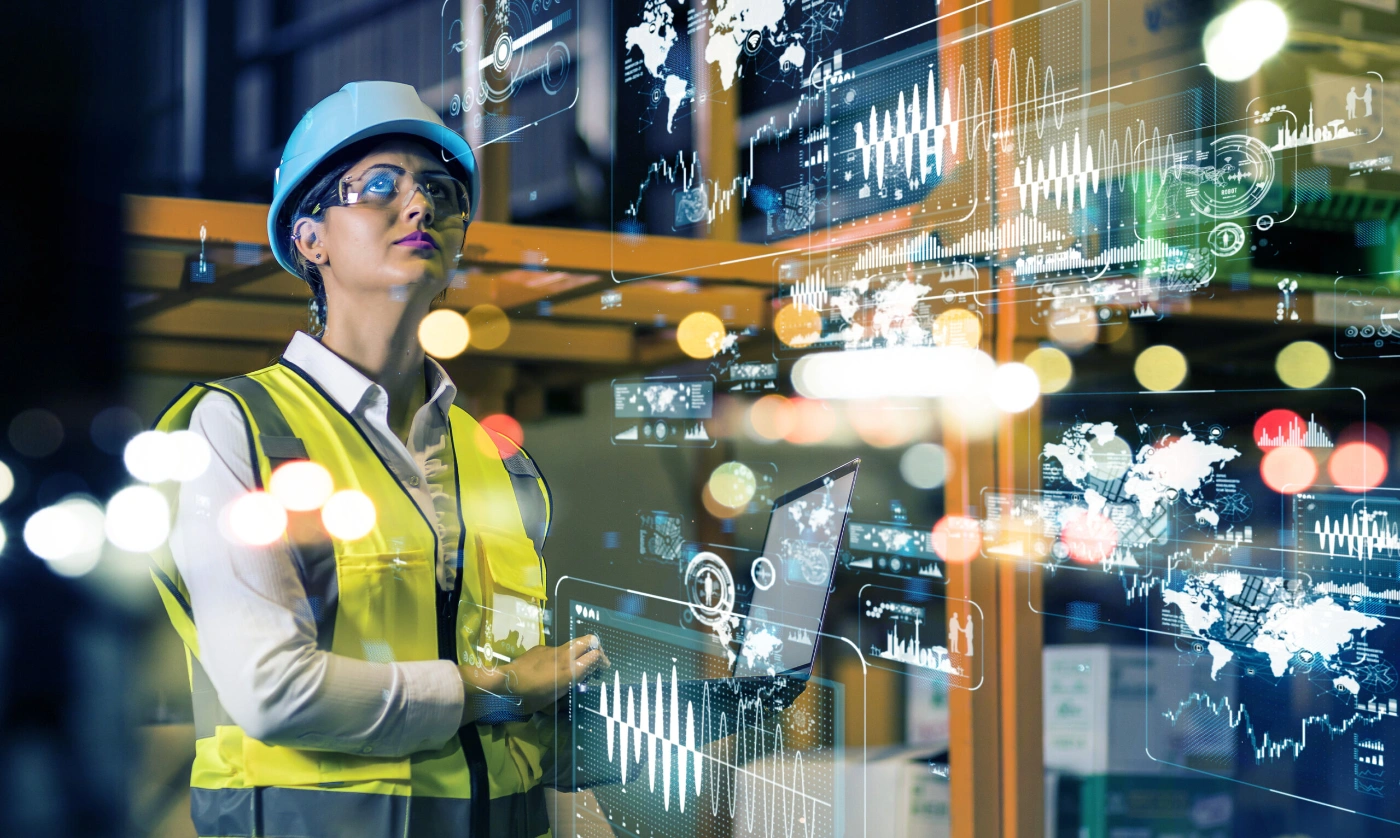
Enterprise Resource Planning (ERP) systems can initially seem at odds with lean manufacturing principles.
ERP focuses on using historical and forecast data to plan for the month or quarter. Lean practices, on the other hand, take a more flexible real-time approach and is is often reviewed day by day. ERP is all about creating goals and steering your business toward them. Lean production takes direction from what is happening on the shop floor and adjusts plans to match actual demand.
Although these two manufacturing strategies use different tactics, the end goal is the same. Both aim for a better use of resources, a more accurate understanding of production requirements, and, ultimately, increased customer satisfaction.
Imagine what will happen when you combine the manufacturing metrics from your ERP software with the power of lean production. The result is a robust overall plan that allows you the freedom and flexibility to make granular decisions as they arise.
Let’s take a closer look at the basics of each methodology. Below we show how you can combine the power of multiple systems to boost efficiency, quality, and accuracy.
“To drive efficiency and labor productivity for distributed fixed assets, optimizing preventive maintenance, reducing the number of maintenance trips, minimizing travel time, and sharing knowledge are key. New technologies. . . allow for significant changes in all these areas.”
McKinsey
Lean Manufacturing: The Bottom-Up Approach
Lean management is all about continuous improvement, eliminating waste, and putting customer demands at the center of your business. The goal, of course, is to deliver the highest quality experience for your customers. And, maybe you’ve heard this before, the path to success frequently starts at the other end: the factory floor.
Heavily influenced by “the Toyota Way” of manufacturing and Kaizen principles (meaning “good change”), lean manufacturing emphasizes continually reviewing business processes. This review will ensure that waste is minimized and systems are streamlined across the business.
Here, you need to view change as a constant. Always be on the lookout for ways to do three things:
- improve lead times
- deliver higher-quality finished products
- ensure raw materials enter the workflow only when needed (known as “just-in-time” manufacturing)
Lean manufacturing uses a range of visual tools (such as kanban), cyclical processes (like Plan, Do, Check, Act), and problem-solving approaches (like root cause analysis). These approaches help you make incremental improvements to workflows. This lets your manufacturing teams streamline operations based on feedback loops and constructive team input.
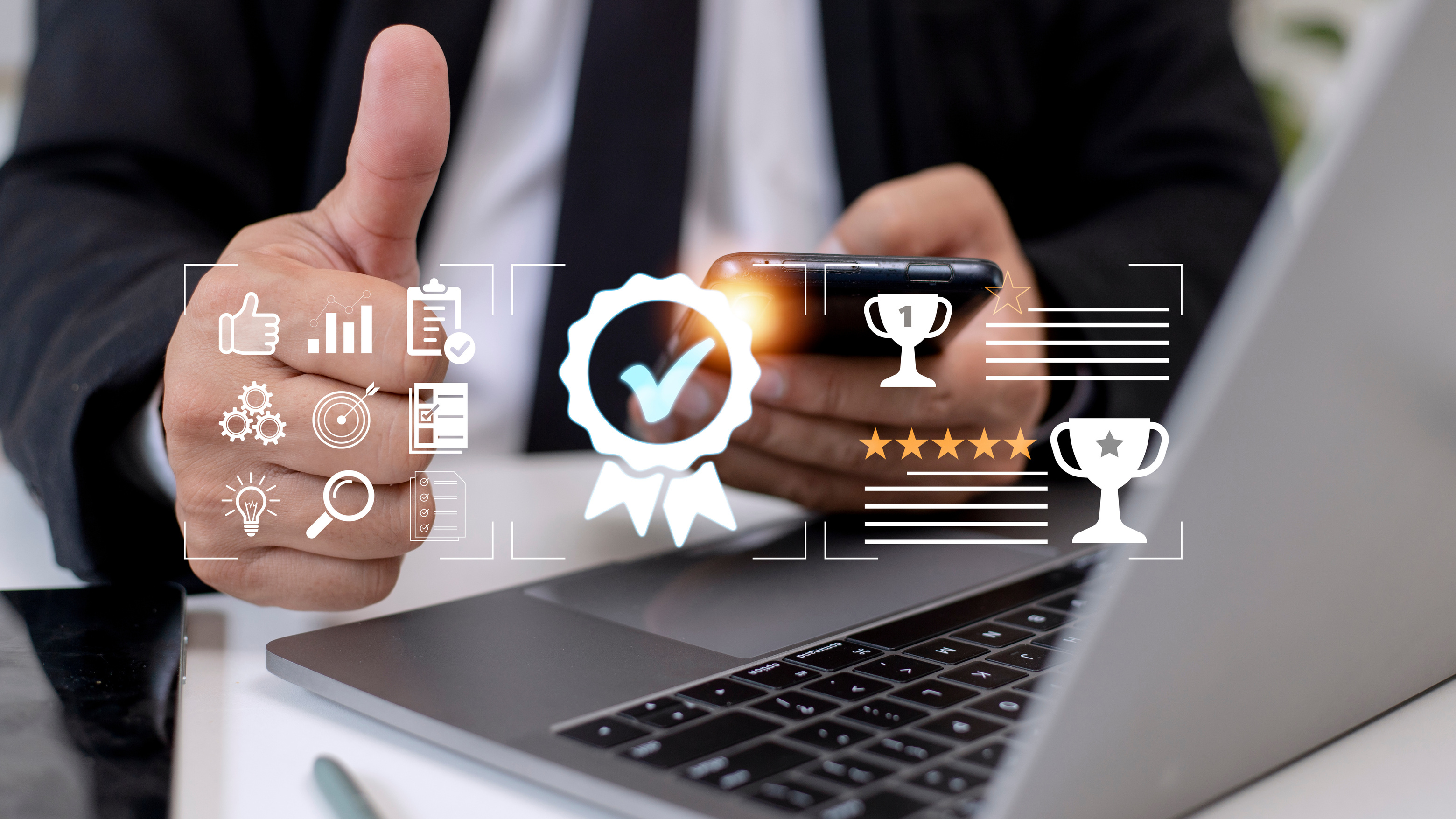
ERP Systems: The Top-Down Approach
ERP solutions like SAP and Microsoft Dynamics can help you better understand what is happening across your operation. Integrating with a CMMS like MaintainX will bring real-time work order data that shows trends and patterns across the board.
Enterprise resource planning–as the term suggests–can help you effectively allocate resources to keep things running smoothly. ERP functionality is typically customized per business, but most ERP implementations center around a handful of key business modules:
- Customer Relationship Management (CRM)
- Business Intelligence (BI)
- Supply Chain Management (SCM)
- Human Resources
- Inventory Levels
- Finance
- Quality
Supply chain management is often part of ERP. But, it often misses a critical part of the manufacturing process: maintenance and material requirements planning (MRP).
You can describe MRP as “ERP Lite.” It’s a software solution that can help you identify the supplies and materials you need and when. This kind of Information on raw materials, bills of materials, and inventory levels can help you:
- fulfill production planning goals,
- avoid costly unplanned downtime, and
- assist with forecasting.
MRP tends to focus on inventory management and materials without the holistic view of manufacturing operations that can come from an ERP system. In some cases, an MRP system will meet your company’s needs. But, an ERP tool is a safer option for more comprehensive management of your operation.
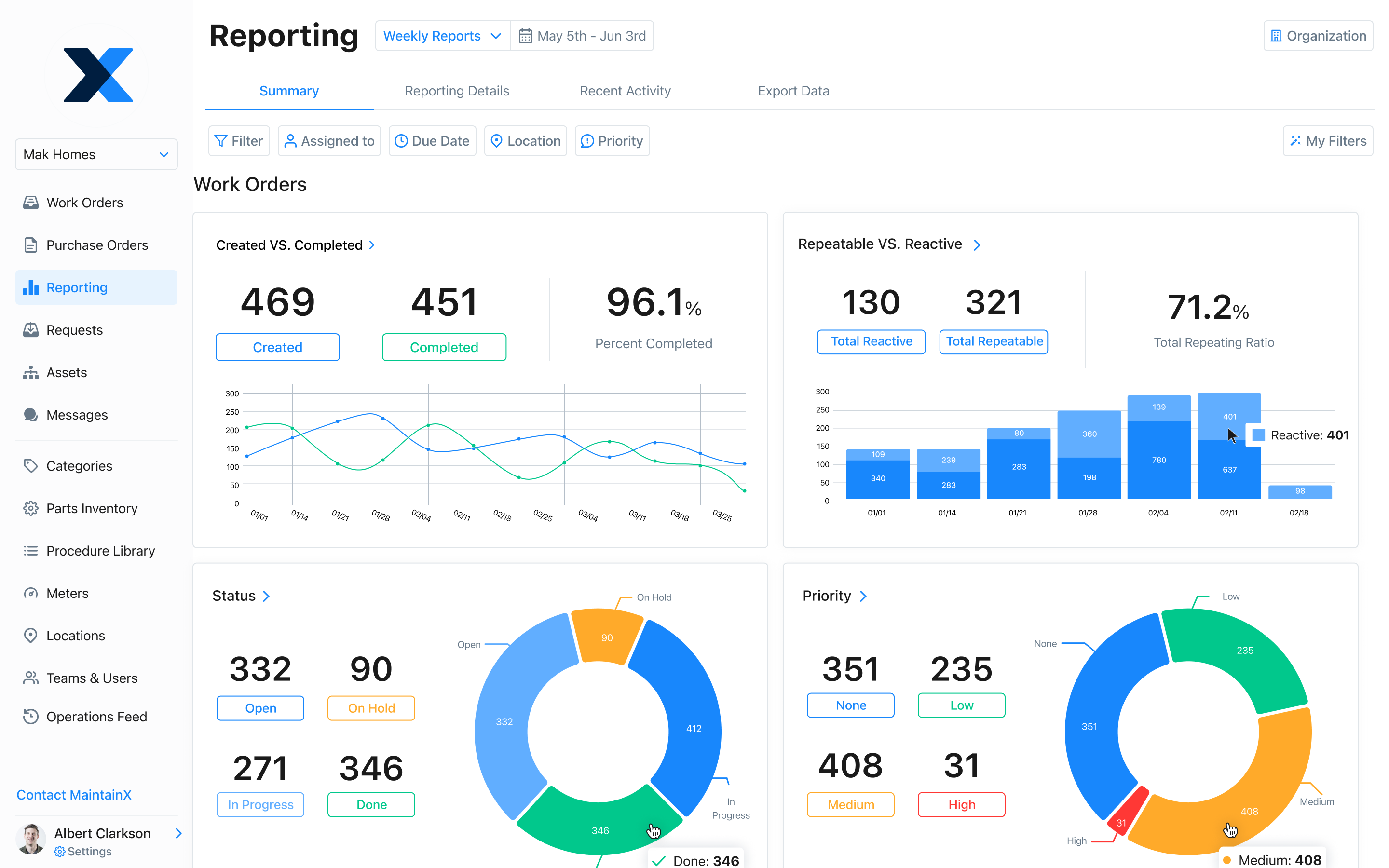
Lean, ERP, MRP, CMMS: All Together Now
The ultimate goal of using any of these management approaches is to better understand what’s happening across your company. Once you know what’s happening, can make informed decisions and avoid costly mistakes.
For example, a lack of historical data on customer purchasing trends can leave you in the dark when you want to replenish your stock.
Likewise, vague and undocumented operating procedures mean employees are left to try to produce the right results without knowing what constitutes a job well done.
The absence of a coordinated view of equipment maintenance requirements can force production teams to sit idle while machines are down or being repaired.
Confident decision-making is at the heart of every successful business, and having the right tools in place can help you plan and act–swiftly and decisively.
The Tools
- Lean manufacturing methodologies help management teams stay grounded and connected to workers and keep the focus on continuous improvement for the good of your business and customers.
- An ERP system will give you the data and the coordinated view to help drive process improvement in your organization.
- MRP software will help you ensure the right materials are available, the warehouse runs smoothly, and your business meets its DIFOT goals.
- Computerized maintenance management software (CMMS) gives you real-time maintenance data both on the factory floor and in the office. It then uses API integration to push data into your ERP. This means your maintenance teams have their own comprehensive portal. And the CMMS captures information tofeed it to your broader business planning system.
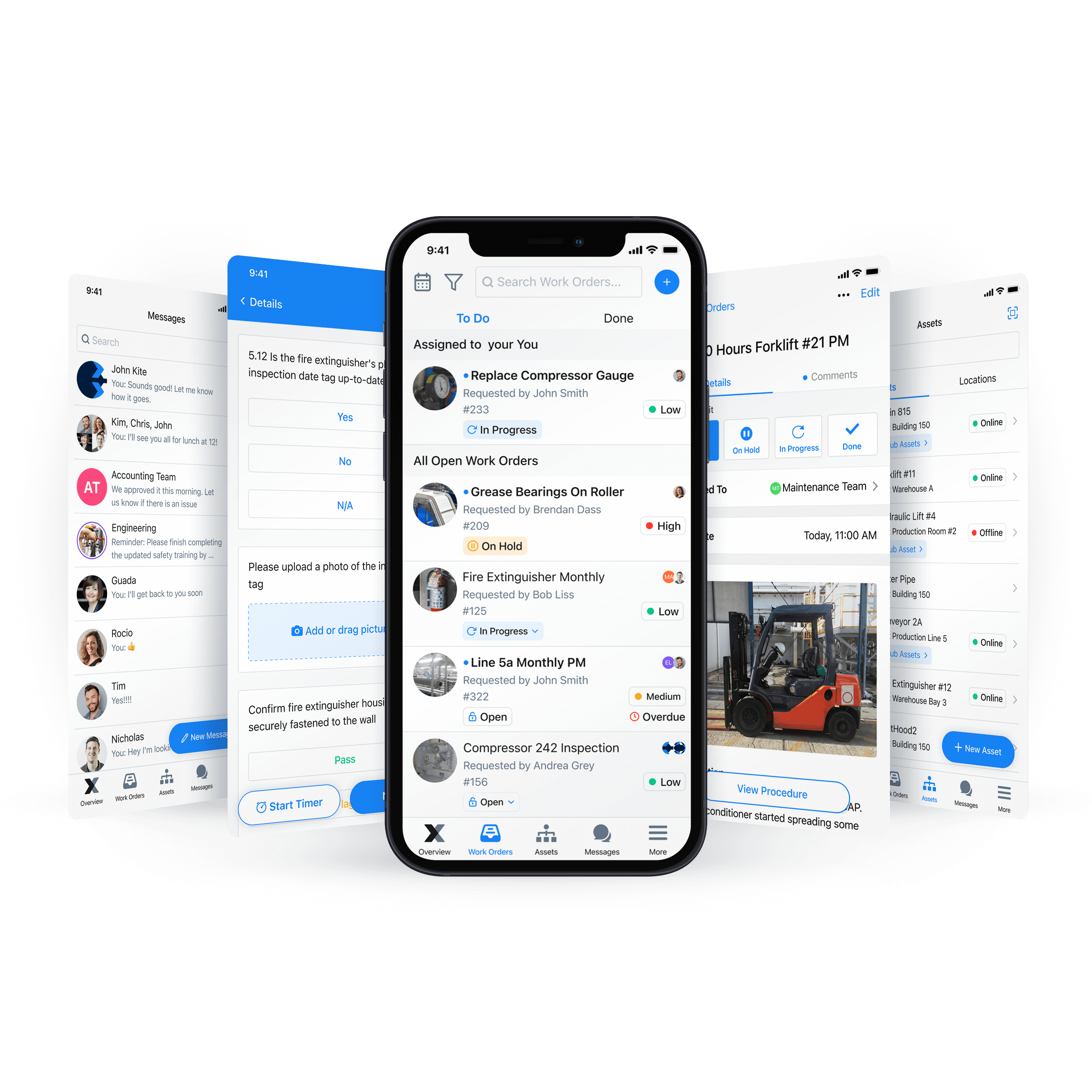
ERP + Lean: Add MaintainX to Supercharge Your Company
CMMS like MaintainX features robust KPI reporting, real-time parts and assets inventory, purchase orders, vendor information, and audit checklists. And that’s only half of it. Integrating a CMMS like MaintainX into your manufacturing plant can help you reduce downtime, increase efficiency, and continue growing your business. Contact our team today for more information on how MaintainX can form part of your ERP journey.
FAQs
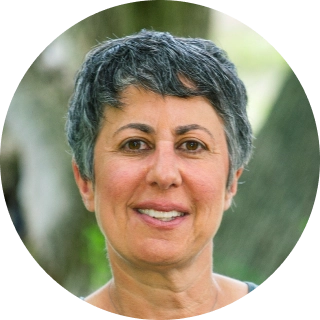
Caroline Eisner is a writer and editor with experience across the profit and nonprofit sectors, government, education, and financial organizations. She has held leadership positions in K16 institutions and has led large-scale digital projects, interactive websites, and a business writing consultancy.