Maintaining batch records the traditional way requires manual effort. It also makes searching the records and gathering relevant information difficult when you need it. That’s why maintaining electronic batch records is more prevalent among modern life sciences manufacturers.
This post explains the meaning of electronic batch records in manufacturing, how to maintain batch records, and why you should maintain batch records electronically.
What Are Electronic Batch Records?
In manufacturing, electronic batch records (EBR) are electronic documentation that includes batch-wise details of production date, raw materials, machinery, personnel, and inspections.
The US Food and Drugs Administration (FDA) has several regulations you must comply with as a life sciences manufacturer, including but not limited to the following:
- 21 CFR Part 820.184: Discusses the rules for maintaining device history records (DHRs)
- 21 CFR Part 820.181: Discusses the need to comply with FDA Quality System Regulations (QSR)
- 21 CFR Part 820: Discusses current good manufacturing practice requirements
- 21 CFR 820.40: Document control requirements
- 21 CFR Part 11: Other regulatory requirements for handling documents electronically
Batch records are critical to assure stakeholders that the manufacturing process aligns with Good Manufacturing Processes (GMP).
However, logging and managing this data can be an administrative burden and prone to human error. That’s why modern life sciences manufacturers are turning to digital solutions.
A computerized maintenance management system (CMMS) is an excellent tool for maintaining electronic batch records. They’re easy to use, cloud-based, and allow you to quickly search and gather information when you need it.
“The batch record is a product quality-control document that collects all the data and information to make a regulated product. Batch records record materials, equipment, people, data, labels, and events during the production of products.”
POMS
Why You Should Maintain Batch Records Electronically
Life sciences manufacturers stand to benefit in the following ways by maintaining electronic batch records:
Helps Compliance Efforts
Electronic batch records’ primary benefit is that they make compliance more manageable. Regulatory agencies require life sciences companies to collect, organize, and report accurate information for each batch. Doing so in a way that makes audits easier helps you and the regulatory agencies, but it’s hard to do on a paper-based system. The ALCOA principle is essential here. The FDA’s ALCOA stands for attributable, legible, contemporaneously recorded, original copy, and accurate.
For example, suppose the Food and Drug Administration wants to audit a specific batch’s records for one of your products. When you produce hundreds of thousands of units each year, finding the batch records for a specific batch can be a hassle, which you can easily avoid by maintaining records digitally. Easy access to master batch records is invaluable during inspections and audits.
Improves Efficient Inventory Management
Batch records can tell you how much you produced during a given month, quarter, or year. The problem is that paper-based records require you to calculate the total production for each batch manually. Then, you’ll need to insert this data into your ERP (Enterprise Resource Planning) or inventory management tool. As you can imagine, the process is prone to human error.
On the other hand, electronic records are easy to search. In addition, you can integrate your batch recording tool with your ERP to relay data automatically. This means your inventory records are always up to date and less prone to human error. Not to mention that data integrity is ensured.
The improved traceability of information comes in handy during an audit. You’ll have a central database of documents, signatures, and other details, making it easier to provide auditors with the necessary information.
Reduces Human Error
Paper-based batch recording leaves room for various types of human errors. For example, in addition to incorrectly entering data, your team might misplace documents or forward them to an incorrect location. These errors can result in wasted time and effort and delay the audit process.
Also, batch manufacturing records are crucial when a team needs to provide evidence of process control systems and product quality management when a production process goes awry.
Electronic batch records stored in a cloud-based platform are accessible to all stakeholders. In addition, finding records is easy on a digital platform, which means you’ll save time that would have been spent on fixing errors and help auditors complete the audit process faster.
“Digital has the potential to break down traditional silos in biopharma and open the door for greater integration of data. This data, including product-quality feedback, can be integrated into research and development, sales, marketing, and other segments. Moreover, the ability to collaborate across functions makes it possible to share data across a product’s lifecycle.”
Deloitte
3 Steps to Start Maintaining Electronic Batch Records
Before you start maintaining batch records electronically, you need the following:
Reliable Data Collection Method
The data you collect and log into your electronic batch production records should be error free. Inaccurate data entry translates to skewed analysis and can cause a problem during an audit.
Before you start maintaining electronic batch records, establish a reliable data collection process. Providing clear directions about who should log and validate the data going into the batch records is critical to avoid data gaps, minimize human error, and execute in-process MES (manufacturing execution systems). This automation is often used in life sciences manufacturing and pharmaceutical companies to track and document the transformation of raw materials to finished goods.
Standard Operating Procedures
Standard operating procedures (SOPs) help build a solid data logging and analysis framework. SOPs act as work instruction guidelines for team members who need to log, report, and analyze data. This ensures all stakeholders have complete visibility over the data sources, enabling them to make crucial decisions faster.
Electronic Batch Recording Software
You need a batch recording tool that’s easy to use, cloud-based and offers built-in collaboration and audit trail features. These features make training your team easy and allow the team to access batch records wherever they are. In addition, if anyone on the team has questions about the batch record process, they can tag the relevant person within the software solution to get help in real time.
A CMMS like MaintainX is an excellent batch recording tool. It’s user-friendly, stores your data in the cloud, and offers built-in chat and electronic signature options for easy collaboration. You can also share pictures to provide context when requesting help from a team member. Also, tracking every step of the batch manufacturing process is essential to verify that your company upholds Current Good Manuring Processes (cGMP) best practices.
Consider integrating your current laboratory information management (LIM) systems and enterprise resource planning (ERP) tools with a CMMS to bring all your systems together and create an online single source of truth. In addition, a CMMS makes activating a unified namespace more efficient, especially with asset and parts inventories.
Maintain Electronic Batch Records with MaintainX
MaintainX is a CMMS that makes maintaining, organizing, and reporting batch records easier. The app stores your data in the cloud, allowing your teams access to the secure data from their mobile devices on the factory floor.
Moreover, MaintainX also comes in handy for other processes at your life sciences manufacturing facility. For example, you can use MaintainX procedure templates to ensure you check all the boxes needed for compliance or create a paperless checklist yourself to streamline your maintenance program workflows.
If this sounds interesting and you are ready for a digital transformation, try MaintainX to see how it adds value to your business processes.
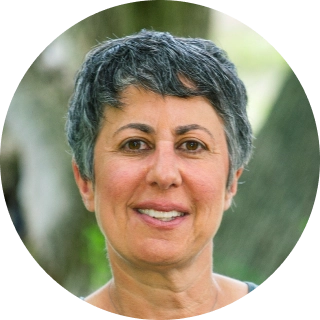
Caroline Eisner
Caroline Eisner is a writer and editor with experience across the profit and nonprofit sectors, government, education, and financial organizations. She has held leadership positions in K16 institutions and has led large-scale digital projects, interactive websites, and a business writing consultancy.
See MaintainX in action