Parking lot maintenance refers to activities intended to extend a pavement’s lifespan. It includes preventive maintenance tasks like cleaning, crack filling, striping, sealing, and asphalt overlay. Parking lot pavement needs routine maintenance because asphalt naturally breaks down over time due to environmental elements. Surface water, oil leakage, weight-bearing vehicles, and sunlight all contribute to asphalt corrosion.
Parking Lot Maintenance
According to the National Asphalt Pavement Association, more than 94 percent of the 2.8 million miles of paved roads in the United States have an asphalt surface. Unfortunately, the black, petroleum-like material weathers over time, leaving dangerous potholes in its wake.
Not only can hitting a pothole damage vehicle shock and suspension mechanisms, but it can also cause drivers to lose control of their vehicles. Like city governments that monitor road wear and tear, facility owners must regularly inspect parking lot conditions. Parking lot maintenance minimizes asphalt corrosion, reduces vehicle mishaps, and keeps drivers safe.
Commercial buildings, public facilities, factories, and warehouses are some of the facilities that rely on parking lot maintenance. Additional motivating factors for maintaining parking lot pavement include maintaining property resale values, enhancing curb appeal, and reducing the need for complete repavings down the line. Strategic preventive maintenance (PM) strategies can further prolong asphalt dependability and reduce long-term spending. Consider that the average cost of resurfacing a parking lot is $1.50 per square foot and the cost of resealing costs an average of $0.19 per square foot or less!
Examples of Parking Lot Maintenance Tasks
Facilities that rely on parking lot maintenance to keep their pavements in good condition include:
- Warehouses and Shipping Facilities: Parking areas in warehouses support heavy vehicles that increase rutting and pavement deterioration along wheel paths. The damage is most prevalent in areas where large trucks slow down and park. Without proper construction planning (e.g. installing thicker asphalt in truck bays where heavy vehicles park) property owners may find themselves re-paving lots sooner than necessary.
- Factories: Similar to warehouses, industrial parking spaces routinely handle heavy vehicles so regular maintenance is important.
- Public Buildings: Courthouses, libraries, and other government buildings should provide well-maintained parking areas that are aesthetically pleasing. Chipped parking lots can also cause damage to light vehicles.
- Retail Stores: Maintaining the parking areas in grocery and department stores helps to prevent accidental falls and damage to vehicles.
- Commercial Buildings: Commercial buildings must stay in good condition to attract new tenants. Parking is part of a prospective resident’s first impression.
Types of Parking Lot Maintenance Workers
General parking lot maintenance technicians perform routine tasks such as cleaning and snow removal during winter. However, commercial facilities primarily engage contractors who specialize in parking lot maintenance. They include:
- Paving Crews: Crews perform routine repair work using heavy machinery.
- Parking Lot Stripers: Stripers deal with parking lot signages and painted lines to ensure that they’re clear and easily visible.
- Mechanics: Mechanics ensure that paving equipment is in good working condition. They perform repairs on equipment as needed.
Tools Needed for Parking Lot Maintenance
Facilities carrying out their own parking lot maintenance must have the right equipment for the job, including:
- Warning signs to alert users when maintenance is in progress;
- Chalk line markers for marking work areas;
- Cleaning tools such as brooms and brushes; and
- Safety equipment such as vests, gloves, and goggles.
Professionals should take on complex maintenance tasks that require heavy machinery.
Parking Lot Maintenance Certifications & Training
Parking lot maintenance workers who want professional certifications to advance their careers should look into these two programs:
- Certified Administrator of Public Parking (CAPP): The International Parking and Mobility Institute (IPMI) offers the CAPP certification to maintenance workers who’ve demonstrated competence in parking lot maintenance.
- Certified Parking Professional (CPP): The CPP certification is offered by the National Parking Association (NPA). The program helps maintenance workers to learn areas related to parking lot maintenance such as design, operations, safety, employee and equipment management, and loss prevention.
Additionally, IPMI provides several other training courses specialized types of parking lot maintenance.
FAQ:
How Do You Clean a Parking Lot?
It’s best to clean a parking lot using high-pressure water to wipe off dirt and spots. In the case of tough stains, hot water can help soften them.
How Long Do Asphalt Parking Lots Last?
The primary factors affecting asphalt parking lot lifespans are frequency of use, weight of vehicles, and consistency of corrective maintenance. The average lifespan of an asphalt parking lot is between 20 and 30 years.
How Do You Maintain an Asphalt Parking Lot?
Generally, asphalt parking lots are long-lasting. Asphalt parking lots can be kept in good condition by:
- Regularly cleaning to remove dirt and debris,
- Routinely applying sealant, and
- Undertaking repairs in a timely manner.
What Is Pavement Resurfacing?
Pavement resurfacing refers to the installation of a new asphalt layer—up to two inches thick—over an existing one. It’s usually performed when the surface is heavily oxidized. But the base should be stable before resurfacing is done.
How Often Should Parking Lots Be Sealed?
Sealants help prevent expensive parking lot repairs. New parking lots should be sealed within the first year after installation. Thereafter, sealing can be done every two to three years.
Get a CMMS for Your Parking Lot Maintenance
Similar to how drivers regularly inspect their vehicles, facility owners must regularly inspect and repair asphalt pavement surfaces. Surface water, sunlight, heavy vehicles, oil spills, and tree roots all contribute to corrosion over time. Parking lot maintenance teams can minimize damage, and extend parking lot life spans, by engaging in preventive maintenance programs. Activities such as cleaning, sealing, and crack filling keep parking lots safe, aesthetically pleasing, and well-preserved.
Park Lot maintenance is crucial to create clean, safe, and functional lots that drivers can appreciate. Use a CMMS like MaintainX to streamline maintenance operations and enhance team communication.
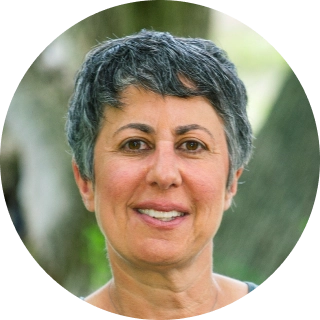
Caroline Eisner
Caroline Eisner is a writer and editor with experience across the profit and nonprofit sectors, government, education, and financial organizations. She has held leadership positions in K16 institutions and has led large-scale digital projects, interactive websites, and a business writing consultancy.
See MaintainX in action