems through preventive maintenance activities BEFORE they escalate into significant issues, you ensure your assets are consistently available, maximizing productivity and keeping operations running smoothly.
2. Longer equipment lifespan
Preventive maintenance schedules help you catch problems that might threaten the lifecycle of your assets earlier before they become significant issues. By addressing minor problems upfront, you can extend the lifespan of your assets and delay the need for costly replacements.
3. Reduced costs
In addition to improving asset availability, proactive maintenance also reduces maintenance costs. Detecting problems earlier often means deploying quicker and cheaper solutions to address the issue and avoid costly repairs associated with a full-blown breakdown. You’ll also be able to prevent expensive rush orders for spare parts required to resolve the breakdowns.
4. Increased productivity
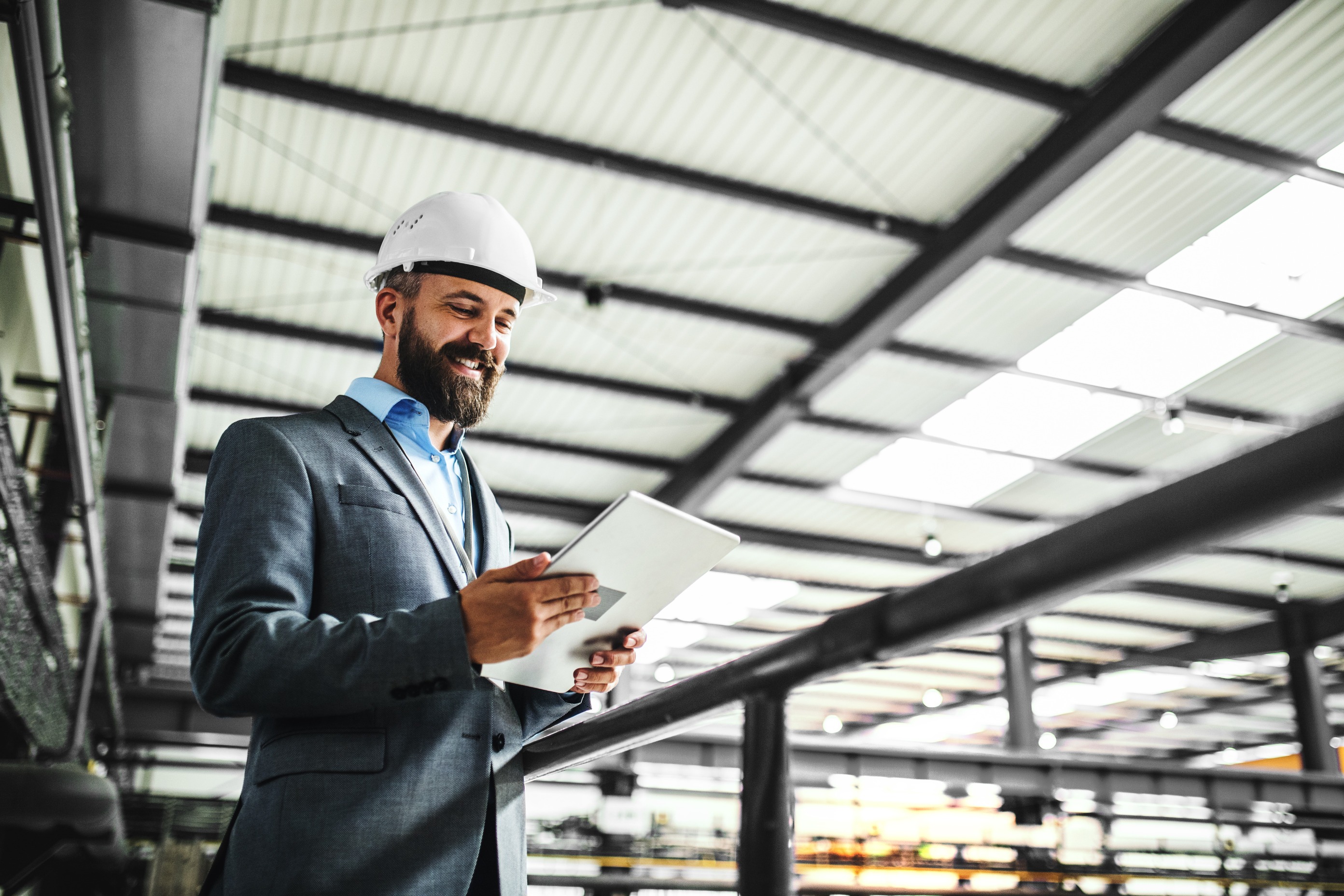
Improved asset uptime means more time spent producing the goods that make you money. While preventive maintenance involves planned downtime for inspections and repairs, the lost production time is far outweighed by eliminating unplanned downtime caused by unexpected breakdowns. By minimizing these disruptions and optimizing your maintenance processes, you can save significant maintenance costs and boost your organization's overall profitability.
5. Enhanced safety
The more often assets are inspected and repaired, the less likely dangerous problems are to occur. Following preventive maintenance schedules reduces the risk of unexpected breakdowns, safety and health hazards, and liability lawsuits. Your staff members will be less likely to suffer accidents due to defective equipment. Similarly, an excellent preventive maintenance process guarantees the quality of your products won’t be compromised due to any asset malfunction.
Disadvantages of preventive maintenance
Despite the benefits of preventive maintenance we’ve highlighted above, this strategy doesn’t come without its unique challenges and limitations. These include:
1. Higher upfront costs
Let’s face it: preventive maintenance isn’t cheap to get started with. It certainly requires more upfront investment than reactive maintenance. You may need to invest in new tools or equipment, train and educate your maintenance team, or stock up on critical spare parts. Plus, when your machines are taken offline for planned downtime, it means less production time and lost revenue for the business. But here’s the thing: these maintenance costs are an investment for the future.
Think of it like getting your car tuned up regularly—it might cost more upfront, but it saves you from costly repairs down the road. The same applies to your business assets. Proactively inspecting and maintaining your equipment can prevent expensive downtime and save more in the long run.
2. Increased labor requirements
With more work orders to complete as part of a preventive maintenance program, you’ll likely need to hire and train additional team members. And the current skilled labor shortage and rising inflation can make it even more difficult and costly to get started with a preventive maintenance program.
To alleviate the labor requirements, you can leverage tools like preventive maintenance software to automate routine tasks, upskill your existing workforce, prioritize PM for only critical assets, or maximize productivity through optimized maintenance scheduling.
3. Time-consuming
Transitioning to a preventive maintenance program can initially feel like more work, and in some ways, it is. Regularly inspecting complicated assets, performing routine maintenance tasks, and juggling complex maintenance schedules can be tedious and time-consuming. Even businesses with simple machinery may feel the burden when getting started with preventive maintenance.
However, modern CMMS software like MaintainX can streamline these processes significantly. You can save valuable time and resources by automating routine tasks like generating work orders or tracking inventory, optimizing maintenance technician schedules based on skillset and location, and providing data-driven insights to prioritize critical assets.
4. Tricky to organize
Building a PM program without a centralized orchestration system in place can lead to disaster. While paper-based systems may suffice for smaller facilities with limited assets, they quickly become unwieldy and prone to errors as your operations scale. Disorganized schedules, overlooked tasks, and lost work orders can render your preventive maintenance program ineffective and negatively impact your bottom line.
With a modern computerized maintenance management system (CMMS) like MaintainX, you can easily centralize your work orders, streamline workflows, optimize maintenance schedules, and gain valuable insight into your asset performance.
Industries that benefit from preventive maintenance programs
Any organization with assets to maintain can benefit from preventive maintenance schedules. Here are examples of some industries and how they use preventive maintenance.
Hotels: Preventive maintenance in hotels involves the regular upkeep of a hotel’s facilities and assets. This includes maintenance of guest rooms, physical assets throughout the hotel, HVAC and electrical systems, elevators, swimming pools, and more.
Fleet management: In fleet management, preventive maintenance involves routine work done to ensure all vehicles remain safe to use and in good working condition.
Property management: Property managers oversee preventive maintenance programs to ensure electrical, plumbing, and HVAC systems remain in working order 24/7. Such facilities could include everything from housing complexes to car wash outlets.
Governments: Government departments and agencies undertake preventive maintenance activities to keep public facilities—buildings, spaces, roadways, statues—functioning optimally.
Other examples include schools, country clubs, the oil and gas industry, and much more.
How to implement a preventive maintenance program
To successfully implement a preventive maintenance program, follow the following steps:
Audit your equipment
Start with a thorough audit of your assets. Note how old each asset is, how frequently you use it, and other crucial information like recent breakdowns and how often they occur. Identifying why your assets are breaking down can help you focus your preventive maintenance efforts on mitigating those issues first.
Establish goals and priorities
Next, identify your maintenance goals for each asset and establish priorities. Are you looking to save money by reducing downtime? Increase asset reliability? Improve asset management? Consult OEM guidelines and industry regulations for the frequency and type of maintenance you need to perform for each asset. A criticality analysis can help you identify the most crucial assets to your business to prioritize first.
Create repeatable workflows and KPIs
Break those goals down into repeatable workflows. Outline the specific tasks your team should perform on each asset and the frequency with which they should be completed. Standard operating procedures, checklists, and templates are vital here, as they help ensure teams don’t miss crucial steps.
Next, determine specific key performance indicators (KPIs) you will track to measure program performance. From MTBF to MTTR, monitoring your KPIs helps you stay on top of your maintenance efforts by identifying what works and what doesn’t.
Implement the right technology
Preventive maintenance requires repeated and consistent work, and the right technology can be the difference between maintenance technicians completing all tasks on time and work falling through the cracks.
When evaluating software to manage your preventive maintenance program, make sure it has all the features you need, like work order management, asset management, inventory management, reporting and analytics, a native mobile app, etc… MaintainX CMMS, for example, is an all-in-one work management platform that streamlines preventive maintenance scheduling, simplifies work order creation and assignment, provides real-time visibility into asset health and maintenance history, and empowers technicians with a mobile-first experience.
Be sure to get buy-in from staff and work closely with frontline workers to train them on the new technology to drive adoption and usage. This will help your organization reap the full benefits of preventive maintenance.
Schedule work orders
The next step is to create and schedule work orders for the actual PM activities. Again, with the right CMMS, you can do this in advance and only need to do it once for some tasks. In MaintainX, for example, if an asset requires weekly lubrication, you only need to create the work order once and automatically set it to repeat weekly.
Analyze results
Continuous improvement is vital for effective preventive maintenance. Monitor your maintenance data and track your selected KPIs to measure your program's performance. This data will allow you to double down on what’s working and eliminate any initiatives that aren’t. The right technology also makes a big difference here. MaintainX’s reporting feature automates much of this work, analyzing your data to generate actionable insights.
MaintainX makes preventive maintenance a breeze
Looking to get started with preventive maintenance? You don’t have to do it alone. MaintainX CMMS helps you mitigate the problems and reap the benefits we’ve highlighted in this article.
Key features to support your preventive maintenance program include:
- Automated PM Scheduling
- Customizable Work Order Templates
- Mobile-First Design
- Asset Management
- Parts and Inventory Management
- Real-Time Collaboration
- Powerful Reporting and Analytics
- And a whole lot more.
Don’t just take our word for it—check out case studies to learn more about customer experiences, and book a tour to see for yourself.
Preventive maintenance FAQs
How do I prioritize preventive maintenance activities?
To prioritize preventive maintenance work, rank assets based on their criticality for production, safety, and compliance, as well as the potential cost of repair or replacement. In addition, consider historical data and manufacturer recommendations when building out a schedule.
What are the risks of neglecting preventive maintenance?
Neglecting PM can lead to equipment failures, increased downtime, higher repair costs, and reduced equipment lifespan, and safety hazards. In addition, teams risk safety hazards and decreased output.
What are some challenges to implementing preventive maintenance strategies?
Challenges to implementing preventive maintenance include resource allocation, data accuracy, resistance to change, and finding the right balance between proactive maintenance and reactive maintenance. Finding the right tools and software to execute a proper preventive maintenance strategy is also a significant challenge.
What is the PM to breakdown ratio?
While there’s no perfect ratio of preventive to reactive maintenance, experts recommend adopting an 80/20 approach (based loosely on the Pareto Principle), where 80% of maintenance activities focus on proactive work and the remaining 20% on reactive work.
What is the difference between preventive vs reactive maintenance?
Preventive maintenance involves scheduled, routine tasks aimed at to preventing equipment failure while reactive maintenance focuses on restoring equipment to working condition after unexpected failures happen.
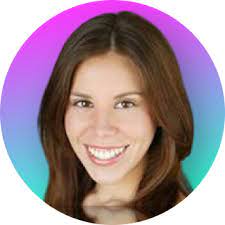