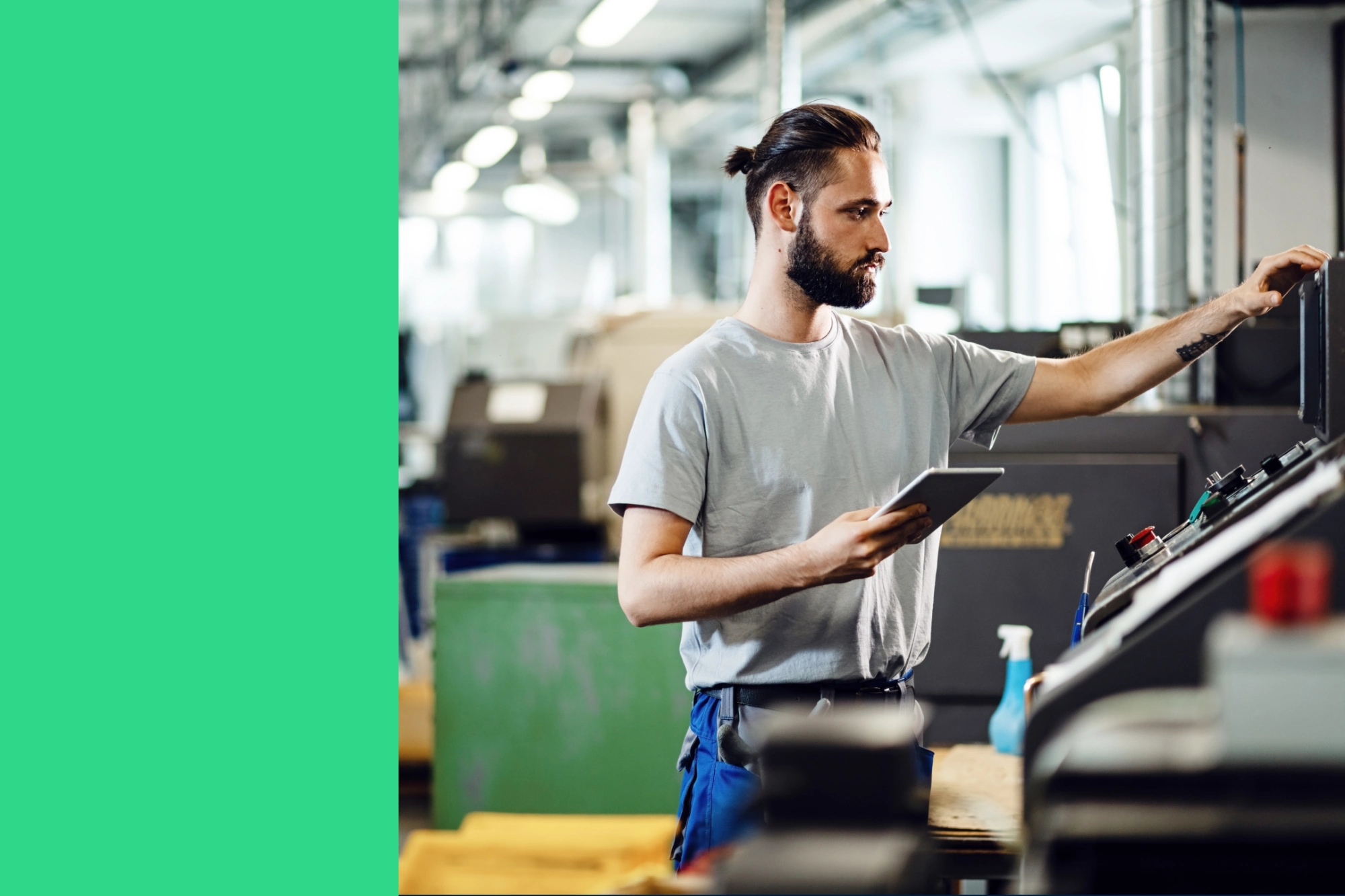
Choosing the right maintenance strategy is critical—not just for cost savings, but also for safety and environmental protection. Take the explosion of the Deepwater Horizon in 2010. The disaster cost the lives of 11 workers and released 210 million gallons of oil into the Gulf of America (neé Mexico).
The cause? There were a number of decisions and failings on the rig and within the company that contributed to this disaster. However, one of the core reasons so much oil was released was poor maintenance.
In other words, a comprehensive maintenance strategy that combined preventive, corrective, and condition-based maintenance approaches could have prevented this catastrophe.
After a thorough investigation of the Deepwater Horizon catastrophe, it was found that the low cost of preventative maintenance in battery and valve seal replacements could have saved billions of dollars in cleanup costs. But it isn’t just preventive maintenance that matters—all maintenance matters, whether you are doing it before stoppages or after. Which types of maintenance you choose will depend on your industry, your equipment, and the consequences of failure. A broken lightbulb in an office kitchen might be fine to replace after it burns out. A failed safety system on an oil rig? That's another story entirely.
In this guide, we'll explore the different types of maintenance strategies, when to use them, and how to implement them effectively. Understanding these different types of maintenance is crucial for any facility manager or operations leader.
Key Takeaways
- As the Deepwater Horizon disaster showed us, poor maintenance of critical systems can lead to catastrophic failures with devastating consequences.
- Preventative maintenance extends equipment lifespan by 20-40% and reduces unplanned downtime by 35-45%.
- The right maintenance mix depends on your specific situation—aim for roughly 80% preventative and 20% reactive maintenance, adjusting based on your industry and equipment criticality.
- Success requires both strategy and execution—even the best maintenance plan needs proper implementation, including operator engagement, clear documentation, and continuous improvement.
- Not everything needs preventative maintenance—for non-critical, easily replaceable equipment, reactive maintenance can be more cost-effective.
Understanding different types of maintenance
We can bucket maintenance types into two fundamental approaches: preventive maintenance and reactive maintenance.
- Preventative maintenance—performing regular upkeep to prevent failures
- Reactive maintenance—fixing equipment only after failure.
Within these categories, you'll find specific approaches, like corrective maintenance for addressing identified issues, and unplanned corrective maintenance for unexpected failures.
Here's how these approaches compare:
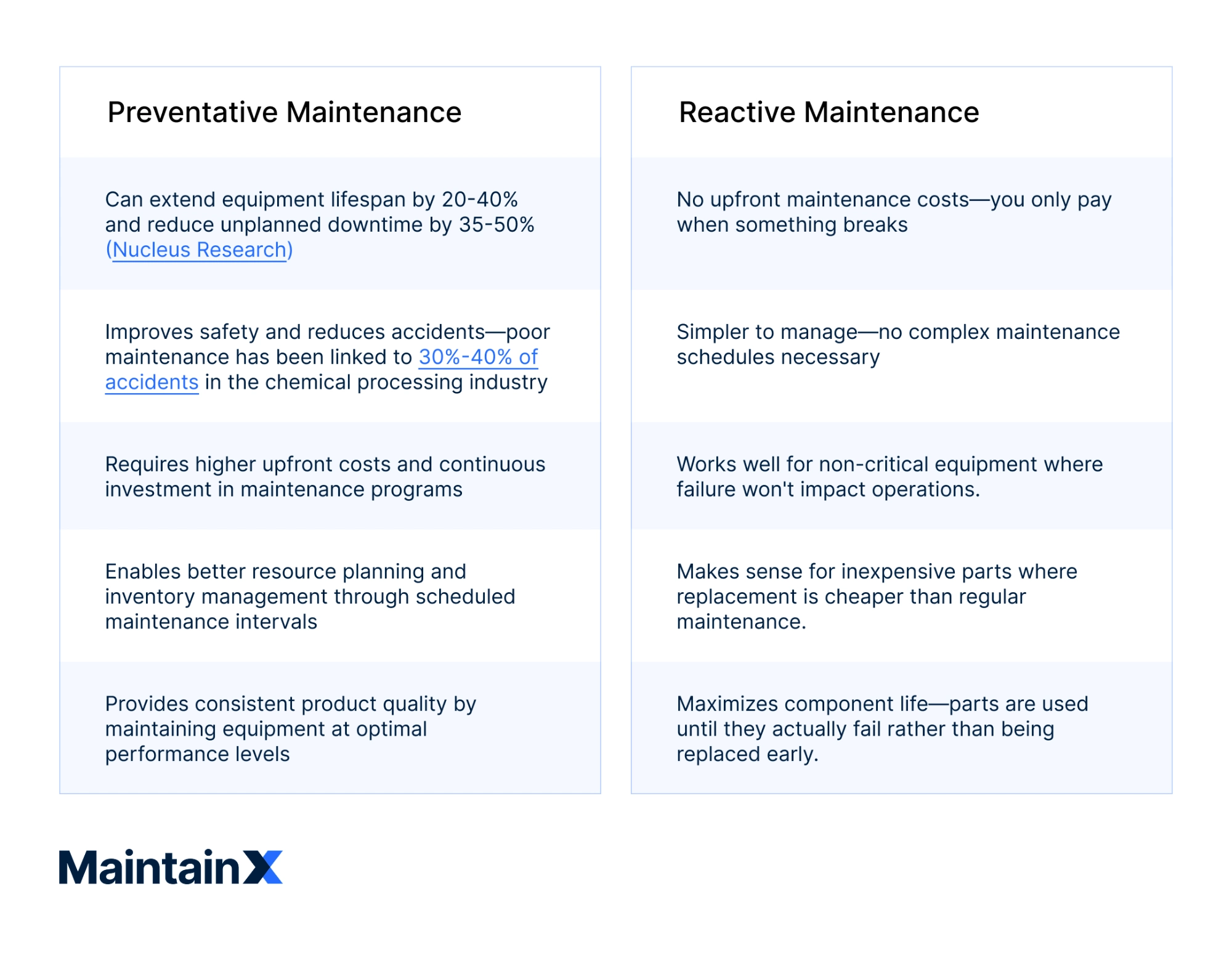
Let’s go through both strategies in detail.
Preventative maintenance strategies
While there are many types of maintenance approaches, preventative strategies can be broken down into three main categories.
1. Time-based maintenance
The simplest form of preventative maintenance is time-based: performing maintenance at set intervals, regardless of the equipment's condition. It's like changing your car's oil every 5,000 miles or getting an annual physical—you do it on schedule, whether you think you need it or not.
This approach works well for equipment that:
- Wears out at predictable intervals
- Has clear manufacturer guidelines for maintenance timing
- Is critical enough that you can't risk waiting for signs of wear
- Needs regular servicing for safety or compliance reasons
For example, in food and beverage manufacturing, production lines must undergo rigorous cleaning and maintenance at set intervals to meet food safety standards. You don't wait for contamination to show up in quality tests—you maintain sterile conditions on a strict schedule. Similarly, automotive manufacturers replace pressing dies and tooling on fixed intervals, knowing that after a certain number of uses, wear becomes inevitable.
2. Corrective maintenance
Next is corrective maintenance, sometimes called condition-based maintenance: monitoring specific indicators of equipment health and performing maintenance when those indicators show deterioration. Instead of changing oil every 5,000 miles, imagine checking its quality regularly and changing it only when it's actually degraded.
This approach involves:
- Regular equipment inspections
- Monitoring specific parameters (vibration, temperature, pressure, etc.)
- Setting threshold values that trigger maintenance
- Responding when those thresholds are crossed
For instance, chemical manufacturing plants monitor the pressure and temperature in their reaction vessels. When these parameters drift from optimal ranges, it signals that seals or heating elements need maintenance. In plastics manufacturing, when melt temperature and pressure in injection molding machines deviate from the norm, screws or barrel components may need maintenance before quality issues occur.
3. Predictive maintenance
The most advanced form of preventative maintenance uses technology to predict failures before they happen. Using sensors, data analysis, and often artificial intelligence, predictive maintenance tries to answer the question: "When is this equipment likely to fail?"
According to the U.S. Department of Energy, predictive maintenance can produce 8-12% cost savings over traditional preventive programs. It's like having a doctor who can predict when you're likely to get sick based on subtle changes in your vital signs.
Modern predictive maintenance typically involves:
- Continuous monitoring through sensors
- Real-time data collection and analysis
- Advanced analytics or AI to spot patterns
- Early warning of developing problems
- Maintenance scheduled just in time—not too early, not too late
For example, building materials manufacturers use predictive maintenance on their kilns and grinding mills. Sensors monitor power consumption, vibration patterns, and acoustic signatures—subtle changes can indicate wearing components long before failure occurs. In automotive assembly plants, robots are fitted with sensors that track servo motor current draw and movement precision. The data helps predict when a robot's joints or motors will need servicing, allowing maintenance to be scheduled during planned production breaks rather than causing unexpected line stoppages.
Reactive maintenance approaches
Just as preventative maintenance has different levels of sophistication, reactive maintenance isn't just about waiting for things to break. A reactive maintenance strategy might seem counterintuitive when discussing maintenance costs, but it has its place in a comprehensive maintenance plan. While emergency maintenance and unplanned repairs often cost more, there are situations where reactive maintenance makes financial sense.
There are two distinct approaches, each with its own place in a maintenance strategy.
1. Run-to-failure maintenance
Run-to-failure is a deliberate strategy—despite its name, it's not the same as neglecting maintenance. Think of it like using disposable cups at a party instead of washing dishes. You're making a conscious choice that replacement is more efficient than maintenance.
This approach makes sense for equipment that:
- Is inexpensive to replace
- Has minimal impact on operations when it fails
- Has failure patterns that are difficult to predict
- Would cost more to maintain than to replace
For example, in general manufacturing, simple conveyor rollers are often run to failure. When they stop spinning smoothly, they're replaced rather than repaired—the cost of regular maintenance would exceed the price of a new roller. In food and beverage plants, certain processing tools, like cutting blades, are deliberately run until they dull because the wear pattern is so consistent that preventative replacement wouldn't save money.
2. Emergency maintenance
Sometimes, despite our best intentions and maintenance strategies, equipment fails unexpectedly. Emergency maintenance is your backup plan.
This type of maintenance involves:
- Rapid response protocols
- Emergency spare parts inventory
- On-call maintenance staff
- Clear priorities for critical repairs
- Documented emergency procedures
For instance, in chemical manufacturing, a leak in a critical pump might require immediate attention to prevent environmental hazards. Plastics manufacturers often keep spare heating elements on hand because if one fails, production can't continue until it's replaced. The automotive industry maintains emergency response teams that can quickly address robot failures on assembly lines where every minute of downtime costs thousands of dollars.
The key is to minimize the need for emergency maintenance through good preventative practices while maintaining the capability to respond quickly when unexpected failures do occur. Even the best-maintained facilities will occasionally need emergency repairs—the goal is to make them rare exceptions rather than the daily routine.
Choosing the right maintenance strategy
Selecting the right maintenance strategy requires balancing multiple factors. Your maintenance team needs to consider equipment failure risks, maintenance costs, and potential cost savings from different approaches. Organizations often need to implement multiple types of maintenance to create an optimal program.
Most successful facilities aim for an 80/20 split: about 80% preventative maintenance and 20% reactive. This balance helps control costs while managing risks. However, your specific mix should depend on your industry and situation. A chemical plant might aim for 90% preventative due to safety concerns, while a general manufacturer might run closer to 70/30.
To figure out what your ratio should be, first, assess your equipment's criticality by asking (and answering) these questions:
- How much does a failure impact production?
- What are the safety implications?
- How expensive is the equipment to replace?
- What's the cost of downtime?
For example, in automotive manufacturing, a main assembly line robot needs preventative maintenance because downtime costs can reach $600 per second. But the hand tools used by quality inspectors might be fine with a reactive approach—if a screwdriver breaks, you simply grab another one.
Consider these factors when choosing your strategy:
Critical safety equipment
Always use preventative maintenance for anything safety-related. The Deepwater Horizon disaster shows us what can happen when safety systems aren't properly maintained. In chemical manufacturing, this means regular maintenance of emergency shutdown systems, pressure relief valves, and gas detection equipment. Never run these to failure.
High-value production equipment
For expensive machinery that directly impacts production, preventative maintenance usually makes the most sense. It reduces overall maintenance costs, prevents the massive costs of emergency repairs, and extends equipment life.
Building materials manufacturers, for instance, typically use preventative maintenance on their kilns and grinding mills because these are expensive to replace and critical to production.
Non-critical support equipment
This is where reactive maintenance often makes sense. Consider using run-to-failure for equipment that:
- Is inexpensive to replace
- Has redundant backup systems
- Doesn't directly impact production
- Has unpredictable failure patterns
In food and beverage manufacturing, this might include backup pumps, standard light fixtures, or basic hand tools.
Consider your resources
Your maintenance strategy also depends on your available resources:
- Do you have the budget for preventative maintenance?
- Do you have skilled maintenance staff?
- Can you invest in monitoring equipment?
- Do you have the systems to track and schedule maintenance?
For smaller operations, a mix of strategies often works best. Focus preventative maintenance on your most critical equipment while accepting reactive maintenance for less crucial items. As your resources grow, you can gradually expand your preventative maintenance program.
Remember: maintenance strategy isn't just about preventing failures–it's about optimizing your overall operations. The goal is to find the sweet spot where your maintenance efforts provide the best return on investment while managing your risks effectively.
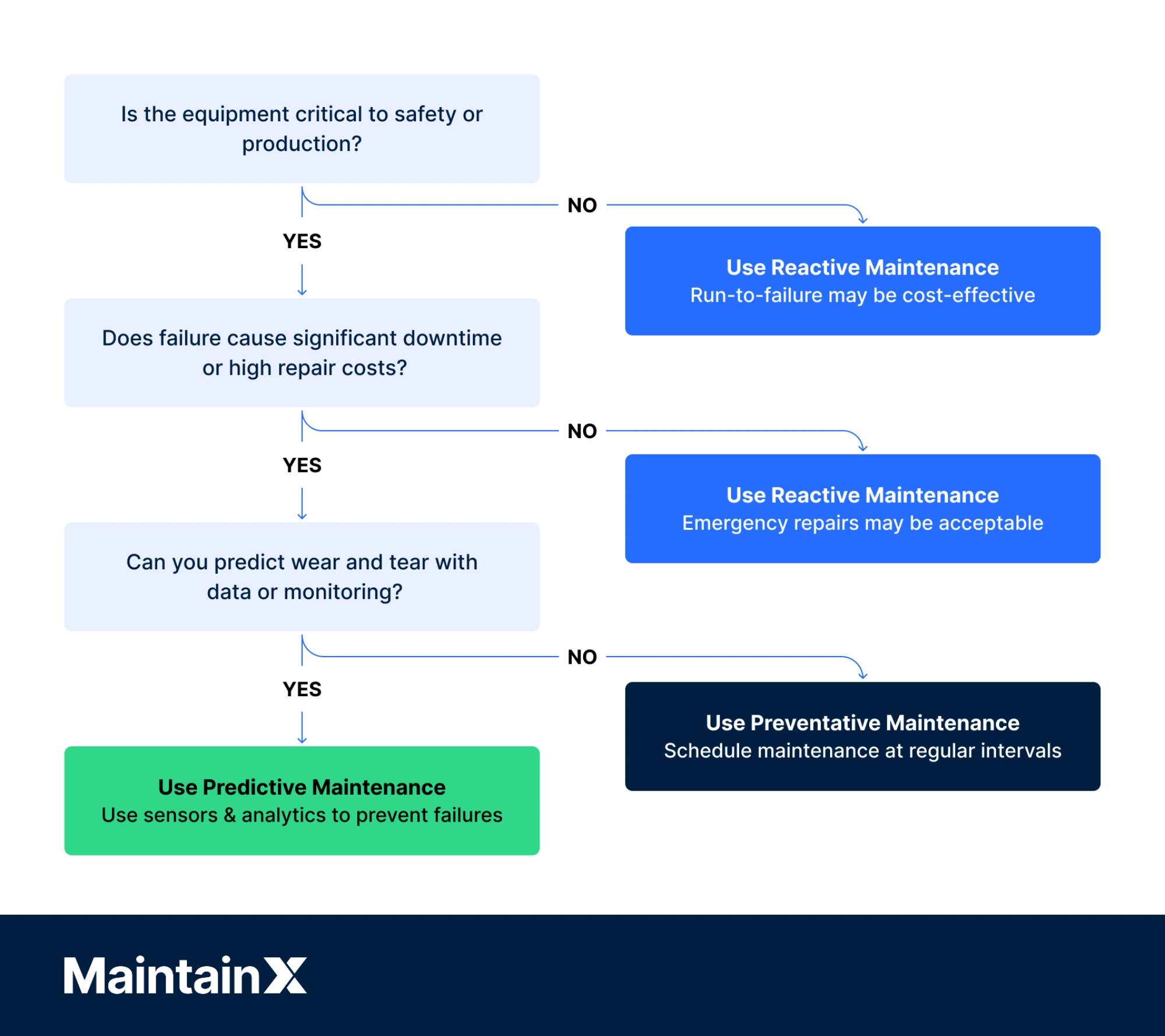
Implementing effective maintenance programs
Successfully implementing different types of maintenance requires careful planning and systematic execution. Whether you're starting from scratch or improving an existing program, successful implementation follows some key principles. Let's look at how to put your maintenance strategy into practice.
Understand the fundamentals
Before diving into advanced predictive systems or complex maintenance schedules, ensure you have your fundamentals in place:
- Inventory all your equipment and assess its criticality
- Document current maintenance procedures and histories
- Train your maintenance team on proper procedures
- Establish clear communication channels for maintenance requests
- Set up a system to track maintenance activities and costs
Don't try to transform everything overnight. The most successful implementations start small and expand gradually. Begin with your most critical equipment and establish basic preventative maintenance routines for them. Collect data, measure results, then adjust and improve based on outcomes.
Gradually expand to more equipment over time. A plastics manufacturer, for instance, might start by implementing preventative maintenance on their main injection molding machines before expanding to auxiliary equipment.
Best practices
Successful maintenance programs share several key characteristics. Here are the best practices that set them apart:
1. Engage your operators
The people running the equipment on a daily basis are your first line of defense:
- Train operators to perform basic maintenance tasks
- Establish clear procedures for reporting problems
- Create ownership by assigning specific equipment to specific operators
- Encourage operators to learn their equipment's normal operating conditions
Successful maintenance activities require close coordination between operators and the maintenance team. Operators should be trained to recognize normal operating conditions and report deviations that might indicate potential issues. This helps with planned maintenance scheduling and reduces emergency repairs.
In automotive manufacturing, operators might be trained to conduct daily checks on their robotics systems, looking for unusual sounds or movements that could indicate developing problems.
2. Use data to drive decisions
Modern maintenance isn't about gut feelings. You need to track repair histories and costs, and monitor equipment performance metrics. Then, you can analyze failure patterns and use this data to optimize maintenance intervals.
Chemical manufacturers, for example, might track the mean time between failures for pump seals to determine optimal replacement schedules.
3. Maintain clear documentation
Good documentation is crucial for consistent maintenance:
- Create detailed maintenance procedures
- Keep accurate equipment histories
- Document modifications and repairs
- Make documentation easily accessible to maintenance staff
Building materials manufacturers might maintain digital records of all maintenance activities on their kilns, including repairs, adjustments, and regular maintenance tasks.
4. Plan for emergencies
Even with the best preventative program, emergencies can happen. Keep critical spare parts in stock, maintain emergency response procedures, and have backup systems and clear escalation protocols. A chemical plant might maintain redundant pumps for critical processes and keep emergency repair kits readily available.
5. Review and improve
Your maintenance program should never be static:
- Regularly review maintenance metrics
- Seek feedback from operators and maintenance staff
- Stay current with new maintenance technologies
- Adjust procedures based on equipment performance
Remember: implementing an effective maintenance program is a journey, not a destination. It requires ongoing commitment, regular adjustments, and continuous improvement. The goal is to create a program that's both effective and sustainable for your specific operation.
Improve your maintenance management system
Your maintenance journey doesn't end with implementation—continuous improvement is key to long-term success. Start by establishing clear metrics for your maintenance program, from tracking the percentage of planned vs. unplanned maintenance to monitoring equipment uptime and reliability rates. These metrics will help you identify areas for improvement and measure progress over time.
Modern maintenance management benefits from digital tools. Consider implementing a Computerized Maintenance Management System (CMMS) to track and schedule maintenance, and explore sensors and analytics for more advanced monitoring. For example, a chemical manufacturer might start with basic digital work orders, then gradually add sensors and predictive analytics to their critical equipment.
Finally, build a culture where maintenance is a company-wide priority, not just a department responsibility. Make maintenance wins visible, encourage collaboration between operations and maintenance teams, and invest in ongoing training.
Remember, improvement is an ongoing process. Whether you're implementing your first preventative maintenance program or advancing to predictive maintenance, there's always room to grow. By continuously improving your maintenance management system, you're not just protecting your equipment–you're protecting your people, your productivity, and your bottom line.
Types of Maintenance FAQs
What are the types of maintenance?
Maintenance strategies fall into two main categories: preventative and reactive. Preventative maintenance includes time-based maintenance (regular scheduled upkeep), condition-based maintenance (addressing issues when monitoring shows problems developing), and predictive maintenance (using technology to forecast when failures might occur). Reactive maintenance includes run-to-failure (planned replacement after breakdown) and emergency maintenance (responding to unexpected failures).
What type of maintenance is most effective?
There's no one-size-fits-all answer. For critical safety equipment and expensive machinery, preventative maintenance is usually most effective–extending equipment lifespan by 20-40% and reducing unplanned downtime by 35-45%. However, for non-critical, inexpensive equipment, reactive maintenance might be more cost-effective. Most successful facilities aim for an 80/20 mix of preventative to reactive maintenance, adjusting based on their specific needs and industry.
What are the three types of repairs?
Repairs generally fall into three categories: preventative repairs (scheduled maintenance to prevent failures), corrective repairs (fixing issues identified during inspections or monitoring), and emergency repairs (addressing unexpected breakdowns). The goal of a good maintenance program is to maximize preventative repairs while minimizing emergency repairs.
What are common preventive maintenance tasks?
Preventive maintenance tasks include regular inspections, lubrication, cleaning, calibration, and component replacement. These tasks, when properly scheduled and executed, help maintain normal operating conditions and prevent unexpected equipment failure.
How does a proactive maintenance strategy differ from reactive maintenance?
A proactive maintenance strategy focuses on preventing failures before they occur through regular monitoring and maintenance activities. Unlike reactive maintenance, which responds to problems after they develop, proactive maintenance combines preventive maintenance tasks with condition-based monitoring to optimize equipment performance and reduce maintenance costs.
How do I choose between different types of maintenance?
The choice between types of maintenance depends on factors like equipment criticality, cost, safety requirements, and available resources. Critical safety equipment typically requires preventive maintenance, while less crucial equipment might use reactive approaches.
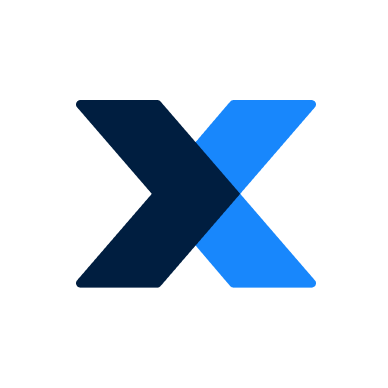
The MaintainX team is made up of maintenance and manufacturing experts. They’re here to share industry knowledge, explain product features, and help workers get more done with MaintainX!