Planned maintenance optimization (PMO) takes a continuous improvement approach to streamline your day-to-day maintenance activities.
Drawing on asset downtime data, work order information, maintenance schedules, and other metrics, this method helps reduce breakdowns and better align your team, equipment, and maintenance budget.
What Is Planned Maintenance Optimization?
Planned maintenance optimization (PMO) refers to a set of organizational methods used to improve existing maintenance practices.
PMO analyzes asset failure history and ongoing preventive maintenance (PM) routines to improve outcomes. The analysis involves reviewing existing maintenance tasks, eliminating unnecessary work processes, and adding missing assignments to maintenance schedules. The goal is to strike an optimal balance between over-maintaining (which wastes resources) and under-maintaining (which increases the risk of unexpected failures), ultimately improving overall operational efficiency and equipment lifespan.
Planned maintenance optimization vs. reliability-centered maintenance
Often confused with reliability-centered maintenance (RCM), planned maintenance optimization is an alternative, PM-based strategy best suited for smaller organizations, facilities, and teams.
While both practices share similar goals – reducing downtime, increasing reliability, and decreasing unnecessary costs – RCM is a resource-intensive process that takes significant time to develop and implement.
For this reason, maintenance teams with large budgets, advanced technologies, and reliability engineers on staff are its primary proponents. Conversely, planned maintenance optimization provides organizations of all sizes with a more flexible template for efficiently carrying out preventive maintenance activities.
Planned Maintenance Optimization is ideal for organizations that:
- Experience equipment downtime, excessive stock inventory, and underutilized workers
- Have yet to perform objective evaluations of PM workloads
- Don’t previously have clearly defined maintenance goals
PMO analysis begins by assessing known equipment failures and maintenance tasks already being performed. Organizations then modify existing routines to develop new maintenance schedules and frequencies based on asset failure history. This approach is different from RCM, which analyzes every failure mode on a given piece of equipment.
How to implement planned maintenance optimization in 3 steps
PM optimization consists of three phases. This practical three-step approach allows organizations to systematically enhance their maintenance practices, reducing downtime and extending asset lifespan. By following these steps, maintenance teams can transform their operations from reactive to proactive, driving significant improvements in plant performance and cost-effectiveness.
Collect data
Organizations need high-quality, reliable data to begin optimizing their maintenance strategies. Tools such as computerized maintenance management systems (CMMS) make it easier for maintenance teams to track equipment data accurately and identify patterns in asset performance.
Consistently collecting real-time data on equipment performance – especially on asset failure – is far more efficient when you have CMMS data to draw on. Reports on unplanned vs. planned downtime, asset availability, and parts usage can be instrumental in setting up your PMO program.
Analyze KPIs for opportunities
After collecting data in a CMMS for several months, organizations should take a closer look at the key performance indicators (KPIs) for their critical assets. Factors determining how critical assets are to plant operations can include mean time between failures (MTBF), mean time to repair (MTTR), and the average cost of asset repairs.
Next, this information is overlaid against existing PM routines to determine whether the failure points fall within acceptable tolerances. Substantial deviations indicate an opportunity for improvement, including modifying existing PM tasks or addressing inefficient or missing maintenance activities.
For example, suppose your CMMS data indicates that the mean time between failures (MTBF) for a compressor is three months, but the manufacturer guidelines stipulate a 12-month service interval for normal operation. In that case, this is likely an area that warrants closer scrutiny to ensure maintenance KPIs are met.
Implement changes and measure impact
The final phase is to delegate the recommended PM adjustments to technicians who can confidently perform the necessary tasks. Continually monitoring the effect of these actions will help you determine if they had a positive or negative impact and help support important maintenance decisions, such as whether a new capital equipment purchase is necessary.
Feedback from maintenance technicians combined with precise data gleaned from your CMMS gives a detailed picture of the impact of your optimization program.
Once you have successfully implemented these adjustments, it’s time to begin the process again. Maintenance programs become truly optimized with a consistent commitment to data collection, data analysis, and readjusting programs over time. The key is to take a cyclical approach and regularly review your data to identify new opportunities for improvement.
Planned maintenance optimization best practices and tips
Implementing planned maintenance optimization effectively requires following key best practices. These tips help maintenance teams avoid common pitfalls and maximize the benefits of their optimization efforts:
- Minimize personal bias and forgetfulness by consulting technicians and backing their input with hard data from your CMMS and ERP systems.
- Try the 6:1 rule, which dictates that organizations aim to find one corrective maintenance task in every six PM tasks performed. This provides a starting point for fine-tuning preventive maintenance processes and programs.
- Adopt a centralized communication system between maintenance technicians and operational managers to capture comments, suggestions, feedback, and field reports.
- Consider asset criticality when prioritizing maintenance goals, routines, and schedules. Equipment breakdowns that halt production should be addressed first before less important equipment and systems that have built-in redundancy.
- Use a technician-friendly CMMS to track assets, inventory usage, and work orders, then draw on this data when analyzing areas for improvement. Implementing a user-friendly system ensures that both technicians and maintenance managers will actually use the software, guaranteeing rich and accurate data.
Benefits of Planned Maintenance Optimization
Planned maintenance optimization can be very impactful. Lab Manager estimates that PMO programs help organizations in the laboratory and life sciences industries reduce maintenance costs by 25 percent.
However, it’s important to be patient—maintenance experts suggest most organizations realize the benefits of PMO within two years of initial implementation. When they arrive, those benefits include:
- Increased asset uptime and improved reliability
- Greater return on investment from assets
- Eliminated waste and more efficient, effective, and leaner maintenance strategies
- Enhanced employee morale through enhanced skill sets
- Increased ability to base maintenance approaches on a proven system
PM optimization enables organizations to enjoy benefits similar to RCM but with less analysis and in less time. It aims to ensure equipment setbacks are avoided and maintenance approaches are practical and efficient.
MaintainX: Re-envisioning how maintenance works
Planned maintenance works best when you have appropriate systems and software in place to enable maintenance operations to run seamlessly. MaintainX gives you the structure and data you need to create a highly efficient PMO program.
Set up and manage preventive maintenance schedules
MaintainX helps you extend the lifespan of critical assets, minimize operating costs, and improve overall maintenance operations by creating detailed PM plans for your equipment.
Flexible work order management
Assign and monitor work across your entire organization by using MaintainX for PM work orders. Use templates to plan preventive and reactive maintenance tasks in a technician-friendly, mobile-first app.
Equipment and asset management
Make planned maintenance optimization simple with data-driven insights that give you visibility across all your assets. Track, manage, and maintain assets to reduce downtime and improve productivity.
Aerial overviews with reporting and analytics
Gain an accurate understanding of your asset health, resource availability, inventory, workload, and more with customized dashboards. MaintainX gives you the data to make informed decisions and successfully optimize your planned maintenance tasks.
Planned Maintenance Optimization FAQs
PMO involves analyzing only the failure modes and breakdown history associated with your existing maintenance plan. RCM, on the other hand, is more time-consuming and labor-intensive, as it begins from a zero base to identify possible failure modes before analysis can begin.
Planned maintenance optimization allows you to improve your existing PM plan by overlaying maintenance tasks with an asset’s failure history. Seeing these two data points together helps maintenance teams identify disconnects between maintenance schedules and actual asset performance.
Take a structured approach to PMO by starting with your most critical assets. Collect information on machine downtime and maintenance history, and combine this with qualitative data from your maintenance technicians. Record all equipment information in a CMMS to allow accurate analysis, and adopt a continuous improvement mindset to ensure ongoing optimization of your maintenance program.
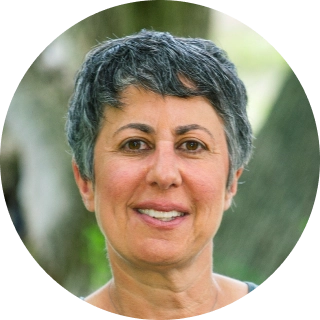
Caroline Eisner
Caroline Eisner is a writer and editor with experience across the profit and nonprofit sectors, government, education, and financial organizations. She has held leadership positions in K16 institutions and has led large-scale digital projects, interactive websites, and a business writing consultancy.
See MaintainX in action