Wrench Time Definition
Wrench time is a maintenance metric used to measure how much time maintenance technicians spend doing actual work assignments. Also known as tool time, it quantifies the time employees spend working with a “tool in hand.”
Wrench time represents the measurement of maintenance work completed while on the clock. When seeking to understand this metric, it’s helpful to understand what it is not.
Wrench time as a measurement of maintenance work hours does not include travel time, work order assessment, tools organization, or task communication. Neither idle time nor work breaks are included in wrench time calculations.
In general, the average wrench time for maintenance technicians is 35 percent. Say a technician works a 10-hour shift; that means he spends an average of 3.5 hours engaged in actual maintenance tasks throughout the day.
Experts emphasize that boosting wrench time to a “best practice” of 55 percent typically increases productivity by 57 percent. For example, a plant might go from fulfilling 500 work orders per month to 785 work orders per month without adding any new technicians to staff.
These days, the easiest method to measure Wrench Time is with a robust CMMS maintenance software.
The Difference between Internal and External Wrench Time
Internal wrench time refers to the amount of time that in-house maintenance technicians spend doing actual maintenance work. On the other hand, external wrench time is wrench time generated by third-party contractors hired to complete specialized tasks.
External wrench time can be affected by outsourcing maintenance procedures, engaging in clearance processes, and fulfilling regulatory requirements.
Wrench Time Controversy
With this in mind, it may surprise non-maintenance professionals to learn that wrench time is hotly debated within the maintenance community. Those in favor of measuring it argue that it’s the only way for maintenance managers to assess “true productivity” on the clock.
Alternatively, many technicians suggest that an over-emphasis on wrench time downplays the importance of other maintenance-related tasks. Therefore, maintenance managers who solely rely on it to measure productivity lack a complete picture of worker productivity.
So, is wrench time a good metric for measuring the performance of maintenance pros? We’ll list the oft-cited pros and cons below and let you decide.
Pros of Measuring Wrench Time
Many maintenance managers rely on wrench time statistics to measure the effectiveness of their maintenance planning and scheduling. Proponents insist that measuring measure it helps them:
- Match Technicians to Assignments: Wrench time can reveal which workers have an aptitude for specific tasks and which ones could be more useful elsewhere. Just analyze the average job competition times over a specified period e for increased insight into task suitability. Adjust assignment-worker pairings as needed.
- Increase Productivity: The higher a maintenance team’s combined wrench time, the more productive the team is. If workers are clocking insufficient numbers, managers can reevaluate standard operating procedures, work instructions, and operational systems for shortcomings to make informed procedural changes.
- Improve Budgeting: Tracking the actual time spent completing projects helps organizations strengthen asset management for accounting purposes. Management must monitor upkeep-related expenses to determine when to replace aging equipment.
- Reveal Time-Consuming Tasks: As with any endeavor, some things just take longer than others. Knowing how long it takes technicians to fulfill specific assignments leads to more effective maintenance planning and better equipment reliability.
- Validate Onboarding Initiatives: Besides matching individual technicians with ideal assignments, the metric can shed light on knowledge gaps. Once management recognizes that several technicians lack the necessary skill set, it can provide continued educational instruction to ensure everyone is on the same page.
Cons of Measuring Wrench Time
Despite the benefits above, there are some potential pitfalls to be aware of when tracking wrench time. It might not be a good idea to measure it because it could:
- Minimize the Importance of Other Activities: One significant drawback of wrench time is that it doesn’t factor in other essential maintenance operations. To effectively complete work orders, maintenance technicians must diagnose problems, identify their root causes, organize resources, and travel to both onsite and offsite locations.
- Discourage Team Members: It’s not uncommon for inexperienced maintenance managers to assume that low wrench times automatically mean team members are slacking. However, this assumption isn’t always valid. Jumping to such conclusions can foster distrust, resentment, and annoyance between O&M leaders and technicians.
- Generate a False Sense of Productivity: Again, if you don’t know how to interpret it correctly, the information may do more harm than good. For example, just because someone completes assignments quickly doesn’t mean they are doing them correctly or according to company standards. In addition, wrench time averages tend to under-value a maintenance team’s high-performers by mixing their times with under-performers.
Departments within an organization strive to prove productivity, increase efficiency, and justify budgetary requests. Plant maintenance departments are no exception.
However, wrench time doesn’t measure the primary goal of maintenance teams: decreasing downtime and increasing reliability. Despite these drawbacks, the metric remains an informative maintenance metric when used within the proper context.
How to Improve Wrench Time
The best way to improve your team’s average wrench time is to a) become aware of standard stumbling blocks and b) engage in effective planning.
Over-reliance on reactive maintenance, inefficient travel routes, inadequate Lockout Tagout procedures, and extended wait times for spare parts orders can all contribute to “false flags.” In other words, poor maintenance management can cause the illusion of unproductivity.
Below are a few tips to improve wrench time:
1. Develop SOPs for Recurring Assignments
Every maintenance manager should document and distribute standard operating procedures (SOPs) for recurring work orders. Clear SOP checklists make it easier for maintenance technicians to understand precisely how to complete work orders according to company standards.
In addition to providing step-by-step instructions on how to complete assignments, your SOPs can include illustrative workflows, equipment manuals, and tools lists. Use a work order software platform like MaintainX to streamline SOP management.
Click here to read more about how to develop effective SOPs.
2. Streamline Communication Systems
Re-evaluate your existing communication systems to ensure maintenance technicians can reach managers quickly and easily. Juggling several different communication methods—voicemails, emails, text messages, sticky notes—sometimes results in unnecessary idle time.
3. Map Facilities
Correctly map out facilities so maintenance technicians can quickly locate machines when filling work orders. This proactive work helps workers efficiently plan travel times when prioritizing incoming work orders and work requests.
4. Automate Inventory Management
Use work order software to set low-quantity alerts for stockroom supplies. Whenever a technician uses a part for a repair job, they can indicate doing so on their mobile device. This automatically signals the software to alert management when to order critical components. Having the right parts on hand goes a long way in reducing idle time and increasing wrench time.
Get MaintainX to Help Increase Wrench Time
Measuring wrench time can alert management to potential red flags that warrant investigation. However, the amount of time technicians spend with “tools in hands” will never be an accurate indicator of team productivity, asset reliability, or decreased downtime. Use MaintainX CMMS to automate work order scheduling, streamline team communication, and track the KPIs that most heavily impact operational bottom lines.
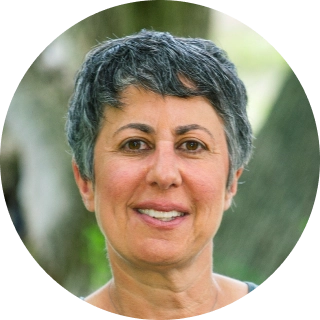
Caroline Eisner
Caroline Eisner is a writer and editor with experience across the profit and nonprofit sectors, government, education, and financial organizations. She has held leadership positions in K16 institutions and has led large-scale digital projects, interactive websites, and a business writing consultancy.
See MaintainX in action