A bill of materials (BOM) is a document that lists raw materials, parts, tools, documents, and other components needed to manufacture or repair a product.
A BOM requires input from various departments, including engineering, purchasing, and operations. Accurate BOMs ensure you have everything needed for an interruption-free production process.
If you find inaccuracies in your BOMs, you end up having to spend time ordering missing parts or bringing parts to the shop floor. The resulting inefficiency and possible unplanned downtime adversely impact your overall equipment effectiveness (OEE) score. As a result, you’ll want to ensure your BOMs are error-free, especially if you are manufacturing complex products. We’ll get to how to ensure this in a moment.
“Creating an accurate bill of materials (BOM) is vital because it ensures that parts are available when needed as well as ensuring that the assembly process is as efficient as possible.”
Investopedia
Types of Bills of Materials
Not surprisingly, bills of materials come in various types, including but not limited to department and purpose.
Department-Specific BOMs
Engineering Bill of Materials (EBOMs)
An engineering BOM (EBOM) contains product design-related items. Engineers typically use software solutions like computer-aided design (CAD) or electronic design automation to generate an EBOM.
EBOMs focus on the design phase and list the raw materials, parts, subassemblies, interrelated data layers, and other design-specific items and instructions. For example, EBOMs include information on the piston size needed to manufacture the product. However, they don’t include information on packaging or labeling—those details are a part of manufacturing BOMs.
Manufacturing Bill of Materials (MBOMs)
A manufacturing BOM (MBOM) includes all raw materials, parts, packaging, and assemblies needed for the manufacturing process and shipping of the final product to customers. Also, it includes information on how parts relate to each other.
MBOMs are generally created using a product lifecycle management (PLM), enterprise resource planning (ERP), or materials requirement planning (MRP) system. They are essential for Lean production planning.
Sales Bill of Materials (SBOMs)
A sales BOM (SBOM) outlines the details of a product before it is assembled during the sales stage. It includes a list of the finished product and the individual components needed to create it, which are listed separately in the sales order. The finished product is treated as a sales item rather than an inventory item in an SBOM.
Other BOMs
EBOM and MBOM are the most common types of BOMs. However, other departments also can create BOMs, such as production bills of materials, assembly bills of materials, and sales bills of materials. For example, configurable bills of materials (BOMs) are commonly used in industries that produce products with multiple options and high levels of configurability. These configurable BOMs allow manufacturers to easily specify the specific components and quantities needed for each unique product configuration.
Purpose-Specific BOMs
In addition, you can create BOMs based on their purpose.
Pseudo Bill of Materials
Pseudo BOMs are flexible BOMs in which you can include the most critical spare parts and replacement parts or group parts to simplify administration.
Maintenance Bill of Materials
Maintenance BOMs include parts that maintenance technicians need to repair or replace an asset. They also ensure that technicians have everything they need to complete the job, streamlining maintenance tasks.
Pro tip: If you use an ERP, you can integrate the ERP system with a computerized maintenance management system (CMMS) to streamline your entire maintenance program.
Equipment Bills of Materials
Equipment BOMs are used by companies that rely heavily on asset management. They list all asset parts and materials, including assemblies and subassemblies.
What to Include in a Bill of Materials
The contents of a BOM depend on its type. For example, if you’re creating a BOM for maintenance, you need to include details like asset ID, part number, tools, and materials needed to perform maintenance.
In general, the BOM structure includes the following details:
Bill of Material Level
BOM level is a unique number representing where each part fits in the overall BOM hierarchy. For example, a BOM for a car would include each major car component, such as the engine, tires, and seats. You would further break down each of these into components and materials. For example, the pistons (level 2) are part of the engine (level 1).
Part Number
A part number is a unique number used to identify a material or asset component. Part numbers don’t necessarily have to be numeric codes. For example, if you have five machines with five pistons each, you can call the first piston in the first machine “PISTON-01” and the last piston in the last machine “PISTON-25” to make part numbers easier to comprehend. Also, you can attach QR or barcodes, which a CMMS like MaintainX can easily read and keep real-time track of in your online parts inventory.
Part Name
Part name is similar to a part number. It helps technicians identify an asset or part quickly.
Quantity
Quantity informs the technician about the number of parts needed for assembly or sub-assembly.
Unit of Measure
Including the units by which you measure quantities on the BOM is essential to avoid inefficiencies and ambiguity. Be consistent with units across the BOM. For example, if you’re using pounds for weight, don’t switch to kilograms halfway through.
Description
Description provides technicians with details necessary to differentiate similar parts. For example, when adding descriptions for pistons, you might differentiate between 40mm and 50mm pistons.
Phase
This represents a part’s stage in the overall asset lifecycle. For example, you can label parts as “in production,” allowing the team to track progress easily and better understand project timelines. Again, if you are using a CMMS for parts and assets inventory, this is easy. MaintainX can track parts and assets by location, vendor, contract manufacturer, sub-asset, and more.
Procurement Type
This section describes how you sourced a specific part. Did you procure it via a third-party vendor? Did you subcontract production to a manufacturer or produce it internally? Including this detail ensures the right team member knows how to procure the part if and when needed. MaintainX can send purchase orders directly to vendors. You can trigger a purchase order when a part falls below a specific amount. This is especially important these days as we continue to face supply chain shortages and longer-than-usual lead times.
Reference Designator
The reference designator identifies the location of a specific part on a printed circuit board assembly.
Bill of Material Notes
These notes should be open ended. In the notes, you can include other relevant information, such as instructions for working on a specific asset with a history of frequent repairs. Also, you could attach a link to a standard operating procedure (SOP) that includes a repair manual and diagrams.
Example of a Bill of Material
In its simplest form, a BOM is just a list of components required to manufacture a new product. For example, suppose you manufacture mobile phones. In this case, your BOM template for manufacturing a cellular device might look like this:
Of course, this is a simplified example. Speaking practically, you can make BOMs as detailed as needed to streamline your manufacturing and maintenance processes. While you’re trying to streamline maintenance, check out MaintainX.
How MaintainX Makes Maintenance Easier
MaintainX is a CMMS that helps streamline maintenance programs and boosts bottom-line growth. With MaintainX, you can use BOMs to improve production efficiency and manufacturing maintenance. Likewise, MaintainX helps you become more efficient across product development and inventory management. In manufacturing, you can translate a production order into a digitized SOP that includes product structure diagrams, procedures, and a comprehensive list of the tools and individual parts your team needs.
Think about it: When you’re about to run out of a spare part, MaintainX automatically alerts you. This way, you can order inventory to ensure everything is included in the BOM. In addition, you can create process checklists and allow technicians to communicate and collaborate using MaintainX’s chat feature so everyone is always on the same page.
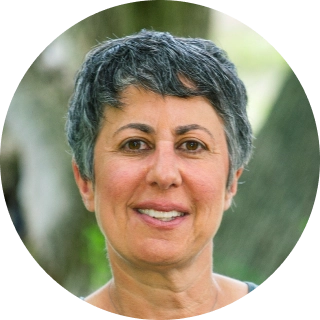
Caroline Eisner
Caroline Eisner is a writer and editor with experience across the profit and nonprofit sectors, government, education, and financial organizations. She has held leadership positions in K16 institutions and has led large-scale digital projects, interactive websites, and a business writing consultancy.
See MaintainX in action