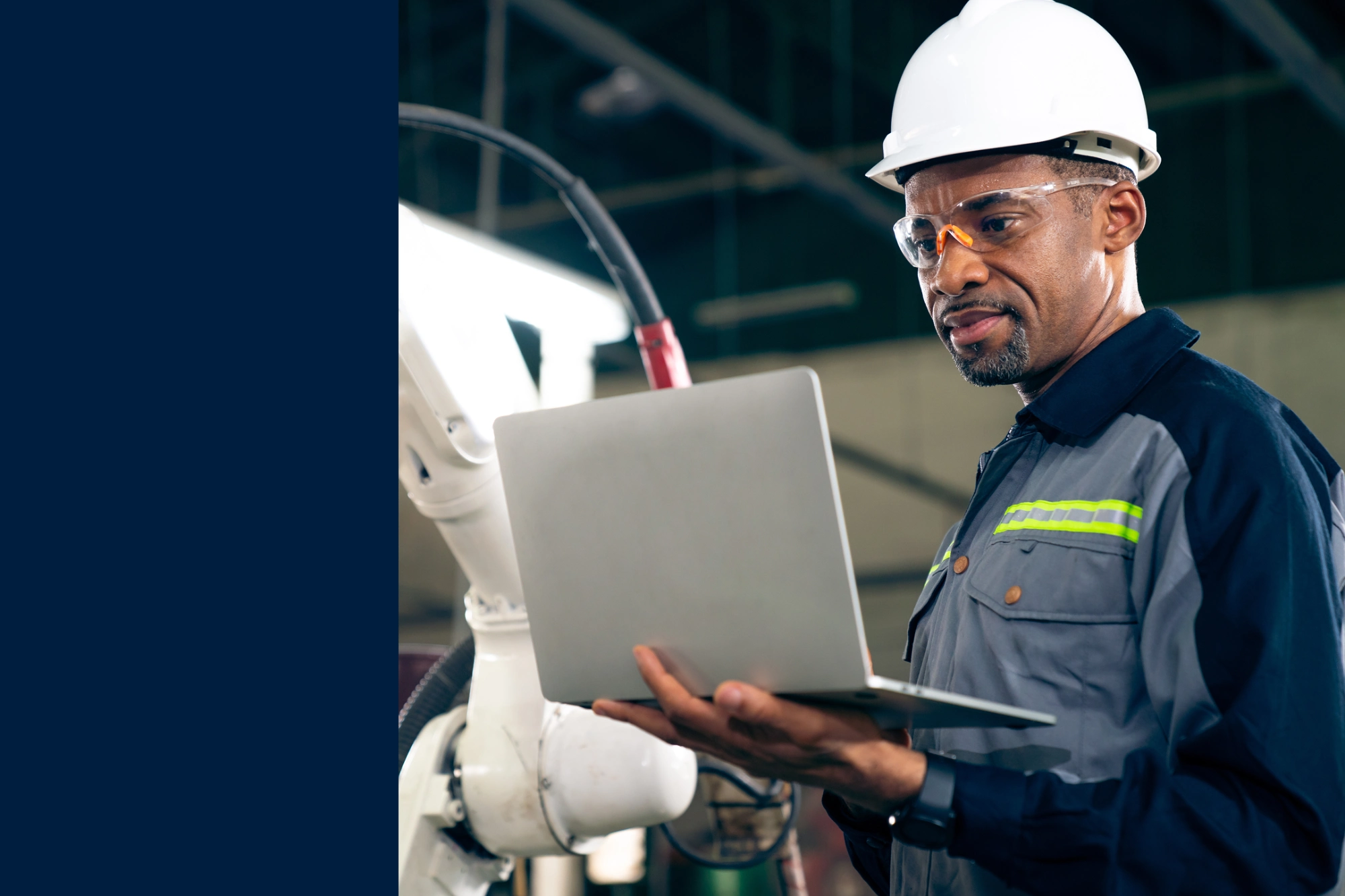
If you’ve ever sat at home sweating in the summer because your air conditioning is broken, or bundled up in the winter when your heating is on the fritz, you know the importance of HVAC maintenance. Scale that up 100X or 1000X, and imagine the problems you get in an industrial setting when these systems go kaput. A poorly maintained 20-ton rooftop AC unit typically fails after just nine years, while a well-maintained unit can reach its expected 14-year lifespan or beyond. The difference in operational costs and replacement timing represents significant savings for businesses that invest in regular preventive maintenance.
Depending on your industry, you could be looking at production lines shutting down due to overheated equipment in manufacturing plants, food spoilage in restaurants and food processing facilities, or damaged inventory in warehouses. Whatever industry you’re in, you’ll be looking at costly downtime, fines for non-compliance, and repairs.
Thus, commercial HVAC maintenance is a must for any enterprise to maintain operational efficiency, ensure regulatory compliance, and protect valuable assets. It can help you prevent costly emergency repairs and business interruptions that can damage both your bottom line and reputation.
Key Takeaways
- A comprehensive maintenance program includes daily monitoring, monthly preventive care, and professional seasonal servicing.
- Proper maintenance significantly extends equipment life—well-maintained units can last 5+ years longer than neglected systems.
- Using CMMS software to track maintenance helps ensure consistent upkeep and enables data-driven decision making.
Understanding commercial HVAC maintenance
Commercial HVAC systems are complex networks of heating, cooling, and ventilation components that work together to maintain optimal indoor conditions in commercial buildings. Modern HVAC equipment often contains more than 100 interconnected parts, from air filters and blower components to sophisticated electrical connections and cooling components. When any single element encounters problems, the entire system's efficiency can decline dramatically, affecting indoor air quality, energy bills, and overall operations.
What is preventative HVAC maintenance?
Preventative maintenance for commercial HVAC systems involves conducting routine inspections, cleaning, and servicing equipment before problems occur. This proactive approach includes regular tasks such as changing air filters, cleaning condenser coils, checking electrical components, and ensuring proper airflow throughout your ventilation systems.
A comprehensive preventive maintenance program typically includes:
- Scheduled service visits by qualified technicians
- Regularly inspecting all heating components and cooling components
- Systematically checking electrical connections and thermostat settings
- Cleaning or replacing air filters on a consistent schedule
- Examining the heat exchanger and cooling systems
- Testing the heat pump system or air conditioning components
- Verifying gas pressure and checking for gas leaks
- Monitoring drain pans and ventilation systems
The cost of neglecting HVAC maintenance
Failing to maintain your commercial HVAC system can lead to significant consequences for any business owner. Equipment failure due to neglect often results in costly repairs that could have been avoided through routine maintenance.
The true cost of neglecting HVAC maintenance includes:
- Increased energy bills due to inefficient operation
- More frequent equipment failure requiring emergency repairs
- Shortened lifespan of your HVAC unit and components
- Loss of fresh air circulation and proper airflow
- Potential safety issues from undetected gas leaks or electrical problems
Essential components of a commercial HVAC system
A commercial HVAC system is far more complex than systems in residential units. It comprises multiple interconnected components that work together to maintain optimal indoor conditions.
Components that require regular maintenance
Modern commercial HVAC equipment consists of several major component groups that each require specific maintenance attention. These critical systems include:
- Air handling and filtration systems, including air filters, blower components, and comprehensive ventilation systems. These components work together to ensure proper airflow and maintain indoor air quality throughout your commercial space.
- Cooling systems, including condenser coils, evaporator units, and sophisticated compressor systems. In many commercial HVAC systems, variable refrigerant flow or multi-split systems provide flexible cooling solutions.
- Heating systems, including heat exchangers, commercial heating elements, and heat pump systems. This can also include critical safety elements such as flue systems and gas pressure regulators.
- Electrical and control systems, including electrical connections, thermostat settings, and various safety switches that control system operation.
- Drainage and ventilation systems, including drain pans, condensate lines, fresh air intake systems, and comprehensive ventilation networks that maintain comfortable conditions in your commercial building.
A Computerized Maintenance Management Systems (CMMS) system can help track maintenance for each of these component groups, automatically generating work orders and maintaining detailed service histories for every part of your HVAC system.
Common system types and their maintenance needs
Different types of commercial HVAC systems require varying approaches to maintenance.
Rooftop package units
These all-in-one systems combine heating and cooling components in a single outdoor unit. Maintenance includes comprehensive quarterly inspections of condenser coils, air filter changes, and refrigerant level checks.
Split systems
Common in smaller commercial spaces, these systems separate indoor and outdoor units for more flexible installation. Maintenance must address both indoor air handler maintenance and outdoor unit cleaning. Teams need to think about regular refrigerant line inspection, air filter replacement, and periodic thermostat calibration.
Variable Refrigerant Flow (VRF) systems
These systems offer simultaneous heating and cooling capabilities and require specialized maintenance from qualified technicians who understand their workings. Regular maintenance should focus on electrical component checks, refrigerant monitoring, and control system verification.
Chiller systems
Typically found in larger commercial buildings, chiller systems require regular water treatment, tube cleaning, and compressor maintenance. Cooling tower upkeep is particularly critical in these systems, as poor maintenance can lead to reduced efficiency and increased energy bills.
Commercial HVAC maintenance checklist
Different maintenance tasks need to be performed at varying intervals to ensure optimal performance and prevent system failure. Using CMMS software to manage these maintenance schedules ensures consistent execution and provides valuable data for optimizing your maintenance program over time. Here’s a simple maintenance checklist for commercial HVAC maintenance.
Daily and weekly maintenance tasks
Regular monitoring and basic maintenance should be part of your facility maintenance’s daily operations. These frequent checks help catch potential issues before they become major problems:
- Daily visual inspections
- Monitor your commercial HVAC equipment for unusual sounds, vibrations, or odors.
- Check thermostat settings and indoor air quality in different zones of your commercial space.
- Ensure all vents and returns have proper airflow and aren't blocked by furniture or equipment.
- Weekly system checks
- Perform basic inspection of visible components.
- Visually check air filters for obvious debris or damage.
- Inspect outdoor units for debris or blockages.
- Check drain pans for proper drainage.
- Verify that all access panels are secure.
Monthly maintenance procedures
Monthly maintenance tasks require more thorough attention and often involve preventive maintenance steps that help maintain system efficiency:
- Filter maintenance. Replace or clean air filters based on usage and environment. Commercial HVAC systems in dusty or high-traffic areas may need more frequent filter changes to maintain proper airflow and indoor air quality.
- System performance checks. These include:
- Inspecting belts and pulleys for wear
- Checking and cleaning drain pans and condensate lines
- Testing electrical connections and controls
- Monitoring refrigerant levels in cooling systems
Quarterly and annual maintenance
Qualified technicians should perform these more comprehensive inspections as part of your regular commercial HVAC services:
- Quarterly tasks:
- Complete inspection of all heating components and cooling components
- Thoroughly cleaning condenser coils and evaporator coils
- Testing all electrical connections and safety controls
- Comprehensive check of refrigerant levels and pressure
- Inspecting heat exchangers and flue systems
- Annual maintenance:
- Full system performance evaluation
- Deep cleaning all components
- Calibrating all controls and thermostat settings
- Complete testing of heating systems before winter
- Thorough inspection of cooling systems before summer
- Professional cleaning of ductwork and ventilation systems
- Detailed inspection of all electrical components
- Comprehensive safety check of gas pressure and connections
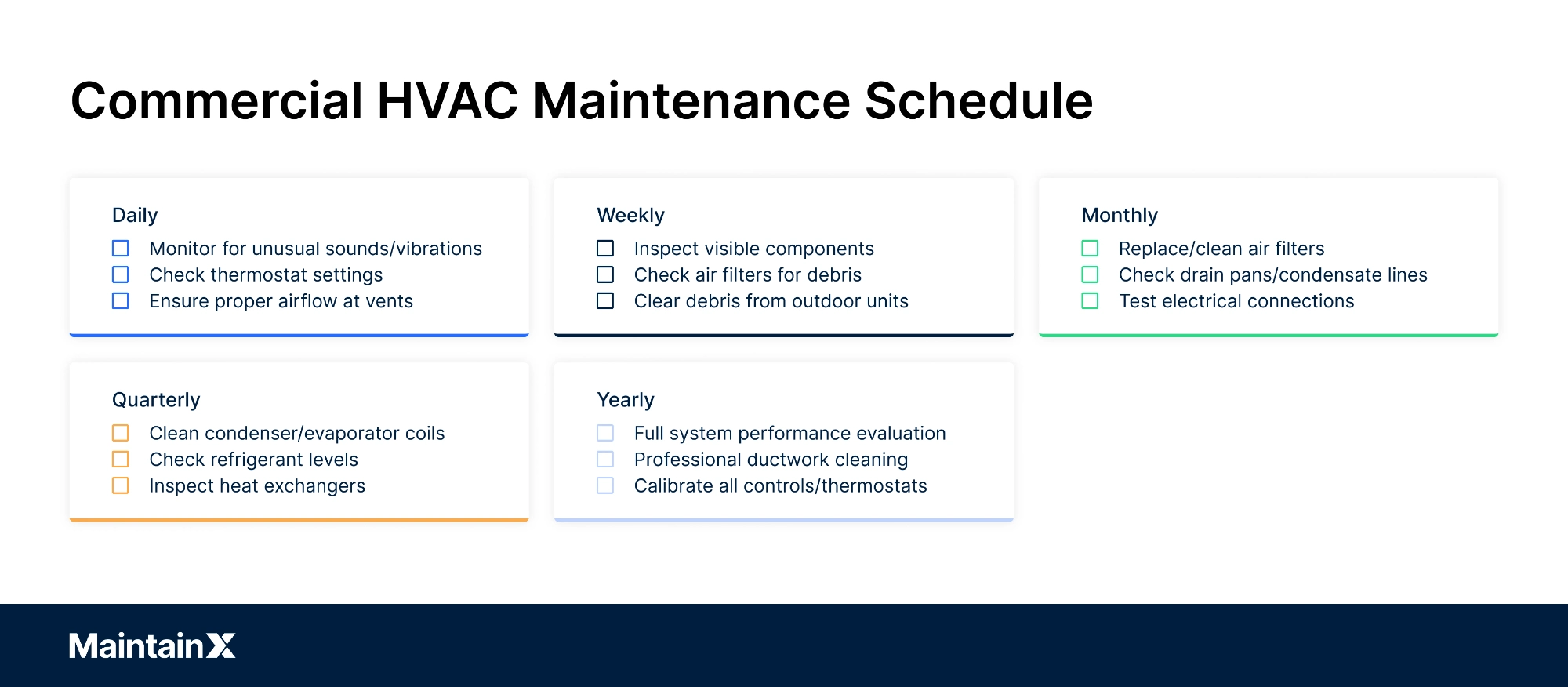
Seasonal maintenance guidelines
Proper commercial HVAC maintenance requires special attention to seasonal changes, as your system faces different challenges throughout the year. Modern CMMS platforms can automatically adjust maintenance schedules based on seasonal requirements, ensuring your team stays ahead of weather-related challenges.
Spring preparation (pre-cooling season)
Before summer heat arrives, technicians should inspect your cooling systems. This ensures all cooling components are ready for peak performance. Key spring maintenance includes:
- Shutting down heating systems properly
- Cleaning or replacing air filters
- Cleaning condenser coils
- Checking refrigerant levels
- Inspecting all outdoor units and clearing winter debris
- Testing and calibrating thermostat settings for cooling mode
- Checking that economizers and fresh air intakes are working correctly
Summer maintenance
During peak cooling season, your commercial HVAC system needs regular attention to maintain efficient operation and prevent breakdowns when cooling demand is highest. Focus areas include:
- Cooling system performance: Regularly monitor AC unit performance, including proper airflow and temperature differentials. Qualified technicians should check refrigerant pressure and clean condenser coils as needed to maintain energy efficiency.
- Ventilation and air quality: Maintain proper fresh air circulation and indoor air quality during high-usage periods. This includes regular air filter changes and ensuring all ventilation systems are operating correctly.
Fall preparation (pre-heating season)
Before cold weather arrives, inspection of all heating components is crucial. Fall maintenance tasks include:
- Properly shutting down cooling systems
- Testing heat exchangers and heating elements
- Cleaning and preparing heating components
- Checking gas pressure and connections
- Inspecting flue systems and venting
- Checking all safety controls
- Calibrating thermostats for heating mode
- Ensuring proper ventilation for heating season
Winter maintenance
During heating season, your commercial HVAC equipment needs special attention to maintain safe and efficient operation. Protect your HVAC equipment from winter damage by:
- Maintaining proper insulation on exposed components
- Checking heat tape and freeze protection systems
- Checking heat pump systems
- Ensuring proper drainage to prevent ice formation
- Monitoring fresh air intake systems to prevent freezing
Implementing an effective maintenance program
A cornerstone of any maintenance program is comprehensive documentation and record-keeping. Facility managers must maintain detailed equipment specifications, warranty information, and service histories to track performance trends and justify maintenance investments. Regularly review these records to identify patterns and potential issues before they become major problems.
Staff training and resources form another crucial element of an effective program. Maintenance personnel need proper training on basic HVAC system operation, safety procedures, and emergency protocols. Investing in human capital ensures daily maintenance tasks are performed correctly and potential issues are identified early.
Tracking maintenance with CMMS software
Modern commercial HVAC maintenance relies heavily on CMMS for operations and to ensure consistent service. These powerful tools transform maintenance from a reactive process to a proactive strategy.
The scheduling capabilities of CMMS software provide significant advantages to facility managers. The system can:
- Automatically generate work orders based on maintenance schedules.
- Send timely reminders for upcoming tasks.
- Track completion of routine maintenance activities.
- Adjust schedules based on equipment performance and conditions.
These systems maintain complete service histories for each piece of equipment, including parts replacement, repairs, and performance data. This record-keeping helps facilities maintain warranty compliance and optimize maintenance schedules.
Resource management becomes more efficient through CMMS software, allowing facilities to track inventory, schedule technicians, and coordinate with vendors more effectively. The system helps managers optimize their maintenance budget by providing clear insights into costs and resource allocation.
Perhaps most importantly, CMMS systems enable data-driven decision-making through advanced performance analysis. By tracking energy efficiency metrics and equipment performance patterns, these systems can help predict potential failures before they occur, allowing for proactive maintenance interventions that prevent costly breakdowns and extend equipment life.
Streamline your commercial HVAC maintenance
Success in maintaining commercial HVAC systems requires a multi-layered approach:
- Establish clear maintenance schedules for daily, monthly, and seasonal tasks.
- Ensure qualified technicians perform all major maintenance work.
- Utilize modern tools like CMMS software to track and manage maintenance activities.
- Pay special attention to seasonal transitions and weather-related challenges.
By following the guidelines and checklists outlined in this guide, you can develop a robust maintenance program that keeps your commercial HVAC equipment running efficiently year-round. The key is consistency—regular, thorough maintenance performed by qualified professionals will help ensure your HVAC system delivers reliable performance and optimal indoor comfort for years to come.
FAQs on Commercial HVAC Maintenance
How do you maintain a commercial HVAC system?
Commercial HVAC maintenance requires a multi-tiered approach that combines daily inspections, monthly preventive care, and professional seasonal servicing. Key activities include regular air filter changes, cleaning condenser coils, checking electrical connections, and monitoring system performance. A comprehensive maintenance program should utilize qualified technicians for major service work and CMMS software to track maintenance schedules and system performance.
What are the four types of maintenance HVAC?
The four main types of commercial HVAC maintenance are:
- Daily/weekly maintenance—basic inspections and monitoring of system performance.
- Preventive maintenance—regularly scheduled service to prevent problems before they occur.
- Seasonal maintenance—specific tasks performed during spring and fall to prepare for cooling and heating seasons.
- Predictive maintenance—using data and monitoring to anticipate and prevent potential system failures.
What maintenance is required on an HVAC system?
Essential maintenance tasks include:
- Regular air filter replacement and cleaning
- Inspection and cleaning of condenser coils and evaporator coils
- Checking and tightening electrical connections
- Monitoring refrigerant levels and pressure
- Testing safety controls and thermostat settings
- Cleaning drain pans and condensate lines
- Professional inspection of heating components and cooling components at least twice yearly
- Seasonal preparation for both heating and cooling modes
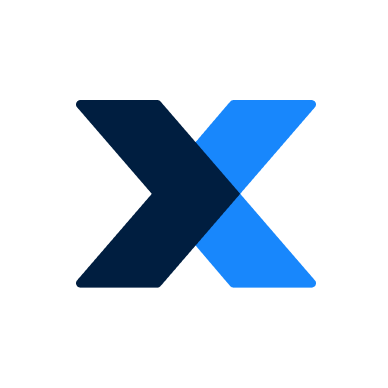
The MaintainX team is made up of maintenance and manufacturing experts. They’re here to share industry knowledge, explain product features, and help workers get more done with MaintainX!