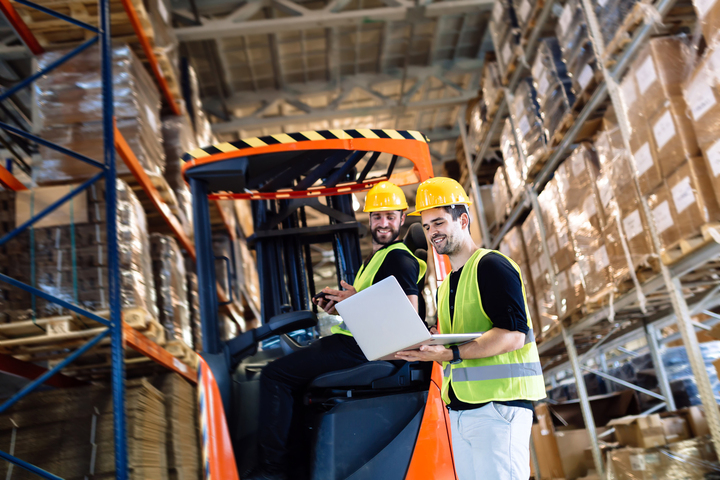
What Are Warehouse Logistics?
Warehouse logistics is an umbrella term for the people, goods, technology, processes, and systems that work together to keep your warehouse moving.
When items arrive in your receiving bay, move through various production stages, get placed into storage, or are shipped to your customers, warehouse logistics are in action.
While supply chain management is a broader term that encompasses things like sourcing and collaboration with suppliers, warehouse logistic solutions focus primarily on the inputs and outputs of your facility. These include:
- Physical inventory management
- Receiving and storage
- Picking and packing
- Dispatch or shipping
- Replenishment, reporting, and stocktake procedures
- Processing returns
- Staff training and development
- Reporting and analytics
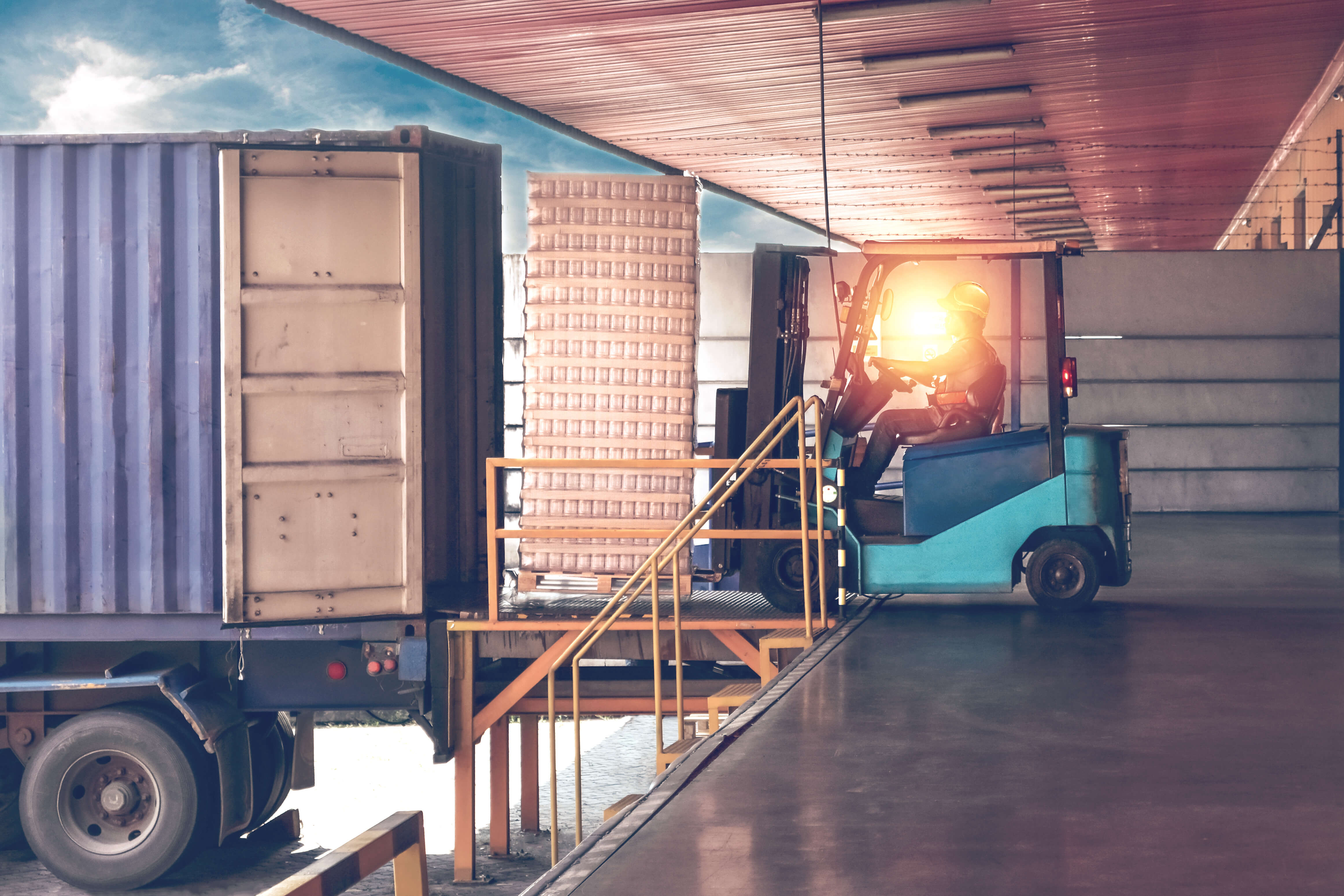
Efficient warehouse operations are a critical link in the supply chain. Focusing on improving warehouse logistics can substantially impact your bottom line. A Deloitte report notes, “79 percent of organizations with superior supply chain capabilities achieve revenue growth that is significantly above average.”
However, optimizing your warehouse management can be complex, with many moving parts and challenges to address.
Finding Opportunities to Optimize
Companies with their warehouse operations dialed in can gain a serious competitive advantage. However, while newer technologies such as automation and robotic warehousing can offer hefty productivity gains, getting the basics right is the first step to improving your logistics operations.
“Warehouse logistics is the heart of any supply chain operation, assimilating and dispatching goods to ensure availability and timely delivery. With more consumers turning to e-commerce, businesses of all sizes need to bolster the supply chain to handle the e-commerce business model.”
River Systems
Many potential solutions are small and easy to implement. They can be as simple as rearranging work areas to create more space, having clear paths to pick stock, or creating visual guides such as signage, pallet labeling, color coding, kanban boards, or floor markings.
Improving Efficiency with These Warehouse Management Tips
Running an organized warehouse makes logistics exponentially more manageable and efficient for your team. This, in turn, helps employees carry out tasks faster, reduces overall costs, increases safety, and helps you fulfill customer orders faster.
Here are four approaches to consider when you are looking to boost efficiency in your warehouse management system.
1. Tap into Lean Principles of Warehouse Logistics
Observing and analyzing how things flow in your warehouse and then getting to work to remove unnecessary waste is an ideal starting point. Using Lean methodologies and tools can help you follow the flow of goods and identify the bottlenecks at each stage.
Simple solutions such as creating a more efficient warehouse layout can shave hours off stock movement times and picking efficiency. Likewise, applying techniques such as SMED (single-minute exchange of die) to stock rotation can help you improve the management of your physical goods.
“A smart warehouse is a technology-driven warehouse that stores inventory or raw materials, using various solutions to monitor inventory and optimize warehouse processes. Unlike traditional warehouses, a smart warehouse leverages the latest technology to streamline internal processes.”
Newcastle
2. Consider the Just-in-time (JIT) Inventory Method
Just-in-time (JIT) inventory management is a lean manufacturing strategy that involves purchasing stock based on current conditions. The JIT model means having inventory filled just in time to meet orders, meaning your inventory moves quickly and doesn’t require as much warehouse space. This method also eliminates the risk of overordering.
Warehouse logistics make inventory management simple and efficient. Because they keep an immediate inventory count, you can make informed decisions about how many orders you can fulfill. In addition, many warehouse logistic software systems can alert you to the best time to reorder from suppliers, ensuring you always have the right amount of inventory according to projected sales.
In addition to less storage space requirements, using JIT also helps reduce the time for inventory counts–reduced stock levels on hand means faster counts, less time spent packing stock on shelves, and fewer storage locations required. All of this adds up to a stock holding that is easier for staff to manage daily.
3. Take Advantage of Warehouse Management Software
Warehouse management software (WMS) is designed to optimize the operational processes in your warehouse. This allows business leaders to gain more visibility into real-time inventory levels, the productivity of employees, and how various workflows function.
Peerless Research Group’s Materials Handling Technology Study reports that “56% of companies are currently using WMS in their operations, and 32% of companies that are either evaluating, purchasing or upgrading software in the next 24 months will be investing in WMS.”
Adopting a digital approach helps to streamline your warehouse by pinpointing any problems as they arise. Automated tracking and reporting functions also mean management teams can review and analyze trends, allowing for more accurate forecasting.
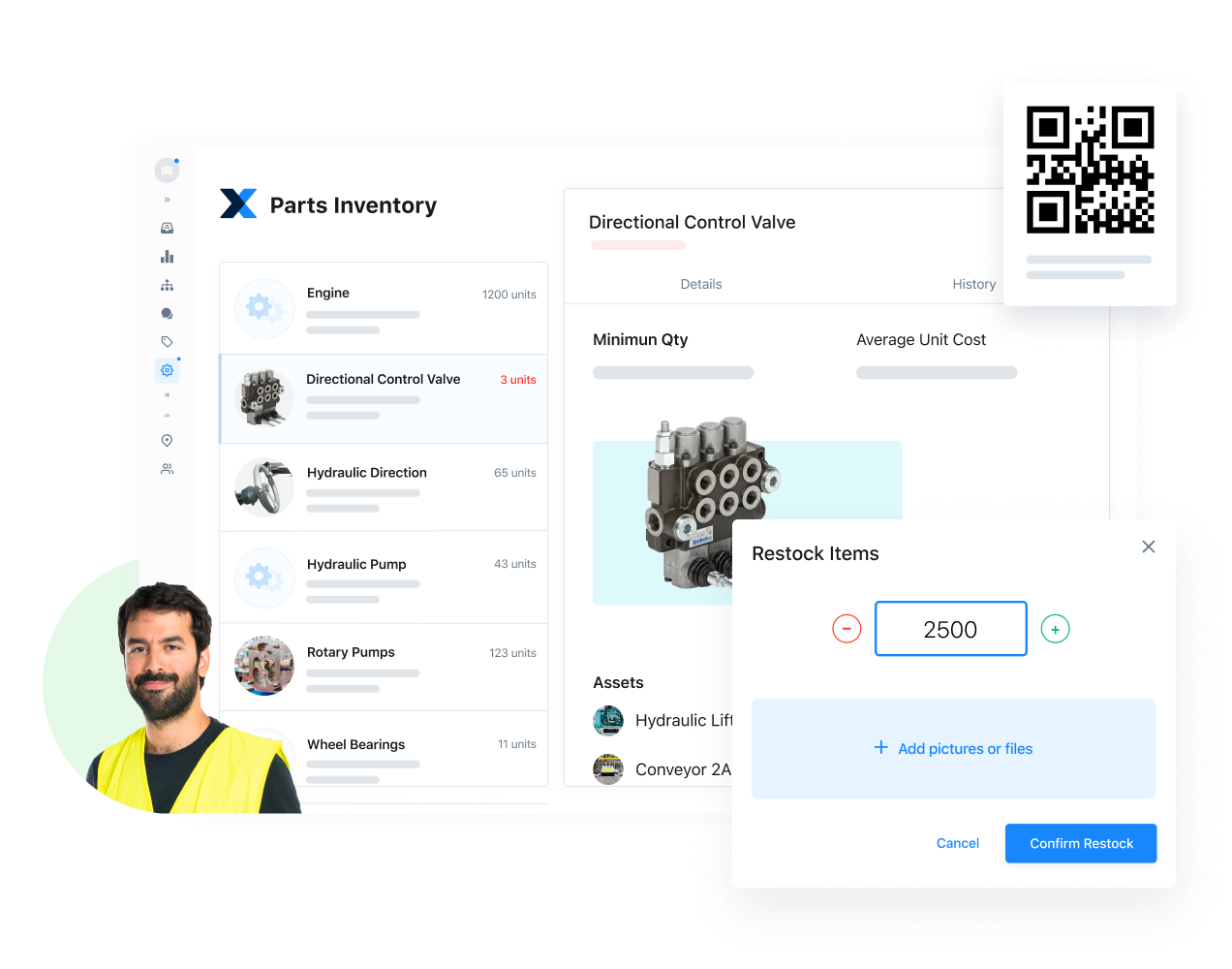
4. Stay Focused on Your Customers
Aside from efficiency gains and reduced operational costs, a warehouse functioning at an optimum level contributes to a better overall customer experience.
High productive efficiency often correlates with higher customer satisfaction and reduced customer returns. When warehouse and production workflows run smoothly, fewer mistakes are made, and orders are fulfilled more accurately.
Whether you are building an e-commerce empire, managing a distribution center, or adding value to raw materials, an organized warehouse is vital to keeping customers happy via on-time order fulfillment.
“The last mile of the supply chain is part of a much larger network of steps—from sourcing materials, refining them, and delivering them to manufacturers so they can build products to getting the products to distributors and customers. But getting orders to customers is far more complex than it sounds.”
Forbes
Leveraging CMMS and Industry 4.0 in Warehouse Logistics
The future of warehouse logistics is tied to the integration of CMMS and Industry 4.0. This synergy is no longer a luxury, but a necessity for competitiveness, bringing enhanced efficiency, transparency, and automation.
CMMS, empowered by Industry 4.0, serves as a strong predictive and preventive maintenance tool, minimizing downtime and boosting productivity. Real-time asset tracking and IoT-backed data collection help predict and address potential equipment failures, enhancing operational efficiency, extending equipment lifespan, and reducing maintenance costs.
Moreover, the blend of CMMS and Industry 4.0 is ushering in a new level of automation in warehouse logistics. AI and Machine Learning enable these systems to learn from past data, optimize operations, and make autonomous decisions, leading to an intelligent warehouse environment. This evolution brings numerous benefits, such as reduced errors and increased speed and productivity, setting the stage for more efficient, smarter warehouses of the future.
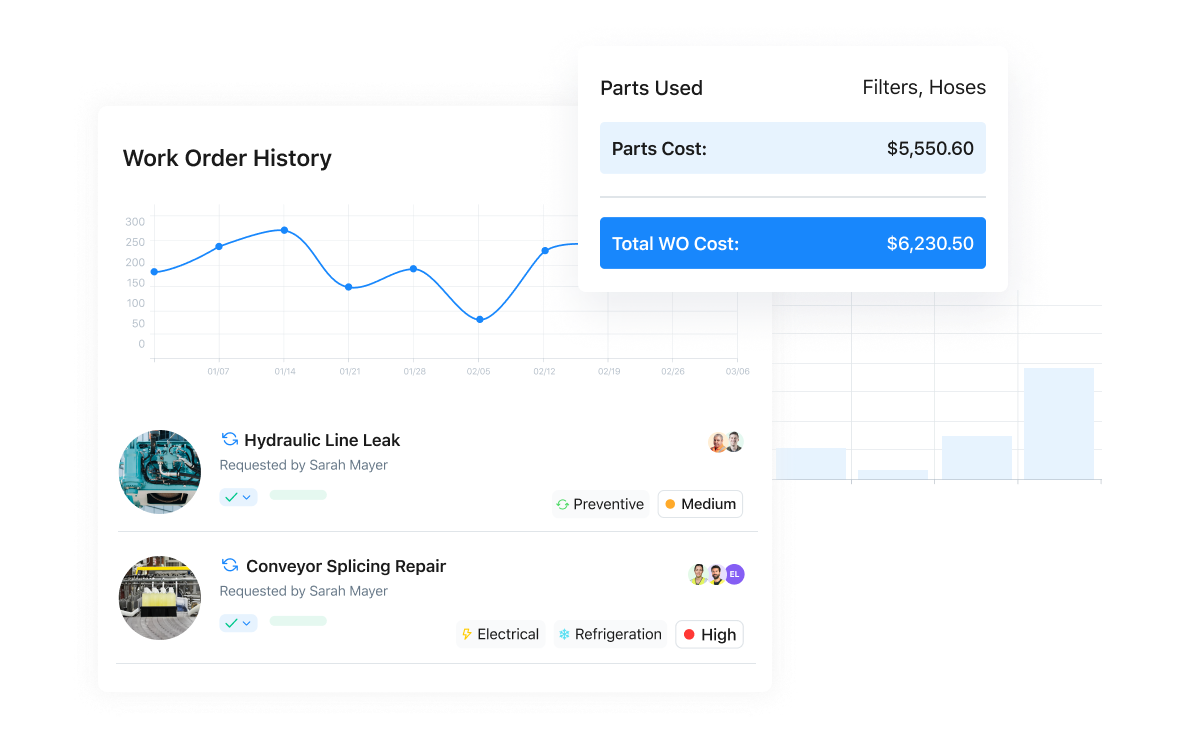
MaintainX Warehouse Management Software
Various software solutions have flooded the market recently, but not all are created equal. Securing the right warehouse and inventory management system can simplify stock management, minimize downtime, and assist with managing equipment maintenance issues, such as forklift breakdowns that threaten to blow out delivery times.
Book a free tour to see how MaintainX can help you grow your warehouse operations to the next level.
FAQs
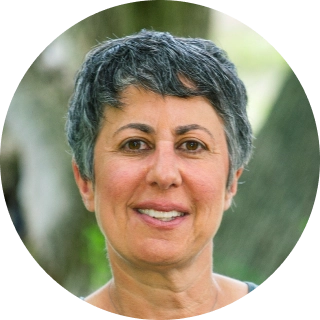
Caroline Eisner is a writer and editor with experience across the profit and nonprofit sectors, government, education, and financial organizations. She has held leadership positions in K16 institutions and has led large-scale digital projects, interactive websites, and a business writing consultancy.