.jpeg)
Being a manufacturing director means leading all kinds of strategic initiatives, and that was definitely the case during the 5+ years of my career as one. However, one initiative in particular still stands out: I was tasked with "implementing a digital transformation” that would improve performance and increase capacity.
After a lot of research, I decided that the best “digital transformation” to address those needs would be to install Industrial Internet of Things (IIoT) sensors to gather data.
The promise of these technologies was exciting—IIoT sensors and connected devices offer incredible potential to improve asset reliability, streamline processes, and increase production capacity.
However, ensuring the project's success was daunting. KPMG reports that most “US businesses say they have not seen an increase in performance or profitability from digital transformation investments.”
Why is that? Simply put, digital transformation isn’t just about adopting a new technology. It is also about understanding how that technology aligns with the business's broader goals.
In this article, I’ll talk about how to beat the odds and successfully implement an IIOT digital transformation initiative. First, we’ll discuss the biggest risk factors, and then I’ll lay out a roadmap you can use to guide your project.
Digital transformation with IIoT devices: Risk factors
For IIoT systems to deliver value, leaders must integrate them thoughtfully into existing workflows and keep the end-user—whether a production manager or maintenance technician—at the center of the deployment strategy. When that happens, digital transformation projects can enhance operational efficiency and asset performance, ensuring long-term success and measurable ROI.
However, research shows that over 70% of all digital transformation initiatives fail to achieve their goals. While these numbers are troubling, their reasons aren’t a mystery.
Let’s take a look at the biggest mistakes people make:
1. Lack of a clear plan
One of the most common reasons IIoT and digital transformation projects fail is that leaders don’t have a coherent plan. While execution is key, a proper project charter at the outset ensures that everyone is aligned on goals, responsibilities, and strategies. Without one, teams—especially those on the frontlines, like maintenance technicians—lack the direction they need to execute the strategy.
2. Failure to align IIoT with end-user workflows
IIoT devices can significantly improve operations only if they align with the teams' current workflows. Maintenance technicians, for instance, are often used to manual inspections and may resist adopting IIoT-driven processes. If the IIoT system is complex, difficult to understand, or disrupts their existing workflows, the chances of failure increase.
3. Unrealistic ROI expectations for IIoT projects
Many companies adopt IIoT technology and expect immediate results. While these devices can lead to improved efficiency, cost savings, and enhanced machine performance, it can take time to see that impact. Unrealistic ROI expectations can lead to disappointment when teams don’t immediately see anticipated improvements.
Make IIoT work for you: Key steps for successful digital transformation
So, how do you avoid those risk factors? Below is a roadmap you can follow to help ensure success:
1. Create a project charter
Your successful IIoT implementation should begin with a well-defined project charter that outlines key information, including:
- The current state of your operations
- A problem statement
- Your desired outcomes
- System architecture
- Timelines
- Responsibilities
- Investment/ROI
Be sure to answer key questions at this stage, like how you will integrate new data into existing workflows and how the IIoT devices will affect current tasks. Addressing these questions upfront helps ensure all teams are aligned on objectives and streamlines the transition process.
2. Be deliberate about change management
Keep communication going throughout the process. You want to ensure that your team understands not only what they have to do, but why.
Beyond knowing the technology, they need to understand its impact and potential. While you may need to provide technical training, you should also offer support on adjusting to the new workflows.
Being transparent with explanations, offering continued guidance, and reinforcing the technology’s benefits will empower your team to fully embrace the new tools. Inspire and facilitate the change with open and frequent communication via daily stand-ups and bi-weekly metric measurement meetings.
3. Prioritize critical assets
It might be tempting to deploy IIoT sensors across all equipment at once. However, that approach can confuse your operations, offering your team little room to adjust.
A more gradual transition allows your team to get used to the new technology. Start by focusing on your pareto analysis (including kanban voting) of the most critical assets. Collaborate with frontline workers to identify how they currently collect and monitor data so you can decide what to prioritize. This targeted approach creates a smoother, more controlled transition.
4. Establish one-point lessons (OPLs)
OPLs are simplified, step-by-step visual guides that help frontline workers complete simple or small tasks. If you’re using a Computerized Maintenance Management System (CMMS), you can incorporate these digitized instructions into the tool and so your team can access them on mobile devices.
Taking advantage of such systems is crucial when introducing new workflows. By using this process, you can break down complex procedures into simple steps for your team and reduce the likelihood of errors. This boosts overall productivity while ensuring everyone follows standardized processes.
5. Introduce gamification
You can use gamification to introduce elements of competition and motivation into maintenance tasks, especially with new tools. For example, using scorecards to track performance metrics like completed work orders or MTTR can excite your teams and engage them more with the new technology.
Teams can set goals and compete across different locations, driving productivity and making the adjustment period more enjoyable. Gradually introducing benchmarks and celebrating early wins helps build momentum, foster accountability, and create a sense of ownership over the new digital tools and processes.
Empower your teams to drive transformation
When leaders implement digital transformation strategies with their frontline teams in mind, the results are clear: increased performance, expanded teamwork and collaboration, and improved ROI. For example, McKinsey reports that companies that successfully leverage digital strategies such as AI, predictive maintenance, and real-time analytics have significantly improved efficiency and reduced costs—with some companies reporting productivity gains of up to 10%.
To achieve these outcomes, take action: ask the right questions, enable your frontline teams from the start, learn from successful examples, and partner with trusted technology experts. By following these steps, you’ll be well on your way to unlocking the full potential of your digital strategy.
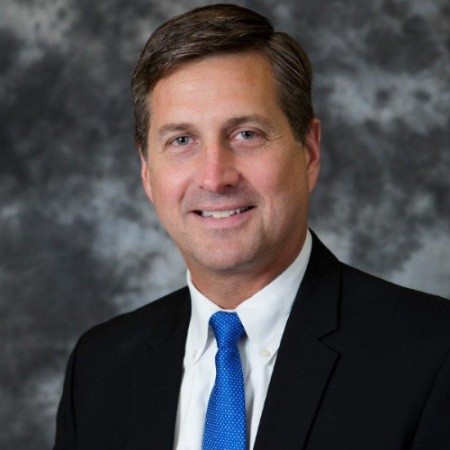