Troubleshooting is the process of systematically identifying and solving equipment failures to bring the equipment back into working condition. Troubleshooting is closely associated with root cause analysis (RCA), though RCA is more formal than troubleshooting.
Turning equipment off and on when it isn’t functioning correctly often fixes the problem. Still, you should try to get to the bottom of what caused the problem. Often, it is a sign of an impending breakdown.
“Traditionally, most maintenance professionals have combined many techniques, both quantitative and qualitative, in an effort to identify failure modes and mitigate downtime in manufacturing facilities. But the rise of new connected technologies can enable machines to do these tasks for them, both maximizing the useful life of machine components while still avoiding machine failure.”
Deloitte
What Is Troubleshooting?
This is when you’ll need to troubleshoot. Troubleshooting involves coming up with possible solutions to resolve a problem. Below we take a closer look at what troubleshooting equipment repair is, how to troubleshoot, and how CMMS apps can make troubleshooting easier.
In addition to instances of breakdowns, the troubleshooting process is used for equipment expected to break down, or that isn’t functioning correctly. However, proactive maintenance can help maintain equipment’s condition and minimize the need for troubleshooting.

Why Do You Need to Troubleshoot?
While preventive and condition-based maintenance can reduce instances of equipment failure, eliminating failure entirely is difficult. In addition, failure or other issues also can raise regulatory challenges. However, if you have a digital regulatory compliance checklist, you’ll be able to flag such challenges sooner and troubleshoot to avoid penalties.
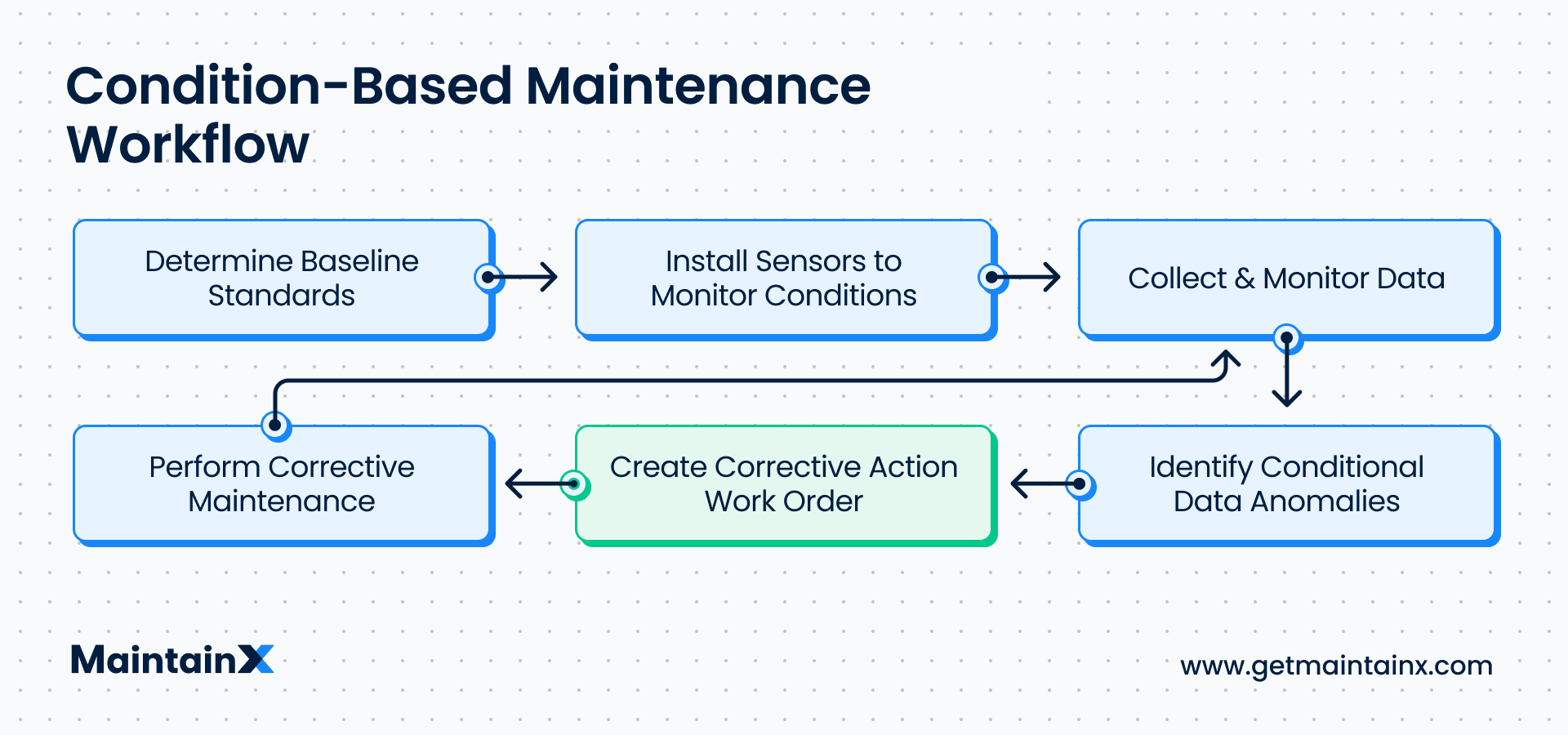
Even when you’re proactive about maintenance, unexpected equipment failure can and does occur. This is why you need troubleshooting techniques. When an asset breaks down or operates abnormally (detected using techniques like temperature reporting and vibration analysis), troubleshooting skills help minimize downtime and ensure regulatory compliance.
Maintenance personnel needs troubleshooting experience for effective troubleshooting, which, unfortunately, requires assets to break down. While you can’t substitute real-time experience, CMMS software helps the maintenance team get the information it needs to determine the possible cause of failure quickly and easily.
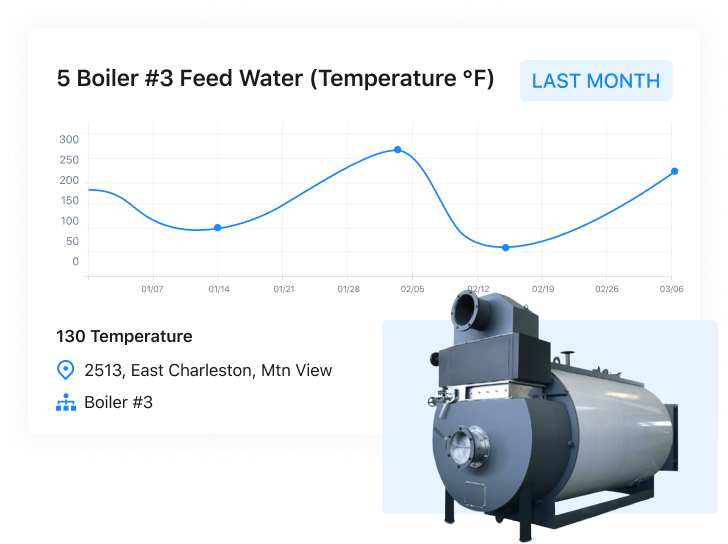
How to Troubleshoot Assets
Having a CMRP professional on the team can help, but in most cases, you can troubleshoot without professional assistance. Troubleshooting is easier when you follow predefined steps. Regardless of the cause–even if it is a common cause, here are troubleshooting steps to help you fix any device or machine.
Step 1: Get Clarity on the Problem
Has the equipment stopped working? Is it just operating abnormally and may stop working? Have you noticed something odd about the equipment and can’t determine if it might lead to a breakdown?
While some equipment has built-in mechanisms—such as a sound alarm, warning message, or error code—to notify you of problems, other equipment simply stops working. Once you’ve identified the problem, you’ll need to look at the equipment’s operational data.
Step 2: Analyze Equipment Data
Once you’ve established the problem, analyze the collected data to determine the cause. Begin by reading the standard equipment data from the Operation and Maintenance Manual and its troubleshooting guide. Then, compare it to the actual number of hours the equipment is used, the purpose it’s used for, maintenance history and schedule, and failure history.
Once you have the data, determine the cause using your technical know-how, reading the manual, or asking experts for input. In most cases, you can track the cause back to a recent change. For example, a changed spare part, a change in usage pattern, or a change in the raw material may be the cause.
However, you may be unable to identify the cause. Look for unexpected data or loose ends if you’re in a similar situation. Maybe you didn’t collect all the information required to identify the cause. If you use a CMMS, you’ll be able to extract accurate information more quickly.
Step 3: Test Solutions
The next step is to devise a solution based on the cause. However, the problem may not have a known solution. In such cases, you’ll need to try a few possible solutions to test them.
Continue testing solutions until you find one that works. As you test solutions, be mindful of the team’s safety and associated costs. In some cases, replacing the equipment might make more sense than repairing it.
Should You Replace or Repair an Asset?
While the cost of repairing an asset may seem lower than the cost of a new asset, maintenance and repairs can sometimes be more costly when you look at an asset’s quarterly or annual cost.
For example, suppose a machine broke down several times over the past quarter. In that case, the cost of repairing it and the cost of downtime might exceed the cost of a new asset, especially when you factor in the monetary value of improved efficiency and other benefits of a new asset.
However, you may need to prove these facts to the finance and admin teams. A CMMS like MaintainX, with robust KPI reporting features, can calculate downtime history. The costs of maintaining and repairing an old asset can enhance the need to buy rather than repair.
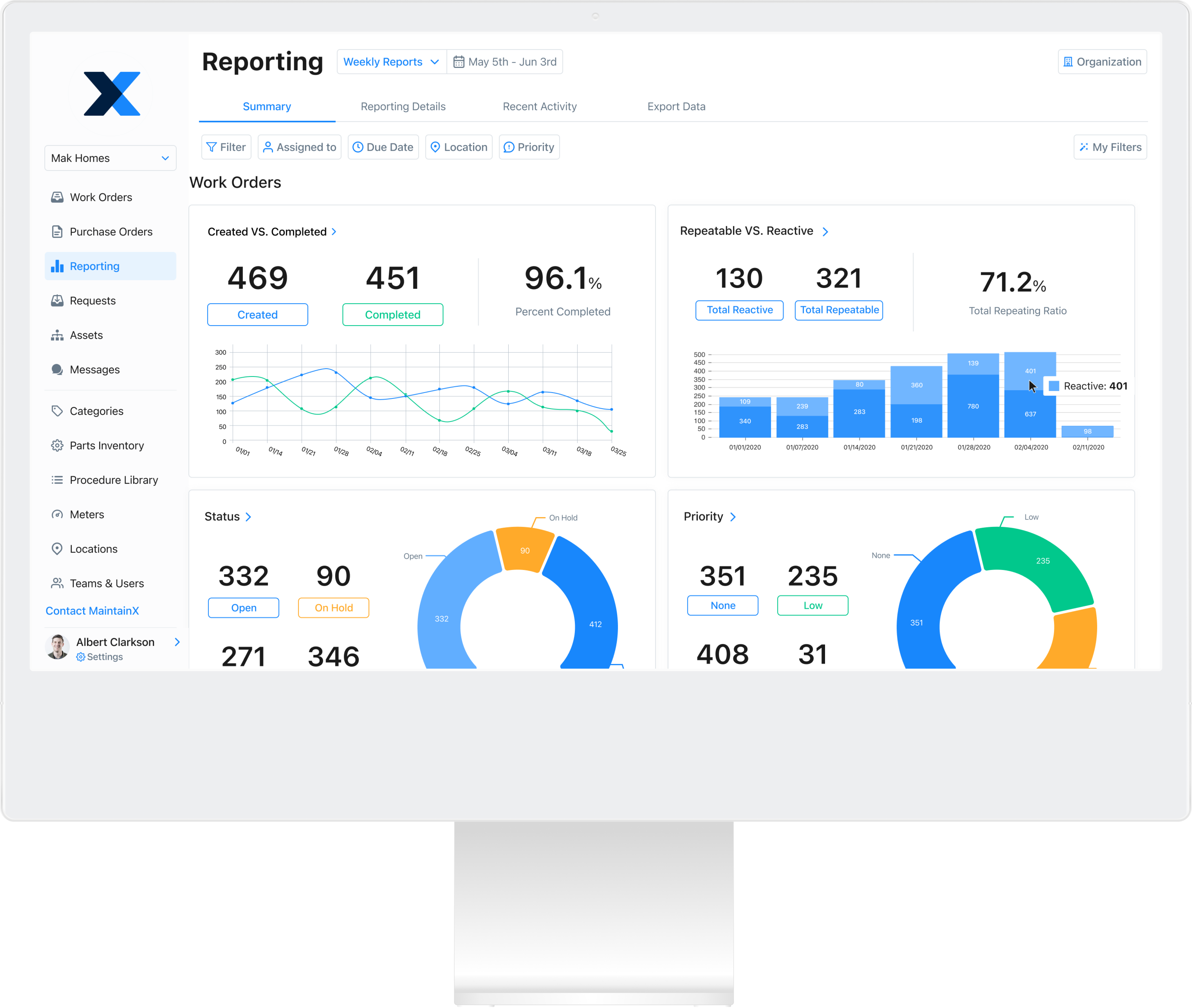
Pros and Cons of Troubleshooting
Troubleshooting offers several benefits but also has some downsides.
Pros of Troubleshooting
- Minimize downtime: Effective troubleshooting helps you minimize expensive downtime.
- Save money: In addition to minimizing downtime, troubleshooting also saves time and money you would spend getting the piece of equipment fixed by a third-party service provider.
- Equipping team with valuable experience: The more your maintenance team troubleshoots issues, the more experience they’ll gain in finding solutions to fix these common issues later. Over time, their experience can pay dividends.
Furthermore, after hiring new maintenance technicians, invest in training programs to help them troubleshoot more quickly. Training will increase their problem-solving skills and increase their process of elimination when they are on the job.
Cons of Troubleshooting
- Can be expensive: Troubleshooting might require maintenance teams to invest a lot of time and resources, which can be costly.
- Not helpful if you decide to replace: If the repair cost is high and replacement makes more sense, you’ll have invested time and resources in troubleshooting only to discard the equipment.
- Availability of third-party services: Often, third-party services can offer help at a lower cost than troubleshooting in-house.
MaintainX Makes Troubleshooting Easy
Using a CMMS like MaintainX can make troubleshooting easy in several ways. For example, you can get real-time troubleshooting data within seconds from MaintainX.
Once you’ve finished troubleshooting, you can easily monitor select KPIs (key performance indicators) via MaintainX Reporting. Monitoring the data helps you quickly identify common problems when they reappear so that you can take prompt action.
Ideally, you also should tweak your preventive maintenance checklist after troubleshooting. Using a systematic approach by creating preventive maintenance work orders will prevent the issue from reappearing.
Make troubleshooting easier with MaintainX!
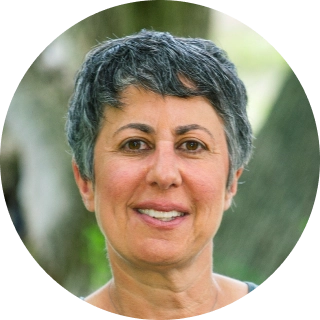
Caroline Eisner
Caroline Eisner is a writer and editor with experience across the profit and nonprofit sectors, government, education, and financial organizations. She has held leadership positions in K16 institutions and has led large-scale digital projects, interactive websites, and a business writing consultancy.
See MaintainX in action