The underlying technologies of a Manufacturing Execution System, or MES, have been around for a while. However, when the term MES was introduced, vendors across the industry started calling their solutions “MES.” The result? MES became a broad term encompassing various solutions used by modern manufacturers.
Over the years, organizations like the Manufacturing Enterprise Solution Association (MESA), the International Society of Automation (ISA), and the Standard Working Group for Measurement and Control Technology in the Chemical Industry (NAMUR) have tried to standardize the definition. This guide explains these standards so you can better understand MES.
What Is a Manufacturing Execution System (MES)?
An MES is a group of digital tools a manufacturer uses to connect, control, and monitor manufacturing operations, systems, and data flows on the shop floor. An MES system helps you optimize the manufacturing process by helping you collect data related to genealogy, material management, traceability, work in progress (WIP), and more.
By genealogy, we mean important manufacturing information: raw materials, equipment used, inspection results, dates, quantities, lot numbers, and serial numbers. In addition, product genealogy can help measure the level of quality output throughout the manufacturing process against the intended product specifications.
Of course, there are various other ways to define the system. For example:
“Manufacturing execution systems (MESs) manage, monitor and synchronize the execution of real-time, physical processes involved in transforming raw materials into intermediate and/or finished goods” (Gartner).
Nonetheless, the broad scope of the system calls for a standardized definition. Multiple organizations have tried to standardize the definition. This may help subject matter experts, but it can lead to more confusion for an end user.
The MESA Model
MESA advises manufacturers on MES systems execution and the effective use of information technology for operations management. The organization issued the first MESA model (MESA-11) in 1996, offering possibly the most accurate definition.
The MESA model defined MES through 11 core functions:
- Operations/detailed sequencing
- Resource allocation and status
- Dispatching production unit
- Performance analysis
- Maintenance management
- Process management
- Quality management
- Data collection/acquisition
- Product tracking and genealogy
- Labor management
- Document control
In 2004, MESA updated its MESA model. The update, “Collaborative MES or C-MES,” expanded MESA-11 to include business operations. The updated model links the core operations in MESA-11 with business operations, including areas like supply chains, customer management systems (like CRMs), and other internal systems like ERP.
In 2008, the C-MESA was updated again. This is its most current version. The current model, the “Strategic Initiatives Model,” includes plant operations, business operations, production, and strategic initiatives like compliance and asset performance.
MESA is currently in the process of updating the 2008 model. The updated standard will break down the complexities of the smart manufacturing landscape. Smart manufacturing includes using emerging and advanced technologies that improve the efficiency of traditional manufacturing processes.
In summary, the MESA model defines MES based on the functions of that system. Therefore, any system that performs all or most of the functions in the model is an MES solution. This also means that the system consolidates the company information and acts as an intermediary between automation and management.
“Data also plays a bigger role on the shop floor, with manufacturing execution systems used to automate tasks such as production planning.”
McKinsey
The ISA-95 Standard
The International Society of Automation has its own standard that defines MES slightly differently than the MESA model. The ANSI/ISA-95 (Integration of Enterprise and Control Systems) standard combines MESA-11 with the Purdue Reference Model.
ISA-95 divides a production system into a five-level hierarchy, creating boundaries between each functional group. For example, the MES functional layer (level 3) sits between ERP (level 4) and process control (level 2). The standard implicitly states that MES acts as the bridge between production and enterprise systems, collects and stores production records, and helps make the production process more efficient.
Unlike the MESA model, the ISA-95 standard doesn’t define MES based on functions but instead based on its role in a manufacturer’s information architecture. The ISA-95 standard enables interfacing between MES and the ERP system, allowing error-free integration.
NAMUR
NAMUR takes an industry-specific approach. However, since every industry’s processes and quality requirements differ, NAMUR—composed mainly of MES users in the chemical and pharmaceutical industries—came up with its own standardized definition.
NAMUR was established in Germany and stands for the User Association of Automation Technology in Process Industries.
NAMUR is based on the MES definition provided by ISA-95. However, it was created explicitly for process manufacturing rather than discrete manufacturing. Process manufacturing industries use MES to control machinery and the plant floor, while discrete manufacturing industries use the system as a control, feedback, and information system for production.
“For much of manufacturing’s modern history, the quality of Manufacturing Execution Systems has set the boundaries for achieving innovation.”
Forbes
Simplifying MES
Ironically, standardization has created more confusion than clarity around MES. However, as an end-user of the solutions, you can locate an MES system by looking at its features. It has most of the critical functions laid out in the MESA model, such as production tracking, quality management, process management, data collection and acquisition, and performance analysis.
MES helps bring efficiency to almost every part of the production process, but using an MES along with a CMMS can offer greater dividends than the sum of its parts.
MES and CMMS have similar capabilities that focus on different business processes.
For example, both have scheduling capabilities, which means you can create a complete production and maintenance schedule to make your shop floor more efficient.
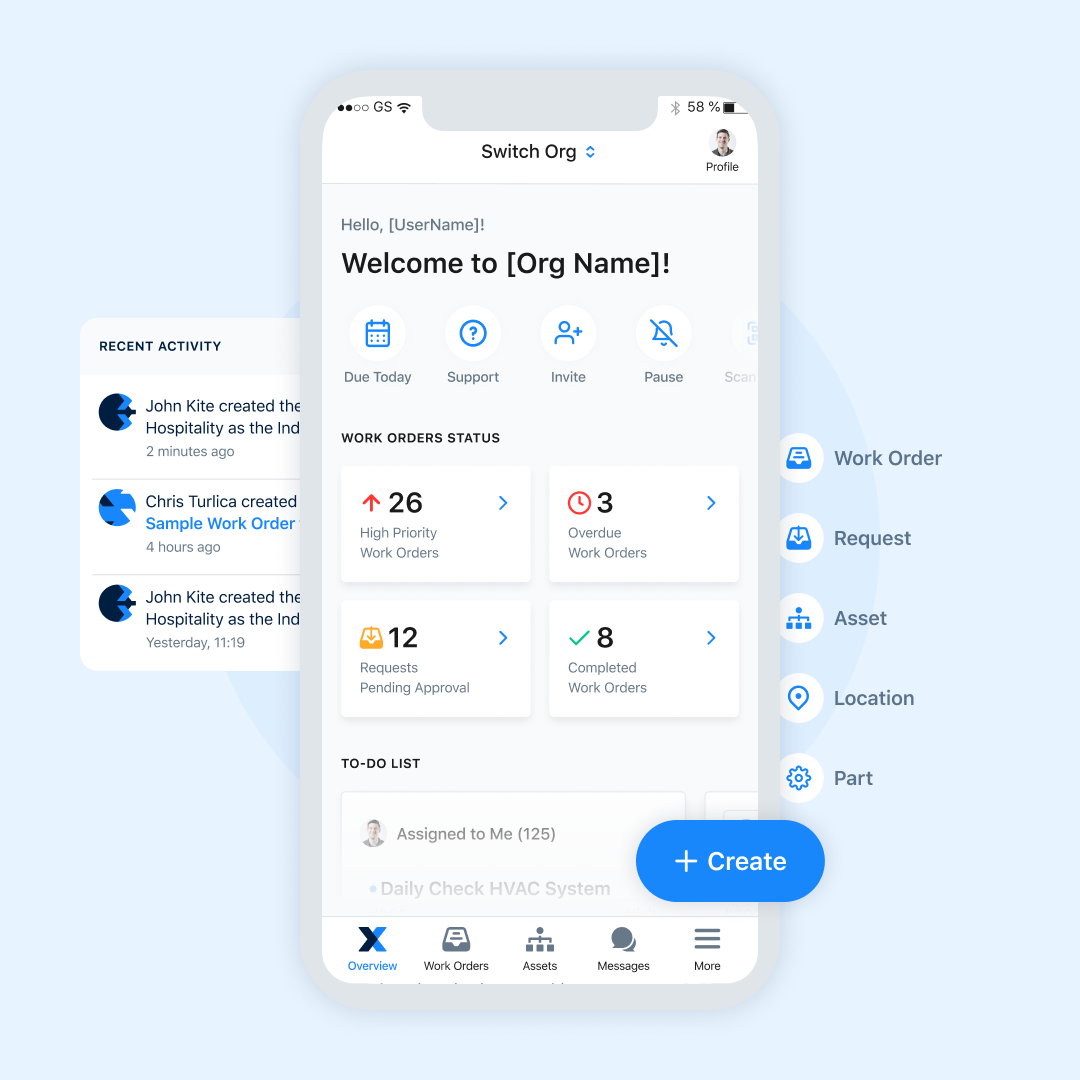
Make the Best of the MES-CMMS Synergies with MaintainX
You’ll need a CMMS with a comprehensive feature set to make the best use of the synergies between MES and CMMS. For example, MaintainX is a mobile-friendly CMMS that stores your data in the cloud and has a built-in chat option for real-time communication.
With these features, you can unify the power of MES and CMMS. For example, you can collect data using the MES and store it in the CMMS for condition-based maintenance. Then, when needed, your technician can use a smartphone to access this data remotely and perform maintenance. If clarification is needed, the technician can request more details from the maintenance manager using the built-in chat option.
Thinking of implementing the MES-CMMS combination at your facility? Try MaintainX to find out how it can streamline your maintenance program and support your MES.
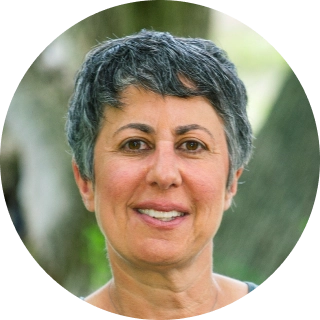
Caroline Eisner
Caroline Eisner is a writer and editor with experience across the profit and nonprofit sectors, government, education, and financial organizations. She has held leadership positions in K16 institutions and has led large-scale digital projects, interactive websites, and a business writing consultancy.
See MaintainX in action