In any organization, effective communication and work management are important to keep things running smoothly. Work requests serve as a foundational tool for organizing work, helping to capture needs or initiatives and turn them into tasks that yield results.
Whether it's a simple request for IT support, a proposal for a new project, or a notification of equipment failure, work requests ensure that teams can identify and address issues in a structured and timely manner. In the maintenance world, where equipment reliability and uptime are critical, work requests are not just administrative tools—they are essential for ensuring that every piece of machinery operates at peak performance.
Here, we explore work requests, how to create effective ones, and how to use them to communicate, prioritize, and resolve issues, ensuring that you prevent small problems from escalating into larger disruptions.
What is a maintenance work request?
A maintenance work request is a document that alerts facility managers when a particular asset needs maintenance repairs. Both customers and maintenance workers can submit them after noticing something isn’t working correctly. This submission can either be manual via paper or through a digital platform, such as a computerized maintenance management system (CMMS).
Part of a maintenance worker’s job is to ensure facilities and equipment remain in good working condition at all times. By responding to work requests—i.e., following up on the notifications—these individuals play an essential role in keeping everyone productive, comfortable, and safe.
However, if not well managed, requests can become burdensome backlogs that hurt organizational productivity. Imagine falling behind schedule and having to sort through a bunch of work requests at once. Beyond the administrative hassle, you’ll be facing problems in your facility as well, with impending failures and possibly prolonged downtime. Under such circumstances, returning your Mean Time to Repair (MTTR) to normal levels can be a major challenge. That’s one reason maintenance teams must develop a proper approach to managing work requests through an overarching maintenance strategy.
Work request examples
Work requests can vary in nature and can come from any department within an organization—or even from a member outside of it.
For example, in manufacturing, it can be as simple as a floor operator noticing a piece of equipment is broken or in need of repair. The operator can then outline the work that needs to be done and submit it to the maintenance team.
As we stated, a work request doesn’t have to originate from a member of your organization. An outside vendor can scope out work requests and submit them in hopes they become work orders. In other industries, like educational institutions, teachers can submit a work request pertaining to their classroom—i.e. a broken heater—aiding in quick turnaround when maintenance is needed.
The difference between work requests and work orders
It’s easy to confuse work requests with work orders. However, there is a distinct difference between the two terms. Work requests represent an appeal for maintenance to be performed on a given asset. Technically speaking, management can approve or deny that request.
Alternatively, work orders are already authorized assignments for planned maintenance to be completed. Maintenance work doesn’t start until a work order is assigned.
In practice, work requests—the ask—become work orders—the assignment—after their submission and approval. Either maintenance supervisors or maintenance planners can approve them. Factors they consider before approving requests include:
- Available maintenance budget
- Staff capacity
- Criticality of the asset
- Severity of the reported issue
- Safety impact of the reported issue
- Planned maintenance activities already in place
- Asset age (Whether it makes the most sense to run to failure, repair, or replace. Up to 40 percent of asset failure is caused by age.)
Types of work requests
Work requests come in various forms, from an urgent request that needs to be completed ASAP for work to continue to those of less importance. Assigning a work request type can help provide context on how crucial the request is and allows organizations to prioritize maintenance tasks.
Work requests are based on the following priority levels:
- Discretionary: These are maintenance tasks that aren’t mandatory. They may include projects such as cubicle upgrading, office painting, and furniture relocation in an office facility.
- Non-discretionary: Technicians perform these emergency maintenance jobs to mitigate problems that can jeopardize safety. Typical examples of these compulsory work order requests include snow removal, power restoration, and chemical spills.
- Urgent: These time-sensitive requests include issues such as running urinals, restoring hot water in a lavatory, and repairing HVAC systems during winter.
- Routine: Workers perform these preventive maintenance (PM) activities to keep assets in good operating condition, extend asset life cycles, and reduce downtime. Such activities include routine cleaning and lawn mowing.
- Non-routine: Operational managers sometimes plan special projects for a variety of reasons. Urgent and non-discretionary tasks often fall into the non-routine category.
What to include in a work request form
Work request forms can be customized to fit the needs of your organization, but there are a few common fields that help ensure their effectiveness. We’ve outlined common elements of a work request below and provided a template to help you get started. The more detailed the documentation, the higher the chance an operational manager will approve the requested maintenance. That’s one reason why effective work order requests usually contain these primary elements:
1. Name/contact information
When a work request is submitted, the submitter should provide their name and an email address or phone number. This allows a maintenance technician to contact that person and ask questions to help provide context behind the request. It also allows you to notify the party when a work request has been accepted and turned into a work order, as well as when the work order has been completed.
2. Request
The largest field on a work request form is often the request field. This is where the requester identifies the primary issue needing maintenance. Typical problems include servicing machines, replacing parts, or even performing emergency repair work on an asset that breaks down. Others include vehicle repair, landscaping, snow removal, carpentry work, and leaky faucets.
Adding detail to the request field is crucial for the success of a work request. At times, problems may not be immediately noticeable or repeatable. For example, if a problem only occurs when first turning machines on in the morning, workers should take note.
3. Location
If the organization has multiple facilities, the request should indicate the specific plant or area where maintenance is needed. Once again, aim for as much detail as possible. This helps to provide the exact location of the asset that needs maintenance and can save time since maintenance technicians fulfill several requests per day.
4. Priority levels
Priority levels depend on how much a reported problem affects an organization’s bottom line, stakeholder well-being, or overall safety. Assign each document a high, medium, or low priority level to help prioritize important requests and ensure operations continue smoothly.
5. Budget estimates
Maintenance technicians sometimes include budgetary estimates on request documents. This step makes it easier to plan maintenance and manage accounting and finance records.
6. Necessary parts and tools
A request should also specify if the work requires any particular tools. For example, if a machine requires a repair, it’s important that the technician has all the tools they need to execute the repair. Not having this information upfront results in wasted effort and prolonged downtime. Similarly, requesters should note any necessary or replacement parts.
7. Department
If a request comes from within the organization, tracking work requests back to departments can be very beneficial. It allows for costs to be properly allocated and can help with end-of-year finances. Some organizations may even break down maintenance tasks based on which department is making the request.
8. Date
Adding the date of the initial request is another field that helps with reporting. By tracking the request date, the date a work order is created, and the day work is completed, maintenance teams can show off their efficiency and provide baseline data on how much time is spent on various maintenance tasks.
Work request form template
We created the following template to help your organization start processing work requests. Feel free to use it and customize it to your organization's needs.
How to manage work requests
Managing work requests properly is crucial to keeping operations running smoothly, and there are different methods you can adopt depending on your resources and the scale of your operations. Here are a few key methods.
Pen-and-paper
This method requires the least amount of work upfront and is very useful for small teams or organizations with infrequent requests and fewer resources. However, while it might be easy to implement, it is an approach that leaves teams at risk. For one, users might misplace requests or misinterpret handwritten instructions. In addition, it becomes harder to track requests over time as their volume increases. Studying or analyzing requests to identify trends will be a difficult process, requiring that you look through piles of paper.
Spreadsheets
Tools like Excel or Google Sheets offer more structure than pen and paper, allowing you to create forms and automate certain aspects. You can also share the document with your team much more easily. As your organization grows, managing work requests this way can become cumbersome, with data spread across multiple sheets and the potential for version control issues.
Software
One efficient method for managing work requests is to use digital solutions. A CMMS, for example, is a centralized and scalable tool that allows you to manage work requests easily. Users can submit, review, prioritize, approve, and track work requests (and work orders) all within one central system. These systems often offer mobile access, allowing you real-time access to requests. While it might require more upfront investment in resources and training, the long-term efficiency gains make it worth it.
Benefits of managing work requests with a CMMS
Using a CMMS to manage work requests offers significant advantages over other methods, from reducing errors to streamlining workflows and providing real-time visibility into request statuses. Let’s explore a few of these benefits now.
Create better work requests
With a CMMS, you can improve the quality of your work requests, ensuring that the overall work quality improves. A CMMS that contains work request templates ensures that your team knows the right information to fill. MaintainX, for example, offers pre-filled templates and required fields that guarantee your team captures the right information every single time. In addition, users can attach photos, videos, and audio to enhance the information they include in a work request. This process allows you to respond to problems faster and more thoroughly.
Review, assign, and prioritize work requests
As work requests come in, you can easily use a CMMS to manage the entire process. You can see each work request as it comes in, approve it, and assign the work order to a team or technician. If you’re using the right software, you can also optimize your assignments with resource insights. MaintainX, for example, enables workload-based scheduling that allows you to assign work based on staff capacity. You can prioritize work orders against others and monitor the process from start to completion.
Share real-time updates
Share and receive updates from the floor in real-time with a CMMS. Instant messaging and work order commenting allow you to communicate and keep everybody in the loop about new developments, from new instructions to updated work statuses.
Maintain detailed histories
By digitizing your work request processes with a CMMS, you’ll automatically create a history of work requests and work orders. This helps you easily pull up information about historical asset performance if you ever need it and identify trends such as repeated failures of specific assets or parts.
Analyze your data
Reporting tools in a CMMS allow you to gain deeper insight into your management process. You can see how frequently certain requests come in and what requests get completed by who. You can also analyze important metrics like mean time to repair (MTTR), downtime, and more. With this knowledge, you’ll be able to make informed decisions to improve your operational processes.
Work request FAQs
The purpose of a work request is to alert the maintenance and operations team of work that needs to be completed. It scopes out the work that the requester would like done, including potential costs, the location of the asset, and the priority level of the request.
There are a few key pieces of information that should be included on a work request. The most important of which is to outline the scope of the work needed. Requester name, contact information, work department, location, budget considerations, and priority level are other pieces of information found in a work request.
The easiest way to create a work request is to leverage the power of a CMMS. By using one, you can establish an easy portal for work requests and simplify the overall process by tagging assets and including pictures. With a CMMS, it’s not just creating a work request that is easy. You’ll improve your tracking, managing, and reporting and gain much-needed visibility on the work your maintenance department manages.
In order to become a work order, a work request must first be approved. Maintenance managers, maintenance supervisors, maintenance coordinators, or facility managers are the roles typically in charge of approving work requests.
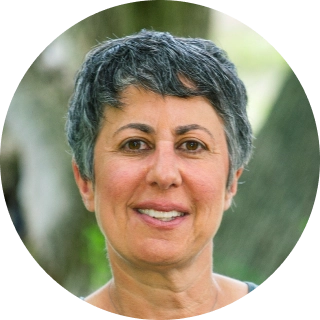
Caroline Eisner
Caroline Eisner is a writer and editor with experience across the profit and nonprofit sectors, government, education, and financial organizations. She has held leadership positions in K16 institutions and has led large-scale digital projects, interactive websites, and a business writing consultancy.
See MaintainX in action