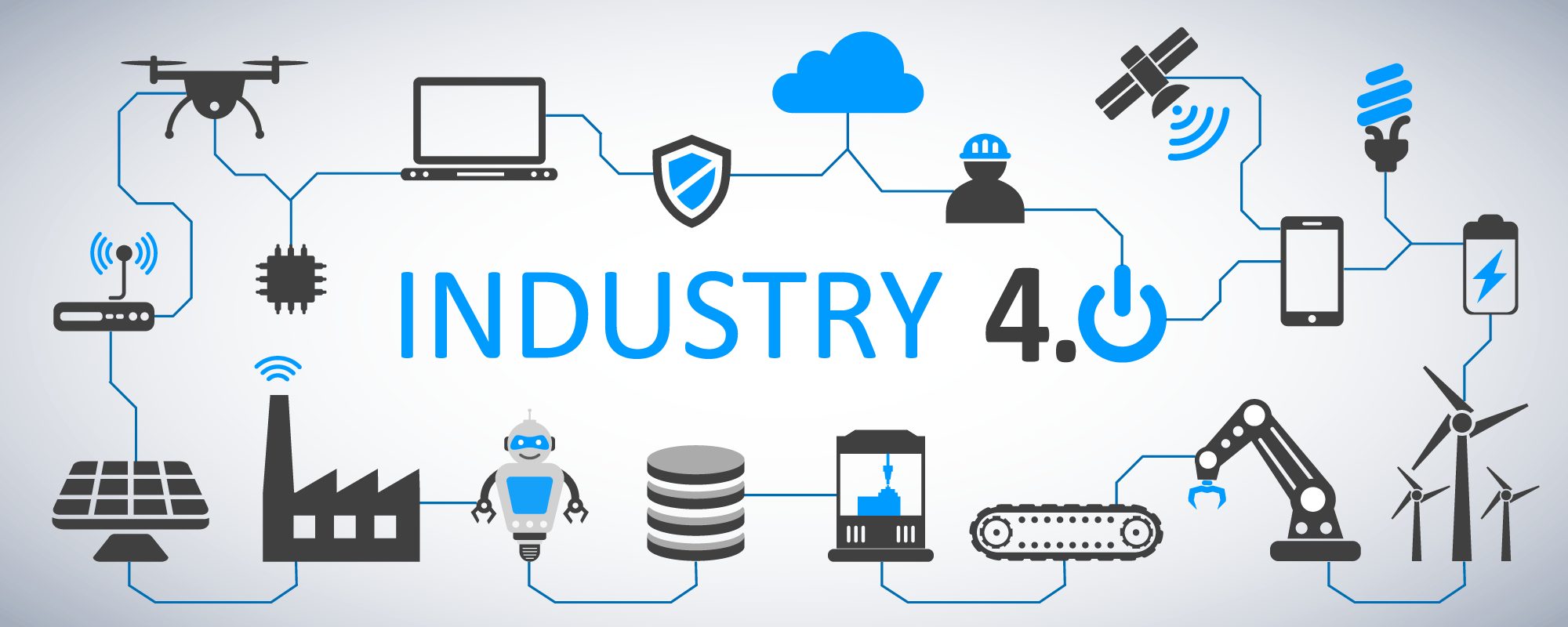
The concept of work instructions is not a modern-day invention. The way we communicate work instructions, however, has continued to evolve as Industry 4.0 scales up modern-day operations exponentially.
The concept of Industry 4.0 is heavily characterized by process-driven technologies, such as automation and connected worker platforms. A well-thought-out process is a series of steps that you’re able to follow to a task’s completion. In order for an organization to develop a predictable and efficient operation, these instructions should be comprehensively crafted to leave limited room for judgment or creativity from the operators.
Following a process can and should mean that work is done more efficiently. Whether your organization is drafting its first set of work instructions or re-evaluating long-standing procedures, it is important to always view them as a work in progress. Companies that successfully measure, iterate, and improve these instructions as part of their internal culture tend to be the ones that last over time.
Procedures and Work Instructions
The term procedure is most often used at the management level to express an idea about how things should be done at a high level. Standardized work instructions are mandatory processes in which little to no room for judgment or personal interpretation is allowed.
Key takeaways:
- Industry 4.0 processes save time.
- Standardized work instructions lead to greater efficiency and productivity.
- Procedures and work instructions should be viewed as equally important.
Industry 4.0 processes save time.
For most companies, maintaining product quality standards, adherence to government compliance policies (OSHA, etc), and accountability tracking usually means relying on clipboards, checklists, and filing cabinets stuffed to the brim with paper which is hard to do within a reasonable time frame.
It’s no surprise that Industry 4.0 is beginning to look for a digital solution that transforms inputs. It also results in increased efficiency, accountability, and productivity. MaintainX is the solution.
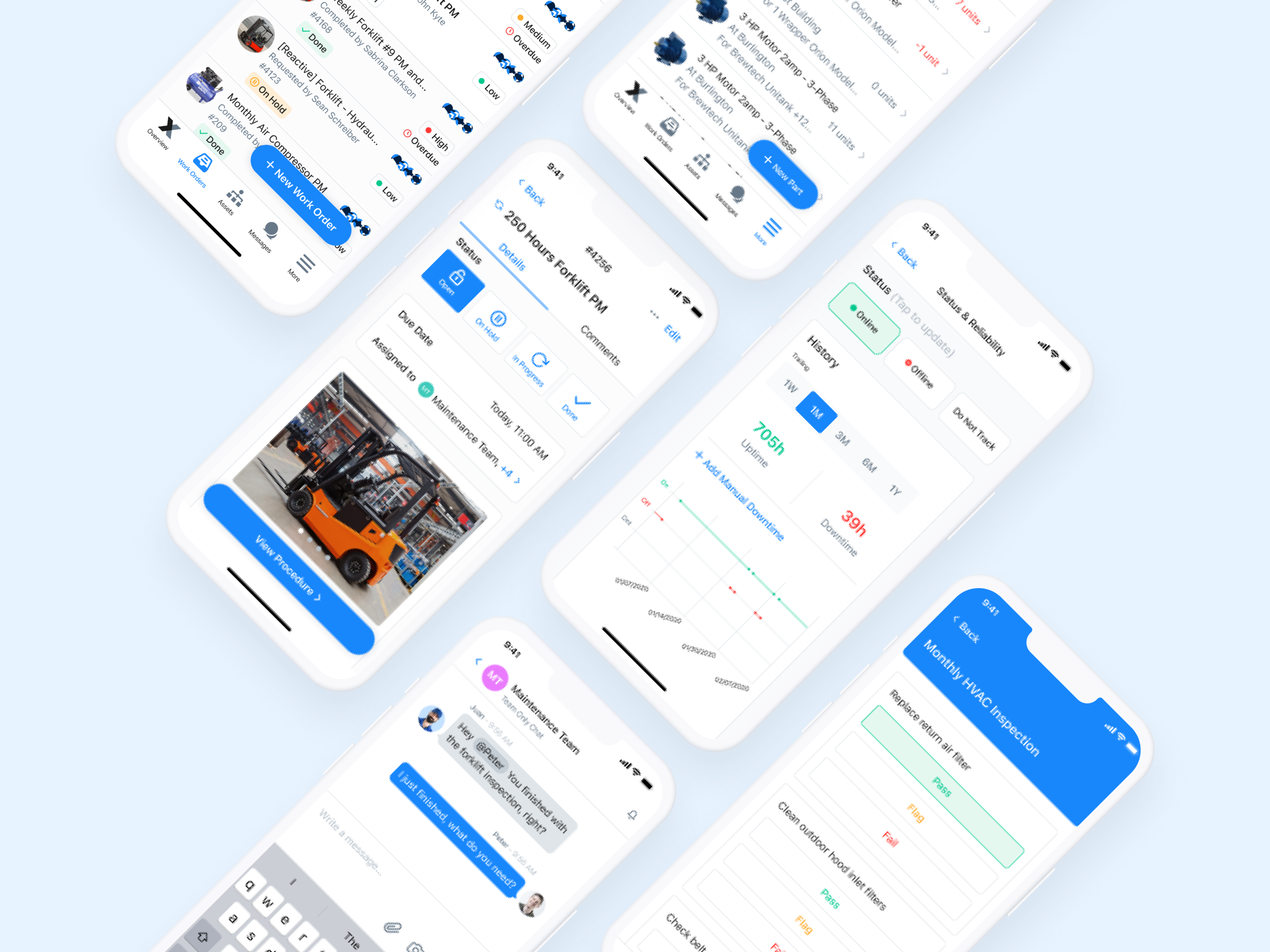
The Industry 4.0 Digital Transformation
The world around us has been transformed by technology more so in the past 50 years than in the past 500. For companies to stay relevant, it is critical to develop or implement solutions to optimize production and efficiency, not just maintain it, and reduce human error.
The first step an organization can take towards optimization is to digitize its processes, including:
- Maintenance
- Production
- Accountability
Digitizing processes for an organization allows for a central repository of information, such as Standardized Work Instructions. You can certainly do additional analysis of collected data to implement new techniques to ultimately achieve:
- Greater productivity
- Reduced costs
- Continuous quality improvement
- Optimum efficiency
“Companies that can deploy Industry 4.0 at scale are transforming their organizations to not only address the toughest disruptions of today but also prepare themselves for the new disruptions of tomorrow.”
McKinsey
Most likely, your company has invested in at least a few digital solutions. Perhaps your technological investments are beginning to feel disjointed, and maybe that’s why you’re reading this blog post right now.
In today’s hyper-competitive marketplace, a company can get a leg up on the competition by using things like connected sensors, increased storage capacities, long-range networks, and even a CMMS. However, despite access to these tools, many organizations are left feeling more disconnected from their front-line teams than before. Investing in a connected worker platform like MaintainX will help your company elevate your team alongside your other solutions to unlock previously unattainable and unscalable results.
The Birth of Digital Work Instructions
At one point, we all considered it revolutionary to be able to scan instructions and attach them as a PDF to an email. However, 80% of the world’s global workforce doesn’t sit behind a desk. It doesn’t make sense to focus on a desktop-first solution PDFs are also difficult to edit and collaborate on, even from a desktop. MaintainX is collaborative, mobile-first, and easy to use.
Today, with the implementation of Industry 4.0 work instructions, workers have the advantage of app-based platforms and programs to create step-by-step instructions for specific tasks. The line between consumer and industry applications has blurred and given rise to a new generation of solutions called Connected Worker Platforms.
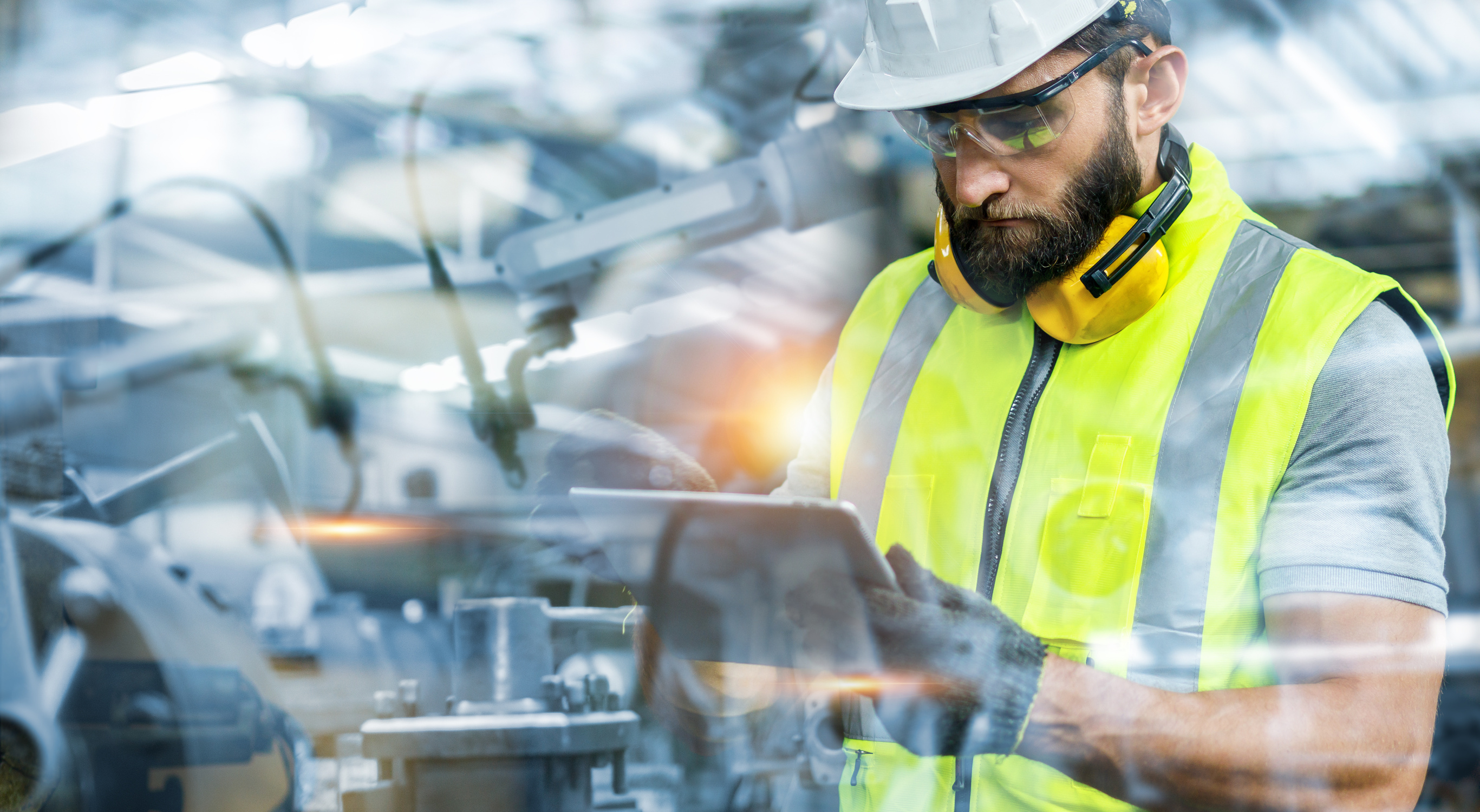
Connected Worker Platforms have key features, such as the ability to:
- Collect and analyze data
- Measure output across locations & teams
- Trigger and time stamp work
- Test and iterate procedures across your organization
- Communicate and collaborate in real time
- Validate jobs and headcount
What Does This Mean for Your Company
In the era of digital standardized work instructions, a company can operate with the assurance that all processes are available, consistent, and repeatable when using a digital solution such as MaintainX.
When work instructions contain the optimal steps needed to perform a process, we see improvements in a variety of areas, including:
- Consistency of your product
- Quality of your product
- Safety of your operators
- Throughput of your process
The coupling of Digital Transformation and Industry 4.0 is improving the workplace, whether on the factory floor or out in the field. With the complexity of production today, organizations are turning to new digital solutions to keep pace with today’s swift-moving, and changing environments to meet the demands of customers.
Why Should Your Company Care?
The cost is your company getting left behind and becoming one of those dreaded “dinosaurs”. By investing in reducing production costs, companies are more likely to pass those savings on to their customers.
Why? Organizations that have moved beyond Industry 3.0 are more efficient. Reducing production costs means they are in a better position to pass on savings to their customers. To meet the demands of their customers.
Key Takeaways:
- Connected Worker Platforms are the future for assigning, managing, and tracking work for deskless workers.
- Digital work instructions have evolved from simply scanning forms in a PDF format to having them readily available to workers on a mobile app.
- Using Standardized Work Instructions means organizations can ensure all processes are timely, consistent, and repeatable.
Let’s consider some of the advantages of moving to digital Standardized Work Instructions.
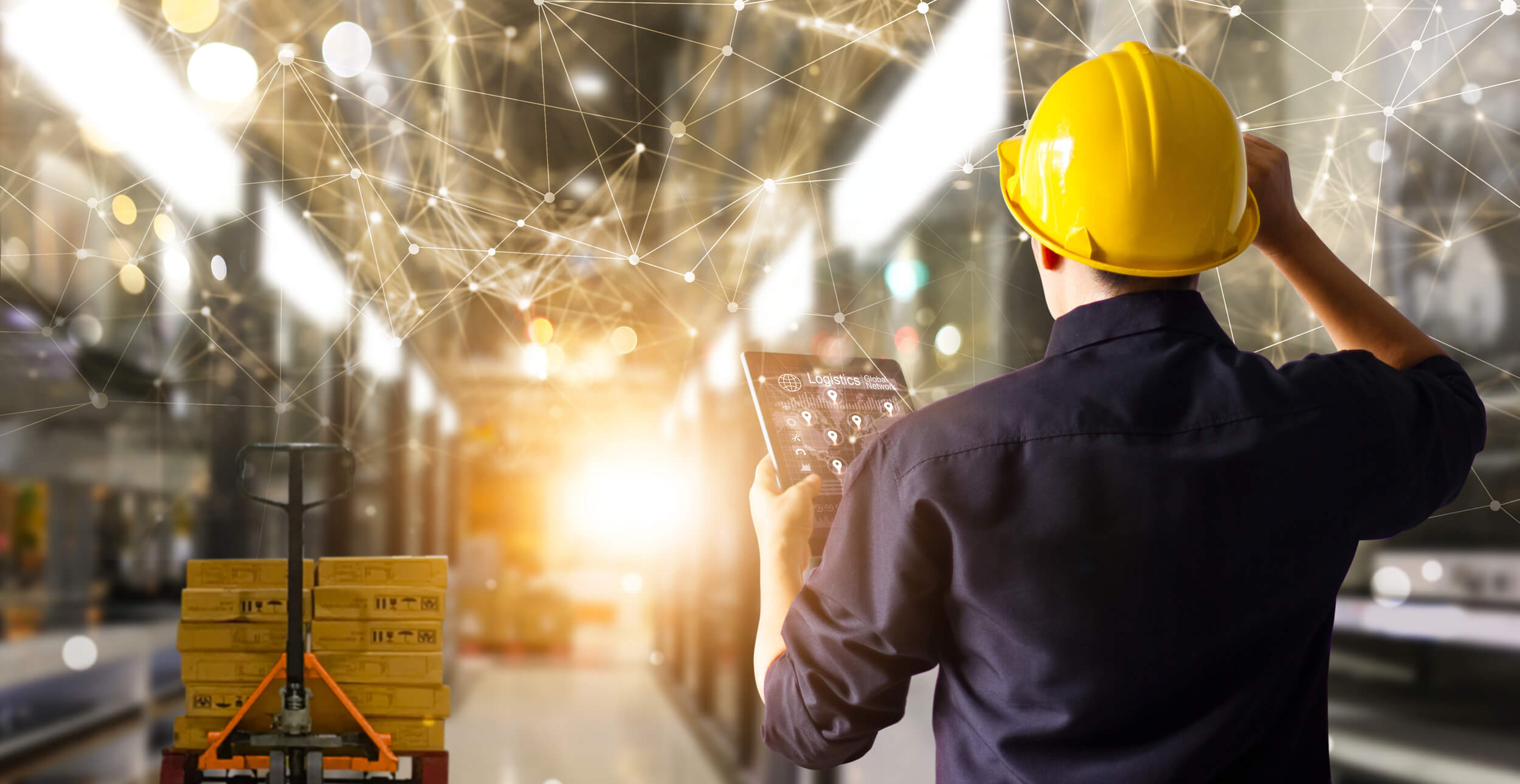
Benefits of Digital Standardized Work Instructions
Moving your company’s processes and Standardized Work Instructions to one digital platform can lead to a variety of benefits.
Centralization
To be competitive in today’s world, we can create and maintain all work instructions with Workflow Management software, such as MaintainX. You can centralize all your instructions and PDFS in one place, in one app, available virtually anywhere you bring your phone. Additionally, you can iterate, improve, and put into action these instructions across your organization instantly – an undertaking that would have previously required months to prepare.
This can and will save you and your workers time digging through hard drives, old files, and filing bins, which ultimately saves you money. Centralizing Standardized Work Instructions and procedures also ensures that your workers are in receipt of instructions.
And another benefit? It makes collaboration much easier.
Process Control
How does your company ensure compliance with workflows and instructions? Without a standardized approach, so that workers can follow every step of a process, this is challenging. This is especially true if your company still relies on clipboards and paper checklists to keep the lights on.
Welcome to Industry 4.0. In this new wave of technology, you can upload Standardized Work Instructions. You can make them available on a digital platform to all of your employees. You can create a series of checklists for procedures to enforce compliance by all your workers. This will leave behind an audit trail of those employees who didn’t complete all the required tasks. This will make your company’s overall ISO compliance easier.
Structured and Linked Workflows
Chances are your work instructions don’t exist in a vacuum but are part of larger or connected procedures and workflows.
Having your work instructions in a linked environment means your workers can launch other necessary workflows should the need arise.
Messaging
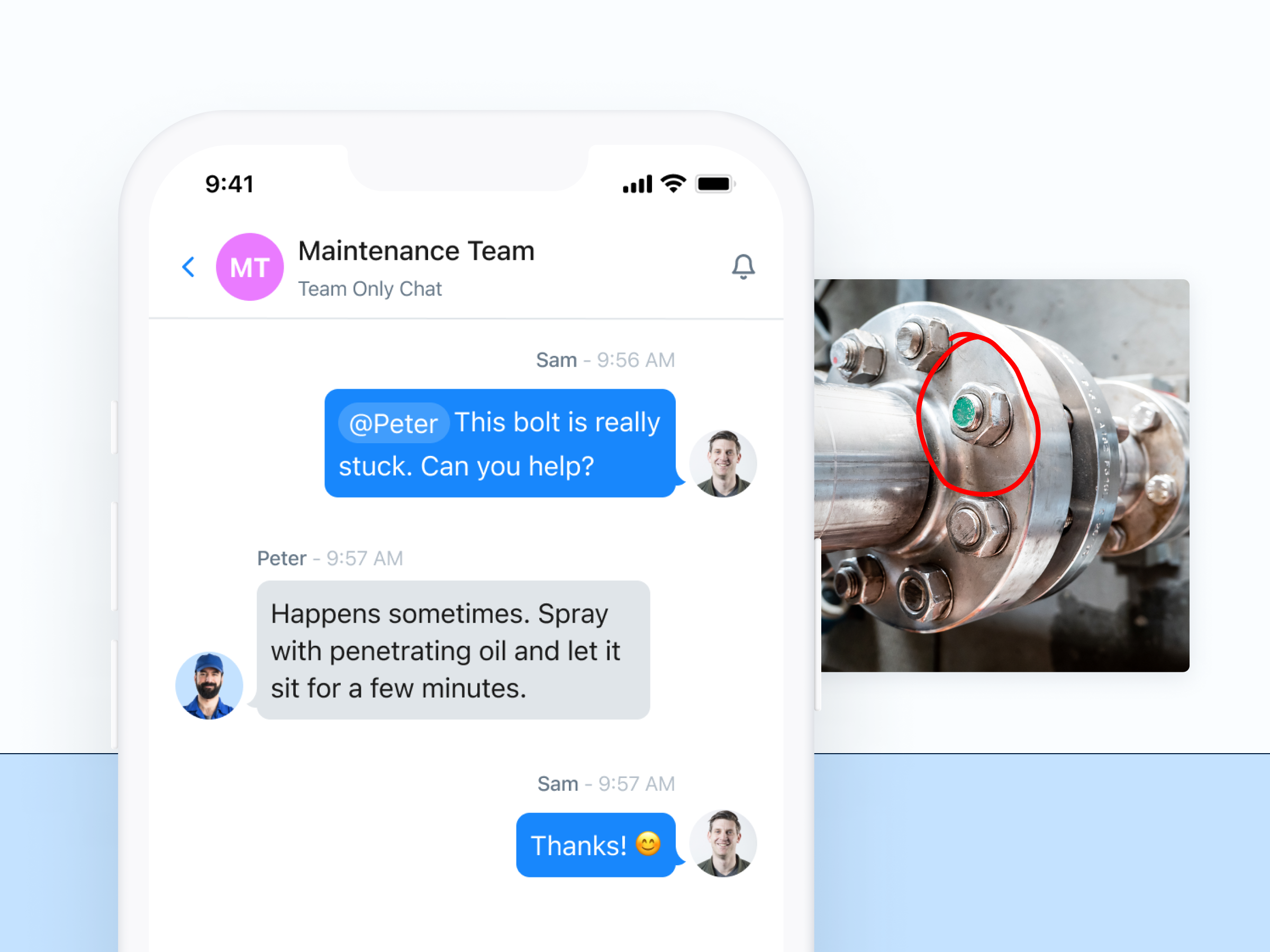
Messaging within your company’s digital platform is extremely important. Instead of requiring your employees to manually input all of their coworkers’ phone numbers, having a messaging system built-in to their Connected Worker Platform keeps the conversation in one place and allows for an audit trail.
Invest in the New Standard: Industry 4.0 Digital Work Instructions
By now, you should have no doubt that your company should move all workflows, standardized Work Instructions, procedures, and employee messaging onto a digital platform to stay competitive in today’s world.
Investing in software to cut down on the time-consuming ways of the past will allow your workers to spend more time being productive instead of trying to track down old paper checklists stuffed in filing cabinets.
FAQs
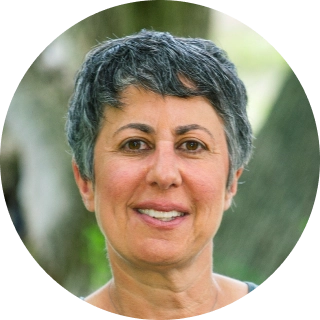
Caroline Eisner is a writer and editor with experience across the profit and nonprofit sectors, government, education, and financial organizations. She has held leadership positions in K16 institutions and has led large-scale digital projects, interactive websites, and a business writing consultancy.