Precision maintenance is a strategy in which maintenance tasks are completed according to well-defined standard operating procedures (SOPs). This ensures operational reliability regardless of who completes a task.
What Is Precision Maintenance?
Precision maintenance is best thought of as a cultural framework for maintaining reliable, consistent, and efficient equipment results. Unlike preventive maintenance, precision maintenance is not a scheduling methodology but an organizational philosophy of “best practices.”
For this reason, it’s important to recognize that what may be considered precise for one organization may well be entirely different for another. Depending on the industry, and the type of equipment involved, ideal maintenance protocols will vary.
The cornerstone of a successful precision maintenance program is documented standard operating procedures (SOPs) that leave no room for error. Clearly articulated SOPs, and proper team training, guarantee consistent task outcomes regardless of who is completing a work order. Precision maintenance SOPs should be detailed, accessible, and up to date.
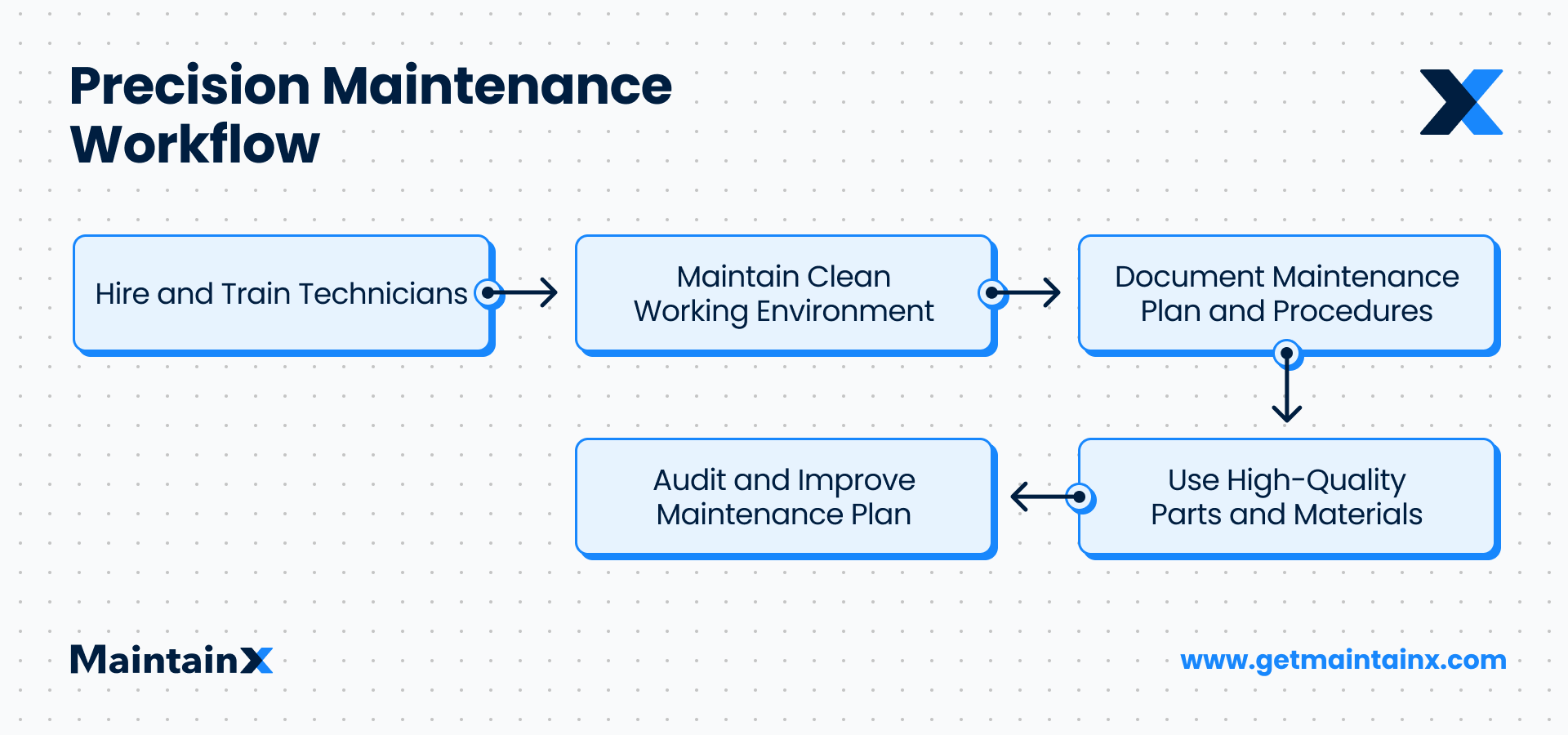
Why Does Precision Maintenance Matter?
In the absence of clearly defined SOPs, technicians might complete assigned work orders differently from one another. Varying work experiences, education levels, and skill levels may yield inconsistently approached projects, which may produce undesirable results.
For example, you may notice that a particular asset often malfunctions during Technician A’s shift, but never during Technician B’s shift. Upon further examination, you learn the workers are approaching the asset’s scheduled maintenance differently. Precision maintenance seeks to eliminate such inconsistencies by establishing precise standards for every type of maintenance project and work role. Essentially, precision maintenance is a quality assurance process that guarantees tasks are always completed in the best possible way.
The Benefits of Precision Maintenance
In addition to reducing downtime, precision maintenance plans can:
- Create a positive maintenance culture
- Ensure the longest possible equipment lifespan
- Increase production via machine reliability
- Create a team of skilled and highly-trained employees
- Continuously improve process efficiency
- Dramatically increase asset reliability
- Reduce the risk of equipment failures (and resulting downtime)
- Keep maintenance and operational costs low and predictable
Precision Maintenance Program Requirements
As previously mentioned, precision maintenance programs may vary in terms of approach. However, here are a few common requirements:
- Skills and Training: Maintenance technicians must have the necessary skills and training to follow maintenance procedures with a high level of precision.
- Proactive Maintenance: To enjoy the benefits of a precision maintenance program, it’s important to have a robust preventive or predictive maintenance program in place. Make sure you’re not running behind schedule for your planned maintenance works.
- Detailed Procedures and Workflows: Detailed workflows and standard operating procedures are necessary for each maintenance task, as well as precise standards for their execution. Employees need to know how to find and use maintenance documentation and be able to follow each step to the letter. The correct fits, tolerances, torques, and tensions all need to be described in the relevant procedures and leave no room for misinterpretation.
- Up-to-Date Procedures: Systematically review all procedures to make sure they’re up to date. Whenever there’s an update—because of upgrading equipment, improving maintenance procedures, or receiving updated maintenance information from equipment manufacturers—make sure that the change is reflected in the related documentation straight away.
- Maintenance Tools Calibration: All tools and equipment necessary for maintenance need to be properly calibrated.
- High-Quality Materials: All maintenance materials, such as lubricants, spare parts, and tools should be of high quality. Only purchase the correct spare parts per the manufacturers’ specifications; avoid cheap replacements.
- Precise Shaft Alignment and Correct Balance: Ensure that precise shaft alignment is maintained, and the balance between rotating elements is correct.
- Correct Operating Temperatures: Maintain correct operating temperatures at all times and for all machines. To do so, perform frequent temperature checks. Implementing an automatic alert system for abnormal temperature readings is an excellent solution.
- Root Cause Analysis: Do a root cause analysis for each failure and make sure that the reasons for the failure are addressed and will not be replicated.
- Document Past Maintenance Work: Document maintenance as it is performed, to have a clear overview of what has been done, as well as the results of each improvement.
Another popular component of precision maintenance is reducing machine vibration levels as much as possible. Excessive machine vibration is often a sign that a piece of equipment is not functioning correctly and that it may soon break down and need expensive repairs.
What Is the Main Purpose of Maintenance?
Maintenance guarantees that facility assets are fully operational at all times and perform according to industry standards. It ensures that all equipment functions optimally, is safe to use, and meets local and national environmental protection guidelines and requirements. Maintenance is a key element in maintaining all production utilities in good working condition or repairing them to restore their full serviceability.
Maintenance includes the inspection, testing, servicing, repairing, and replacing of all necessary equipment, machine parts, or infrastructure. Thanks to precision maintenance, facilities can operate at their optimal capacity while minimizing the financial burden of unexpected downtime or the breakdown of a piece of equipment. When implemented correctly, it can greatly improve the quality of maintenance, thus reducing costs and downtime.
How Does Precision Maintenance Reduce Downtime?
Facility equipment must be correctly maintained to function at maximum efficiency and capacity. The best way to achieve this objective is by combining a solid predictive or preventive maintenance program with the consistent execution of precision maintenance principles.
Precision maintenance leads to improved equipment reliability and lessens the risk of asset failure in four ways:
- Extends Asset Life and Uptime: Maintenance teams can extend the lifespan of assets by always using high-quality parts, tools, and lubricants. This dramatically reduces the risk of unexpected breakdowns and downtime.
- Reduces the Need for Reactive Maintenance: Although precision maintenance cannot completely eliminate the need for reactive maintenance, it can greatly reduce the number of instances when reactive maintenance is required. This helps to limit maintenance costs and to operate within tight budgets.
- Improves Performance: Equipment can only function at optimal capacity when correctly maintained All maintenance and facility managers are subject to the same pressures to sustain high output levels at all times, regardless of the specific sector or industry. Precision maintenance improves machine reliability and helps keep production at optimal levels, with a minimum amount of downtime necessary.
- Eliminates the Likelihood of Maintenance Overtime: Precision maintenance allows managers to predict project timelines with greater accuracy. When maintenance procedures are properly documented, and technicians follow SOP checklists, it’s easy to predict how long routine tasks will take. This means that maintenance work will not take longer than expected and scheduled downtime will not need to be extended.
Precision Maintenance Examples
Precision maintenance can be paired with many different types of maintenance programs and schedules.
Here are a few examples of precision maintenance in action:
- Using only high-quality tools, spare parts, and lubricants and always storing them correctly
- Maintaining an environment that is clean and 100% contamination-free
- Frequently checking operating temperatures to make sure they stay within required ranges
- Maintaining low machine vibration levels at all times
- Ensuring the precise alignment of all rotating parts
- Systematically applying the correct torque levels for each nut of a piece of equipment
How to Start a Precision Maintenance Program
Launching a precision maintenance program at your facility may feel like a daunting task, especially if your team has relied heavily on reactive maintenance in the past. However, it’s worth the effort. Follow these seven steps to transition to precision maintenance.
1. Conduct a Team Skill Assessment
Assess and analyze any skills gaps that your organization needs to overcome. What additional skills must technicians acquire to perform all maintenance tasks with high precision? Assess each employee’s skills, knowledge, and aptitude for following SOPs when completing assigned tasks. This will allow you to better understand the training needs of your team and concentrate your efforts. Emphasize that the assessments aren’t being done to penalize employees, but to help them strengthen their capabilities. Results will likely range from minimal to high needs for improvement.
2. Create a Culture of Continuous Improvement
Commit to creating a culture of excellence and ongoing improvement. Clearly communicate the strategic importance of implementing a precision maintenance program. Having everyone on board by investing in your workers’ skills will guarantee that each employee understands their role in achieving the high-level goals of the organization.
3. Invest in Maintenance Personnel Training
Enlist the support of maintenance managers and experienced technicians to perform hands-on training sessions. Here they can teach precision maintenance procedures step-by-step while replicating real-world situations. According to Ian McKinnon, the founding principal of Reliability Solutions, hands-on training is crucial for maintenance personnel to fully understand the value of performing precision maintenance.
Several precision maintenance training programs are available:
- SKF offers instructor-led training programs and eLearning courses.
- Louisiana Delta Community College offers Precision Maintenance Training, developed in partnership with Reliability Solutions.
- The Advanced Manufacturing Institute at Polk State Corporate College proposes a 5-day Precision Maintenance Program.
- The Reliability and Maintainability Center at The University of Tennessee offers an RMIC® certification for Practitioners in Precision Maintenance.
- The Mobius Institute offers certifications in Reliability & Performance and Vibration Analysis, also available as online courses.
4. Identify High-Maintenance Equipment
Some machines require more routine maintenance than others. They may break down more often due to intense usage or require more frequent servicing based on manufacturers’ recommendations.
Prioritize tracking equipment that is:
- Expensive
- Crucial to productivity
- Prone to high levels of vibration.
Use a CMMS to track all maintenance work in order to identify your highest-maintenance equipment over time. These assets are most likely to benefit from precision maintenance and deliver the highest ROI.
5. Create Detailed Workflows and Procedures
Create clear, step-by-step procedures and workflows. Procedures should be highly detailed and leave no room for interpretation. Document all requirements, including torque, pressure, and alignment numbers. Be sure to detail each process so that maintenance technicians never have to guess.
Standard operating procedures should be up-to-date, well-organized, and understandable for everyone. You also need to document all completed maintenance work in order to further analyze your results, streamline processes, and improve procedures.
6. Invest in a User-Friendly CMMS
A user-friendly CMMS can provide full visibility of your maintenance work, asset history, and opportunities for cost savings. Features you should prioritize include:
- User Experience: If it’s not easy to navigate, nobody will use it.
- Instant Messaging and Chat: Workers should be able to communicate with each other within work orders.
- Recurring Work Order Scheduling: It’s essential.
- KPI Tracking: KPI tracking will allow you to measure your results and know which elements need improvement.
- User-Friendly Digital Checklists: The best apps provide drag-and-drop templates that can be customized to meet your needs.
7. Conduct Progress Reviews
Precision maintenance requires continuous involvement. Measure results and frequently assess key performance indicators (KPIs), such as:
- Equipment failure
- Asset life
- Operational costs
- Downtime
- Equipment performance
This way, you’ll have enough data to analyze what procedures are working and what can be improved. Strive to continuously improve SOPs and keep digital checklists up to date. Additionally, assess the progress of each maintenance technician with one-on-one progress reviews. This shows that you value each team member and are willing to invest in their skills and development.
What Are the Other Types of Maintenance?
Here are five common programs often used in combination with precision maintenance:
- Corrective Maintenance: Corrective maintenance is executed once a breakdown occurs. The goal is to return the equipment back to working order as soon as possible via repairs or replacements. Corrective maintenance is necessary because unexpected problems will always occur. It is even preferable in some cases for inexpensive, non-crucial parts.
- Preventive Maintenance: Preventive maintenance is the scheduled inspection and maintenance of assets. Its main objective is to maintain optimal equipment performance, fix issues before they become problems, and reduce the need for corrective maintenance. Preventive maintenance minimizes operational costs and reduces the risk of unscheduled downtime.
- Predictive Maintenance: Predictive maintenance measures the condition of a given piece of equipment to predict its lifespan and prevent failure. It heavily relies on sensor monitoring and data analysis and has been used in facilities since the 1990s. Predictive and precision maintenance are highly compatible, and both use similar techniques, such as vibration analysis, thermography, energy use analysis, and more.
- Predetermined Maintenance: In predetermined maintenance, maintenance technicians follow manufacturers’ guidelines on how to plan maintenance tasks and schedule them accordingly. This is an imperfect strategy, as it is based on the analysis of existing statistical data (e.g., on the mean time to failure), and for newer equipment, the data may not be complete.
- Condition-Based Maintenance: Condition-based maintenance is a strategy that monitors equipment performance in real-time to spot impending failures. It has a high implementation cost, as it uses sensors and spot readings. However, it is a rather economical solution in the long run, as it helps significantly decrease the risk of failure and downtime. The terms condition-based maintenance and predictive maintenance are sometimes used interchangeably. Condition-based maintenance can be used in combination with precision maintenance.
The History of Precision Maintenance
Finally, you may be wondering about the history of precision maintenance. Dr. Wernher Von Braun pioneered the philosophy at NASA during the 1960s. With the help of his team, Braun discovered that reducing vibration had a significant impact on the life cycle of bearing parts.
The team found that reducing vibration by 20 percent increased the lifespan of bearing parts twofold. The term, “precision maintenance,” was later coined by Ralph Buscarello, who also understood the destructive power of vibration and the benefits of its reduction.
Thanks to his devotion to educating maintenance professionals, we now understand the value of vibration reduction. Based on their findings, precision maintenance nowadays uses diverse detection and analysis methods, such as vibration monitoring, energy use analysis, thermography, and more. In the past decades, maintenance managers have used precision maintenance worldwide to improve asset reliability and minimize the risk of downtime.
Conclusion
Precision maintenance is a strategic approach in which maintenance tasks are performed consistently, accurately, and with a high level of precision. To succeed, management must document SOPs, eliminate maintenance personnel skills gaps with training, and track KPIs. The rewards of a strategic precision maintenance program are reduced downtime, improved asset performance, reduced costs, and greater equipment predictability.
See MaintainX in action