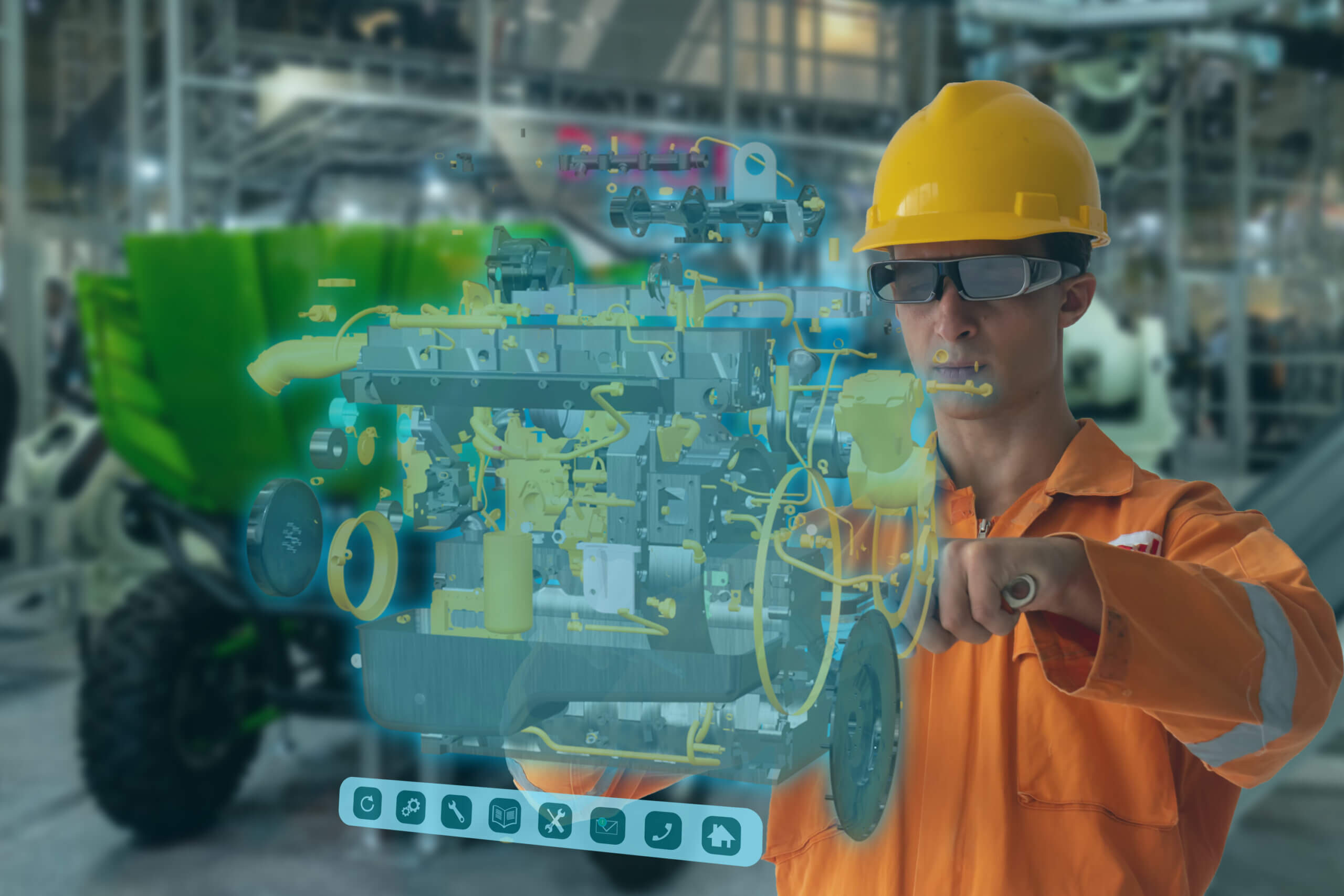
The MESA Model is a framework we use to study, understand, and categorize manufacturing processes. Developed by the Manufacturing Enterprise Solutions Associations (MESA), the model has gone through several incarnations. Over the years, business practitioners and academic professionals have used these various models to gain insight into what happens in manufacturing enterprises.
The latest Mesa Model is subtitled “a framework for smarter manufacturing.” As the name suggests, the model focuses on smart manufacturing. Specifically, it focuses on established manufacturing processes that innovations and modern technology have transformed.
The new MESA model comprises three concepts: lifecycles, cross-lifecycle threads, and enabling technologies. We'll explore what these concepts consist of shortly, but first, let's take a look at how the present mesa model came to be.
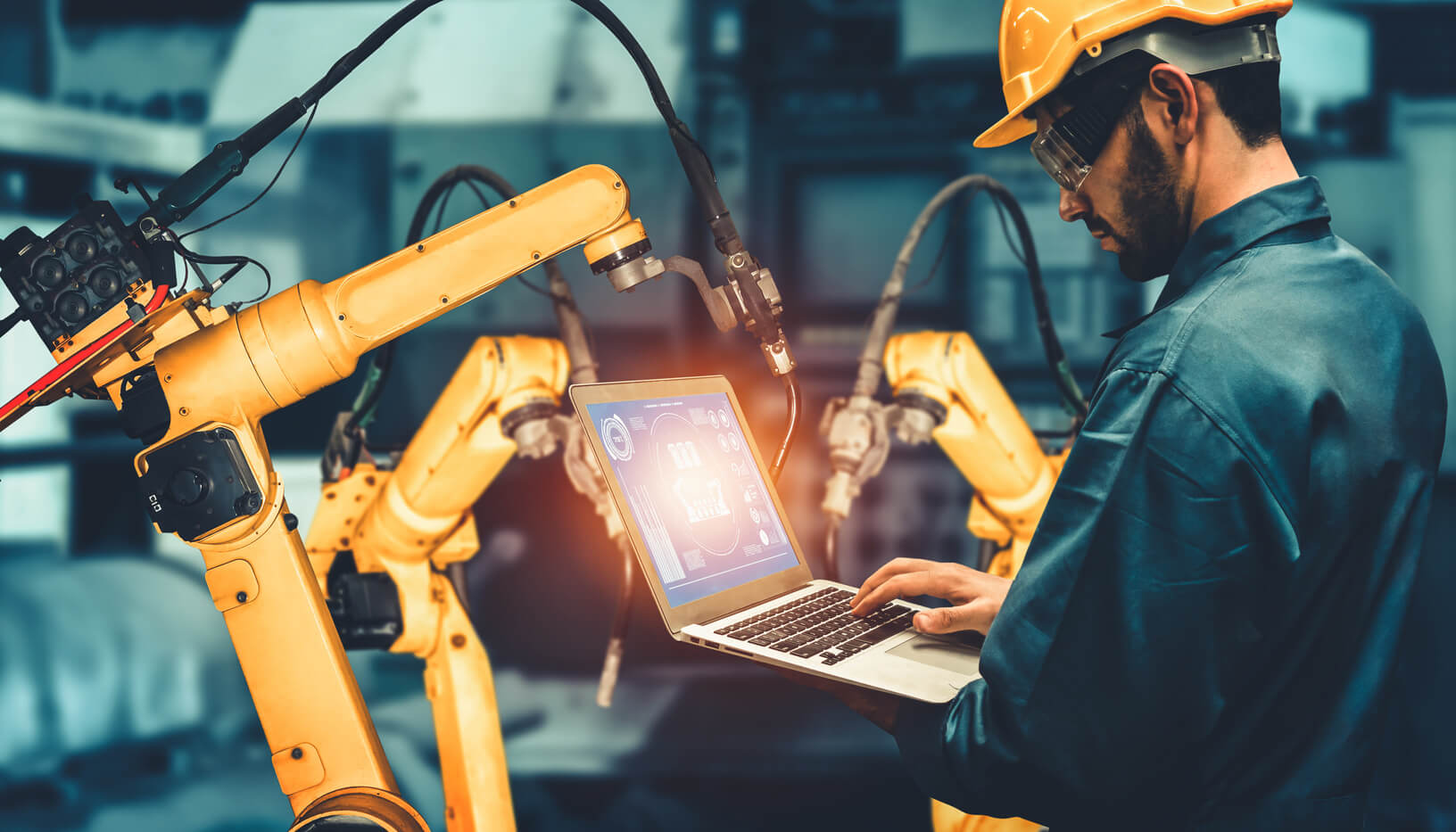
History of the Mesa Model
MESA International has created four models in total since 1996. These models are the MESA-11, CMES, Strategic Initiatives Model, and the 2022 Smart Manufacturing model. Let's look at each one.
MESA-11
This is where it all started. Mesa International published the Mesa-11 model in 1996. The model formally defined manufacturing execution systems according to 11 core functions. These core functions focused on how manufacturing systems relate to external enterprise systems.
The specific core functions are:
- Operations/Detailed Sequencing
- Resource allocation and status
- Dispatching production units
- Product tracking and genealogy
- Labor Management
- Process Management
- Quality Management
- Maintenance Management
- Data Collection and Acquisition
- Document Control
- Performance Analysis
Mesa then grouped these core functions into five areas:
- Supply Chain Management
- Enterprise Resource Management
- Product/Process Engineering
- Controls
- Sales and Service Management
C-MES
Next, in 2004, Mesa International unveiled the C-MES model. C-MES (Collaborative MES) focused on core operations and how those operations interact and integrate with business operations.
The model took into account issues such as supply chain optimization, asset optimization, and increased competition. The new business models incorporated by the model are:
- Controls such as Distributed Control Systems (DCS) and Programmable Logic Controllers (PLC)
- Financial and Performance-Focused Systems such as Enterprise Resource Planning (ERP) and Business Intelligence (BI) software
- Supply-Focused Systems such as Procurement and Supply Chain Planning (SCP)
- Customer-Focused Systems such as Customer Relationship Management (CRM) and service management platforms
- Product-Focused Systems such as Computer-Aided Design/Computer-Aided Manufacturing (CAD/CAM) and Product Lifecycle Management (PLM
- Compliance-Focused Systems such as Environmental Health and Safety
- Logistics Systems such as Transportation Management Systems (TMS) and Warehouse Management Systems (WMS)
Strategic Initiatives Model
The 2008 Strategic Initiatives Model expands focus even further. It included production and business operations and strategic initiatives like lean manufacturing, real-time enterprise, and return on investment
The Strategic Initiatives Model focuses on how enterprise-level operations relate to strategies and plant operations. Specifically, the model illustrates how strategies and enterprise-level operations play out on the actual plant floor. What are the top-level objectives and how do they affect day-to-day operations on the shop floor?
The Mesa strategic initiatives are:
- Asset Performance Management (APM)
- Return on Investment (ROI)
- Product Lifecycle Management (PLM)
- Lean Manufacturing
- Quality and Regulatory Compliance
- Real-time Enterprise
- Manufacturing Key Performance Indicators (KPIs) and Metrics
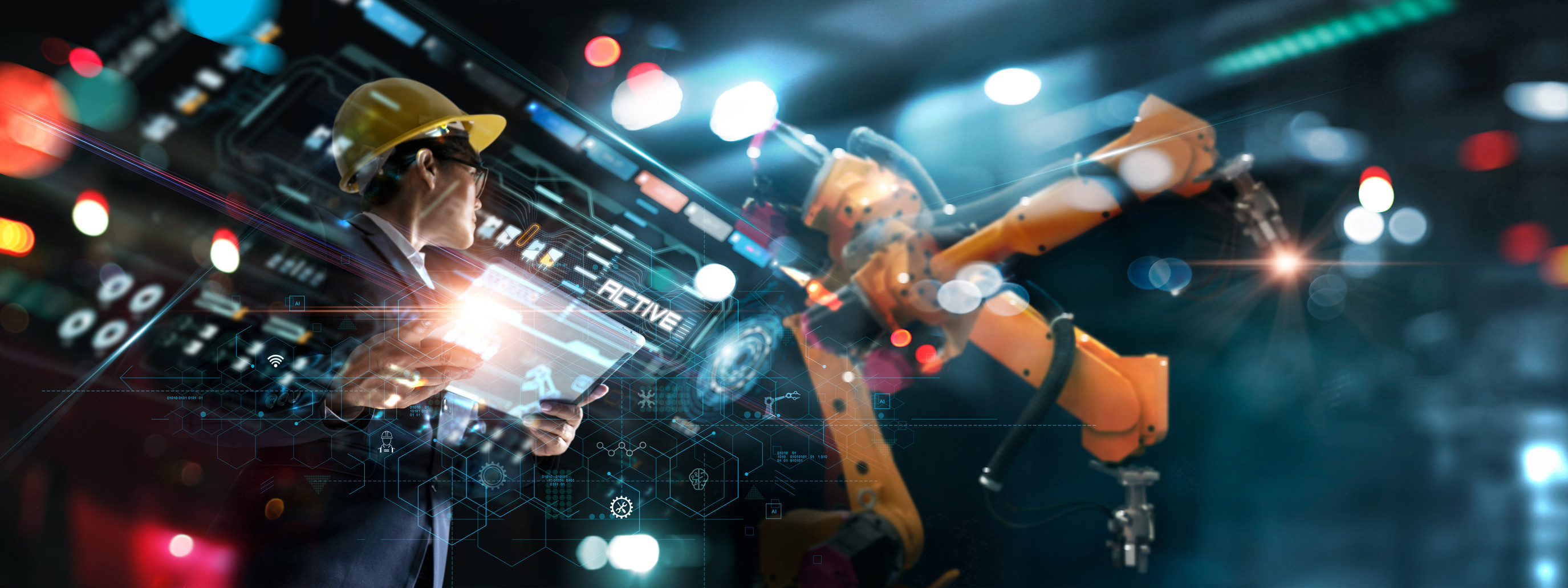
MESA Smart Manufacturing Model
The newest Mesa model was published in 2022. As stated earlier, the model integrates the three concepts of lifecycles, cross-lifecycle threads, and enablement technologies.
These concepts aim to separate manufacturing into manageable and easy-to-understand segments. This provides everyone using the model with a shared understanding. While separate, these concepts are interrelated and work together to provide insight into business processes. So let's take a closer look at these concepts now.
Mesa Smart Manufacturing Concepts
Lifecycles
The Lifecycles step defines smart manufacturing as it relates to your stakeholders and their objectives. It focuses on the stages of business operations that smart manufacturing techniques can optimize.
Optimization here refers to increasing connectivity and transparency and lays out aspects of the enterprise that smart manufacturing can transform. The Lifecycles are:
- Production
- Production Asset
- Product
- Supply Chain
- Workforce
- Order-to-Cash
Cross-Lifecycle Threads
This step involves lifecycles that interact with one another. For example, one business process might involve production and value chain lifecycles. Others may require data analysis of production assets and the workforce. This concept links lifecycles under the following umbrellas:
- Quality
- Compliance
- Energy
- Analytics
- Security
- Digital Twin / Thread
- Modeling / Simulation
Linking these functions helps ensure lifecycles operate cohesively. For example, staying compliant or achieving quality standards is easier to achieve when you have one unified view of quality across your operations.
Enablement Technologies
The third concept in the Mesa smart manufacturing model is enabling technologies. This refers to the technologies that make smart manufacturing possible and form part of the foundation of Industry 4.0.
These technologies can include concepts such as the blockchain, robotics, and the Industrial Internet of Things (IIOT). In addition, big data, artificial intelligence (AI), and machine learning (ML) are other concepts supporting enablement technologies.
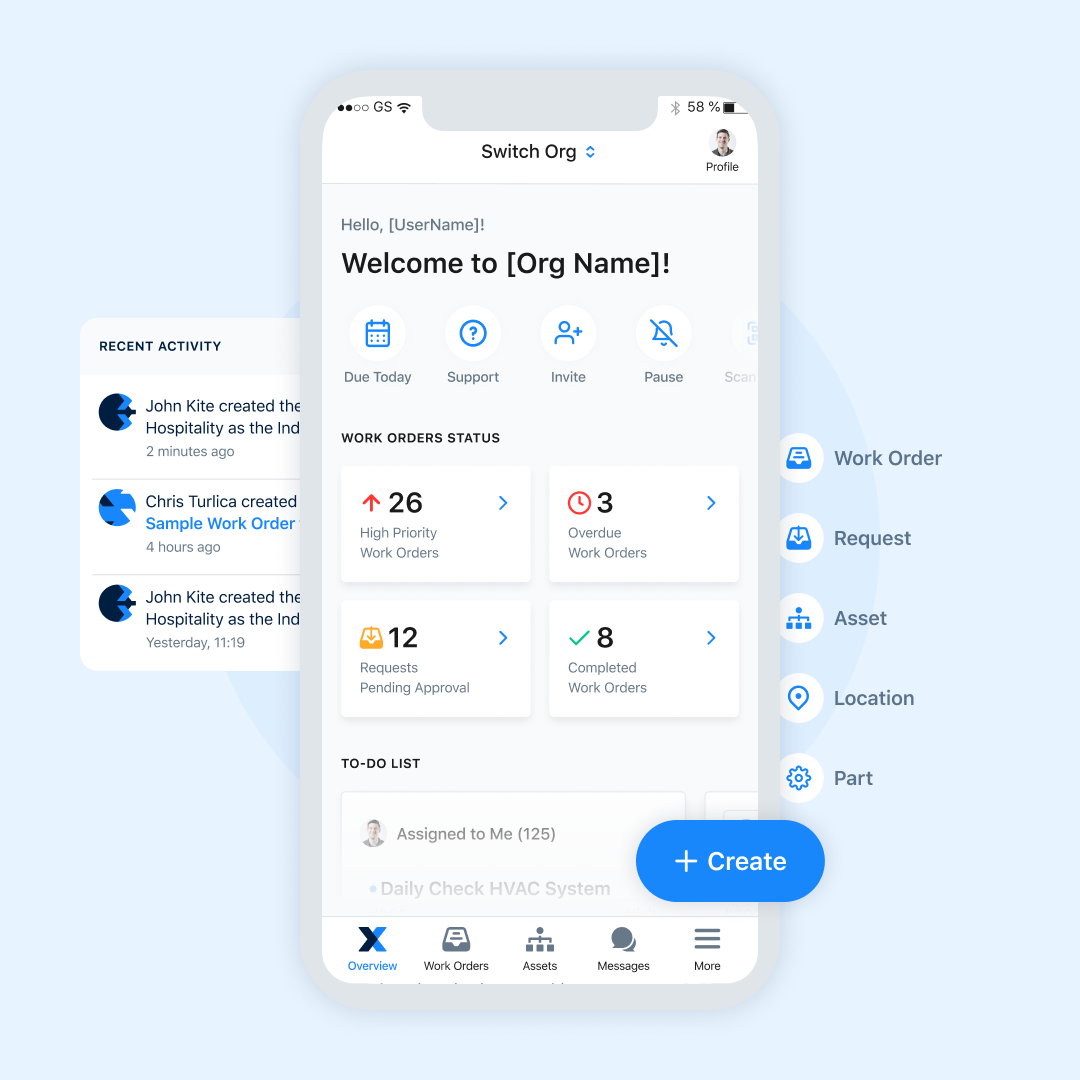
Get MaintainX to Implement your MESA Model
As detailed as the mesa model is, it's not exactly a strict guide. If it doesn't work for your needs entirely, you can adapt it to your own manufacturing needs.
Whether you choose to apply the cross-lifecycles concept to your operations or if you're currently using enabling technologies, you'll benefit from using a Computerized Maintenance Management System (CMMS) like MaintainX to organize your workflows.
We offer a wide range of features: a native-first mobile application, instant in-app chat, automated work orders, real-time notifications, and our Global Procedures Library. What's more, our robust Reporting features, and a range of filters, allow you to:
- Standardize your processes and SOPS
- Track performance and store real-time data on how the model is working
- Analyze performance data over time via our robust Reporting features
- Generate performance reports
Try MaintainX today!
FAQs
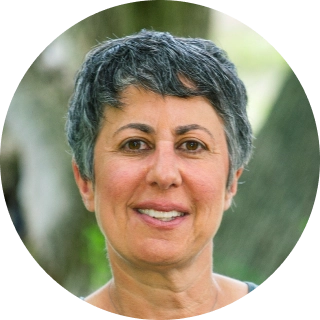
Caroline Eisner is a writer and editor with experience across the profit and nonprofit sectors, government, education, and financial organizations. She has held leadership positions in K16 institutions and has led large-scale digital projects, interactive websites, and a business writing consultancy.