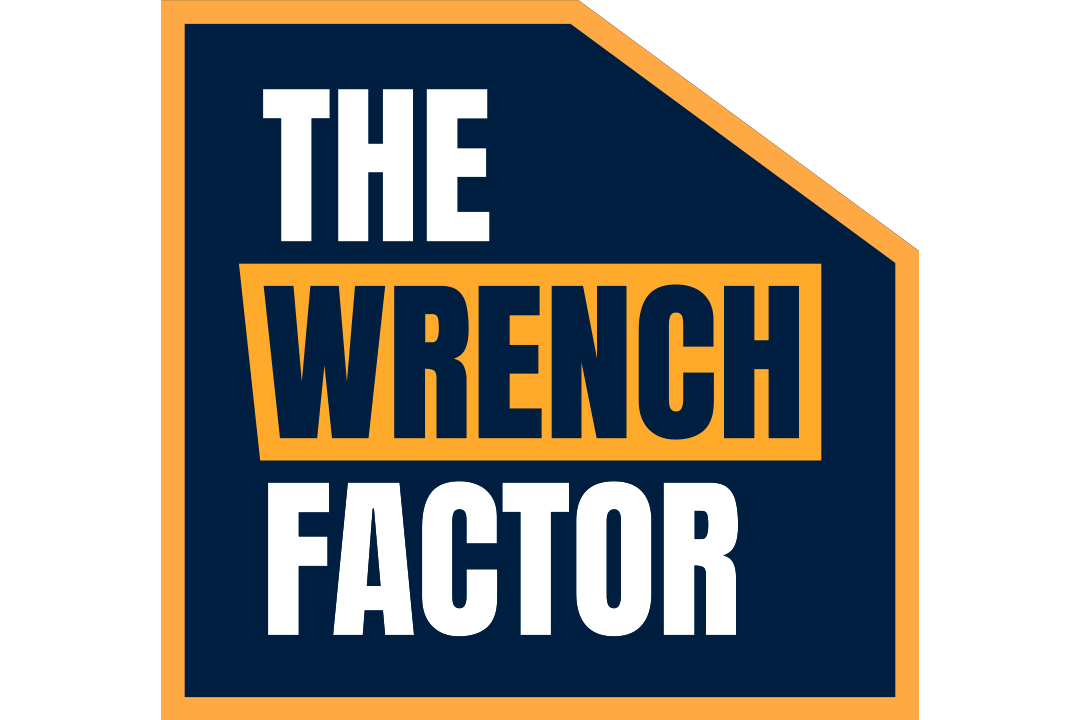
As maintenance strategies shift from reactive to predictive, the integration between enterprise systems and specialized maintenance solutions has become even more important.
The MaintainX team recently hosted Alex Quek, a senior client partner at LeverX, on our The Wrench Factor series. Read on or watch the podcast below to see how technology partnerships are reshaping maintenance management and driving value for asset-intensive organizations.
The evolution to public cloud solutions
A major transformation is underway as organizations move from traditional on-premise systems to cloud-based solutions. An example of this is SAP's strategic shift toward public cloud offerings, which is creating new opportunities for organizations to modernize their maintenance operations.
Alex noted, "What we're seeing with public cloud is that it's becoming the number one focus for SAP, especially in the mid-market space." This move represents a fundamental change in how organizations approach system customization and integration.
The traditional approach of heavy ERP customization is giving way to a more modular, flexible architecture that installs a clean core while allowing for specialized extensions. This framework enables maintenance-specific solutions, such as CMMS and EAM, to seamlessly integrate with core business processes, ensuring data flows efficiently between operational technology (OT) and information technology (IT) systems.
Bridging the OT-IT gap with mobile-first solutions
One of the biggest challenges in industrial maintenance has been the disconnect between OT and IT. Traditionally, maintenance teams rely on real-time equipment data, while IT systems focus on long-term analytics, planning, and enterprise resource management. However, without seamless integration between these two domains, critical machine data often remains trapped in siloed legacy systems, leading to delays, inefficiencies, and increased downtime.
Tyler Hufstetler, a partnerships leader at MaintainX, explained how we’re addressing this fundamental issue: “We want information to flow into MaintainX, provide actionable insights, and then push that information back out. We're providing the connection between traditionally disparate sources, capturing data from the shop floor from sources such as MES and IoT data from vibration sensors—creating a hub of information that gets pushed to the appropriate databases of record.”
MaintainX’s mobile-first approach unites data from the shop floor with enterprise-level insights, ensuring that both OT and IT stakeholders can collaborate in real time. By breaking down silos and delivering actionable data directly to technicians and decision-makers, we empower teams to optimize equipment performance, minimize downtime, and drive continuous improvement.
Accelerating ROI through data-driven maintenance
The discussion also covered how teams can benefit from flipping the traditional digital transformation approach. Rather than starting with heavy ERP implementation followed by operational technology, organizations can achieve faster ROI by beginning with maintenance optimization.
"If we start with the OT driving the quick wins and operational transformation, and then deploy the heavier ERP workflows behind it, we're able to establish ROI today while putting them on their digital transformation journey for the future," explained Tyler.
Unleashing the power of AI and automation
As maintenance data becomes more accessible and connected, artificial intelligence is emerging as a transformative force in predictive maintenance. MaintainX's CoPilot uses AI to make every maintenance technician an expert by providing targeted guidance and insights directly through mobile devices.
This approach to AI focuses on practical application, putting insights and expertise at technicians’ fingertips when and where they need it. Rather than requiring extensive training or system knowledge, AI-powered tools can analyze historical data, maintenance procedures, and asset performance to recommend the best approach for specific scenarios.
Creating a connected ecosystem through partnerships
The discussion emphasized how the partnership between specialized solutions like MaintainX and broader ERP platforms like SAP creates a powerful ecosystem for customers. Integration partners like LeverX play a crucial role in connecting these systems, ensuring data flows between platforms.
"We've developed expertise within these industries that allows us to become advisers for our customers and help bridge the gap between SAP and our customers," noted Alex. This expertise translates into tangible results, with implementations achieving "40% reduction in order processing time or 30% reduction in operational costs."
By connecting maintenance activities with broader business processes, organizations can achieve holistic visibility into asset performance, maintenance costs, and operational impact.
The future of maintenance: Flexible, connected, and intelligent
The maintenance landscape will continue to evolve toward more flexible architectures where specialized solutions integrate seamlessly with core business systems. Organizations that embrace this approach can adapt more quickly to changing conditions while preserving their core investments.
The integration of real-time operational data with AI-powered analytics will accelerate the shift toward predictive and prescriptive maintenance. Maintenance will become truly intelligent—not just predicting problems but prescribing and automating solutions through the entire maintenance workflow.
For organizations navigating this transition, partnering with experts who understand both the technical and operational aspects of maintenance transformation is key. The right partnerships can accelerate time-to-value and ensure maintenance initiatives deliver impact.
Taking the next step
As you consider your own maintenance transformation, remember that you don't have to tackle everything at once. Start with the areas that will deliver immediate value, often at the operational level, and build momentum for broader digital initiatives.
MaintainX's mobile-first platform provides an ideal starting point, delivering immediate operational improvements while integrating seamlessly with your existing and future ERP system. By focusing on the frontline first, you can drive change today while positioning your team for long-term success.
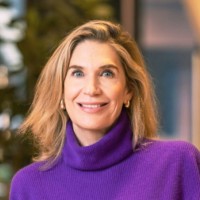
Head of Corporate Communications