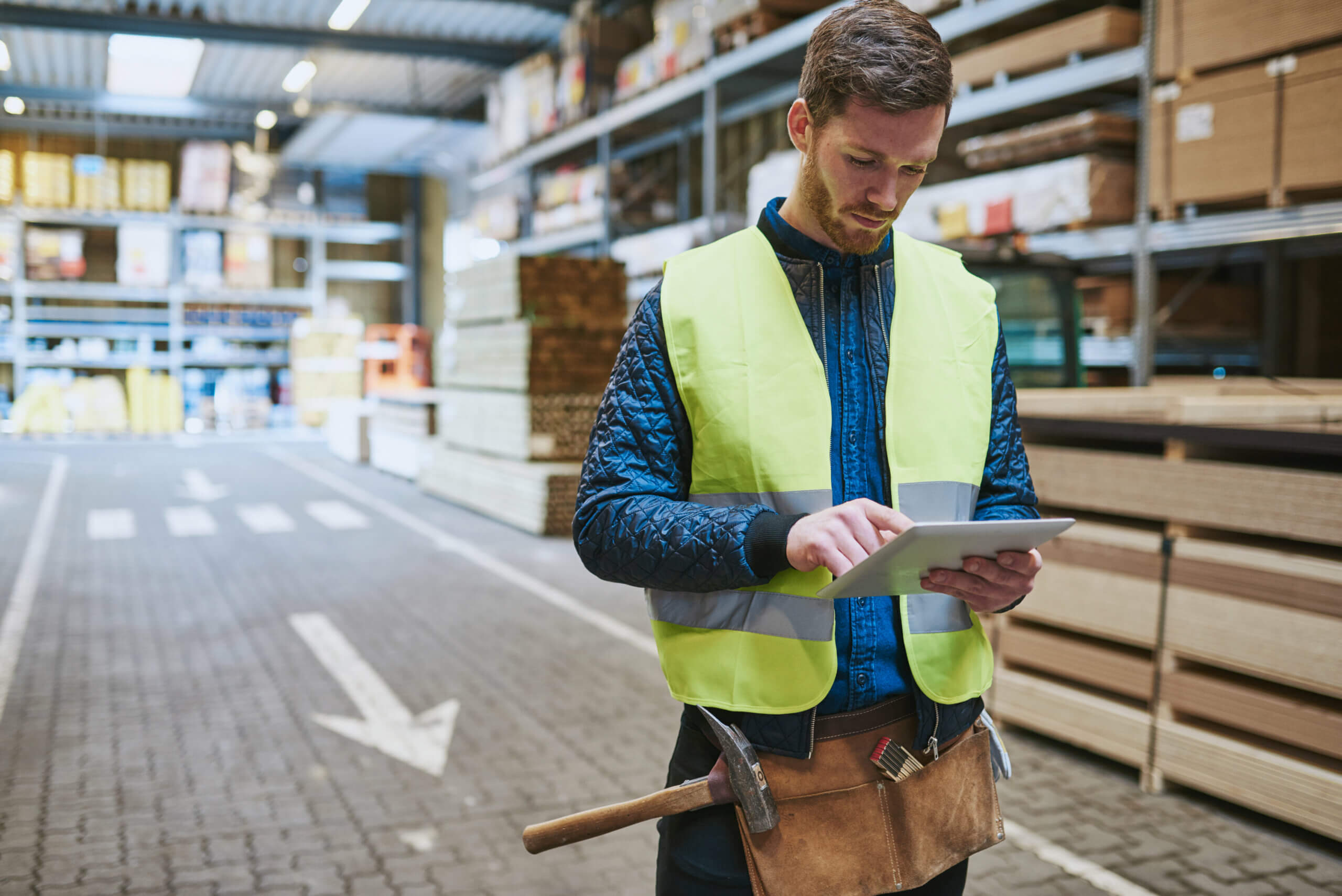
Strategic preventive maintenance (PM) programs can increase ROI (return on investment) by reducing unnecessary O&M spending. Practicing PM is not about eliminating all equipment problems as much as preventing larger ones from taking place.
Efficient PM programs reduce unnecessary spending associated with unplanned breakdowns in four primary ways:
- Reduces Unplanned Downtime Risks
- Increases Operational Efficiency
- Increases Equipment Life
- Improves Customer Service
Businesses cannot thrive until they minimize operating costs with optimized maintenance scheduling. Preventive maintenance (PM) is an effective strategy used globally to reduce downtime, increase productivity, and minimize emergency maintenance repair costs.
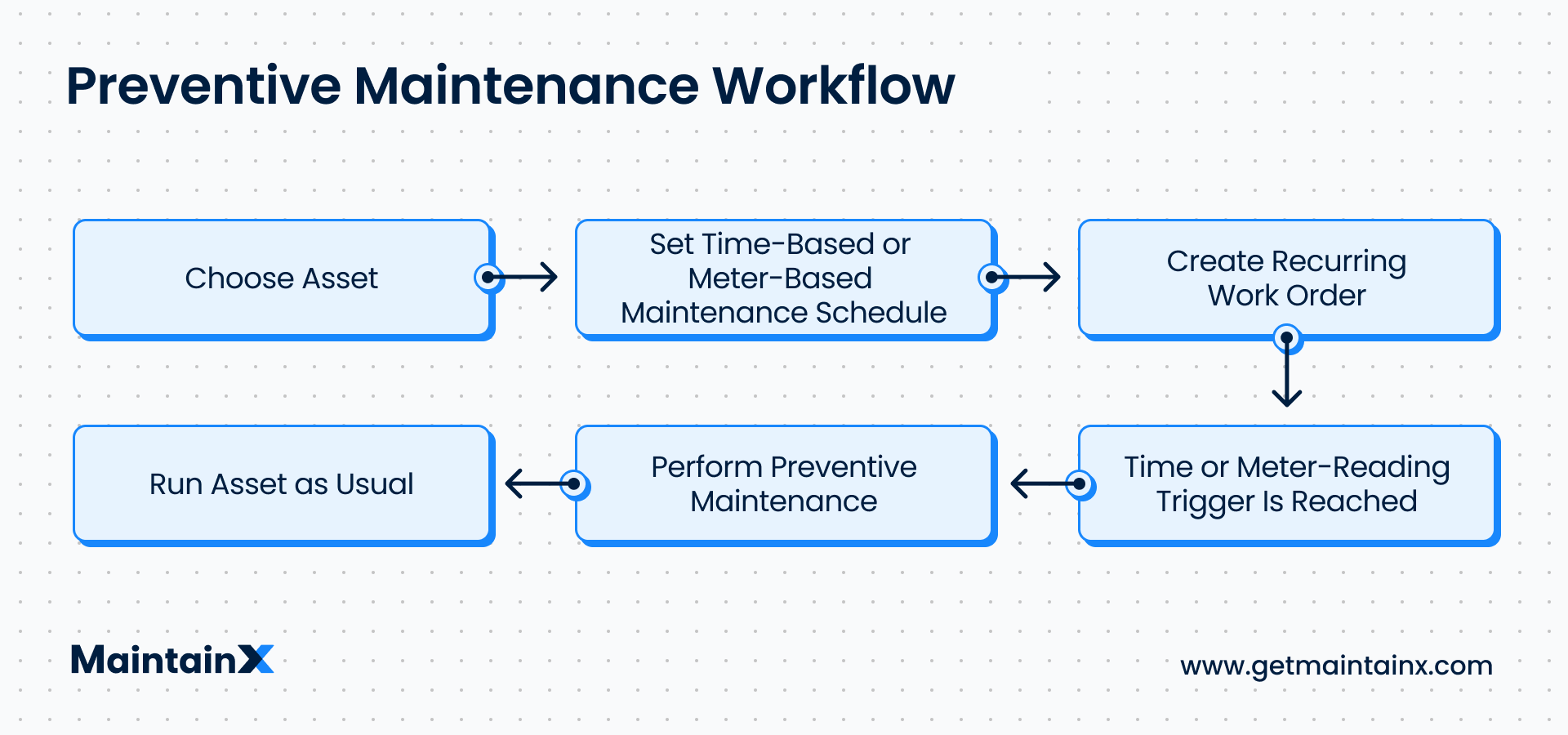
Increasing ROI with Manufacturing Maintenance
The key to creating a successful preventive maintenance schedule is identifying the correct maintenance interval for each asset.
The correct interval planning allows you to maximize resources while reducing the chance of unexpected breakdowns. To create an effective preventive maintenance schedule, follow these steps:
How to Create an Effective PM Schedule
1. Inventory Assets
Create an inventory of your organization’s most crucial assets. These pieces of equipment should receive preventive maintenance first. You can use a spreadsheet or a computerized maintenance management system (CMMS) to catalog your asset entries. We recommend adopting a user-friendly platform like MaintainX to maintain asset records, cross-reference data, and glean cost-saving insights over time.
2. Determine Priorities
Prioritize assets critical to production, require regular maintenance, or have high repair and replacement costs when making your preventive maintenance schedule. Remember: it is more cost-efficient to place non-critical and older assets on reactive maintenance programs. You might be replacing them soon, after all.
3. Identify Ideal PM Intervals
Of course, preventive maintenance is not without a potential downside. Without proper planning, you risk wasting precious resources on unnecessary inspections and repairs. Likewise, avoid overdoing it by identifying ideal PM ratios for your individual assets.
4. Schedule Recurring Work Orders
Modern, cloud-based CMMS platforms are scalable, affordable, and user-friendly. Artificial intelligence, work order automation, and inventory management—are all very much a part of the best CMMS.
Furthermore, the software allows you to automate both long-term maintenance schedules and short-term schedules based on quarterly, monthly, weekly, and daily tasks. In addition, IoT and meter-based readings add a level of protection that works hand-in-hand with preventive maintenance and condition-based maintenance planning.
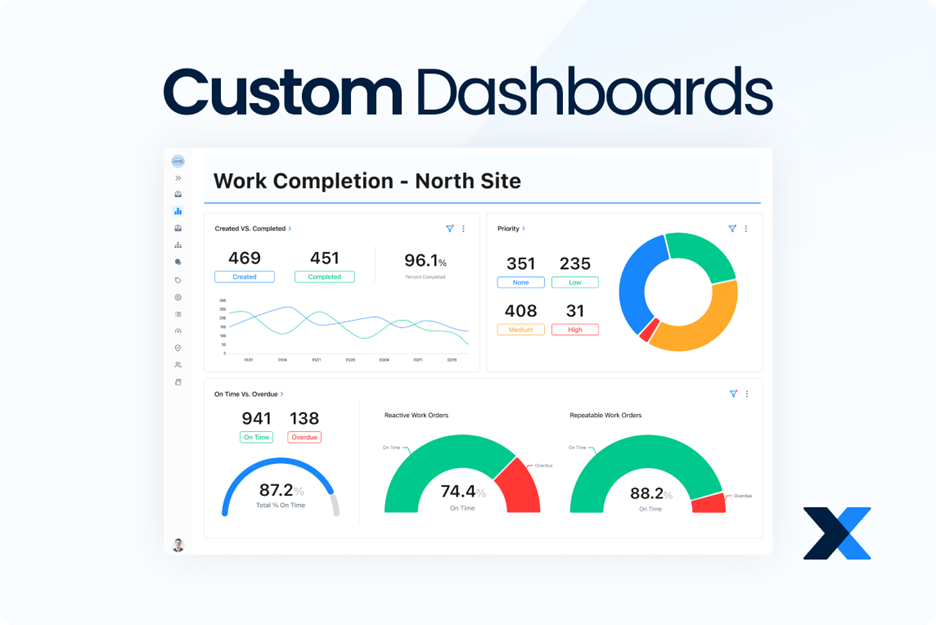
5. Monitor Progress
Lastly, periodically monitor the progress of your maintenance schedules and identify areas for improvement. Most importantly, evaluate how many PMs your teams have completed since creating your initial maintenance schedules. Additionally, several metrics/KPIs are available to track the progress of your PM program, including:
- Mean Time Between Failure (MTBF): MTBF is the average time between asset breakdowns.
- Planned Maintenance Percentage (PMP): PMP measures how many scheduled maintenance activities have been completed compared to your overall number of maintenance tasks.
- Scheduled Maintenance Critical Percent (SMCP): This metric measures how late a recurring maintenance activity is in relation to how often it should be performed and completed.
- Overall Equipment Effectiveness (OEE): OEE measures the level of productivity for an asset. It combines asset availability, performance, and production quality to determine the efficiency of an asset in production.
Finally, despite a maintenance team’s best efforts, the team may still find itself performing what is called “unplanned maintenance,” often the result of unanticipated equipment failure.
Improve Manufacturing Maintenance KPIs to Increase ROI
A maintenance strategy is a systematic approach to maintaining assets in prime working condition for efficient production. It involves equipment maintenance checks, data analysis—of KPIs, failure rates, performance, and costs—and repairing or replacing faulty equipment. High-level maintenance programs typically mix several different maintenance strategies based on the needs of individual equipment.
Evaluate every aspect of your production line. Pay special attention to measuring throughput—the average number of units your company produces in a given period. This measurement will highlight any issues with specific machines.
Why Are KPIs Important?
KPIs are essential for manufacturers because they are defined, measurable metrics that help businesses focus on what is most important to track, analyze, and optimize performance over a period of time.
A Key Performance Indicator (KPI) or metric is a well-defined and quantifiable measure that an organization uses to gauge its performance over time. For example, manufacturing companies specifically use KPIs to monitor, analyze, and optimize operations, often comparing their efficiencies to competitors in the same sector.
For example, key performance indicators are crucial to determining the return on investments (ROI), whether it be new equipment, additional employees, or the latest automated sensors.
The only way to stay ahead in this fiercely competitive industry is to implement manufacturing KPIs and metrics. Remember, each time you improve a KPI, you increase your return on investment.
Measuring KPIs to Increase ROI
Every KPI needs a clearly defined goal. It is essential that you can objectively measure your progress toward the goal. There must be a clearly defined data source with a strict procedure for measuring and collecting data. There should be nothing left to interpret here.
Reporting your data is just as important as collecting it. Different manufacturing KPIs will have different reporting frequencies.
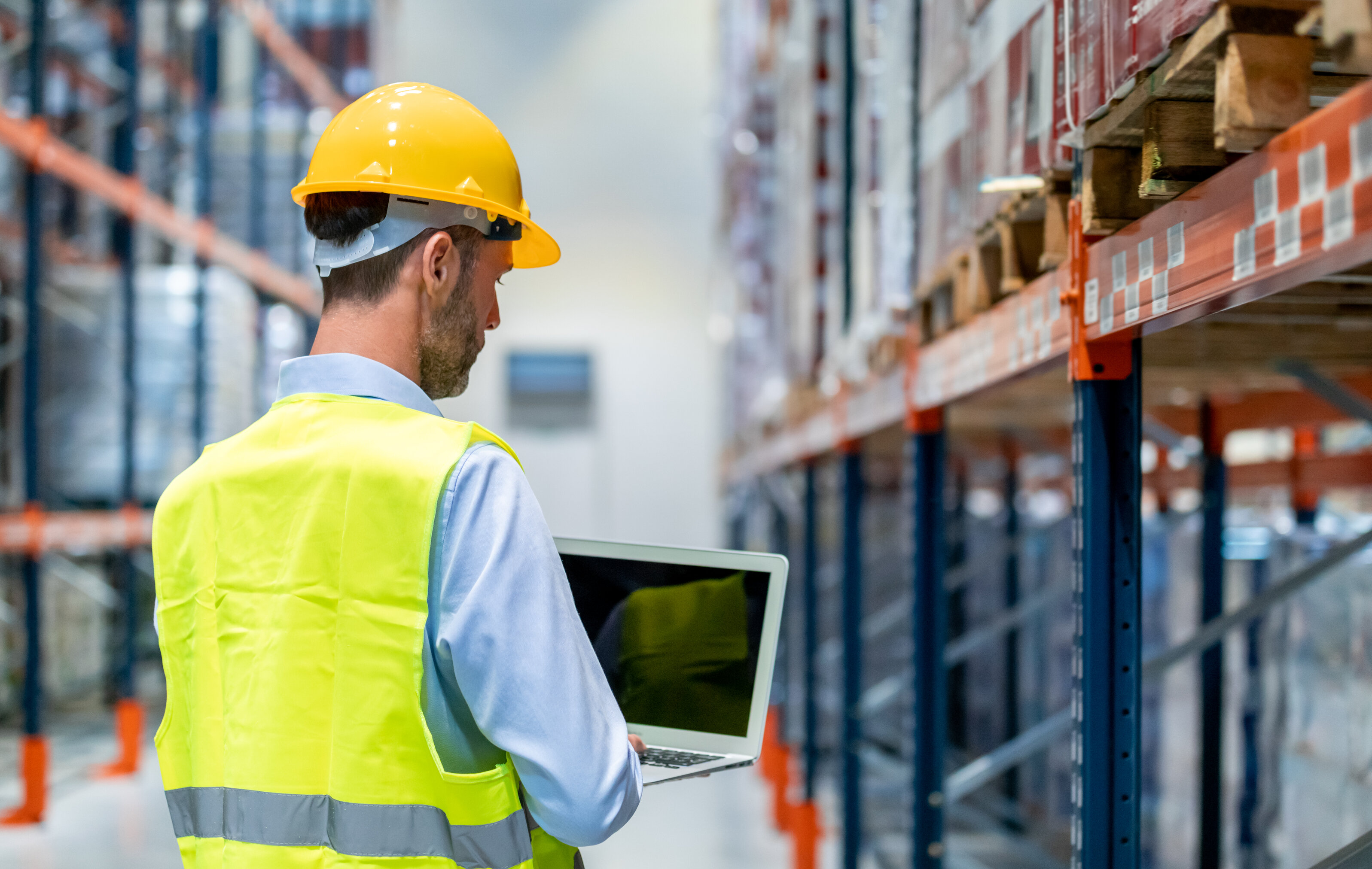
Ideally, CMMS should cross-reference work order data by the assigned technician, asset type, priority status, and time to complete to integrate into meaningful reports that support sound decision-making.
Key performance indicators are also useful to figure out your return on investment, especially if you already use a CMMS for planned maintenance in your manufacturing maintenance workflow. Planned maintenance is a maintenance approach focused on minimizing equipment downtime and returning to uptime as soon as possible after a breakdown.
Every asset wears out at some point. However, leaders can keep equipment efficiently running as long as possible with planned maintenance. The easiest way to execute effective scheduled maintenance work is with a Computerized Maintenance Management System (CMMS).
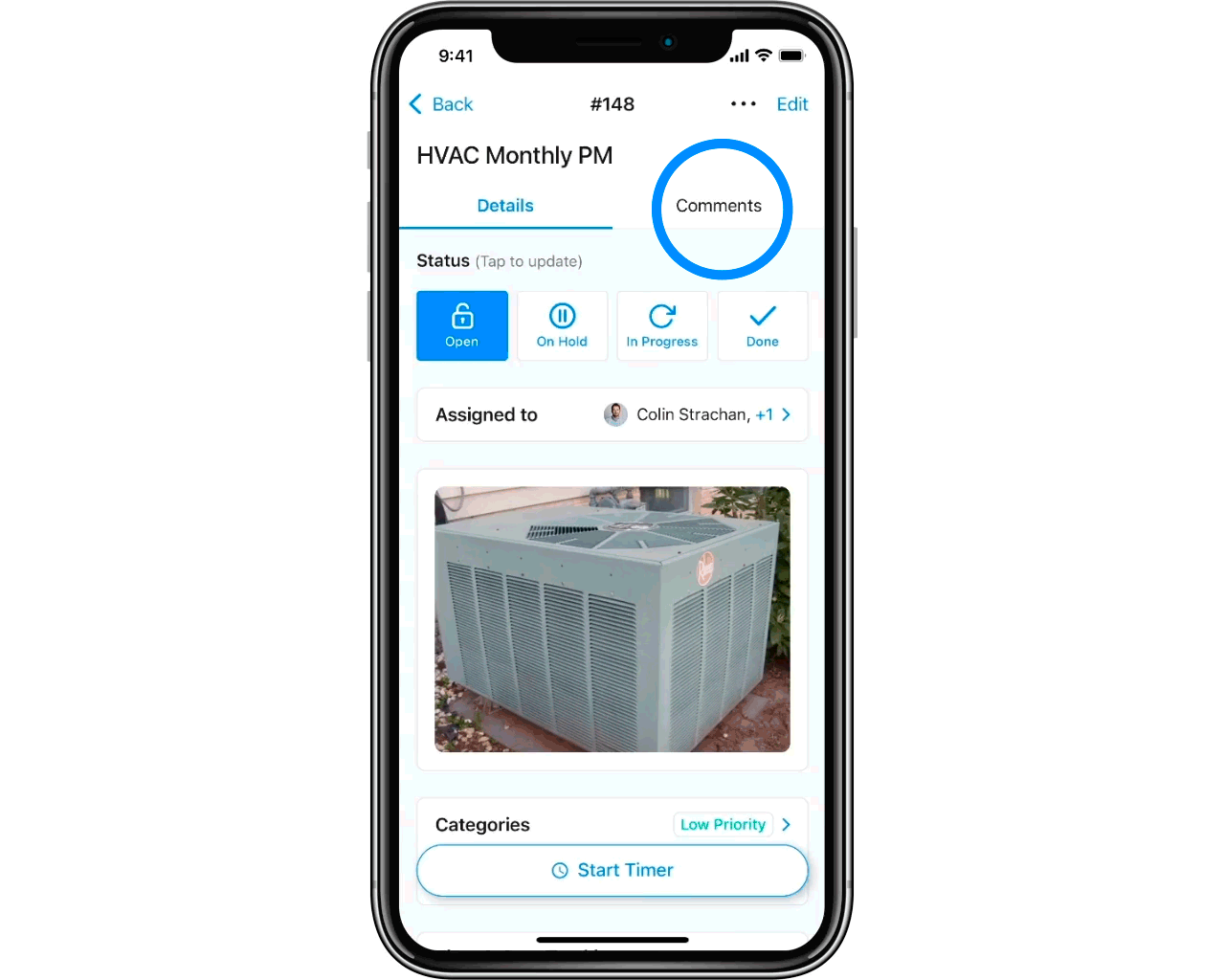
Benefits of Maintenance Management
Smart preventive and predictive maintenance management prioritizes, strategizes, and delegates maintenance-related objectives to maintain company assets.
It involves tracking, controlling, and maximizing equipment lifespans to increase organizational profitability, increase manufacturing processes and efficiency, and reduce downtime and shutdowns.
Unfortunately, manufacturing machine downtime is a common issue for production lines, manufacturing maintenance teams, and plant managers. Unfortunately, there is no easy way to overcome this. However, production delays and downtime are variable, and reducing your Mean Time to Repair (MTTR) is a reasonable goal.
Modern CMMS software systems provide preventative maintenance functions, optimal spare parts inventory levels, improved scheduling and planning, and measurable regulatory compliance.
Preventive maintenance offers a company several benefits. Advantages include decreasing downtime, increasing asset life span, reducing maintenance costs, improving workplace safety, and enhancing company culture.
Decrease Downtime
Preventive maintenance ensures that your equipment continues to run smoothly without unexpected downtime or work stoppage—schedule preventive maintenance at regular intervals.
Help Budget Accurately
Well-designed manufacturing maintenance management systems will enable your organization to be more insightful about how your team’s resources are spent. Fortunately, effective maintenance management software can identify how the team spends most of its time.
Manage Compliance
Beyond sharing documents with regulators, maintenance management systems track and schedule work orders that maintain compliance standards. During inspections, these digital audit trails validate that the appropriate personnel performed tasks efficiently and on time.
Iterate and Optimize
Your most expensive technicians may be spending far too much time performing routine tasks that fewer senior team members can accomplish, especially when a total productive maintenance program may lead to better production efficiency.
Improve Safety
Consequently, maintenance management software can provide timely reminders to follow safety guidelines when performing assigned tasks.
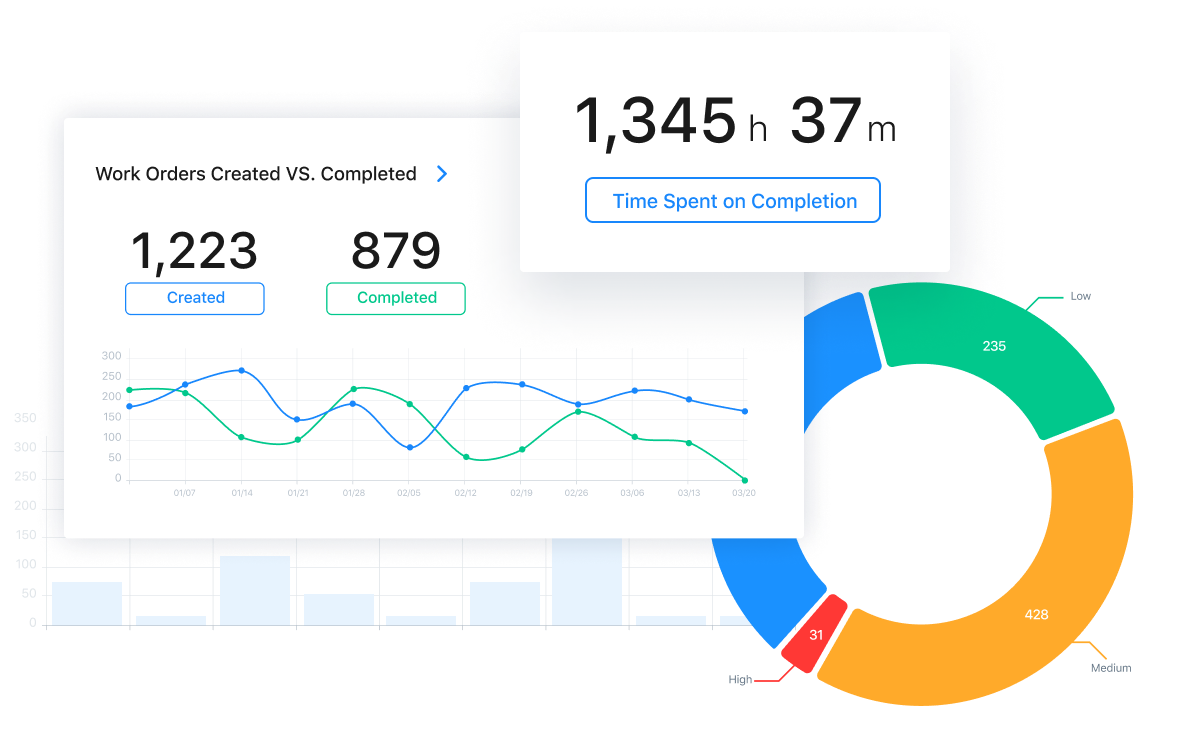
Minimizing Equipment Downtime to Increase ROI
Another important KPI to monitor against your CMMS return on investment (ROI) is equipment downtime. Equipment downtime is the amount of time production stalls due to a non-functioning piece of machinery.
The Cost of Equipment Downtime
Unfortunately, machine failures affect critical business functions, limit profitability, and hack away a company’s bottom line. Some of the costs a manufacturing organization can incur because of equipment downtime include:
- Detection Costs
- Containment Costs
- Recovery Costs
- Equipment Costs
- Lost Revenue
- User Productivity Loss
- Third-Party Costs.
- Business Disruption
In addition, unexpected equipment downtime forces maintenance personnel to divert their focus from preventive maintenance activities to reactive maintenance. Furthermore, reactive maintenance is often more expensive than proactive maintenance plans and predictive maintenance systems. And we know that smart preventive and predictive maintenance plans increase ROI.
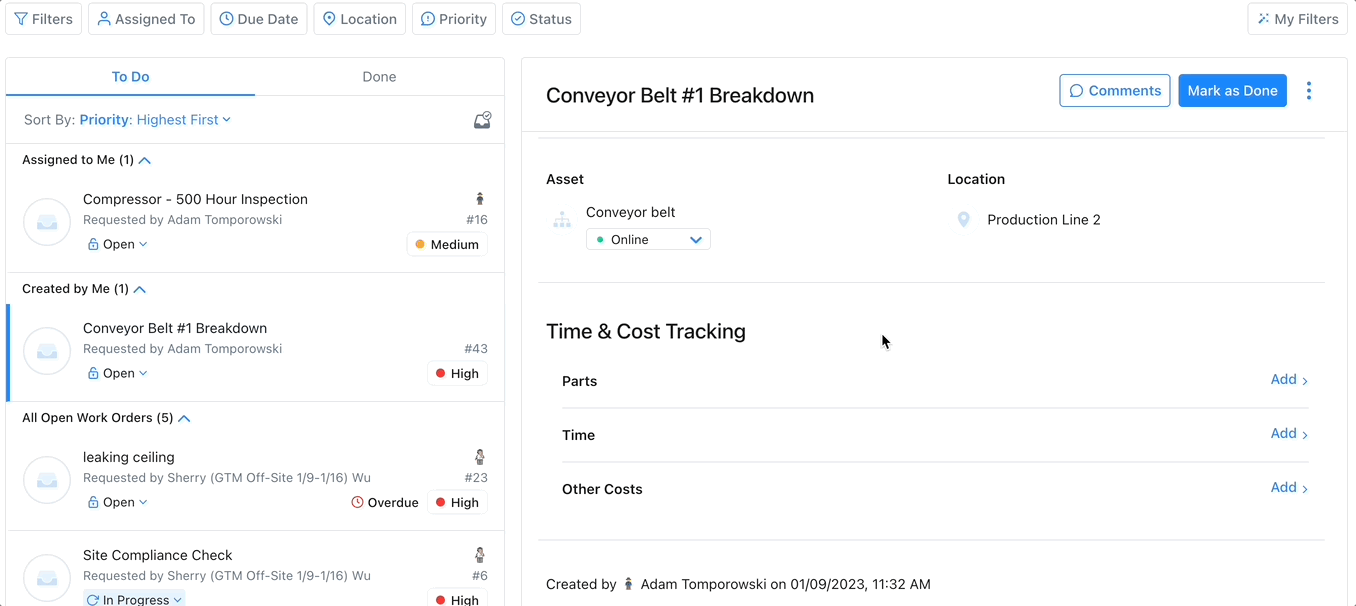
Benefits of Tracking Downtime
Tracking equipment downtime allows operational managers to develop proactive maintenance strategies.
Practicing preventive maintenance (PM) on critical assets means technicians correct minor parts issues before they cause total breakdowns. Benefits of tracking equipment downtime include:
- Enabling maintenance teams to focus on proactive maintenance due to minimal unplanned downtimes
- Providing maintenance managers valuable insights to prioritize work orders
- Encouraging the accurate implementation of corrective maintenance activities
- Supporting higher equipment uptime, reliability, and efficiency
Manufacturing industry experts suggest striving to maintain equipment at 90 percent availability with less than 10 percent downtime.
To be clear, switching from reactive to proactive maintenance mode requires consistent asset historical data analysis, adequate staffing, and a commitment to following a strategic preventive maintenance program.
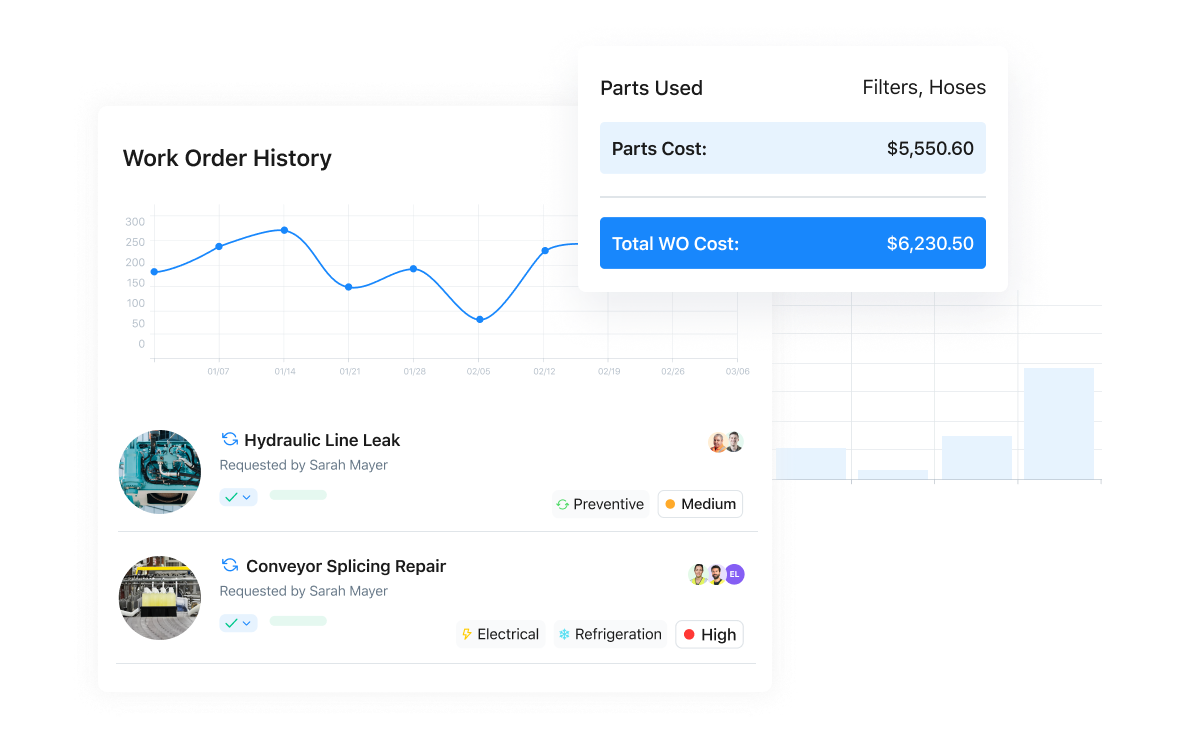
Minimizing Unnecessary Downtime Costs
- Anticipating the impact of downtime on the business
- Tracking an asset’s Useful Life cycle
- Using advanced technology
CMMS software can track probable causes of equipment downtimes and enable maintenance managers to make effective decisions. Additionally, such technology helps to inform where the organization should direct its maintenance efforts to increase ROI. Tracking equipment downtime saves money and time by directing resources to the right maintenance activities.
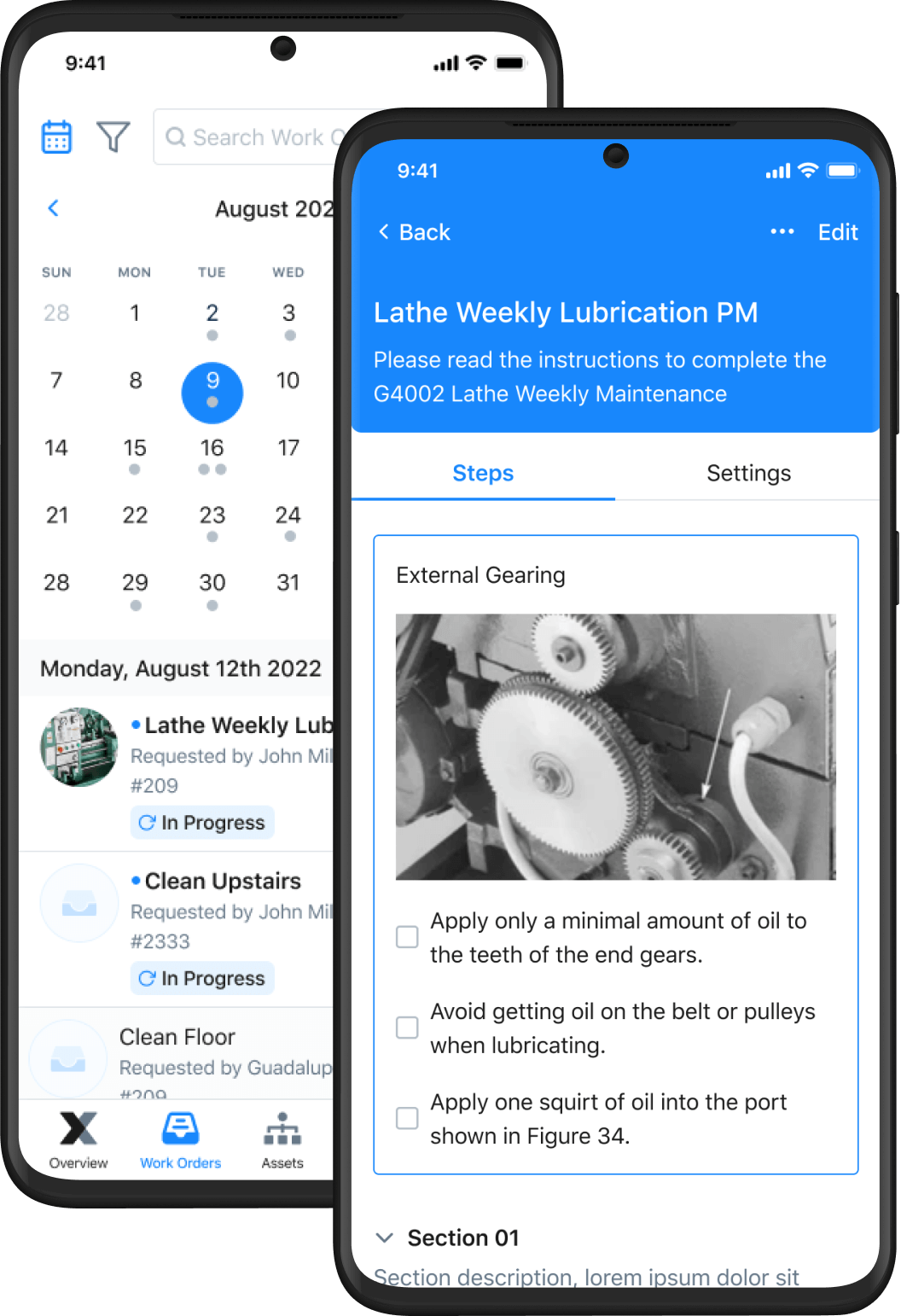
Preventive Maintenance Tips to Increase ROI
Most facility and maintenance managers already understand the value of preventive maintenance. As a result, many of them invest in Computerized Maintenance Management Systems (CMMS) to digitize, assign, and organize work orders. In addition to choosing a user-friendly CMMS, we recommend the following:
1. Tracking Costs for Savings Opportunities
A user-friendly CMMS will make data collection a breeze so that maintenance does not feel burdened with cumbersome data entry steps. In addition, the more equipment data you collect, the less likely your facility will experience downtime, and the faster it will meet customer deadlines.
2. Enhancing Team Communication
The most efficient way to communicate effectively is via business messaging platforms. For example, our CMMS allows manufacturing team members to upload PDFs, take equipment photos, and chat directly within the comment section of digital work orders.
3. Negotiating Preventive Maintenance Arrangements with Equipment Providers
While you should strive to complete most maintenance in-house, collaborating with an experienced equipment service provider on essential assets can be beneficial.
4. Shadowing Equipment Providers
Whenever an outside technician visits, consider assigning an in-house technician to shadow his work. Taking advantage of every training opportunity is key to establishing an effective manufacturing preventive maintenance program.
5. Stocking Frequently Replaced Parts
Stock the most commonly replaced parts to reduce potential downtime and save money in the end.
6. Planning Preventive Maintenance based on Seasonal Variables
Schedule preventive maintenance tasks that require downtime during slower seasons.
Leading a Connected Workforce to Increase ROI
Metrics collected from work orders (WO) can demonstrate how effective or ineffective an organization is operating. Modern connected worker dashboard metrics include information calculated through work orders, such as WO completion, time on task, reactive vs. preventive ratio,
Mean Time Between Failures (MTBF), Mean Time to Repair (MTTR), safety inspections, inventory cost tracking, and more. Improving these metrics decreases downtime, improves efficiency, and therefore increases return on investment.
Leading toward Efficiency
- Choose the appropriate software platform, if one is not already in place
- Build lists of assets and equipment that need to be maintained under the plan
- Create work orders and standard operating procedures to maintain both equipment and operational standard
- Assign work orders to appropriate teams and employees
- Execute work orders following best practices
- Complete all required information on the platform
Leading with Training and Continuing Education
In addition to collecting and analyzing KPI data, leaders can ensure that employees are well trained to complete standard operating procedures efficiently and safely. Actionable insights generated by a connected worker platform provide training opportunities and even re-training to build employee buy-in and reduce errors.
Training, feedback, and opportunities to encourage workers to improve KPI metrics go a long way to eliminating any anxieties brought on by workplace change.
Leading with Accountability
Accountability and digital transformation efforts go hand-in-hand. Strong leadership, built on transparency, employee buy-in, and SMART goals, can create an organizational culture of improvement and dedication.
Strong leadership in this area requires leaders to retain top employees, those with the skills and training—or the willingness to learn new skills—to meet maintenance KPIs, especially as a company grows.
Moving to a KPI model that includes tracking employee performance metrics means that employees need to understand and buy into a system based on measured performance.
Leaders who actively seek to measure and improve performance need to locate what is causing work order bottlenecks and what additional training employees may need. By defining and using smart goals combined with KPI reporting dashboards to increase productivity and efficiency, strong leaders provide employees with achievable performance goals.

Calculating ROI with MaintainX
The MaintainX Reporting Dashboards capture manufacturing industry-standard KPIs, including workforce productivity, completion rates, distribution type, and open work orders, to name a few. The real-time data enables you to check your workforce’s efficiency and effectiveness, equipment, assets, and inspections as they happen.
In MaintainX Reporting, you have access to eight reporting dashboards. From each dashboard, you can filter work order details to go deeper into the specifics.
However, your work should not stop there, even if using MaintainX has already made a world of difference. Our interactive dashboards show you everything you need to run your team and manage your assets with precision.
Dashboard metrics are evidence of the success or failure of workflows throughout a company or a team, with an individual, or even with a particular piece of equipment. Furthermore, data is only as good as what is input by the people doing the work. For example, if no one is creating the MaintainX work orders correctly in the first place, it will be hard to gather the data you need. Similarly, if the work orders are created correctly, but no one fills them out, your data will also be incomplete.
Analyze Performance across Teams and Sites
In addition to the real-time functionality of the Dashboards, you can also look at each dashboard and customize the details you are most interested in. To do this, we offer a range of reporting filters by time and by data.
Through these dashboards and filters, you can focus on how your team, equipment, assets, and facilities are performing and use this information to make data-driven decisions.
By analyzing work orders created and resolved in a specific department, across a facility, within a team, or completed by an individual, you will get both real-time snapshots and deep dives into how the work is getting done.
Using the right CMMS helps organizations:
- Navigate real-time performance data for KPIs
- Identify insights that allow you to highlight organizational bottlenecks and take action
- Track assets to manage asset downtime and capital equipment allocations
- Monitor team performance to identify top performers and employee performance efficiency
- Monitor metrics to calculate KPIs across assets, teams, and locations
Are You Ready to Increase ROI?
MaintainX can improve OEE, reduce downtime, and manage safety and quality inspections—all with one simple-to-use platform.
FAQs
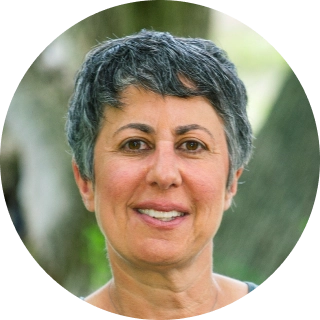
Caroline Eisner is a writer and editor with experience across the profit and nonprofit sectors, government, education, and financial organizations. She has held leadership positions in K16 institutions and has led large-scale digital projects, interactive websites, and a business writing consultancy.