Manufacturing is all about minimizing inefficiency and effectively allocating for efficiency. Wondering about the importance of productive efficiency? Consider that inefficiency can cost a manufacturer up to 30 percent of its revenue yearly.
In addition to lost money and time, inefficiency often leads to a lower quality overall product and an unhappy workforce.
So how can a manufacturer effectively use all of its available resources to maximize the production process? Read on to learn more about productive efficiency (PE), why it’s so important, and how to improve it.
Productive Efficiency (PE) Explained
So what is productive efficiency? It’s defined as a measurement manufacturers use to determine how long and how well a company can keep up with demand by comparing current and standard production rates. It can be applied to both short-run and long-run manufacturing.
A higher rate of production efficiency often leads to better use of resources. PE also can help a company establish advantages in competitive markets. High rates of production efficiency also can help manufacturers:
- Reduce resource usage and minimize waste, which is especially beneficial when supply chain issues or situations involve scarce resources. Of course, resources are more than just materials and include labor, energy, equipment, capital, and technology. The bottom line is that all these inputs need to be effectively managed through a workflow to optimize processes.
- Achieve better financial results with maximum production. Higher PE also translates to economic efficiency.
- Provide customers with a better overall experience (marginal benefit).
Calculating Production Efficiency
Production efficiency is calculated by dividing the standard output rate by the actual output rate and multiplying that figure by 100.
Production Efficiency = (Actual Output Rate/Standard Output Rate) x 100
The actual output rate is what a company can produce in a certain period of time. The standard output rate is the production goal that a company sets. Managers can use this key metric for improvement over time.
Furthermore, you can measure point-in-time production efficiency for manual and automated work to determine if your manufacturing company is working above or below capacity.
From an economic standpoint, productive efficiency connects macroeconomics to microeconomics. This helps companies with their efficiency in both big and small ways. Economists define macroeconomics as large-scale factors, while microeconomics are smaller-scale expenses. Econometrics is one of the most interesting aspects of PE, especially related to marginal cost, opportunity cost, and average total cost.
Production Possibility Frontier (PPF)
As noted above, managers can use this metric as a benchmark for improvement or a bigger-picture scenario, especially when companies need to consider more than one product or process.
The production possibility frontier—also referred to as the production possibility curve, boundary, or transformation curve—is often used to show combinations of goods produced with fixed resources and available technology. The curve consists of different points (Point A, Point B, Point C, Point D, Point E) depicting products, output rates, and available resources, and whether production technology or capacity needs to be added to meet these goals.
The PFF cost curve can also serve as a tool for leaders trying to find the right mix for their companies, both when it comes to domestic and international trade. For example, companies may determine whether they can handle additional units based on the PFF results.
On a related note, some companies also may deploy data envelopment analysis or examine the Farrell measure as a complementary tool to gauge economics.
How to Improve Productive Efficiency
As we’ve said, the higher your PE score, the better your manufacturing company is performing. But PE is a metric that should be measured and improved upon for a company to:
- Continually optimize resources,
- Improve economies of scale, and
- Continue to establish competitive advantages.
Here’s a look at how manufacturers can improve production efficiency.
Increase Productive Efficiency with Equipment Maintenance
We’ve discussed unexpected downtime on this blog and how it can completely derail production functions and profits. The good news is that when manufacturers focus on preventive maintenance, many unexpected equipment breakdowns and resulting problems can be largely avoided.
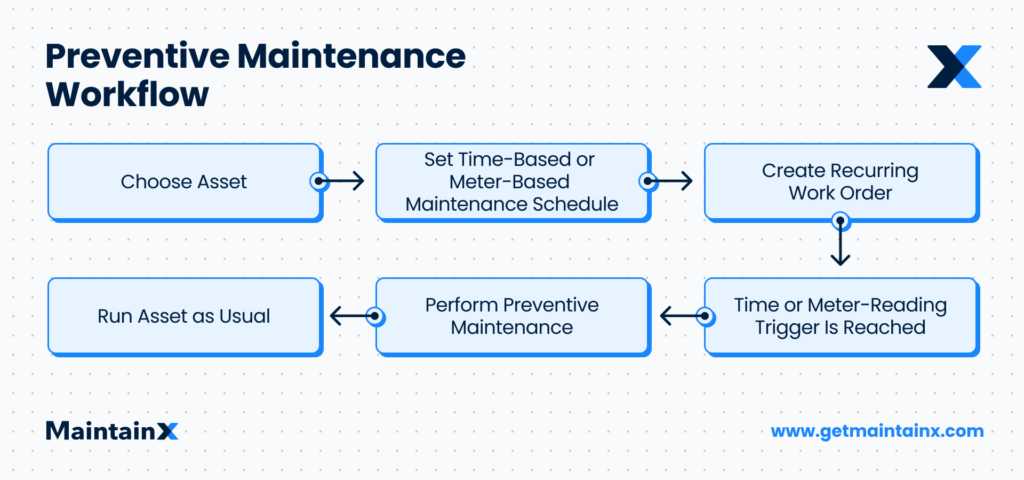
Just as drivers take their vehicles in for oil changes, tire rotations, and multi-point inspections, manufacturers can ensure that their equipment is on a robust preventative maintenance plan to avoid costly and time-consuming fixes that sap productivity.
Engage the Workforce
Remember, resources in manufacturing are more than just equipment and materials, but people too. But unfortunately, studies show that only about a quarter of shop-floor workers feel engaged with their duties while on the job.
Furthermore, manufacturing companies report an average turnover rate of around 20 percent. Therefore, a key to productivity is an engaged and satisfied workforce. Firms that make the proper investment in their people and work to grow their skills are likely to retain more employees and have a more engaged overall workforce.
Get Lean
Lean methodology is one way to reduce waste and improve efficiency on the shop floor—and it’s increasingly being embraced by more companies worldwide. Lean manufacturing technologies like Six Sigma, Kaizen events, and just-in-time manufacturing may take time to implement and get employee buy-in. But, the payoff in productivity advances has the potential to be significant.
Optimize the Manufacturing Plant Floor
From inventory management to the layout of the shop floor, companies can implement changes to the physical facility to streamline productivity and efficiencies. However, PE is more than just technical efficiency. It’s also about how a company stocks the correct amount of input material and spare parts to perform preventative maintenance.
From a plant layout perspective, studies show that arranging workers and machines into cells based on production steps—rather than spreading them throughout the facility—can optimize efficiency.
Use a CMMS to Increase Productive Efficiency
A robust computerized maintenance management system, or CMMS, is essential to drive these PE improvements. MaintainX’s CMMS system, for example, digitizes operations, creates checklists for preventative maintenance, simplifies overall maintenance, manages supply-chain disruptions, scores procedure completion, reports real-time data, and tracks purchase orders and vendors.
Ready to digitize your manufacturing maintenance processes on MaintainX? It’s free.
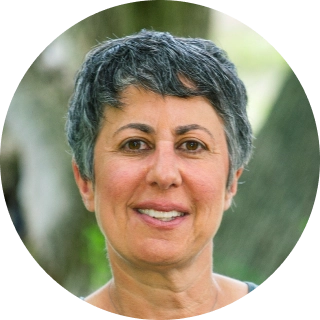
Caroline Eisner
Caroline Eisner is a writer and editor with experience across the profit and nonprofit sectors, government, education, and financial organizations. She has held leadership positions in K16 institutions and has led large-scale digital projects, interactive websites, and a business writing consultancy.
See MaintainX in action