Case studies
A CMMS platform employees love to use
Learn why thousands of organizations trust MaintainX to digitize and transform their asset maintenance and frontline-worker operations.
Trusted by leading manufacturers
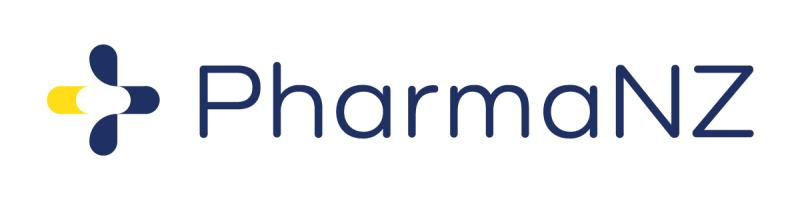
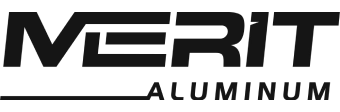
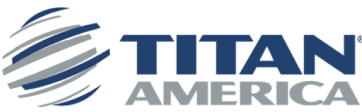
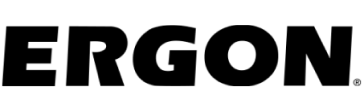
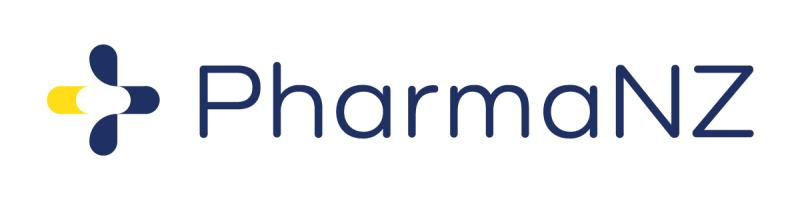
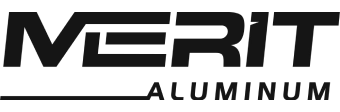
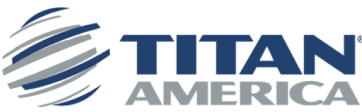
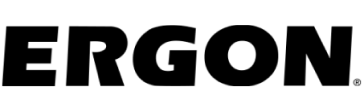
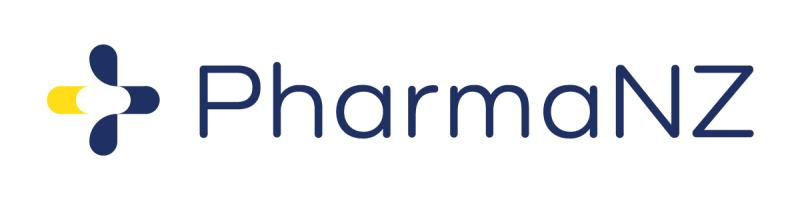
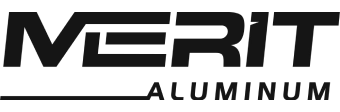
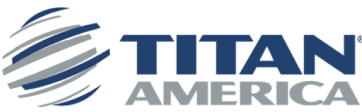
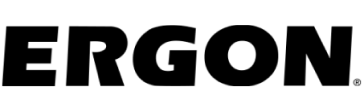
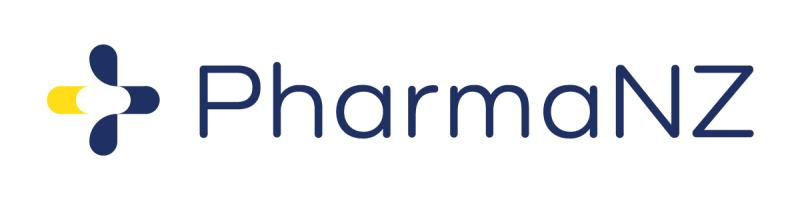
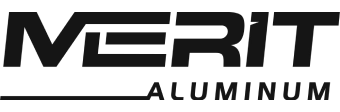
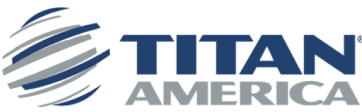
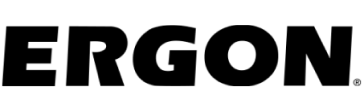
Investing in a modern CMMS drives real results
250h
Saved per year for maintenance managers
34%
Reduction in parts inventory costs
32%
Reduction in unplanned downtime
82%
Companies reported reduced safety risk
Browse all case studies
Thank you! Your submission has been received!
Oops! Something went wrong while submitting the form.
MaintainX is the #1 CMMS & EAM software across third-party review sites
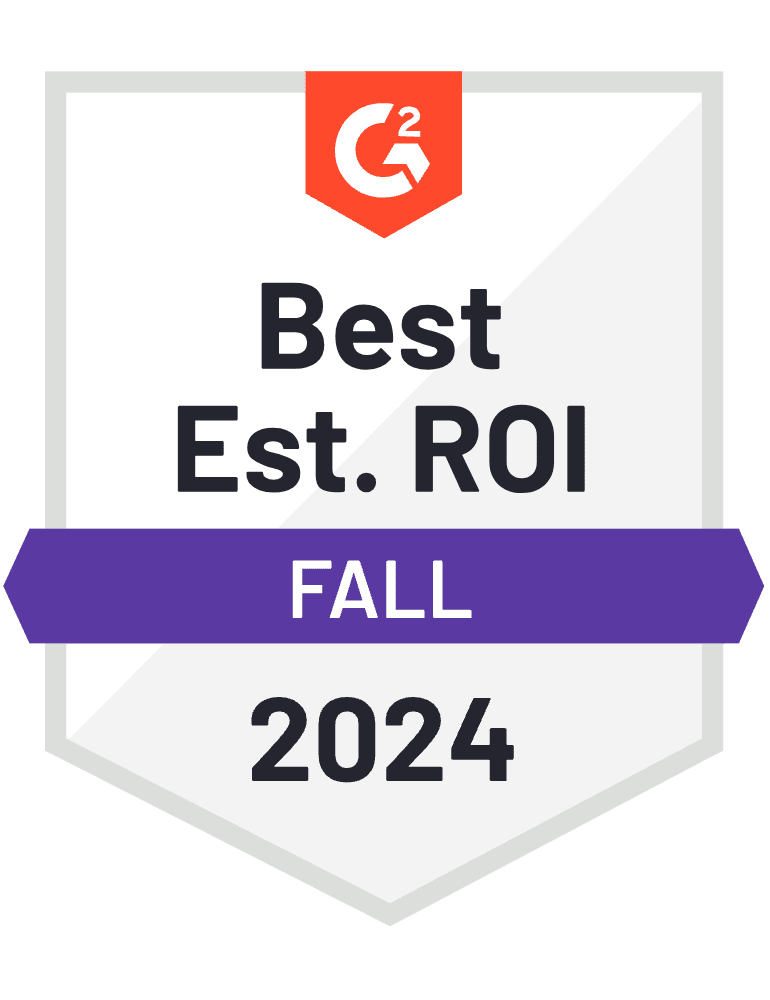
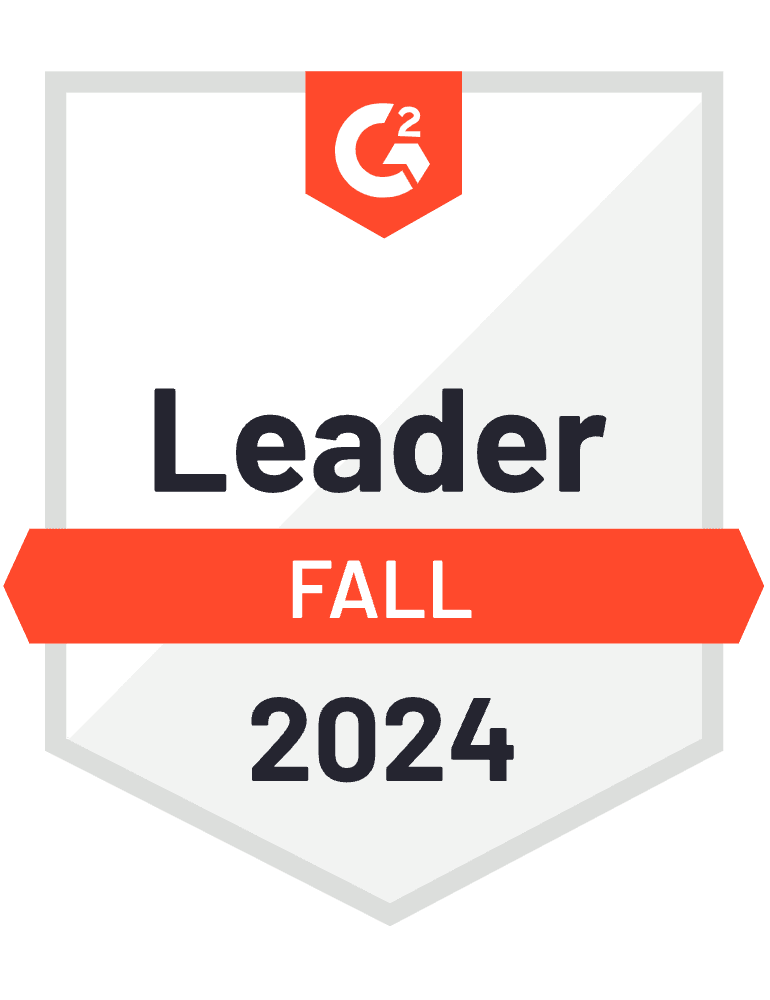
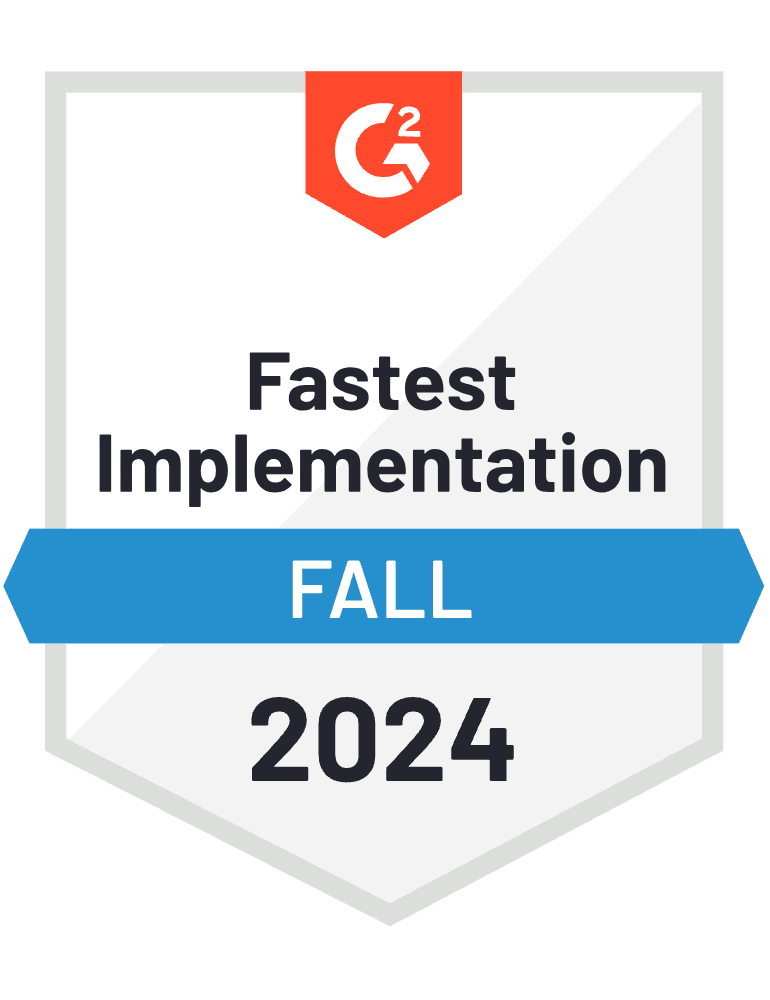
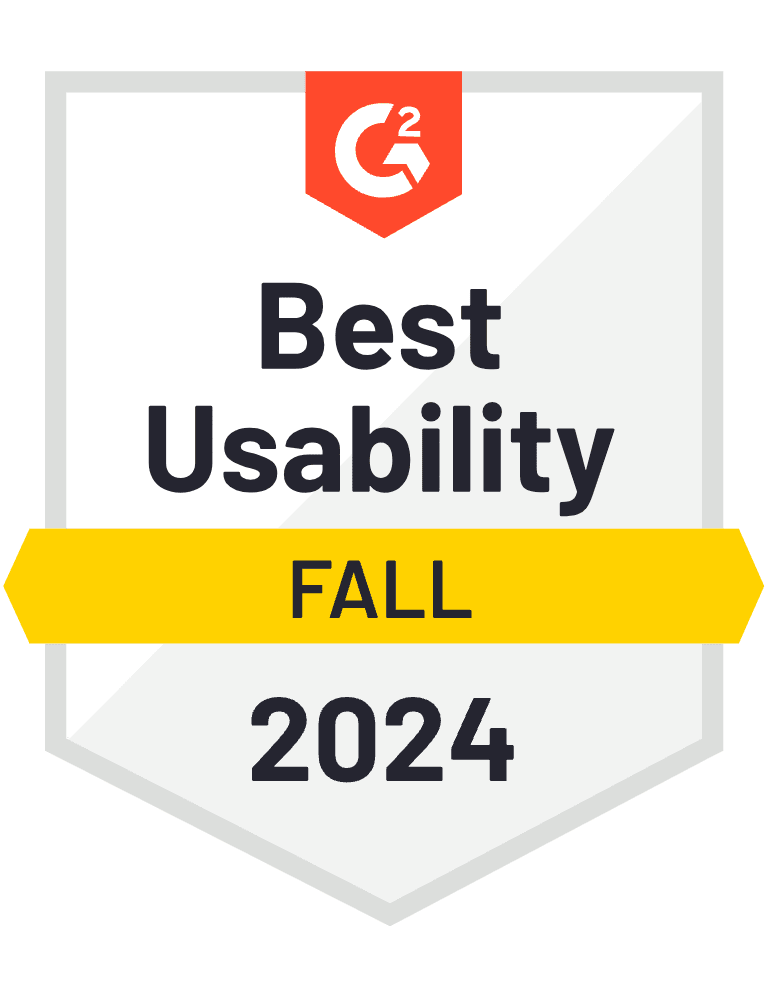
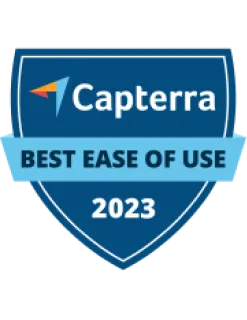
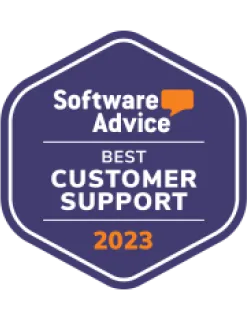
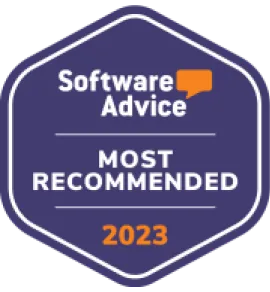
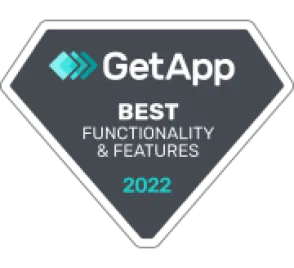
See what customers have to say
Get more done with MaintainX
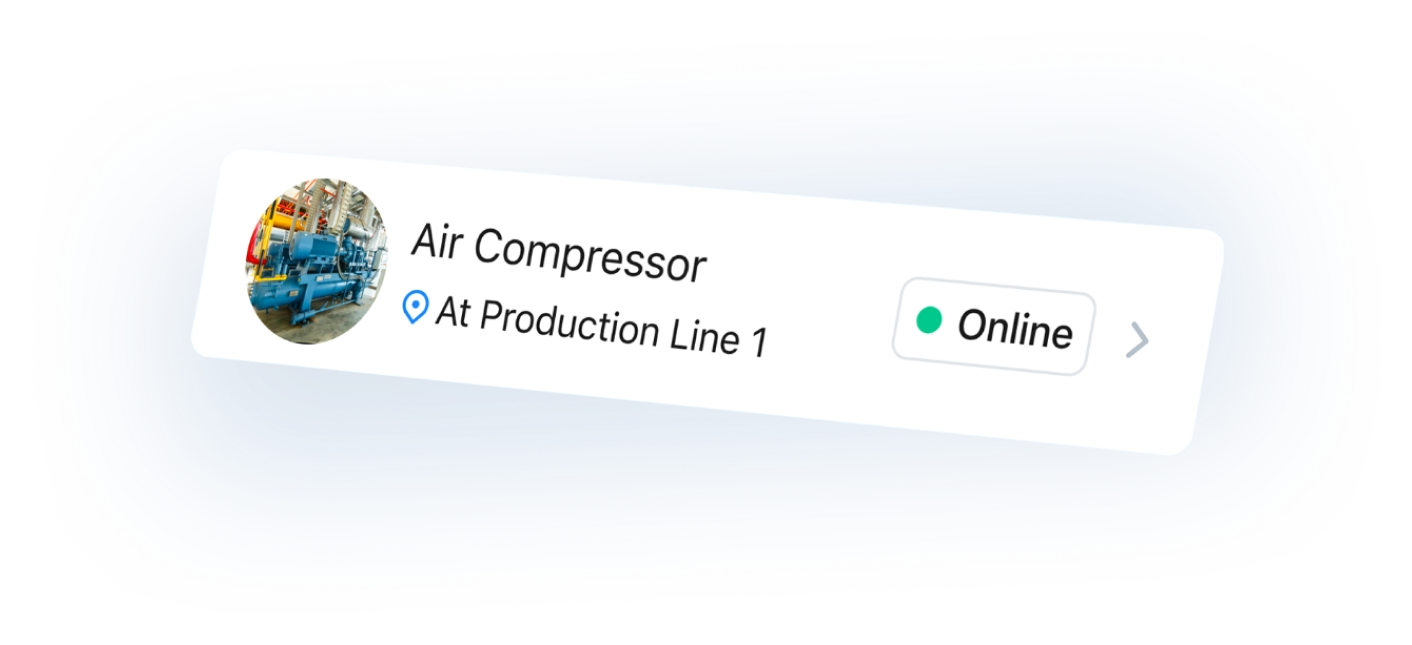
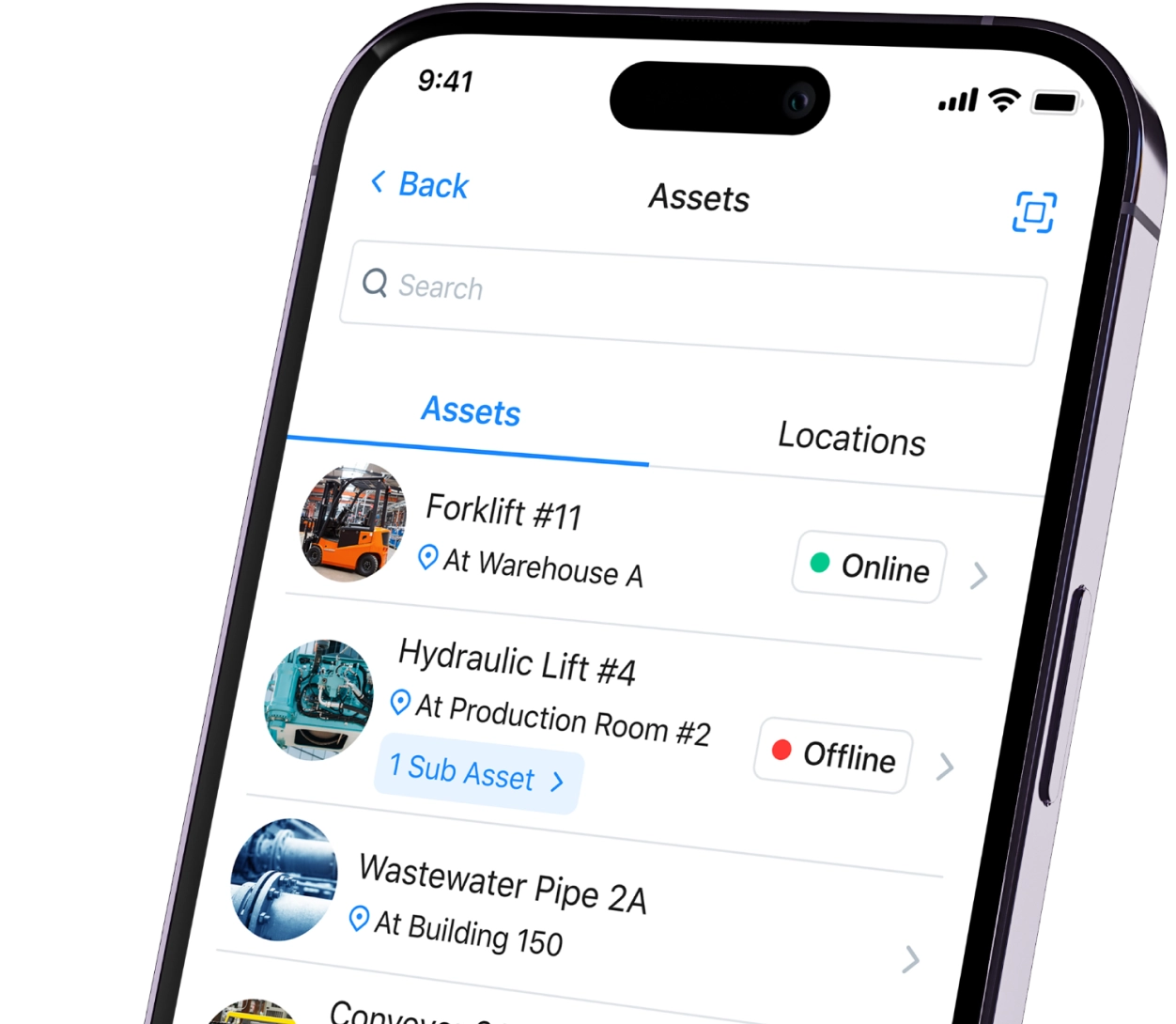