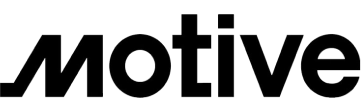
Overview
- Avoid major vehicle issues and costly repairs by proactively conducting scheduled and condition-based maintenance
- Trust the fleet and maintenance information in both systems since your assets and data are automatically synced
- Stay on top of all fleet maintenance processes from start to completion, ensuring seamless workflow management
- Sync mileage and engine hours into meters in MaintainX
- Trigger a work request or work order in MaintainX when a vehicle throws a fault code
- Map assets in both systems, so your teams have one source of truth
How it works
STEP 1:
Connect with your dedicated account representative to understand your existing workflows and objectives for integrating MaintainX and Motive.
STEP 2:
Identify members of your team that will be part of the integration process — such as members of your Operations and IT teams.
STEP 3:
A MaintainX integration consultant will meet with you to determine the scope of the integration before providing the cost and statement of work.
If you decide to move forward with this integration, your MaintainX integration consultant will add necessary custom fields, and map existing fields so your data — including fault codes, mileage, and maintenance information — flows between MaintainX and Motive.
STEP 4:
Test the integration with your team. Start developing internal training material to set your users up for success.
STEP 5:
MaintainX and Motive are now in sync. Your maintenance technicians have what they need to keep your fleet in optimal health.
Requirements
- Must have a Motive plan.
- Must have the MaintainX Enterprise plan.
FAQs
Can we review/assess the work requests that are triggered by the Motive integration?
Yes, you can review and approve or decline the work request in MaintainX. If approved, you can assign it to a team or a specific technician and monitor the progress from start to finish.
How frequently can data be sent between MaintainX and Motive?
Data can be sent every hour.
Will the MaintainX work request or work order be routed to the correct Motive asset or location?
Yes, the work request or work order will be routed automatically. Your MaintainX integration consultant will assist you with mapping to the correct asset or location.
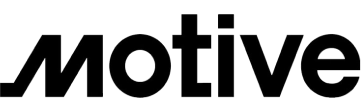
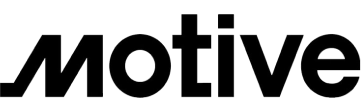
Find other integrations
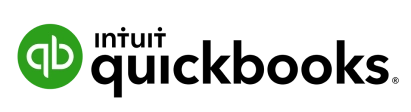
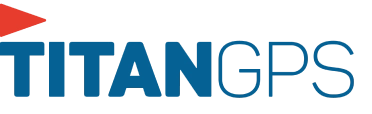
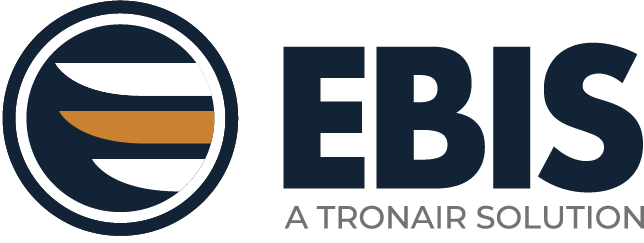
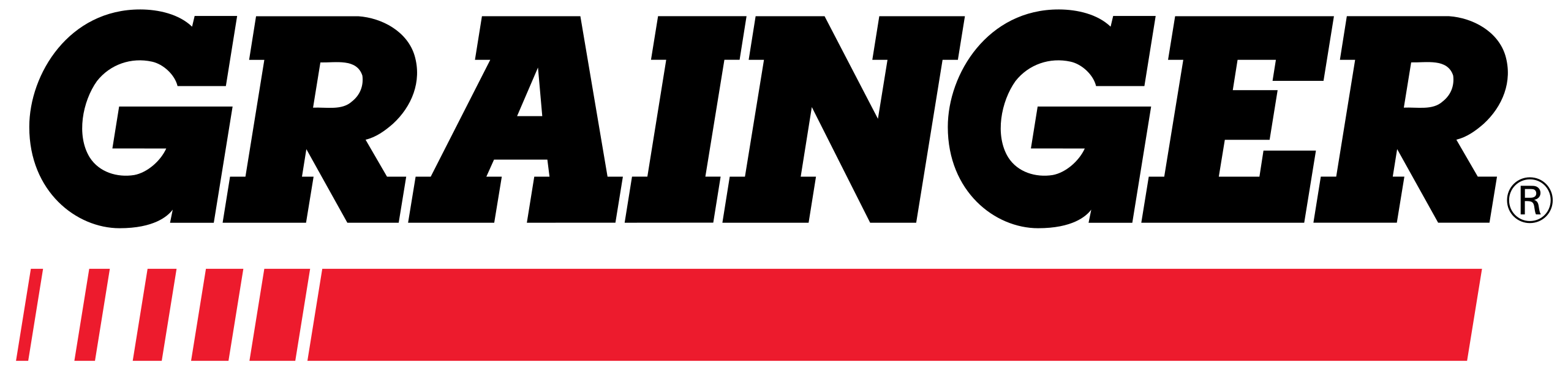
Get more done with MaintainX
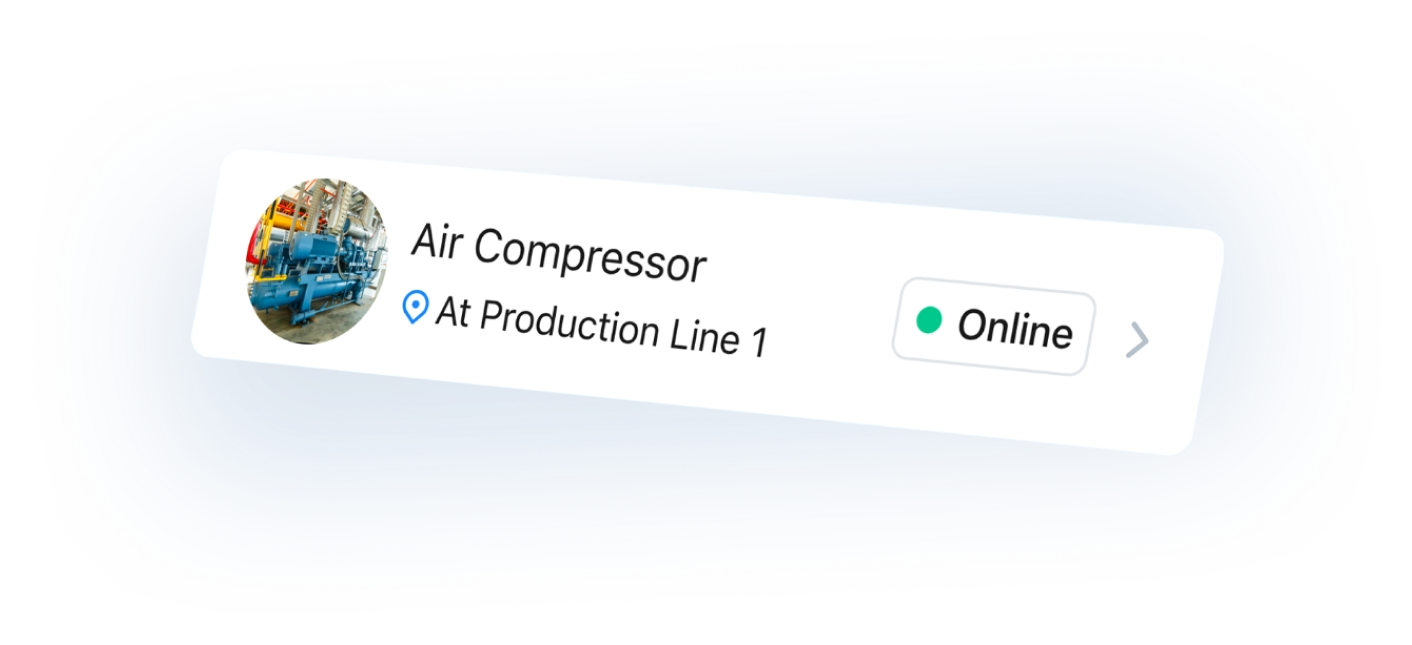
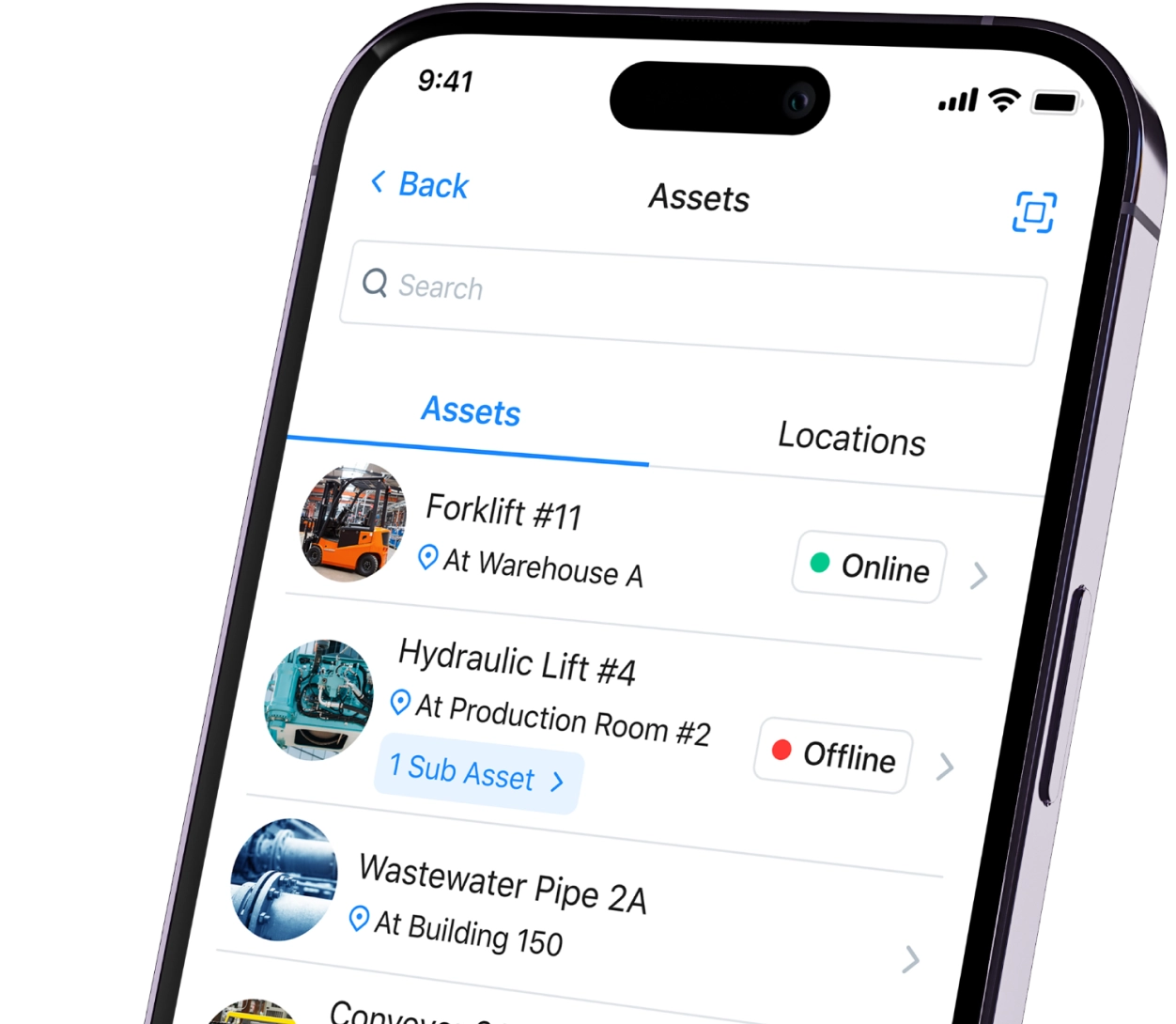