
In today’s fast-paced world, organizations are continuously seeking innovative ways to optimize their processes and maintain a competitive edge. One of the most effective methods to achieve this is through a comprehensive preventive maintenance program. In this post, we will delve into some of the top preventive maintenance examples utilizing a CMMS, demonstrating its capabilities in optimizing maintenance operations and key performance indicators across various industries.
From scheduling routine inspections to monitoring equipment performance, a CMMS can revolutionize how organizations approach their maintenance needs. Read on to discover how this powerful tool can transform your maintenance operations and help your organization achieve new levels of efficiency.
Preventive maintenance is a proactive approach to maintaining equipment, facilities, and other assets, aiming to minimize unexpected breakdowns, increase the lifespan of assets, and reduce overall maintenance costs. A CMMS is a powerful tool that can streamline preventive maintenance tasks, improve resource allocation, and ultimately enhance an organization’s productivity.
Implement Preventive Maintenance
Equipment failures cannot be eliminated—they will happen. However, preventive maintenance programs have been proven to reduce breakdowns, keep workers safe, and reduce unnecessary expenses.
Preventative Maintenance (PM) is planned maintenance that prolongs the lifespan of company assets, equipment, and infrastructure. Also spelled “preventive,” PM includes adjustments, cleaning, lubrication, repairs, and replacements.
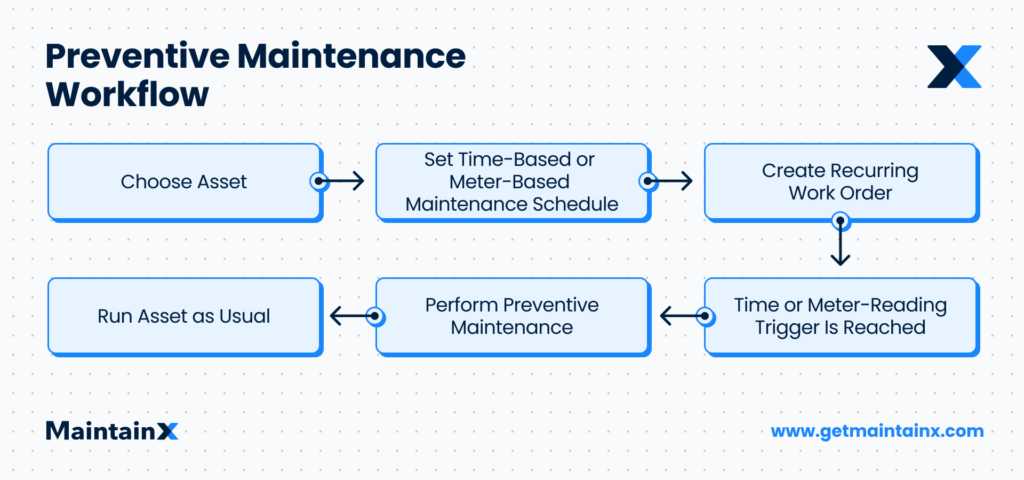
A preventive maintenance strategy works based on the principle that detecting and fixing minor problems before they interfere with asset performance is better than dealing with them when they have become significant issues. This doesn’t mean that reactive maintenance, or run-to-failure maintenance, is always inadequate. Any strong maintenance strategy will include plans to handle the inevitable breakdowns that preventive maintenance cannot stop from happening.
“You need to define the type of plan: Is it for risk-based, corrective, condition-based, or preventive maintenance? You must also understand the business and who is affected. Determine if you have the resources, in-house skill set, and capabilities. Also, have metrics that show you where you have been, where you are today, and whether you will hit requirements.”
Forbes
Types of Preventive Maintenance
There are many types of preventive maintenance. They include the following:
Routine Maintenance
This involves carrying out preventive maintenance tasks according to a calendar-based schedule, no matter the condition of the assets. This regular maintenance can include regular inspections and weekly oil changes, for example. Other examples include testing fire alarms and servicing HVAC and air-conditioning units.
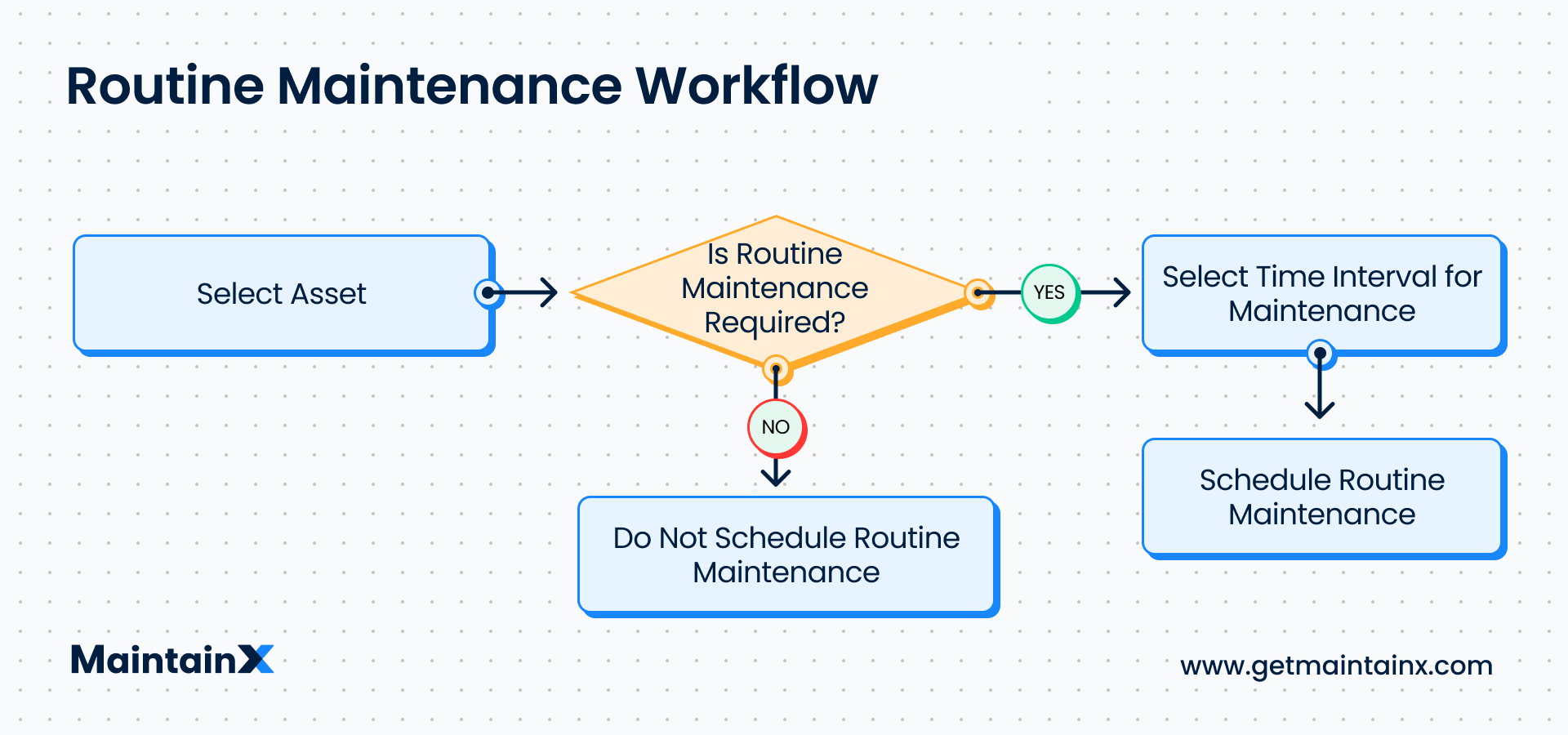
This maintenance is also called Time-Based Maintenance, as teams carry out the preventive maintenance schedule within set intervals. Scheduling can also be usage-based, meaning maintenance is based on equipment usage.
Predictive Maintenance
Predictive maintenance (PdM) is an advanced form of planned maintenance that monitors asset conditions in real-time. The proactive strategy relies on sensors that alert maintenance teams when preventive maintenance is needed to maintain optimal performance levels.
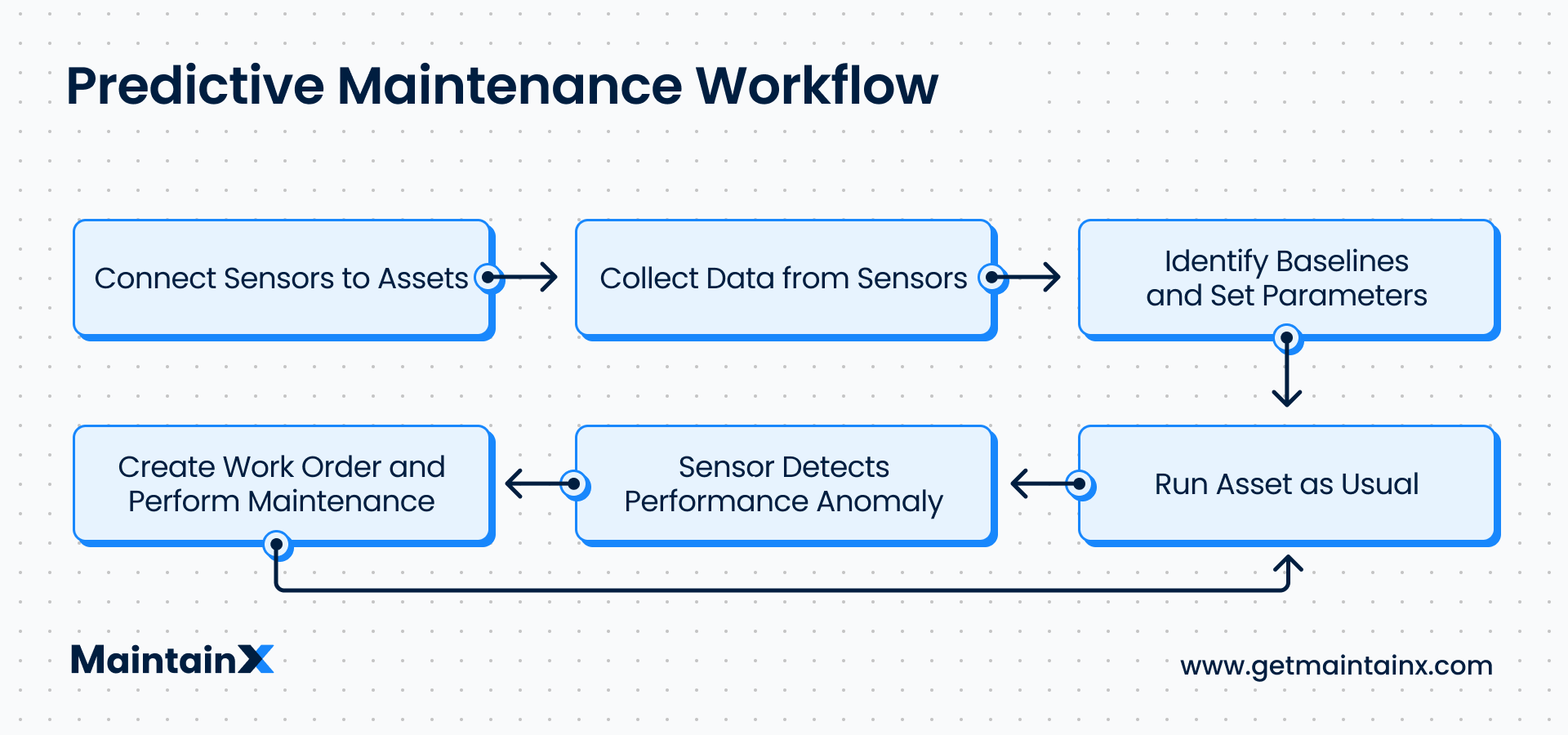
This works based on monitoring asset performance, pinpointing the likely occurrences of failure, and scheduling maintenance work to coincide with those periods. Preventive maintenance can be time-consuming. As such, the goal of predictive maintenance (PdM) is to minimize wasted effort and only carry out preventive maintenance when necessary.
“Predictive maintenance typically reduces machine downtime by 30 to 50 percent and increases machine life by 20 to 40 percent.”
McKinsey
Here are the key differences between the two:
While there are other differences between predictive and preventive maintenance programs, these are the primary factors. As you can see, both strategies have unique advantages and disadvantages.
Condition-Based Maintenance (CBM)
CBM is a form of predictive maintenance that aims to predict when to perform maintenance based on close attention to an asset’s condition. Condition monitoring lets you know when assets are beginning to show signs of deterioration, requiring maintenance work.
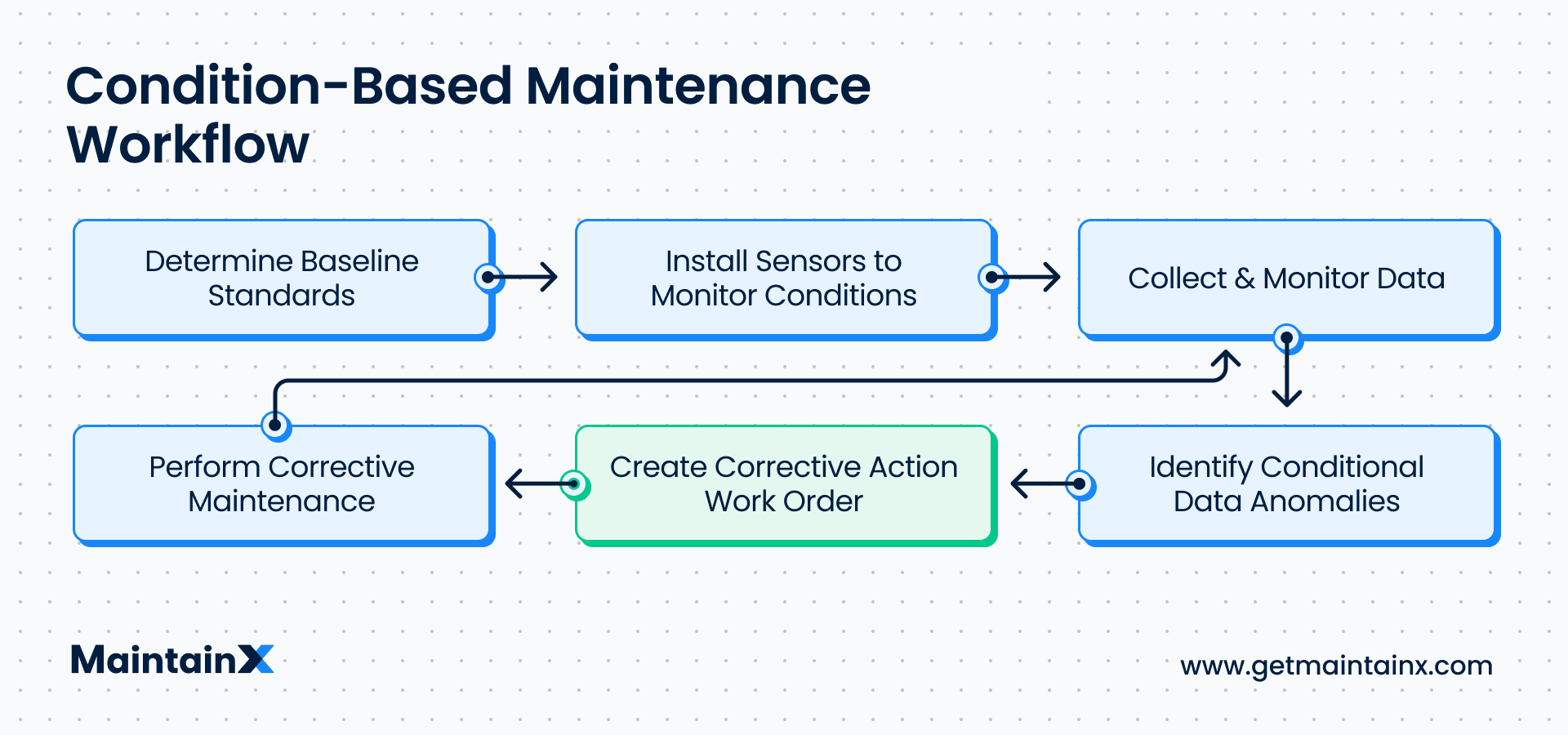
Preventive Maintenance Examples
Preventive maintenance can be time-consuming and effort intensive. A big part of this is the planning required. Depending on factors like the nature of your facility and the number of assets you oversee, you might need different plans to handle different kinds of equipment.
Preventive maintenance software, specifically a CMMS Computerized Maintenance Management System), is the smartest way to manage maintenance. CMMS software, like MaintainX, can streamline your maintenance operations.
Let’s look at examples of preventive maintenance and how the right CMMS can help.
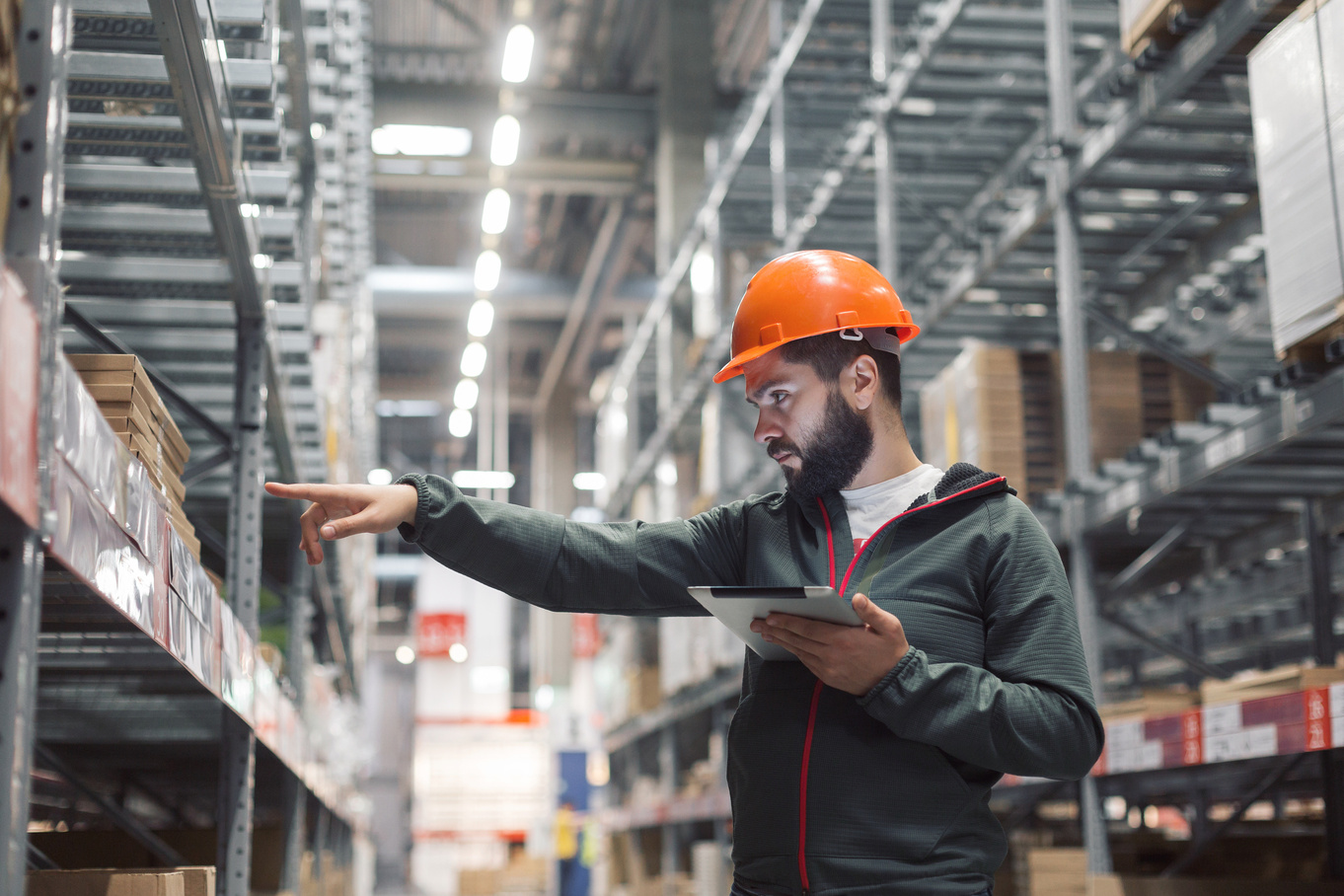
PM Parts Replacement
An excellent example of preventive maintenance in action is replacing parts. Imagine an asset failing and production shutting down all because a small part broke off. You can easily avoid this by changing deteriorating parts before they break entirely.
Not only does this planning ensure assets remain in service, but you’ll protect your employees from any potential hazards that might result from failure. If a part breaks down or malfunctions, you don’t want to prolong any downtime because technicians can’t find a replacement in your spare parts inventory.
A robust CMMS can simplify your asset management and monitor your inventory all in one place. Technicians can update the inventory when they take a spare part out of stock. In turn, you can automate your inventory so that your CMMS notifies you when specific parts run low. With MaintainX, you can also automate purchase orders to vendors to ensure your preventive maintenance runs smoothly.
PM Fire-Alarm Testing
Another preventive maintenance example is inspections and tests. If you manage a facility, whether residential or commercial, you likely need effective emergency protocols in place. Regular testing of fire alarms is one such process.
Regulations require that you run inspections during safe and calm periods to ensure your emergency procedures work correctly. A CMMS can create an advanced schedule for your testing and assign work orders to the appropriate teams. This way, nobody needs to manually set or send reminders beforehand. The CMMS will send automated work orders to the teams and technicians involved in the testing.
With MaintainX, you can schedule repeatable work orders. So, once you sit down to create your weekly or monthly schedule, you’ll get reminders unless you modify the schedule. Your work orders can also include step-by-step procedures and checklists for your testing process.
PM Equipment Lubrication
Keeping parts lubricated when needed is crucial to prolonging the useful life of your equipment. Manufacturers will often include recommended lubrication schedules in equipment manuals.
If you follow this, you can create advance PM schedules with a CMMS to repeat the work orders. In other cases, you might observe your assets yourself, note how much and how heavily you use them, and create a schedule from there.
Whatever the case, a CMMS can help you create schedules and record activity. You can store details of what brand of lubricants and what procedures to use, ensuring that knowledge is standardized and available if vital staff members are unavailable for scheduled maintenance.
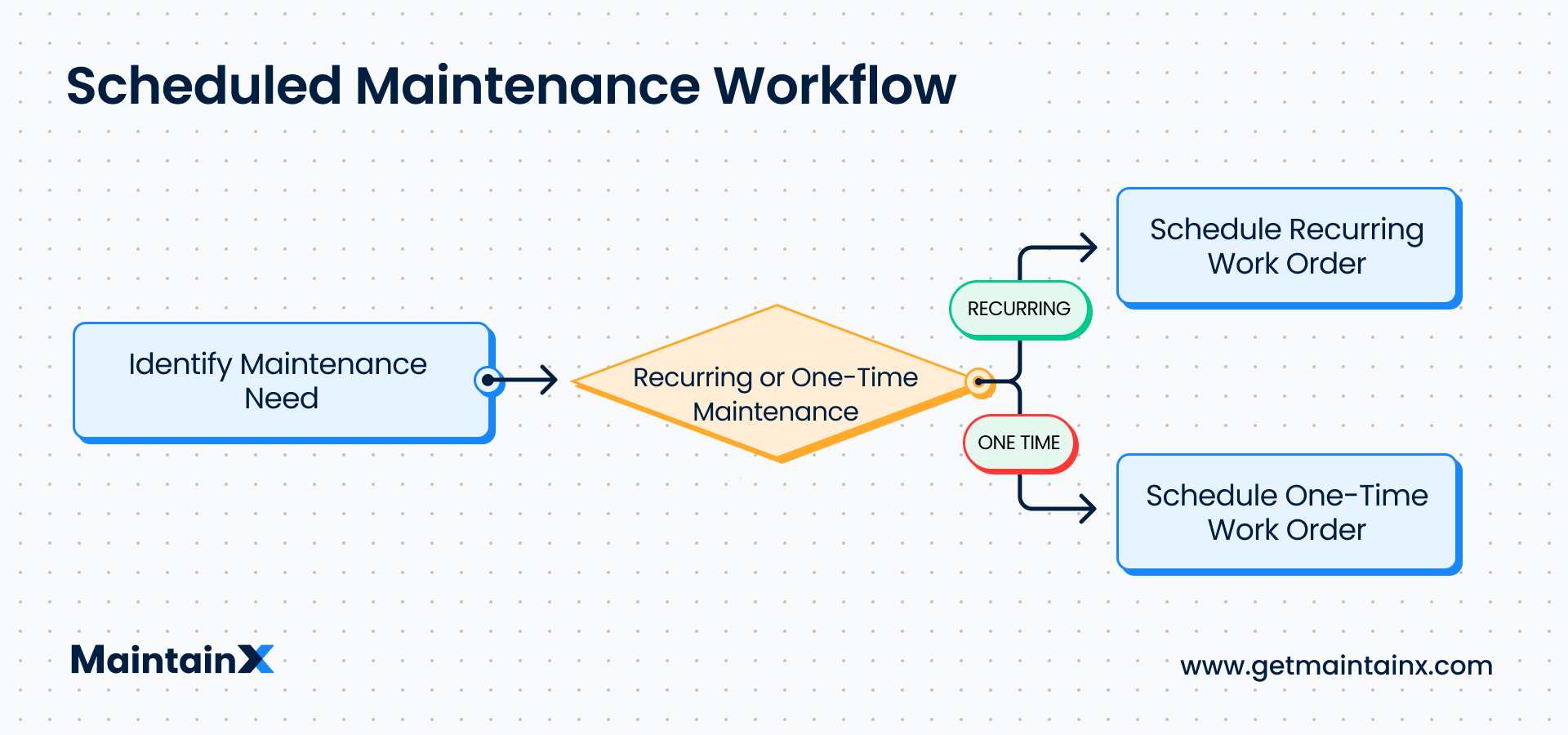
This also helps with root cause analysis: if your system isn’t effective, you can investigate your activity history in your CMMS. MaintainX, by the way, offers our Premium and Enterprise customers unlimited access to their work order history and advanced analytics.
Benefits of Preventive Maintenance
The advantages of creating a robust preventive maintenance plan include the following:
PM Reduces Downtime
Reducing your equipment downtime, especially unplanned downtime, is paramount for the smooth running of any company or facility. Whether you’re in manufacturing and thinking about equipment and production cycles or more concerned with building and facility management and, for example, elevators, the last thing you want is to prolong the time critical assets are out of service. Preventive maintenance activities ensure you fix problems before they lead to breakdowns, ensuring assets are always available for production or other uses.
PM Reduces Cost
In addition to keeping assets available, proactive maintenance will reduce your maintenance spending. Detecting problems before they cause shutdowns often translates into deploying quicker and less-expensive solutions than the costly repairs you need in the event of a full-blown breakdown.
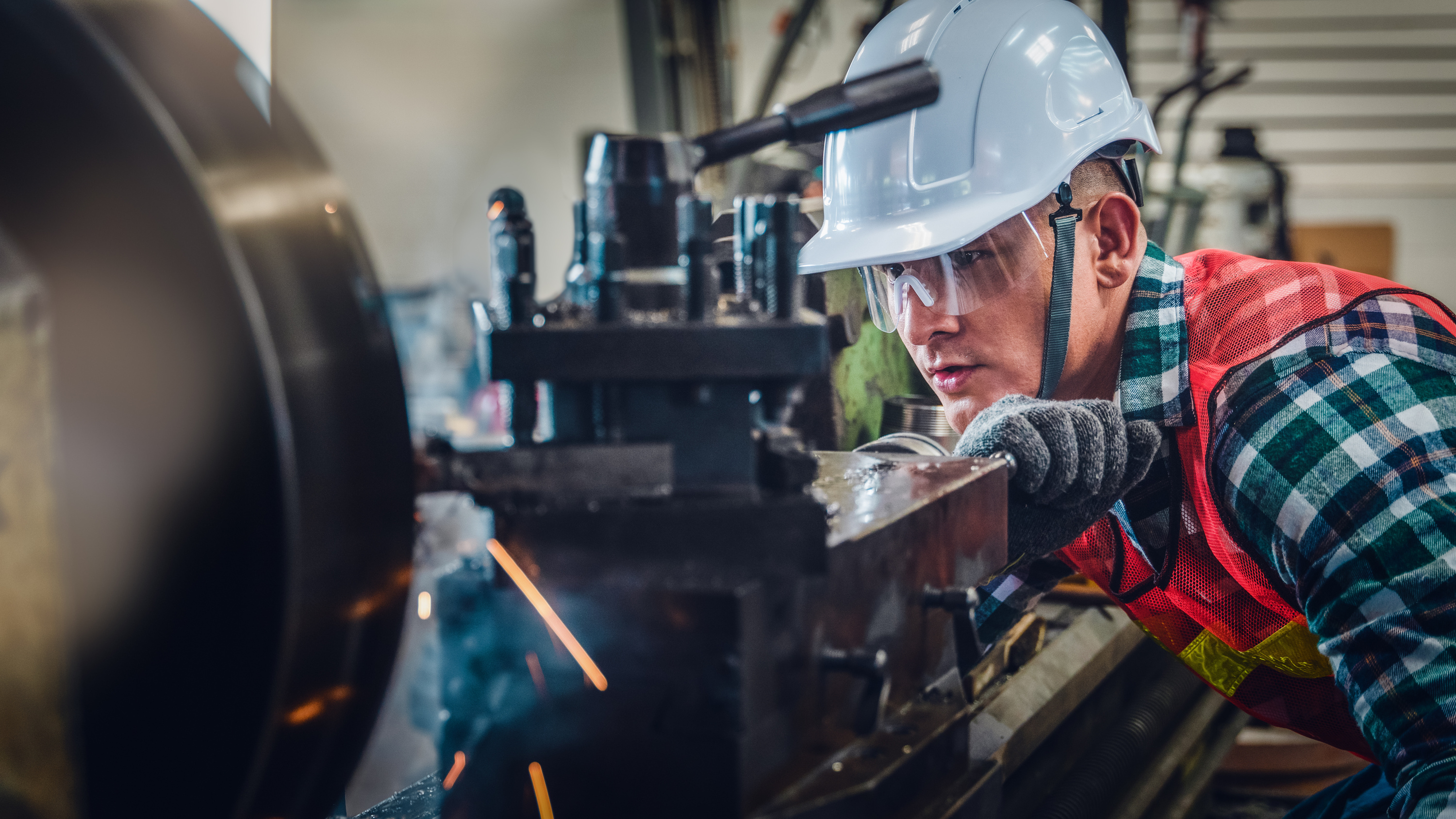
PM Increases Asset Useful Life
Going beyond present-day equipment reliability, another significant benefit of a PM program is keeping your assets functional for longer. Of course, a broken-down asset can be fixed by reactive or corrective maintenance, but you’re playing catch-up by that point.
One major downside of emergency maintenance work is the likelihood of maintenance teams or technicians reaching for the quickest possible solutions just to get a piece of equipment back up and running. When you address potential problems beforehand, you’re more likely to apply lasting solutions that preserve and extend the useful life of your critical equipment.
PM Increases Safety
Top on the list of your priorities should always be safety: for both your employees and your customers. Keeping your assets in good condition ensures that your employees are less likely to suffer any accidents due to defective equipment.
Similarly, an excellent preventive maintenance process guarantees the quality of your products won’t be compromised due to asset malfunction.
PM Increases Bottom Line
If you work in manufacturing, keeping your assets up and running means more time spent producing the goods that make you money. This, combined with savings in maintenance costs from a preventive maintenance program, can result in bottom-line gains for your organization.
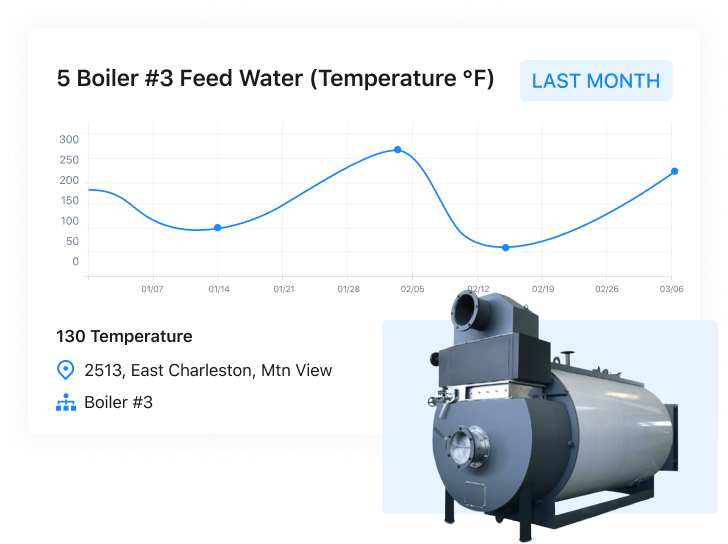
Use MaintainX for Your Preventive Maintenance
Whether it’s lubrication, safety audits, HVAC inspections, or pest control, MaintainX will help you optimize your preventive maintenance workflows. Create preventive maintenance checklists, assign work orders, and get real-time updates from the shop floor with our desktop and mobile-first apps.
FAQs
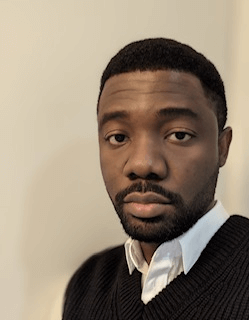
Lekan Olanrewaju is a content writer with years of experience in media and content creation. He has held positions at various media organizations, working with and leading teams at print magazines, digital publications, and television productions.