Few things can send your operations into a downward spiral like equipment downtime. The impact can be hard to contain: One key machine goes down, and all of a sudden, your schedule is derailed, and angry calls from customers start pouring in. And that's before you start accounting for the financial losses. Every hour a production line sits idle can cost thousands in lost productivity, replacement parts, and overtime labor.
For maintenance, repair, and operations (MRO) professionals, minimizing downtime is near the top of the priority list. But with skilled labor shortages and rising costs, it's more complex to pull off than ever.
This guide breaks down the types and causes of equipment downtime, how to measure it, and how maintenance teams can reduce it using modern tools like a Computerized Maintenance Management System (CMMS).
Key takeaways
- Equipment downtime is any period when a machine or system is unavailable for use.
- Unplanned downtime is often the most costly type, but idle and planned downtime can also impact productivity.
- Common causes of downtime include equipment failure, poor planning, operator error, and missing parts.
- CMMS software helps reduce downtime through better scheduling, real-time tracking, and standardized processes.
Types of downtime
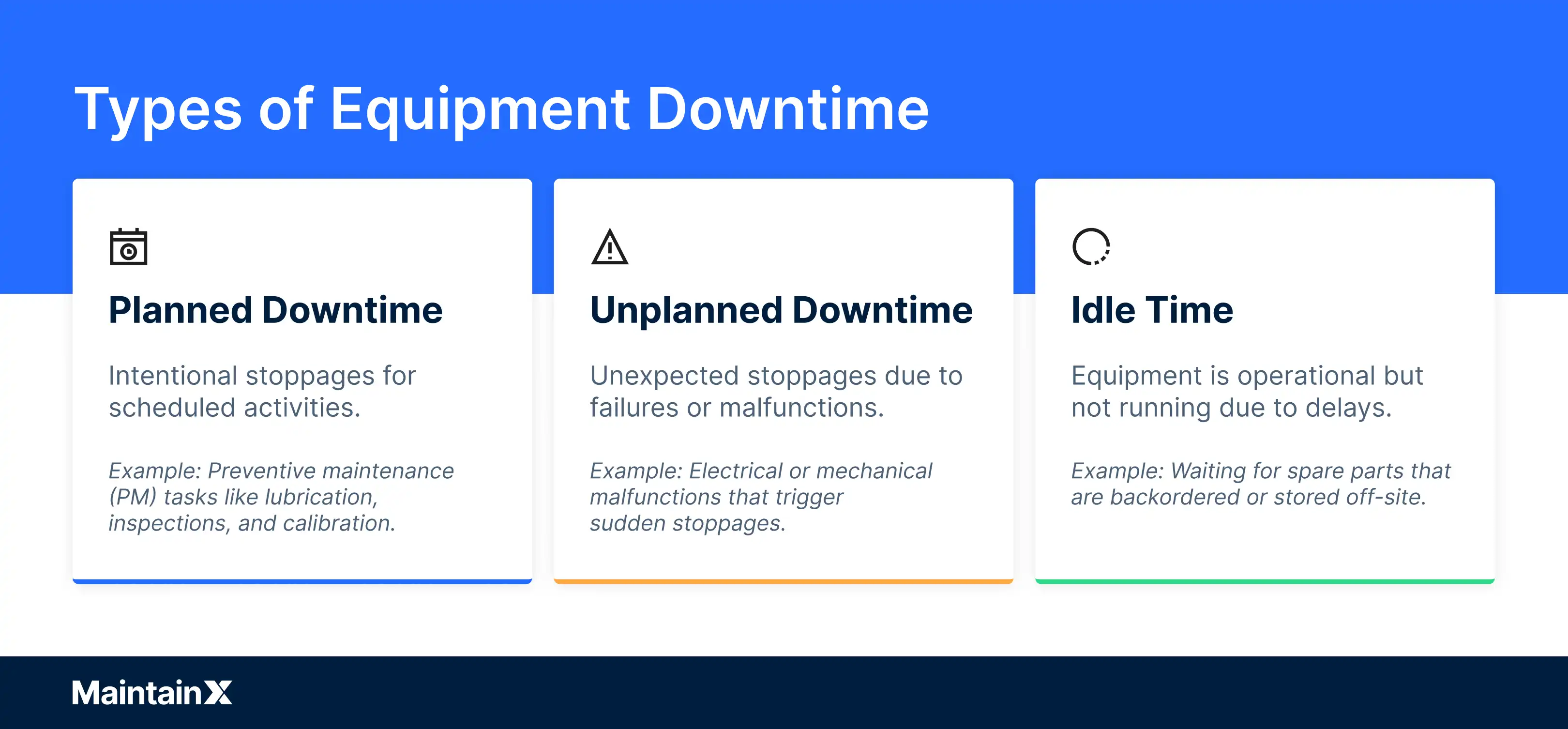
Not all downtime is created equal. Different types of downtime affect equipment utilization and overall productivity in different ways, and knowing how to classify them helps you prioritize responses and uncover root causes.
Planned downtime
Planned downtime refers to periods when equipment is intentionally taken offline for scheduled activities. This is the best kind of downtime: It still interrupts operations, but it's predictable and far easier to manage than its unplanned counterpart.
Common examples of planned downtime include:
- Preventive maintenance (PM) tasks like lubrication, inspections, and calibration
- Routine cleaning of machines to comply with safety or hygiene regulations
- Software updates or system upgrades that require stopping production temporarily
- Scheduled production breaks or changeovers between product runs
Because it’s expected, planned downtime can be scheduled during off-hours or slow production windows to minimize disruption.
Unplanned downtime
Unplanned downtime, also known as unexpected or unscheduled downtime, occurs without warning. It’s the ultimate headache for facility managers, who have to locate and fix the issue before it leads to significant losses.
Some common causes of unplanned downtime include:
- Equipment failure due to aging parts, lack of maintenance, or design flaws
- Electrical or mechanical malfunctions that trigger sudden stoppages
- Emergency maintenance needs stemming from safety incidents or asset breakdowns
Unplanned downtime tends to wreak havoc across the entire facility. It pulls teams away from whatever they’re working on and incurs spend on overtime labor and expedited part orders.
Idle time
Idle time is the most insidious of the three types of downtime. It happens when equipment isn’t running even though it’s technically operational.
Examples of idle time include:
- Waiting for spare parts that are backordered or stored off-site
- Delays due to shift changes or unavailable technicians
- Unclear instructions or lack of authorization to proceed with repairs
While idle time may not stem from a machine failure, it still represents lost production hours and
reduced equipment utilization. These delays can quietly drain efficiency and negatively affect
KPIs like OEE (Overall Equipment Effectiveness) and labor productivity.
Common causes of downtime
Downtime doesn’t happen in a vacuum. It usually results from a combination of preventable issues, including technical, operational, and process or communication gaps.
Let’s walk through some of the most common causes of equipment downtime.
Equipment failure
This is the most obvious and frequent cause of machine downtime. It’s also mostly preventable. Machines usually fail because they’re old or haven’t been maintained properly.
Inadequate maintenance planning
Preventive maintenance is the best way to avoid equipment downtime. But it’s easier said than
done. Getting it right requires putting together maintenance plans and ensuring your teams follow them to a T. Teams that rely on a reactive maintenance framework open themselves up to more frequent failures.
Lack of spare parts
You can’t fix what’s broken if essential components are out of stock. Unexpected downtime becomes extended downtime as technicians wait for deliveries or scramble to source emergency replacements. It’s not reasonable to have a backup of every single component, but you should keep the most commonly used ones in stock.
Operator error
Even perfectly maintained equipment is subject to occasional human error. Some mistakes are
unavoidable, but most of them can be minimized or prevented entirely with proper training. Anyone who operates a machine should be well-versed in required safety checks and standard operating procedures (SOPs).
Poor training or documentation
Maintenance staff are far more likely to make mistakes if they don't have proper training or
documentation to reference. The most common culprits here tend to be inconsistent work
practices and out-of-date manuals. While staff are responsible for adhering to published policies, managers are responsible for making sure those policies are accurate and up-to-date.
How to measure downtime
Reducing equipment downtime starts with tracking it properly. Here are some of the most important metrics to keep an eye on.
Downtime rate
Downtime rate measures the percentage of time your equipment is unavailable during scheduled production. It covers all three types of downtime: planned, unplanned, and idle.
The formula looks like this:
Downtime Rate = (Total Downtime / Total Available Time) * 100
Why it matters: Downtime rate gives you a high-level snapshot of how often your machines are up and running. The lower the percentage, the better your equipment utilization. If your overall downtime rate drops in a given week or month, you'll want to drill into that number via your CMMS to see what's driving it.
MTTR (Mean Time to Repair)
This metric tracks the average time it takes to fix equipment after a failure. A lower MTTR
means your team is resolving issues quickly and efficiently. A rising MTTR, on the other hand,
might signal that something's broken. Maybe your team is having trouble sourcing parts, or they’re overworked.
Here's how to calculate it:
MTTR = (Total Maintenance Time / Total Number of Repairs)
Why it matters: MTTR helps identify bottlenecks in your response and recovery process. It’s
one of the most useful metrics for reducing downtime costs over time.
MTBF (Mean Time Between Failures)
MTBF measures the average run time between equipment failures. Higher MTBF values
generally indicate more reliable equipment and effective preventive maintenance practices.
Here's the formula:
MTBF = Total Operational Time / Number of Failures
Why it matters: If your MTBF is dropping, it could mean you’re relying too heavily on reactive
maintenance or dealing with aging equipment that needs attention.
OEE (Overall Equipment Effectiveness)
OEE provides a holistic view of how well your equipment is performing. It combines three factors:
- Availability (Is the machine running when it should?)
- Performance (Is it running at optimal speed?)
- Quality (Is it producing good output?)
This is the formula:
OEE = Availability * Performance * Quality
Why it matters: OEE is the gold standard for measuring a facility’s productivity. A low OEE score often points to hidden issues like frequent stops, slow cycles, or product defects. These all tie back to downtime.
The cost of equipment downtime
Sustained equipment downtime wreaks havoc in all sorts of ways. Financial costs are just the
tip of the iceberg.
Let’s break down the real-world costs of machine downtime:
Lost productivity
The most immediate and obvious cost of equipment downtime is lost output. When a production line stops, so does your ability to generate revenue. Even short bursts of unplanned downtime can snowball into incomplete customer orders. Multiply that across shifts, sites, or high-volume production runs, and the loss adds up fast.
Overtime costs
To make up for missed production targets, teams often have to work longer hours, sometimes
late into the night or over weekends. That extra time comes at a premium. Labor costs spike as companies are forced to pay out overtime or bring in contractors to close the gaps.
Replacement parts and rush orders
Equipment usually fails because one or more of its components breaks. That means teams
need to order replacement parts, often on short notice. And expedited shipping or emergency
sourcing tends to cost far more than standard procurement. What’s worse, if you don’t have
real-time visibility into your parts inventory, you may end up ordering duplicates or rushing the
wrong component.
Delayed orders or production runs
Customers aren't always willing to wait for your facility to get back up and running. If downtime causes them to miss a key shipment window, they might opt for a competitor next time. If it becomes a regular occurrence, you risk developing an unreliable reputation in your industry.
Damage to employee morale and efficiency
Constant firefighting wears teams down. When technicians are always in reactive mode, it becomes harder to focus on continuous improvement. Morale drops, burnout increases, and over time, skilled workers may leave for environments that prioritize preventive maintenance.
How to reduce equipment downtime
No maintenance team can eliminate downtime entirely. But just about every organization can reduce their downtime by putting systems in place that make breakdowns less frequent and less severe.
Here’s how leading MRO teams are minimizing downtime across their operations:
Use a CMMS to schedule and track maintenance
A modern CMMS is one of the most effective software tools for reducing downtime. It makes all
aspects of your maintenance operations far easier to manage.
A CMMS helps teams:
- Automate preventive maintenance (PM) schedules.
- Track work order completion and technician assignments.
- Monitor asset performance and failure trends over time.
- Document inspection history and service logs.
- Forecast and reduce unplanned machine downtime.
Standardize SOPs
Downtime often stems from inconsistent execution. Relying on different procedures and tribal knowledge is a recipe for consistent errors. SOPs ensure that every technician performs tasks
the same way every time.
Clear SOPs help:
- Reduce operator error and maintenance mistakes.
- Improve onboarding for new hires or temporary workers.
- Ensure compliance with safety and quality protocols.
- Build a repeatable system for inspections, troubleshooting, and repairs.
Your SOPs should be current and easy to access within your CMMS so they’re always
at your team’s fingertips.
Train technicians in root cause analysis (RCA)
Any time a piece of equipment goes down, teams need to figure out what went wrong so they
can prevent it from happening again. This process is known as root cause analysis (RCA). It’s a
problem-solving method that digs beneath the surface to uncover the real source of a failure.
Training technicians in RCA means they can:
- Identify underlying causes instead of treating surface-level symptoms.
- Prevent recurring breakdowns that eat up time and budget.
- Document lessons learned to improve future responses.
- Contribute to a continuous improvement mindset across the team.
Conduct regular inspections and audits
Routine inspections are the frontline defense against unexpected equipment downtime.
Inspections should be:
- Easy to perform and record using mobile tools or checklists
- Tied to usage, run hours, or seasonal cycles
- Supported by audits that track compliance and improvement areas
Maintain a well-organized parts inventory
Even if you diagnose the issue and assign the right technician, repairs can stall if you don’t have the parts. Poor inventory management is a silent contributor to extended idle time.
You can reduce delays by:
- Keeping critical spares in stock for your most-used assets
- Using a CMMS to track usage and set automated reorder points
- Auditing inventory monthly to remove obsolete or overstocked items
Downtime is costly. Here's how to take control.
Reducing downtime reduces costs. It's that simple.
The hard part is the execution. Shifting from a reactive to a proactive maintenance framework
requires the right blend of change management and modern tools.
A CMMS like MaintainX is a critical ingredient in this framework. With all of the equipment info you need at your fingertips, you can both minimize unplanned downtime and recover quickly when the unexpected hits.
Don't just take our word for it. See for yourself how four companies used MaintainX to lower their downtime costs.
FAQs
Planned (scheduled maintenance), unplanned (unexpected breakdowns), and idle (waiting on labor, parts, or instructions).
Preventive maintenance keeps assets in good condition and helps catch issues before they lead to unexpected downtime.
Yes. Predictive maintenance uses real-time data to flag potential failures so you can act before breakdowns happen.
Downtime directly reduces output, causes schedule delays, and often leads to costly workarounds or overtime labor.
Use the downtime rate formula (shown above) to get your downtime percentage. Tracking MTTR, MTBF, and OEE also provides a fuller picture.
See MaintainX in action