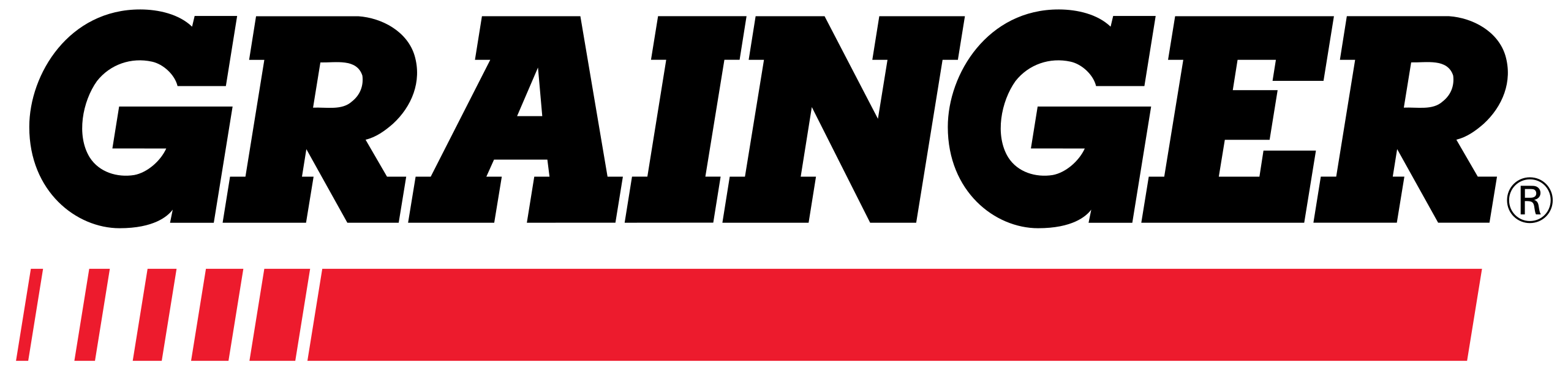
Overview
- Save time spent on manual data entry in MaintainX and Grainger
- Easily track costs related to ordering parts
- Order the most-used parts and keep your inventory lean
- Avoid emergency shipping costs by placing orders based on low inventory levels
- Monitor your parts inventory and get alerts when stocks run low
- Automate re-orders to keep critical parts on the shelf
- Push purchase orders directly to Grainger so your order can be fulfilled
- Track the status from start to finish in both MaintainX and Grainger
How it works
STEP 1:
Connect with your dedicated account representative to understand your existing workflows and objectives for integrating MaintainX and Grainger.
STEP 2:
Identify members of your team that will be part of testing and implementing this integration — such as members of your Operations, Finance, and IT teams.
STEP 3:
A MaintainX integration consultant will add necessary custom fields, and map MaintainX purchase order fields to Grainger fields.
STEP 4:
Test the integration with your team. Start developing internal training material to set your users up for success.
STEP 5:
MaintainX and Grainger are now in sync. You can keep critical parts on the shelf with this time-saving integration.
Requirements
- Must have an account with Grainger.
- Must have MaintainX's Premium or Enterprise Plan.
FAQs
Where do I find information and specifications for Grainger products?
Product information, specifications, buying guides, and more are available on the Grainger website (grainger.com).
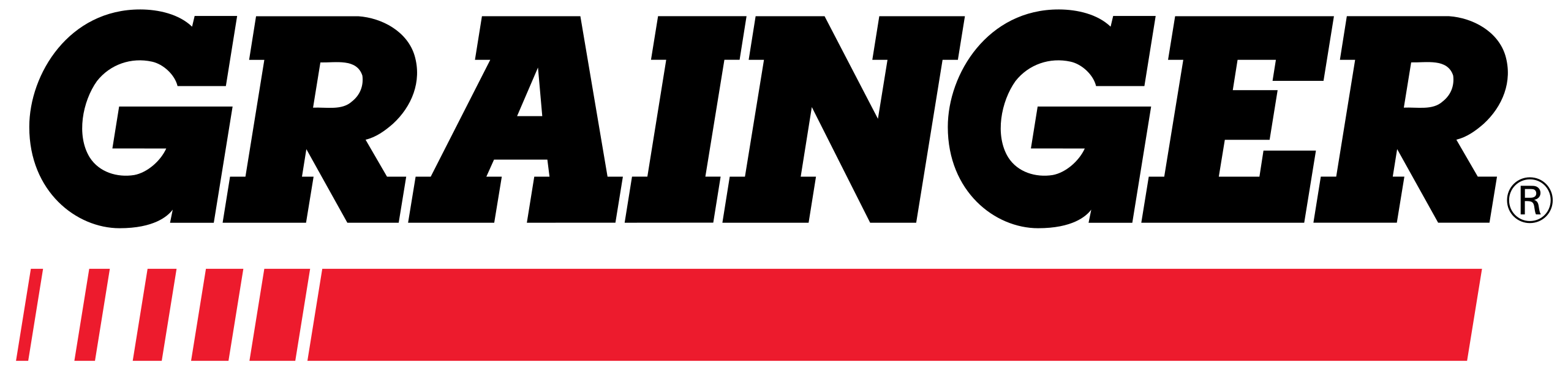
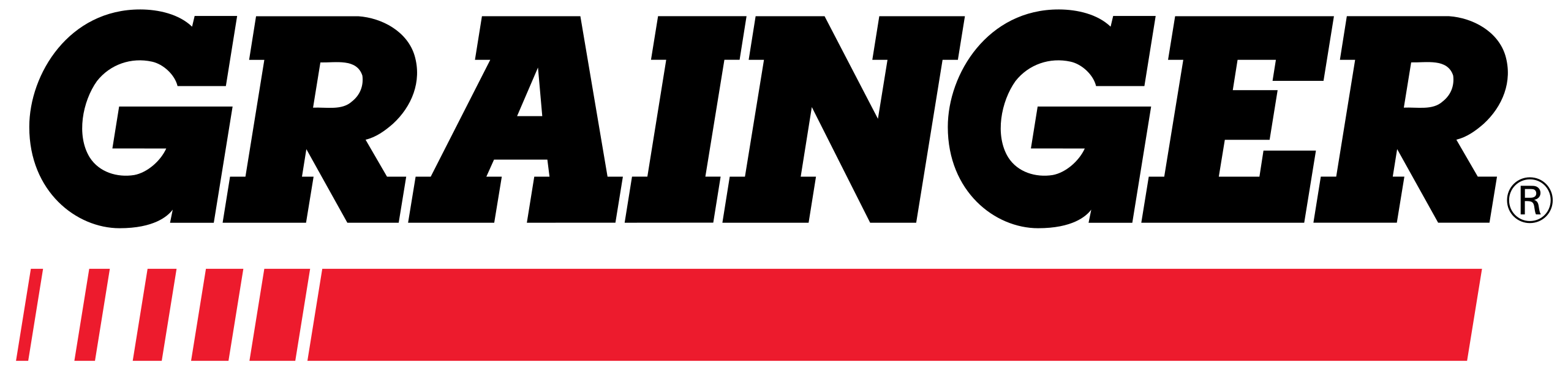
Find other integrations
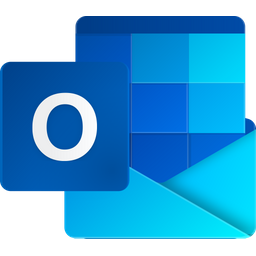
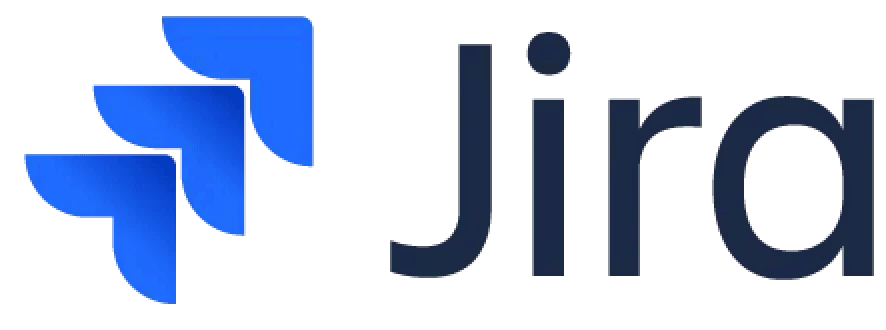
Get more done with MaintainX
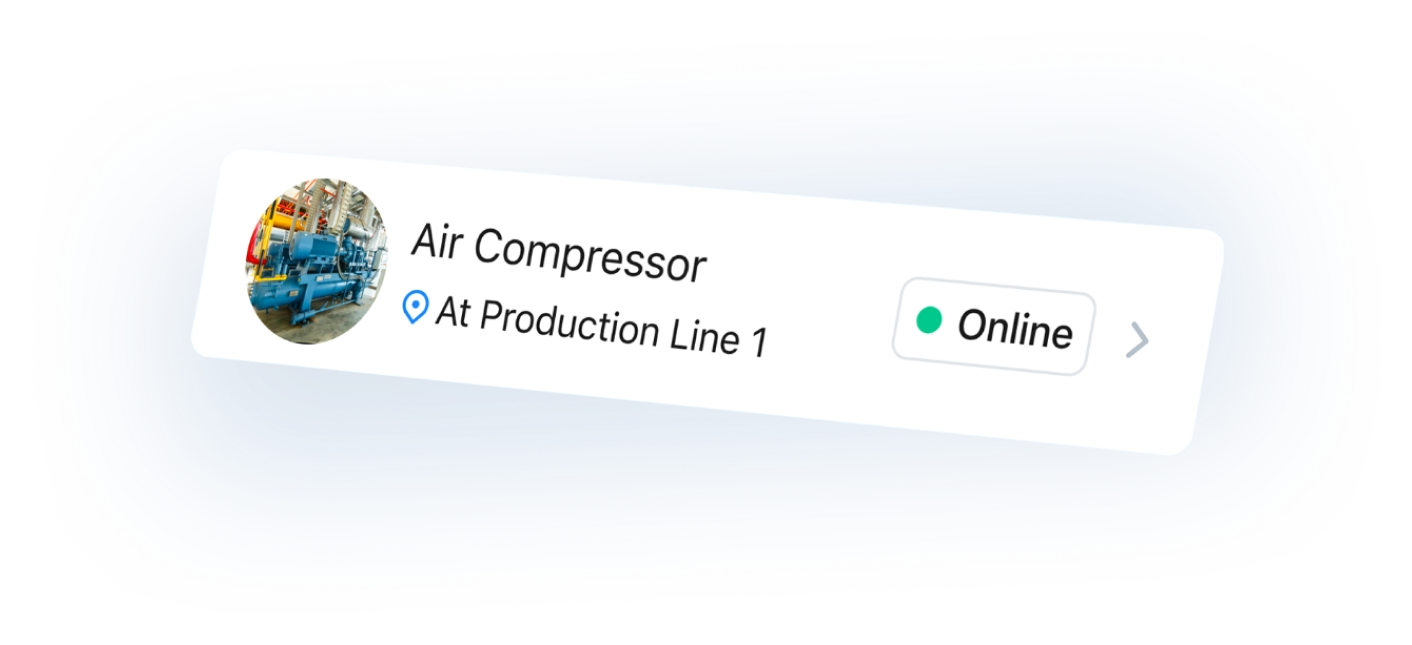
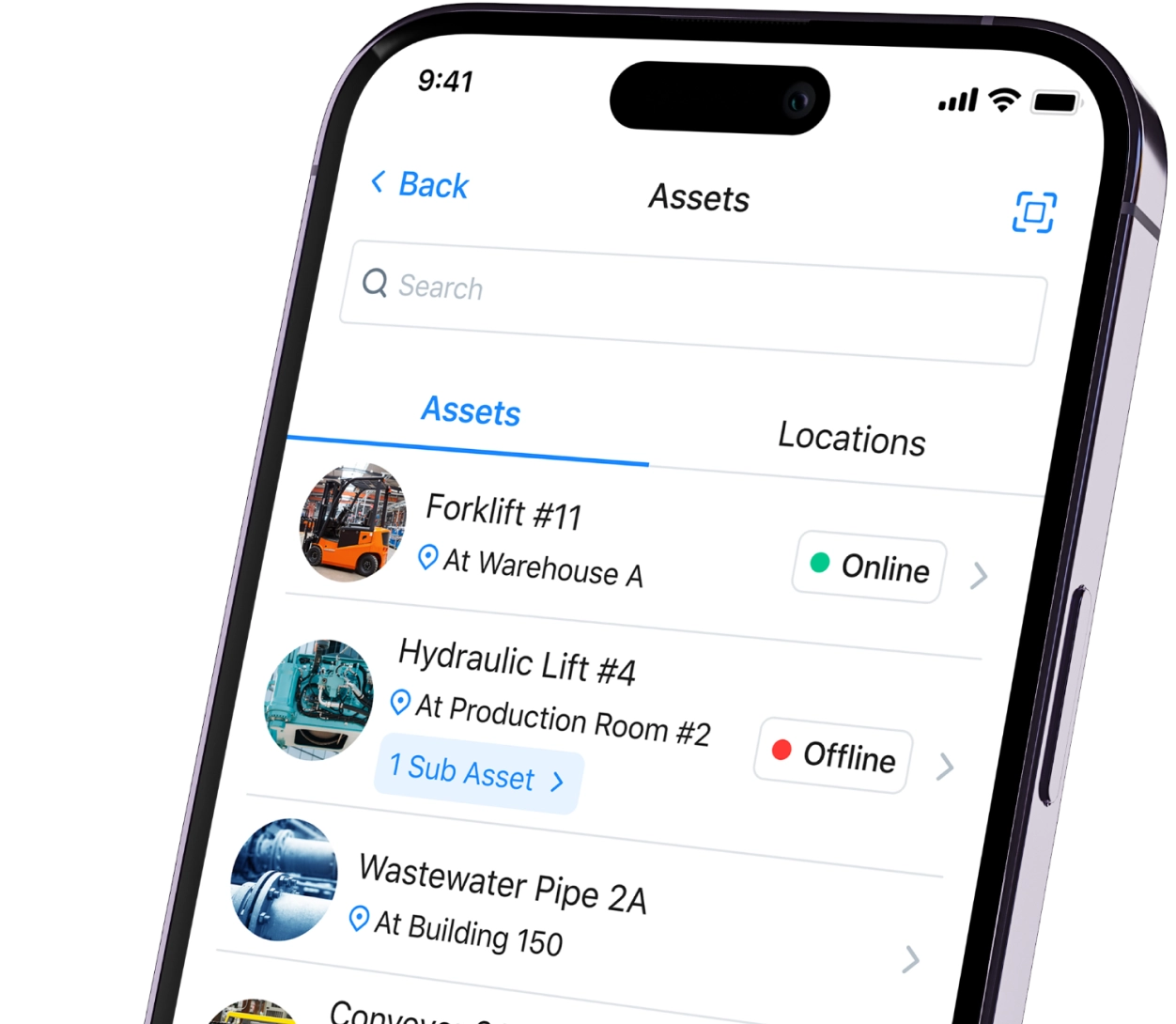