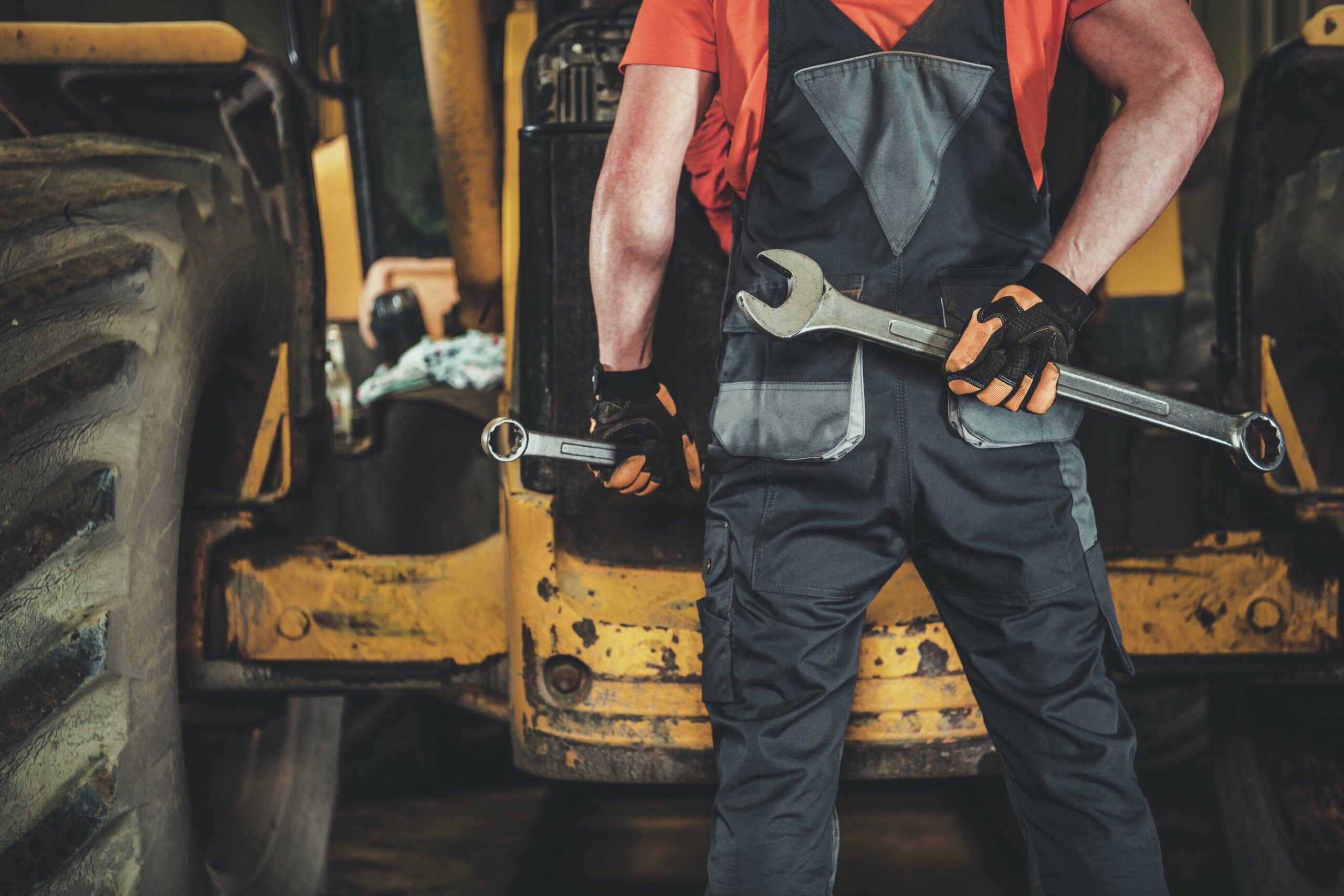
Preventive maintenance in manufacturing refers to regularly scheduled inspections, tests, and other maintenance activities performed on equipment and machinery in a factory or manufacturing setting. These activities are designed to identify and address potential problems before they can cause equipment breakdowns or downtime, disrupting production and negatively impacting the business.
Preventive maintenance is a type of planned maintenance instead of reactive maintenance. Reactive maintenance is the world’s oldest approach to maintenance. Also called “run-to-failure,” reactive maintenance refers to maintenance tasks performed after an asset has broken down.
A preventive maintenance strategy typically involves various activities, such as cleaning and lubricating equipment, replacing worn or damaged parts, and conducting regular inspections and tests to ensure the equipment operates correctly.
These activities are typically performed on a regular schedule, such as daily, weekly, monthly, or annually. Maintenance will depend on the type of equipment and the frequency of use.
The goal of a preventive maintenance plan is to reduce the likelihood of equipment failure and unplanned downtime, which can be costly for a manufacturing business.
The goal is to identify and address potential problems before they become significant issues. Preventive maintenance can help to ensure that equipment is operating at peak performance and can help to extend its useful life.
Additionally, regular preventive maintenance can help to improve the overall efficiency and productivity of the manufacturing process and lead to cost savings.
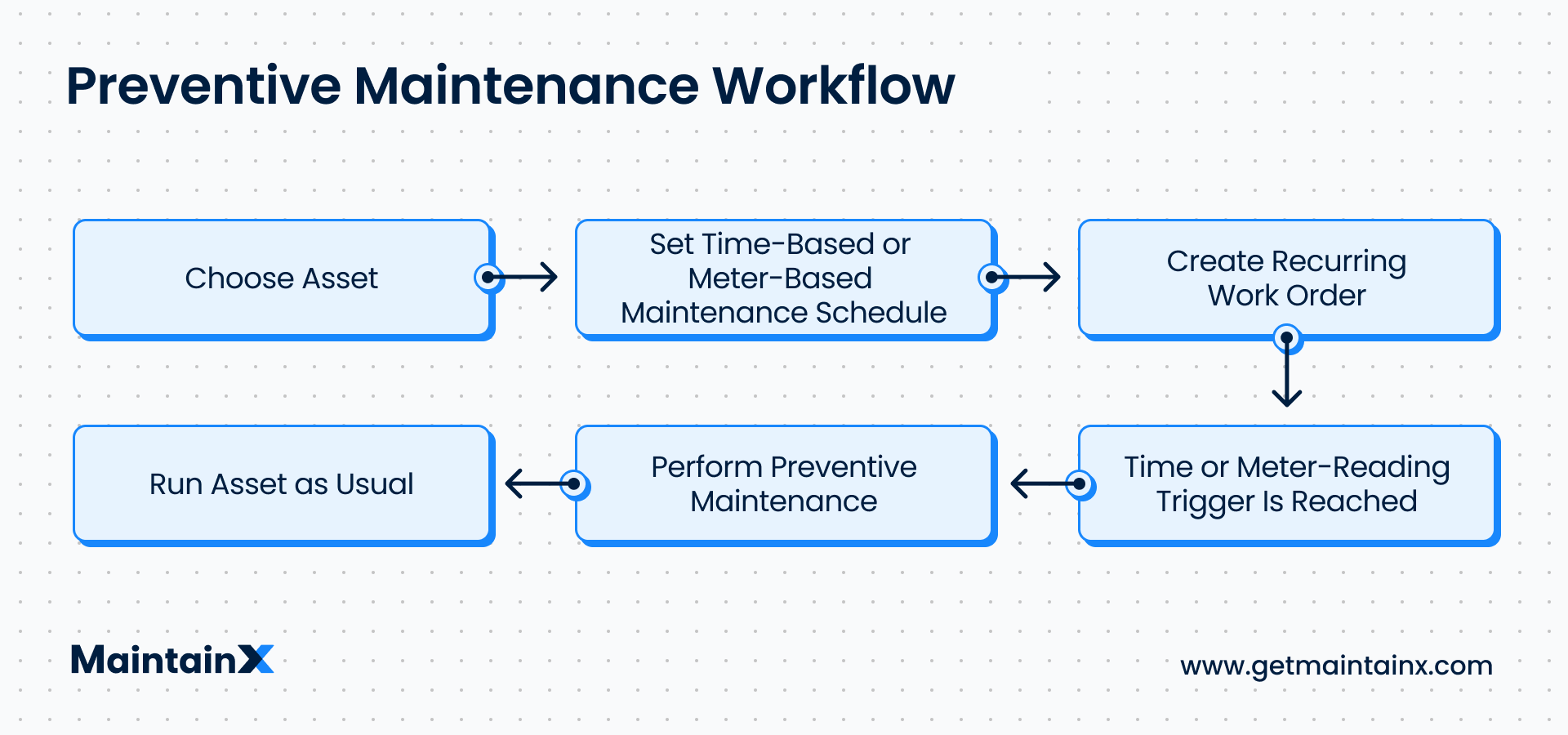
4 types of preventive maintenance in manufacturing
Four main types of preventive maintenance are commonly used in manufacturing settings. Examples of preventive maintenance include:
1. Periodic or Time-based preventive maintenance
This type of periodic preventive maintenance is based on the passage of time. It involves performing regular maintenance activities on equipment and machinery according to a set schedule. For example, a machine might be scheduled for cleaning and lubrication every week or a more thorough inspection and maintenance every six months.
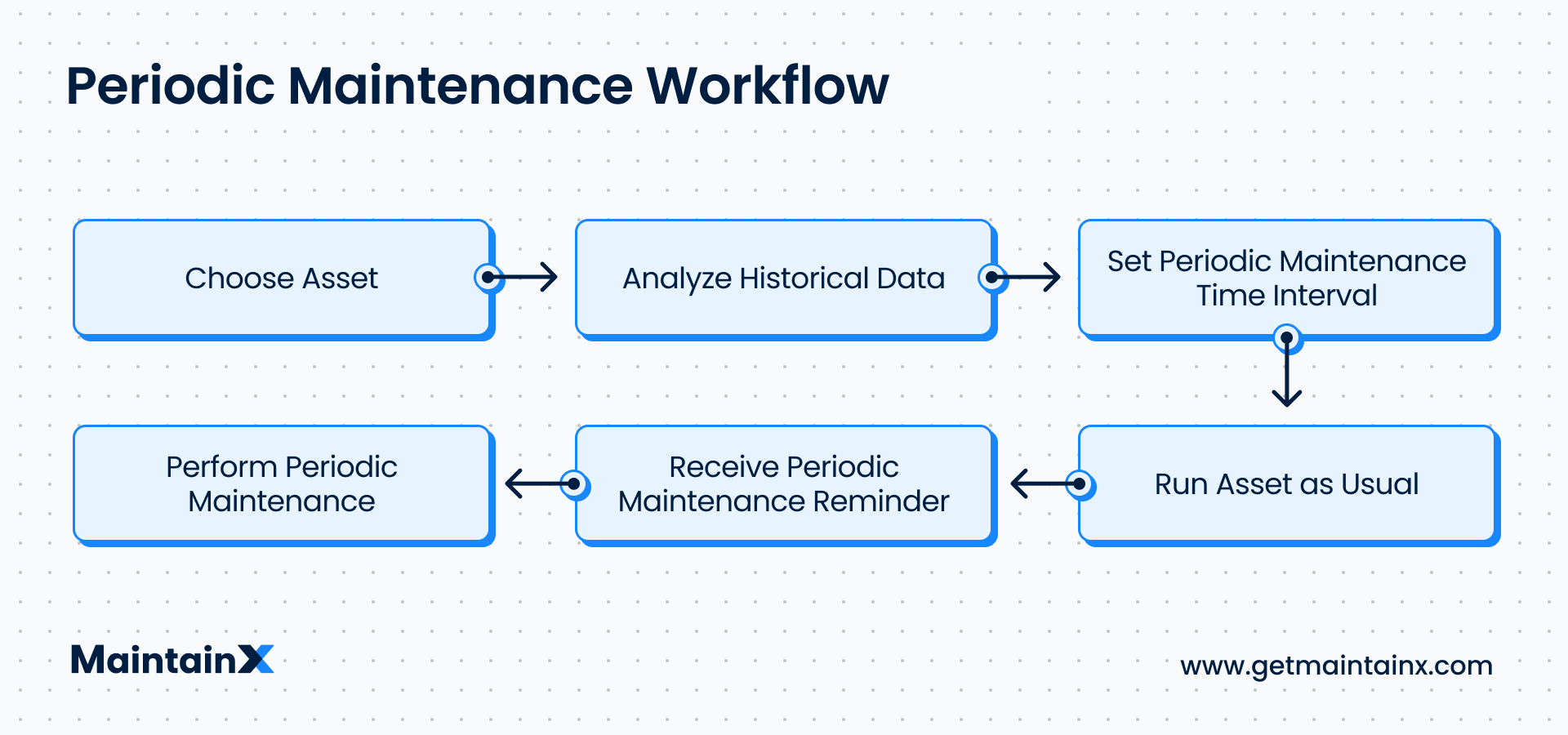
2. Usage-based preventive maintenance
This type of maintenance is a form of predictive maintenance (PdM). It is based on the amount of usage that equipment or machinery receives. In this case, maintenance activities are performed when a certain usage level has been reached.
For example, a machine used heavily might require more frequent maintenance than one used less frequently.
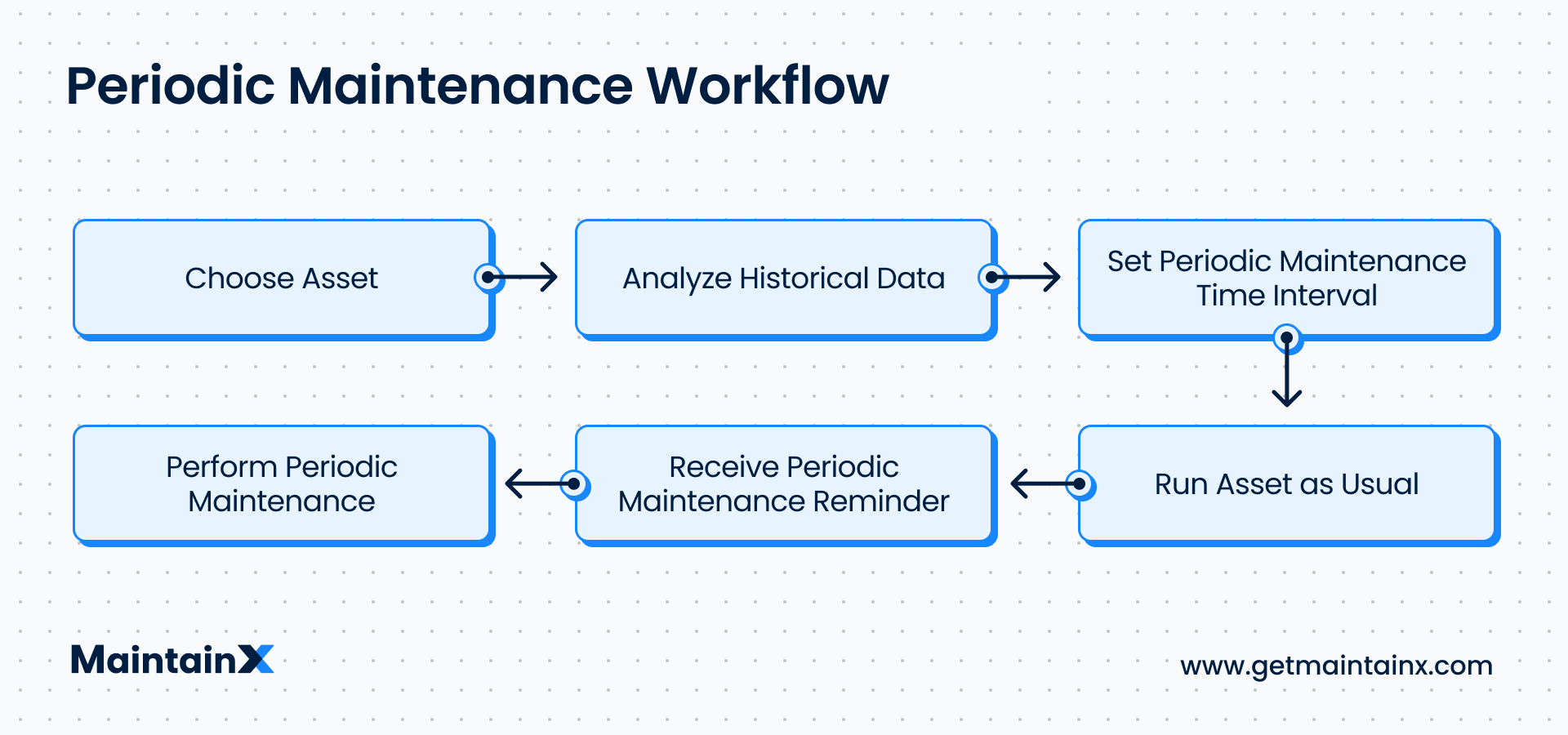
3. Condition-based preventive maintenance
This type of preventive maintenance is based on the current condition of equipment or machinery. In this case, technicians perform maintenance activities when specific indicators suggest that equipment is beginning to show signs of wear or degradation.
For example, technicians may monitor a machine for changes in its operating temperature or noise levels. They perform maintenance when these indicators exceed certain thresholds.
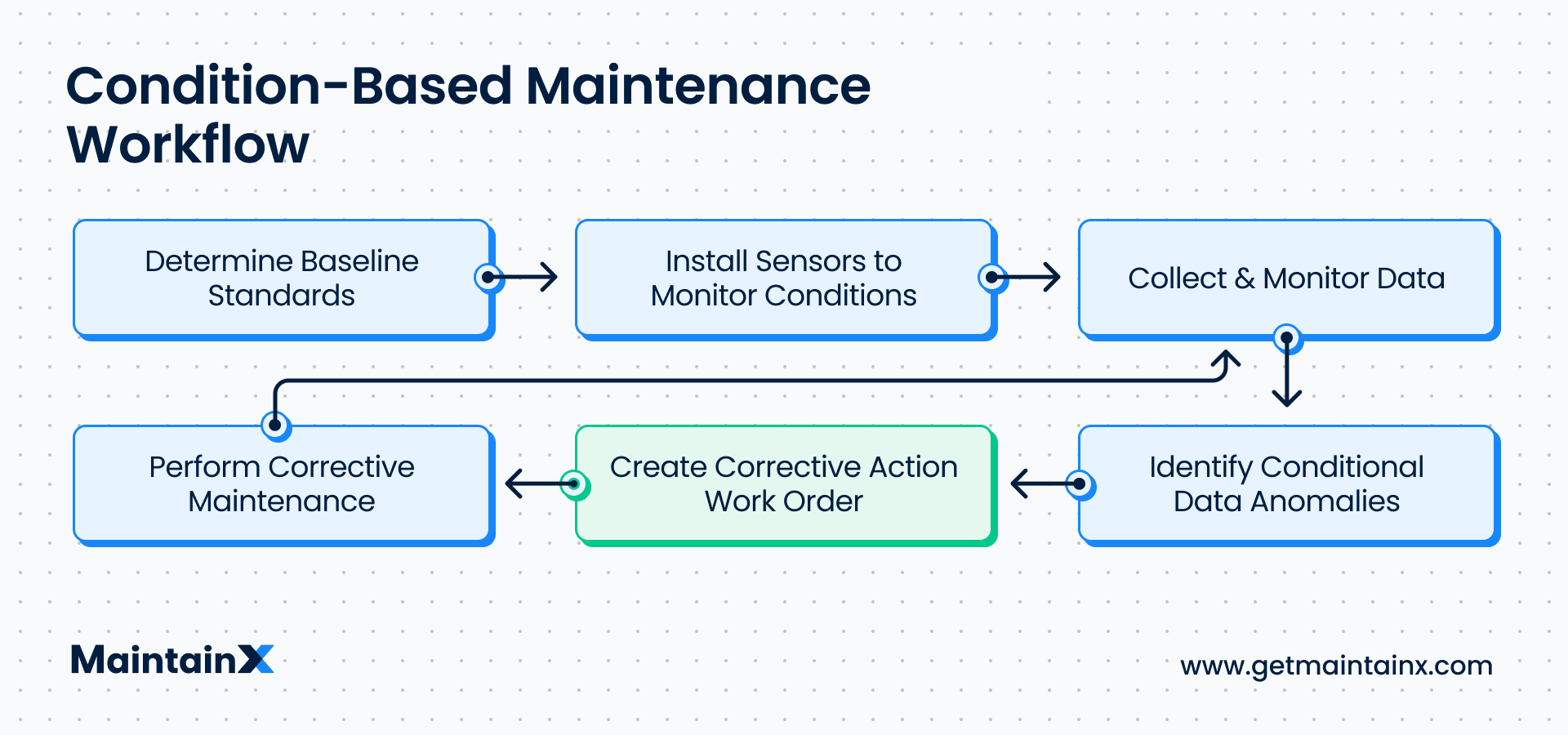
4. Predictive preventive maintenance
This type of preventive maintenance is based on using predictive analytics and other technologies to anticipate maintenance needs. In this case, management collects data from equipment and machinery. Mangers then analyze it to identify trends and patterns that signal when technicians should carry out maintenance.
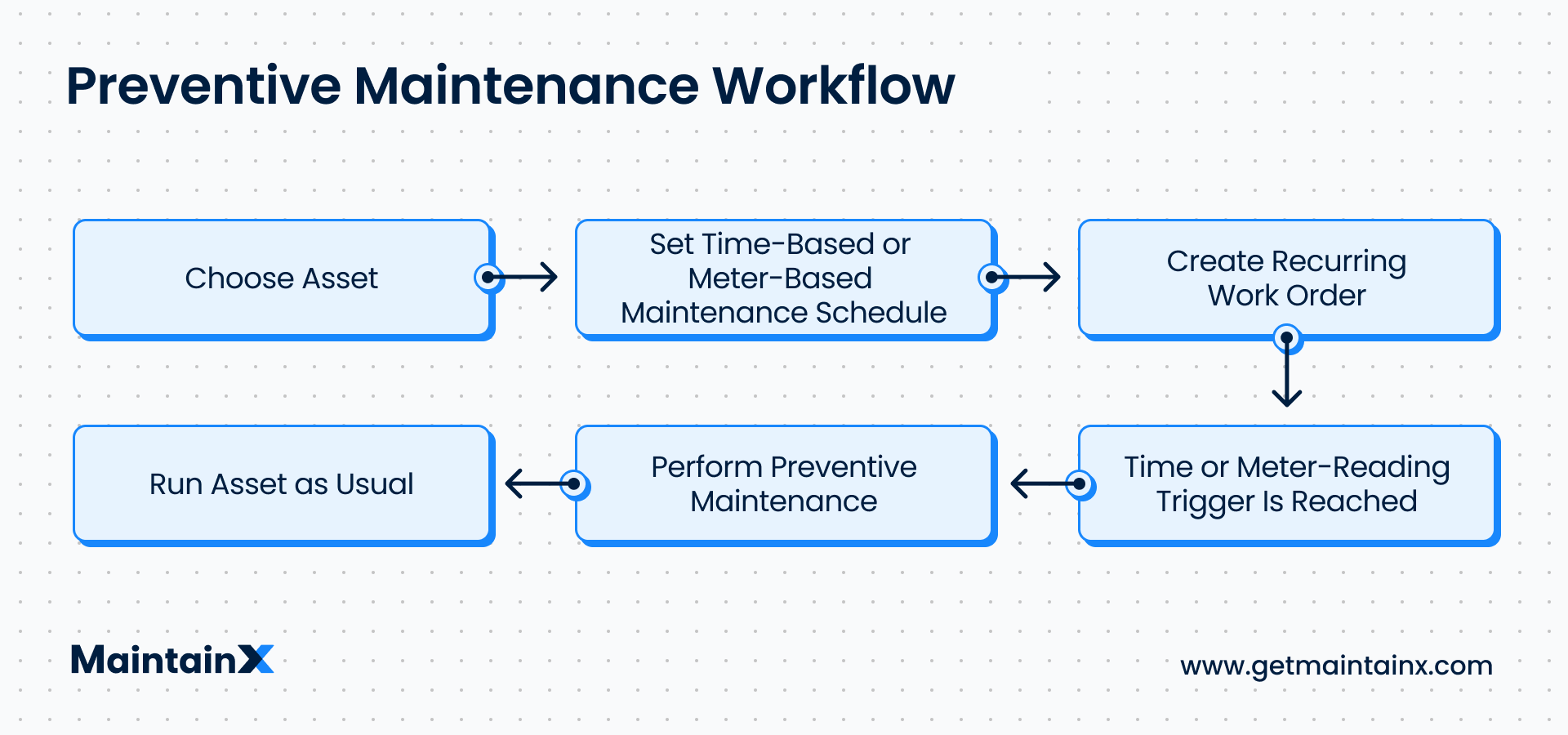
This can help to improve the accuracy and effectiveness of preventive maintenance efforts. It also helps to reduce the likelihood of equipment failure or downtime.
“Predictive maintenance programs have been shown to lead to a tenfold increase in ROI, a 25%-30% reduction in maintenance costs, a 70%-75% decrease of breakdowns and a 35%-45% reduction in downtime.”
Forbes
7 elements of preventive maintenance in manufacturing
The seven elements are the key components that make up a comprehensive preventive maintenance program. These elements include:
1. Planning
The first element of preventive maintenance is planning (included in a PDCA cycle). This involves identifying the specific equipment and machinery included in the program and the types of maintenance activities that technicians will perform. Planning also involves setting up a schedule for performing these activities and establishing procedures for tracking and documenting maintenance activities.
Standard operating procedures (SOPs) are detailed instructions (and checklists) that outline the steps technicians need to perform for a specific task or process. Companies use SOPs to document the procedures for performing preventive maintenance on equipment and the procedures for responding to equipment failures.
Work orders are documents that request and track maintenance work. They typically include details about the equipment or facility that needs maintenance, the required maintenance, and the date and time the work is to be performed.
2. Inspection
The second element of preventive maintenance is inspection. This involves regularly examining equipment and machinery to identify potential problems or issues. Technicians can do this visually, using tools and instruments, or using advanced technologies such as infrared cameras or ultrasound equipment. OSHA inspections are especially important to manage.
3. Cleaning
The third element of preventive maintenance tasks is cleaning, which involves removing dirt, debris, and other contaminants from equipment and machinery. This can help to prevent the build-up of these materials, which can cause equipment failure or other problems.
4. Lubrication
The fourth element of preventive maintenance is lubrication. This involves applying lubricants to equipment and machinery to reduce friction and wear. This can help extend the equipment’s useful life and improve its overall performance.
5. Adjustment
The fifth element of preventive maintenance is adjustment. This involves making small adjustments to equipment and machinery to ensure that they are operating within their optimal parameters. This can include adjusting tension on belts or chains, aligning parts, or making other small changes to improve performance. OEE (overall equipment effectiveness) is a useful KPI to measure optimal performance.
6. Replacement
The sixth element of preventive maintenance is replacement, which involves replacing worn or damaged parts on equipment and machinery. This can help prevent equipment failure and downtime and extend the equipment’s useful life. It’s important to ensure that spare parts inventory is up-to-date and automated so critical assets are always up and running.
7. Documentation
The seventh and final element of preventive maintenance is documentation, which involves keeping detailed records of all maintenance activities. This can help track the effectiveness of your preventive maintenance program. It also provides valuable information for future maintenance and repair activities.
“An example of facility operations would be a manufacturing facility. The main concern in facility operations is operational in nature, such as ensuring that day-to-day management meets the objectives of the organization. There are also strategic concerns, as well, such as an imperative to follow best practices, meet productivity and efficiency standards, and satisfy legal and safety requirements.”
Investopedia
5 benefits of preventive maintenance in manufacturing
Preventive maintenance in manufacturing can provide a range of benefits, including:
1. Improved equipment performance
By regularly inspecting, cleaning, and lubricating equipment and machinery, manufacturers can help to ensure that their equipment is operating at peak performance. This can help to improve production efficiency and productivity and can reduce the likelihood of equipment failure or downtime.
2. Extended equipment lifespan
Regular preventive maintenance can help extend equipment and machinery’s useful life. By identifying and addressing potential problems before they become major issues, manufacturers can prevent pieces of equipment from wearing out prematurely and can help to save on the costs of replacing equipment.
3. Increased safety
By regularly inspecting and maintaining equipment, manufacturers can help ensure that their equipment operates safely. This can reduce the risk of accidents or injuries and can help to create a safer working environment for employees.
4. Better resource allocation
By tracking and managing maintenance activities using a computerized maintenance management system (CMMS), manufacturers can more effectively allocate their resources to the most important tasks. This can help to improve the efficiency of their maintenance efforts and can help to reduce the overall costs of maintaining equipment.
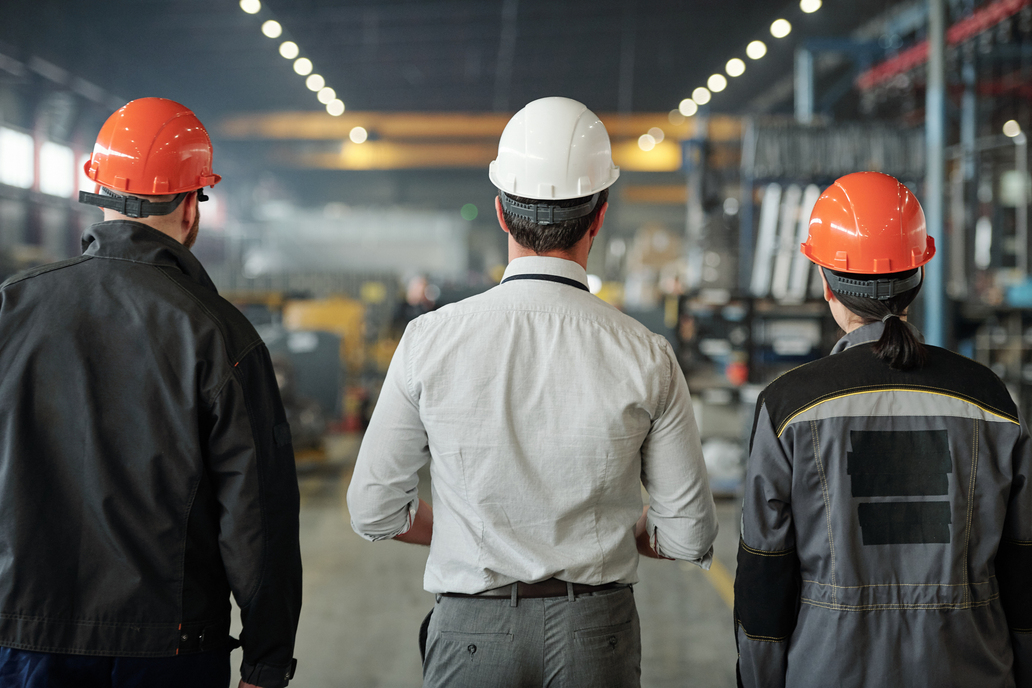
5. Improved compliance
Regular preventive maintenance can help manufacturers to comply with industry regulations and standards. By regularly inspecting and maintaining equipment, manufacturers can demonstrate that they are taking the necessary steps to ensure the safety and performance of their equipment, which can help protect their business and reputation.
3 PM manufacturing examples
Here are three examples of a preventive maintenance schedule in manufacturing:
1. Machinery cleaning and lubricating
In many manufacturing processes, machinery is subjected to high levels of heat, pressure, and friction, which can cause it to wear out quickly if it is not properly maintained.
To prevent this, manufacturers may perform regular cleaning and lubrication of their machinery as part of their preventive maintenance program. This can involve using cleaning agents to remove dirt and debris and applying lubricants to reduce friction and wear on moving parts.
2. Electrical system inspection and testing
Electrical systems are critical to the operation of many manufacturing processes, and failure of these systems can cause costly downtime. As part of their preventive maintenance program, manufacturers may perform regular inspections and tests of their electrical systems to identify and address potential problems before they can cause equipment failure. This can involve visual inspections of wiring and connections and the use of specialized testing equipment to check the condition of electrical components.
3. Regular replacement of filters and consumable parts
Many manufacturing processes involve using filters and other consumable parts that technicians must regularly replaced to maintain equipment performance.
As part of their preventive maintenance program, manufacturers may regularly establish a schedule for replacing these parts. Up-to-date inventory is crucial to increase equipment uptime.
A CMMS with robust parts inventory is a crucial aspect of this routine maintenance workflow. This helps maintenance technicians be able to keep equipment operating at peak performance. Proactive maintenance here means replacing parts before equipment failure, obviously reducing downtime.
Implement a CMMS to boost your manufacturing PM progam
A computerized maintenance management system (CMMS) is a software tool that can help with preventive maintenance in manufacturing. A robust CMMS helps organizations manage their maintenance activities and equipment more effectively and can provide a range of benefits when it comes to preventive maintenance.
Centralized and digital Platform
One of the key ways that a CMMS can help with preventive maintenance is by providing a centralized, digital platform for tracking and managing maintenance activities.
With a CMMS, organizations can create a schedule for performing preventive maintenance activities on their equipment and machinery and track the completion of these activities in real time. This can help to ensure that teams perform maintenance activities on time and according to schedule and can help to prevent equipment failure or downtime.
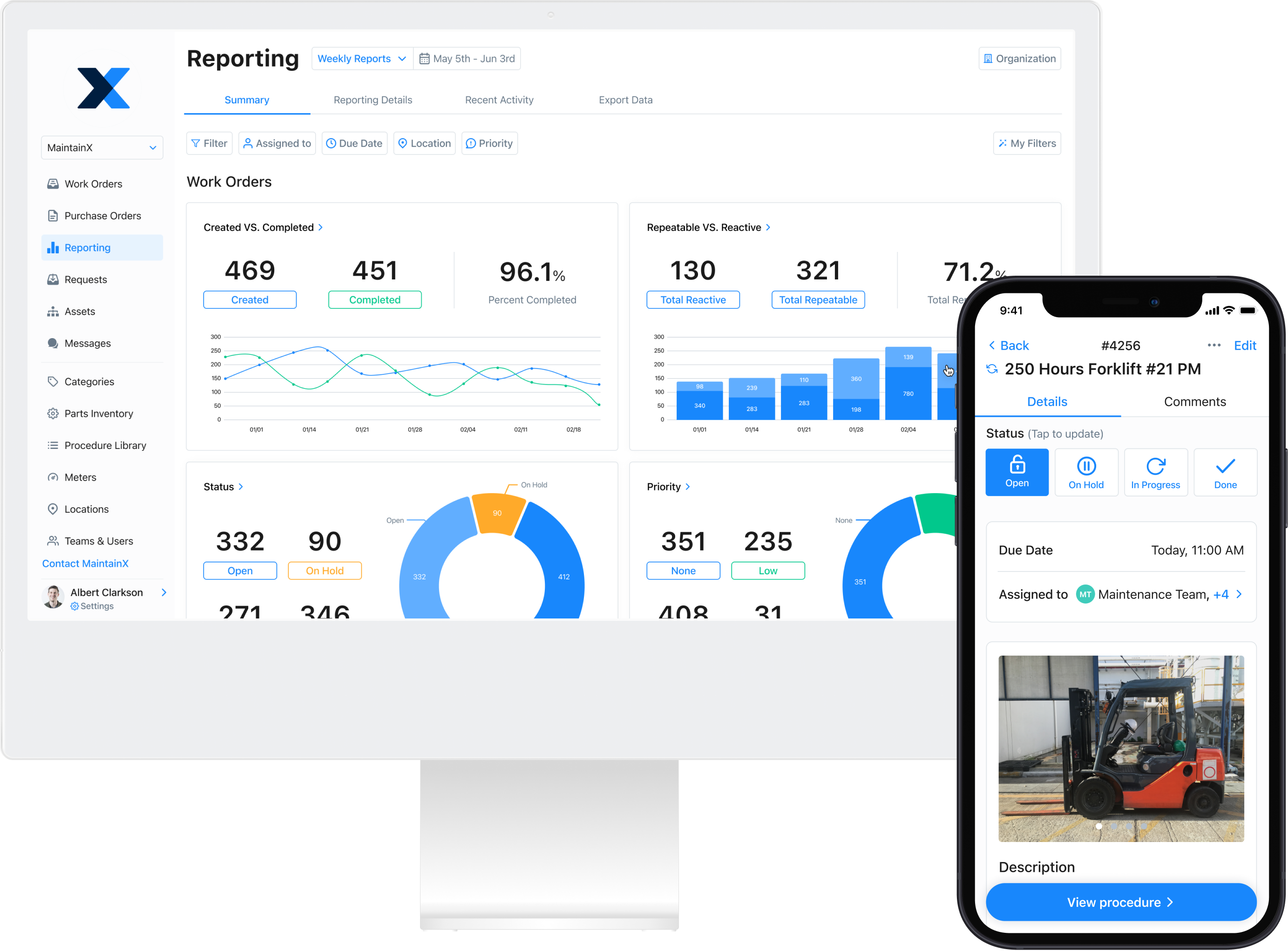
Maintenance key performance indicators (KPIs)
Key Performance Indicators (KPIs) are metrics used to measure the effectiveness and efficiency of a company’s maintenance processes. These metrics help organizations track and improve their maintenance operations by clearly showing how well they are performing.
Two maintenance KPIs are Mean Time Between Failures (MTBF) and Mean Time To Repair (MTTR)
MTBF
MTBF is a maintenance metric that measures the standard amount of time between expected equipment failures for an asset performing under normal operational usage. To calculate MTBF, divide the total uptime of a repairable asset by the number of failures of that asset within a given period to arrive at an hourly measurement.
MTBF = Total Uptime of Repairable Asset / Number of Failures of Asset within given time period
MTTR
Mean Time To Repair (MTTR) measures the amount of time it takes to repair a piece of equipment after it has failed.
Calculate Mean Time to Repair (MTTR) by tracking the total amount of time an asset undergoes recovery after downtime, then dividing it by the number of times the asset in question has failed within a given time.
MTTR Formula:
MTTR = Total Maintenance TIme ÷ # of Repairs
Notably, MTTR doesn’t depend on an asset’s uptime. It only factors in how long each unplanned stoppage lasts.
By tracking these metrics, organizations can identify areas for improvement in their maintenance processes and make necessary changes to increase efficiency and reduce downtime.
Improved efficiency
Additionally, a CMMS can help improve preventive maintenance efficiency by automating specific tasks and providing access to essential data and information.
For example, a CMMS can automatically generate maintenance schedules based on equipment usage or other factors and provide alerts when maintenance is due.
Overall, a CMMS can be a valuable tool for improving the effectiveness of preventive maintenance in manufacturing and reducing maintenance costs.
With a CMMS, maintenance KPIs, preventive maintenance, standard operating procedures, and work orders are all essential tools and techniques that organizations can use to improve the effectiveness and efficiency of their maintenance operations.
By tracking and analyzing these metrics and processes, organizations can identify areas for improvement and make necessary changes to increase efficiency and reduce downtime.
MaintainX is a comprehensive manufacturing preventive maintenance CMMS that helps businesses streamline their maintenance operations. It provides an intuitive user interface and powerful analytics to help businesses make informed decisions.
MaintainX also offers a range of features that help businesses maximize the effectiveness of their preventive maintenance operations. These include automated scheduling and tracking, real-time alerts, and detailed reporting.
In addition, MaintainX offers an extensive library of templates and workflows that businesses can use to create custom maintenance plans and schedules. Businesses can easily develop customized preventive maintenance strategies tailored to their specific needs.
FAQs
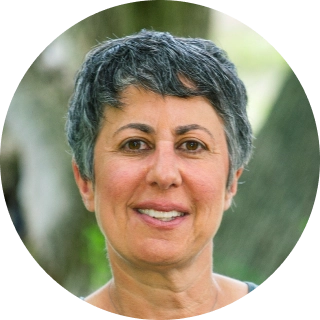
Caroline Eisner is a writer and editor with experience across the profit and nonprofit sectors, government, education, and financial organizations. She has held leadership positions in K16 institutions and has led large-scale digital projects, interactive websites, and a business writing consultancy.