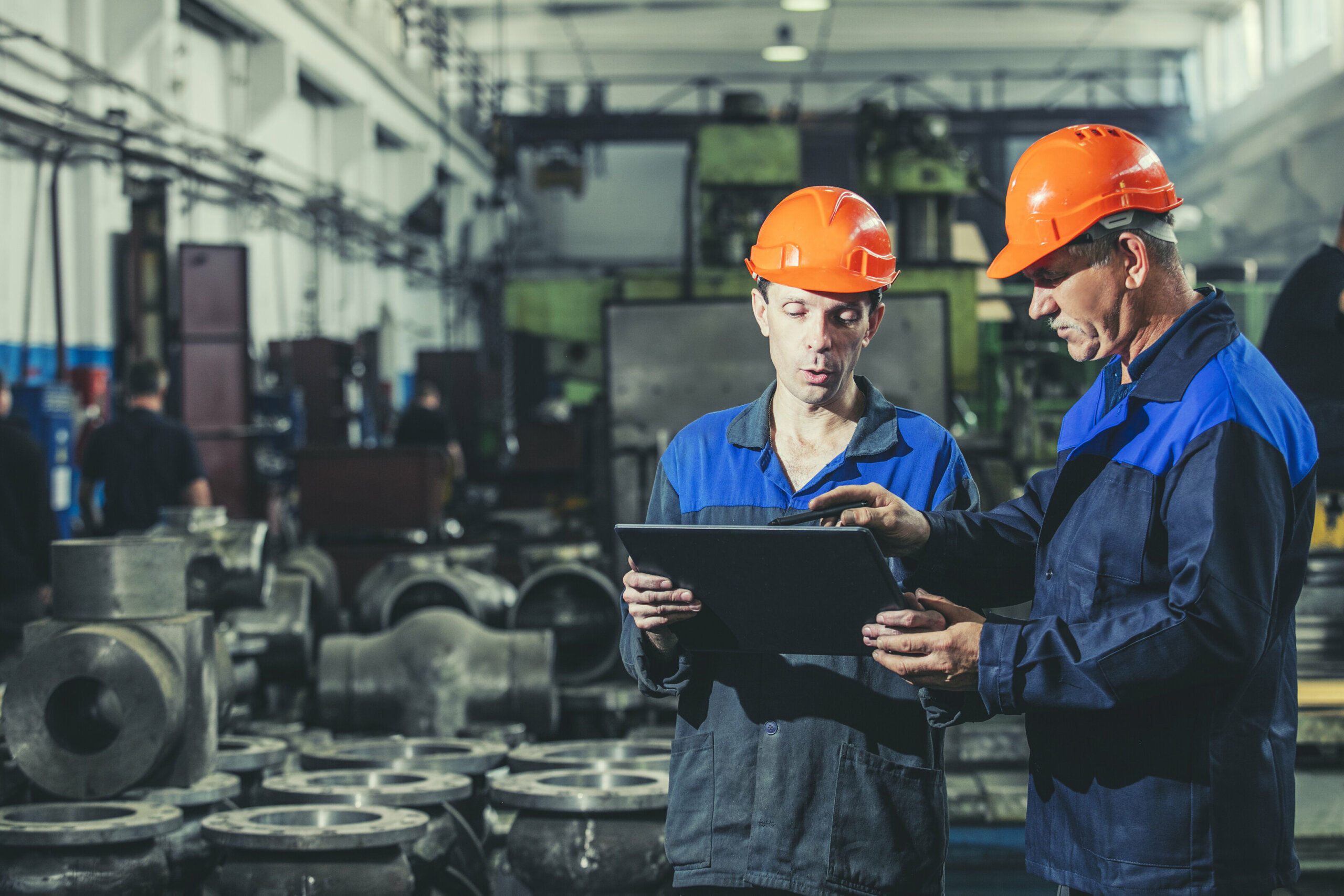
If you want your company to be successful, you need to deliver consistent results for your customers every time. That is where standard operating procedures, or SOPs, can be helpful. Even if you don’t have the best product in the industry, you can still generate significant revenue as long as your product is reliable.
This article reviews how SOPs help you create and maintain efficient, safe, and reliable preventive maintenance programs and environments for your customers and employees.
What Is a Standard Operating Procedure?
A standard operating procedure is an official document that provides detailed, step-by-step instructions on how to perform a specific task. SOPs can be used day-to-day or according to set schedules Taking the time to implement SOPs is key to creating robust workflows and efficient processes.
Organizations with SOP documents in place avoid real-time miscommunication, streamline repetitive processes, codify business processes, and provide consistent results for their customers, stakeholders, and clients.
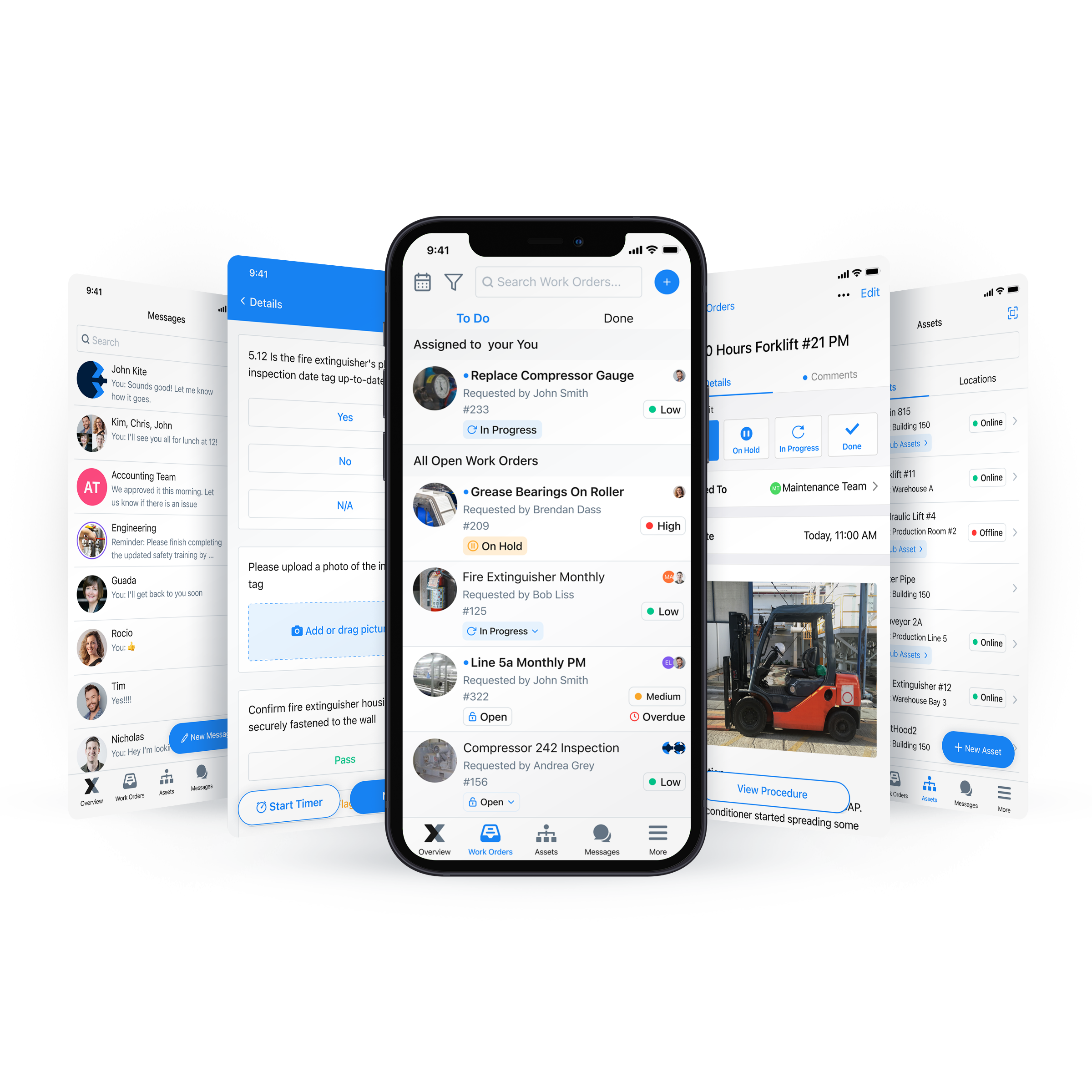
Who Uses Standard Operating Procedures?
Manufacturing
Mass production in the manufacturing industry includes everything from airplane parts and car tires to semiconductor chips and cleaning supplies. The manufacturing industry relies on standard operating procedures to produce consistent results every time.
These days, the manufacturing industry relies on automation. And maintaining this automation is possible because effective and efficient SOPs are continually reviewed and fine-tuned.
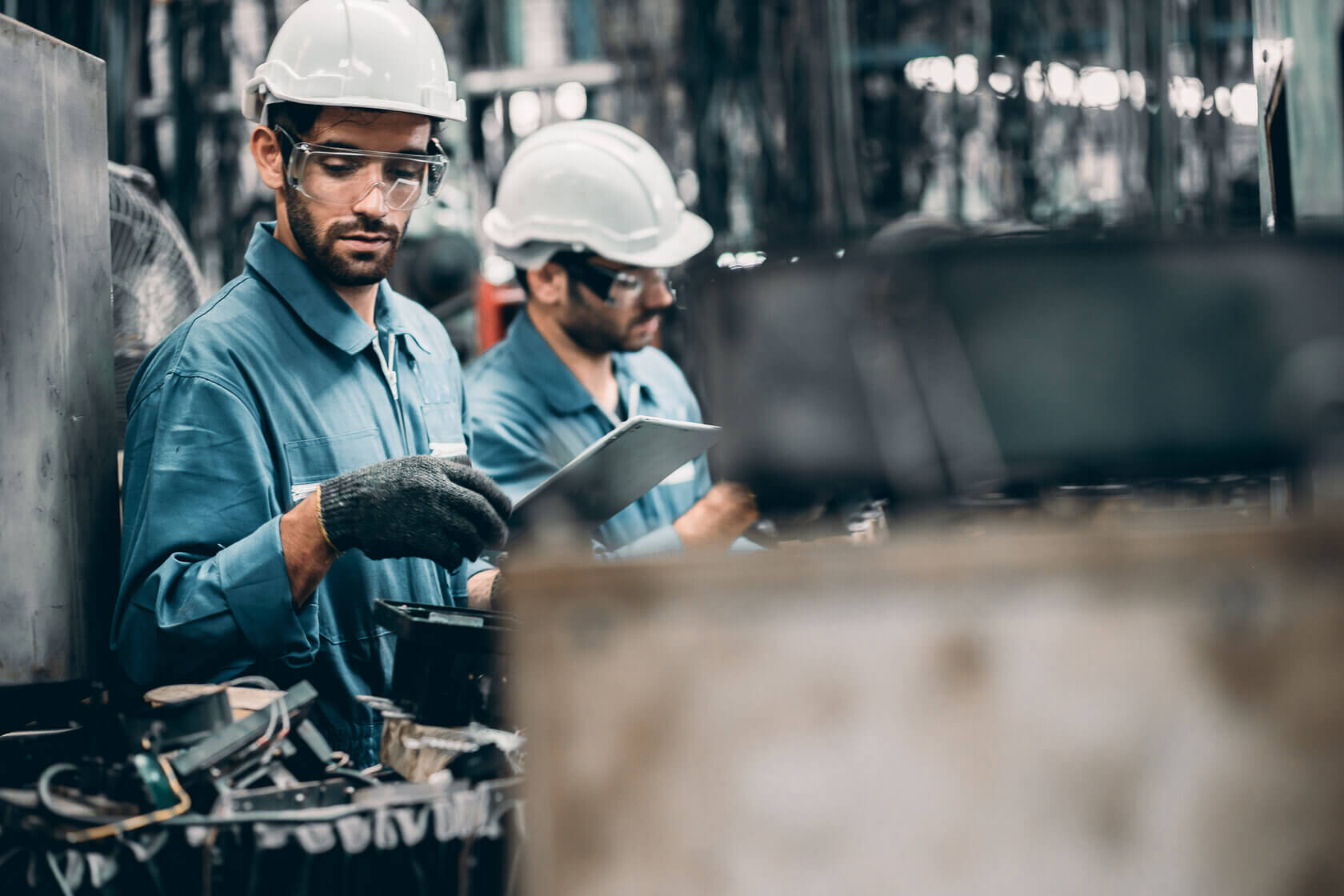
Automotive Industry
When you take your car to the shop for either routine maintenance, condition-based maintenance, or even reactive maintenance, there is a good chance that your mechanic uses standard operating procedures to make sure your car runs smoothly and safely. When your car leaves the shop or dealership after a maintenance check, you should feel comfortable knowing it runs as it should. Fleet maintenance is another good reason to implement SOPs.
Food Service Industry
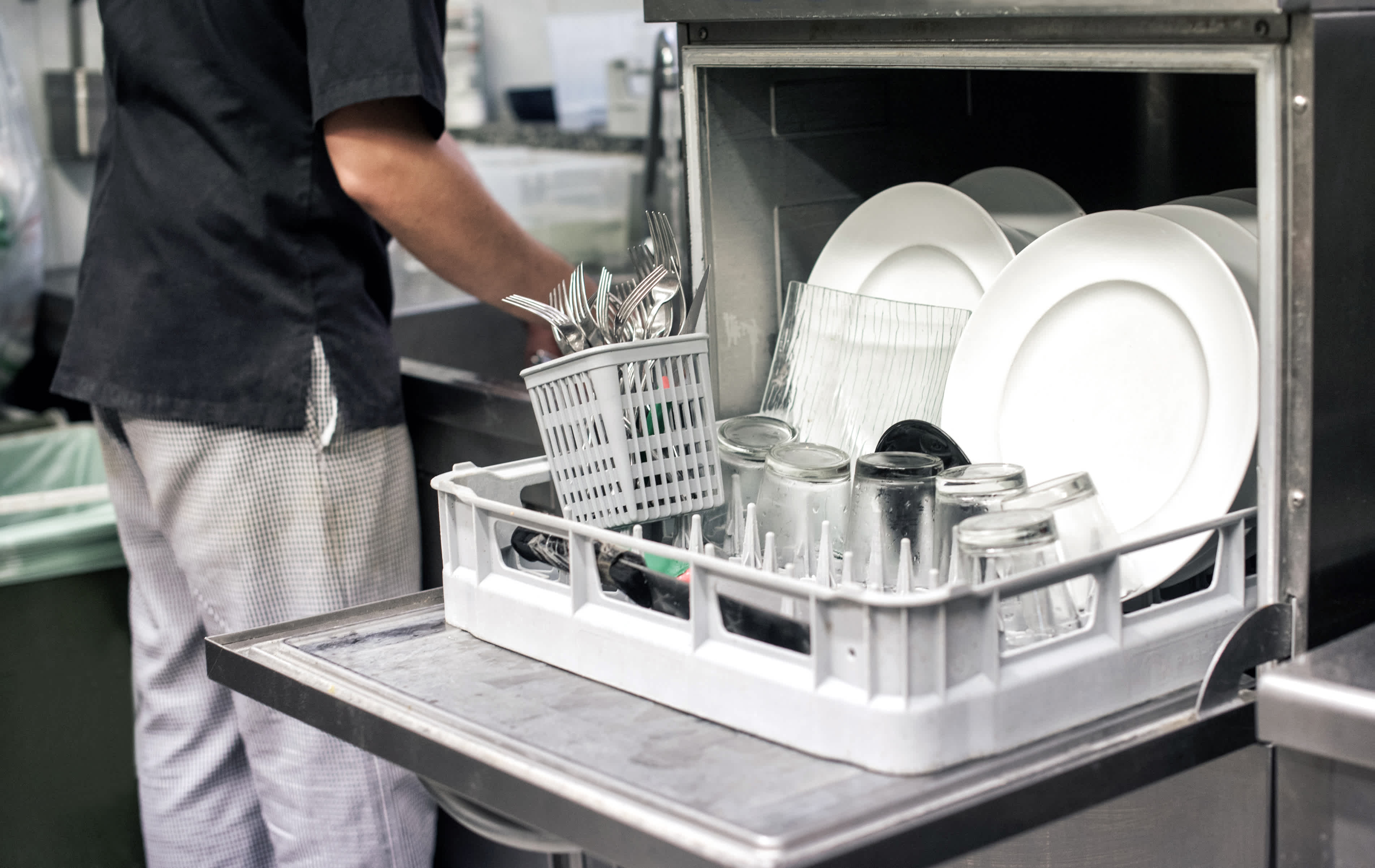
In food service, safety is paramount. Standard operating procedures prevent food-borne illnesses, ensure restaurant safety, and adhere to FDA regulations to meet crucial inspections. Regulatory SOPs, for example, dictate how long and at what temperature foods need to be cooked, how long food can be stored and at what temperature, and even how hot the water needs to be for dishwashing and sanitizing.
Support Centers
Quality-control standard operating procedures lay out step-by-step processes for responding to customer needs, troubleshooting technical snafus, and even completing sales. Typically, people who work in technology follow standardized instructions and workflows that walk them through exactly how to respond per user situation.
In addition, the project management team may perform quality assurance audits from time to time. This is one reason why call center phone calls are recorded. In addition, a standard operating procedure may be revised post audit to better respond to customer needs.
“Overall, the consistent use of SOPs creates a streamlined, cost-effective way to grow a business and its human capital, and lays a foundation for a rock-solid virtual culture for a distributed workforce.”
Forbes
Simple Steps to Create SOPs
If you want to ensure that your business has high-quality standard operating procedures in place, follow these simple steps:
1. Focus on the Process
Write your standard operating procedures in easy-to-follow steps. Use images and photographs to provide visual direction if possible.
2. Keep SOPs Simple
Even though you don’t want to omit important details, avoid wordiness and jargon. The shorter the document, the better. If it is too long, essential steps may get overlooked. The best SOPs include easy-to-follow SOP templates that workers can follow with minimal-to-no guidance from other team members
3. Write to Your Audience
This is simple: write SOPs for the technicians who will use them. Maybe you don’t need to explain everything–like turning the screwdriver to the right to tighten the screw and to the left to loosen it. But you need to ensure that a range of users can understand and execute the SOP on the spot with the tools they have.
4. Create SOPs for Specific Tasks
As you write your standard operating procedures, stick to the specific task or procedure. That is, avoid scope creep. Define the skills necessary to complete the SOP efficiently and effectively. Assign the SOP to the workers with the roles and responsibilities necessary to understand the outlined process. Test your SOP to ensure the designated techs can follow the instructions and complete the task.
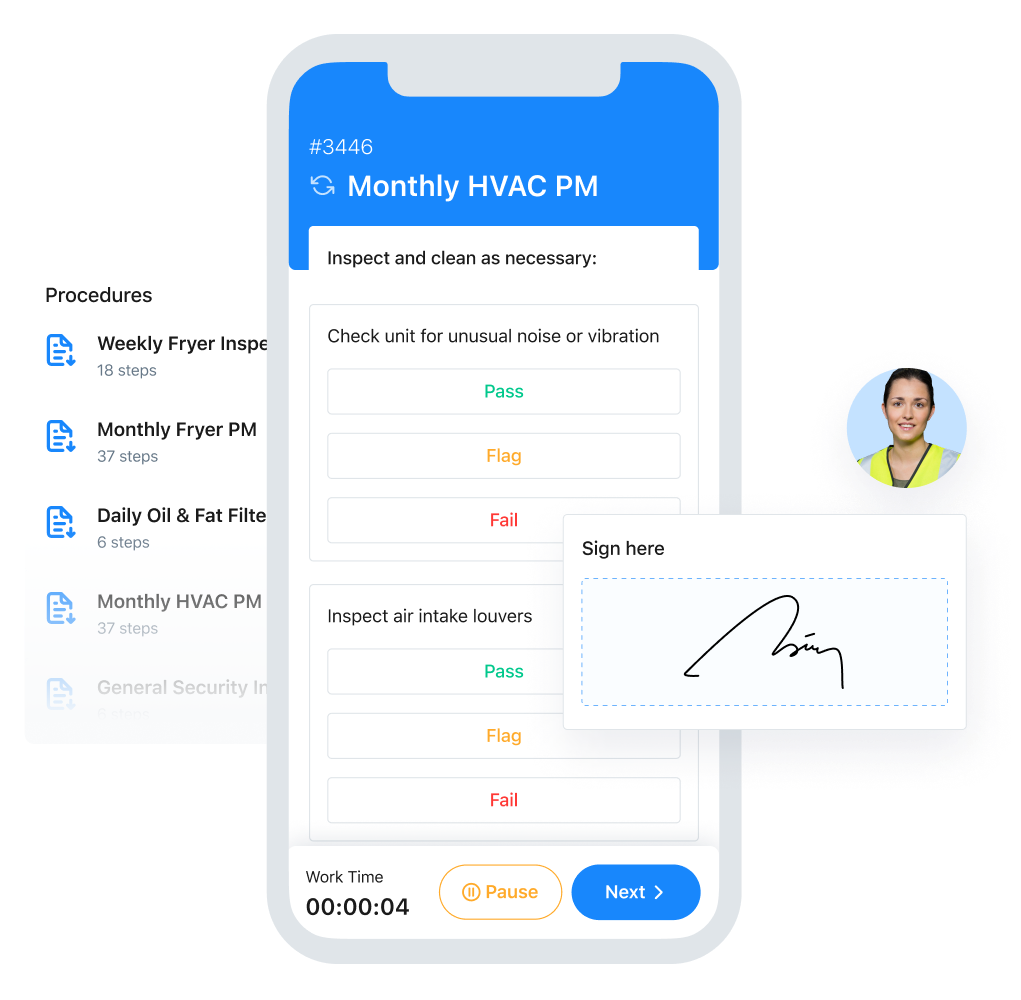
Benefits of Standard Operating Procedure
Reduce Mistakes and Mishaps
Well-written and tested standard operating procedures reduce mistakes, keep employees safe, and increase efficiency.
Reduce Regulatory Liability
The best standard operating procedures reduce equipment downtime and your regulatory liability. When creating and testing your document, follow industry regulations, such as those required by OSHA. This way, during inspections, you can feel confident that everyone has followed standard procedure. Furthermore, if you use a computerized maintenance management system like MaintainX, you have a real-time digital audit trail.
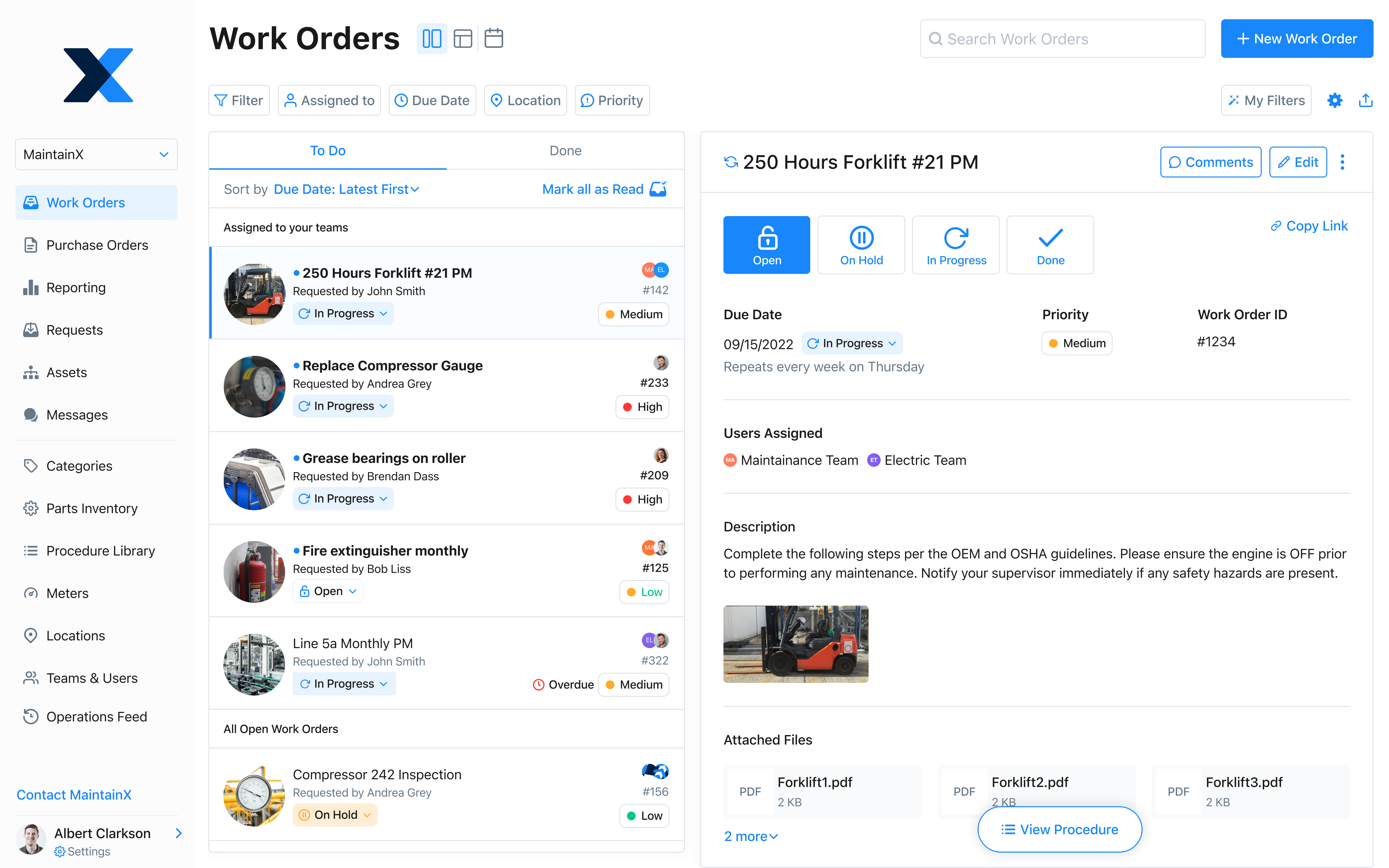
Deliver Consistent Results
In today’s ultra-competitive environments, you need to keep your customers happy. Therefore, your results need to be reliable and consistent. With standard operating procedures, the results should always be the same no matter which technician works on the project.
Save Time by Avoiding Redundant Steps
Operations managers are always looking for ways to reduce time on task and increase uptime. With SOPs, the best way is to eliminate redundancy. Tasks should not need to be completed twice. Make it easy to deliver consistent results by finetuning your SOPs.
Digitize Your SOPs with MaintainX
Check out MaintainX’s Global Procedure Library for SOPs across industries. And our digital work order feature provides a ready template for all your standard operating procedures, from proactive to reactive maintenance. By digitizing your SOPs, your company can move closer to the 80:20 preventive to reactive maintenance best-in-class indicator of excellent maintenance performance.
Click the image below to use MaintainX’s procedure templates for mobile, tablet, or desktop—it’s free.
FAQs
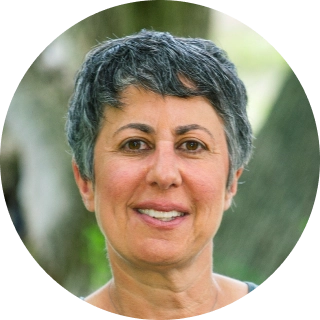
Caroline Eisner is a writer and editor with experience across the profit and nonprofit sectors, government, education, and financial organizations. She has held leadership positions in K16 institutions and has led large-scale digital projects, interactive websites, and a business writing consultancy.