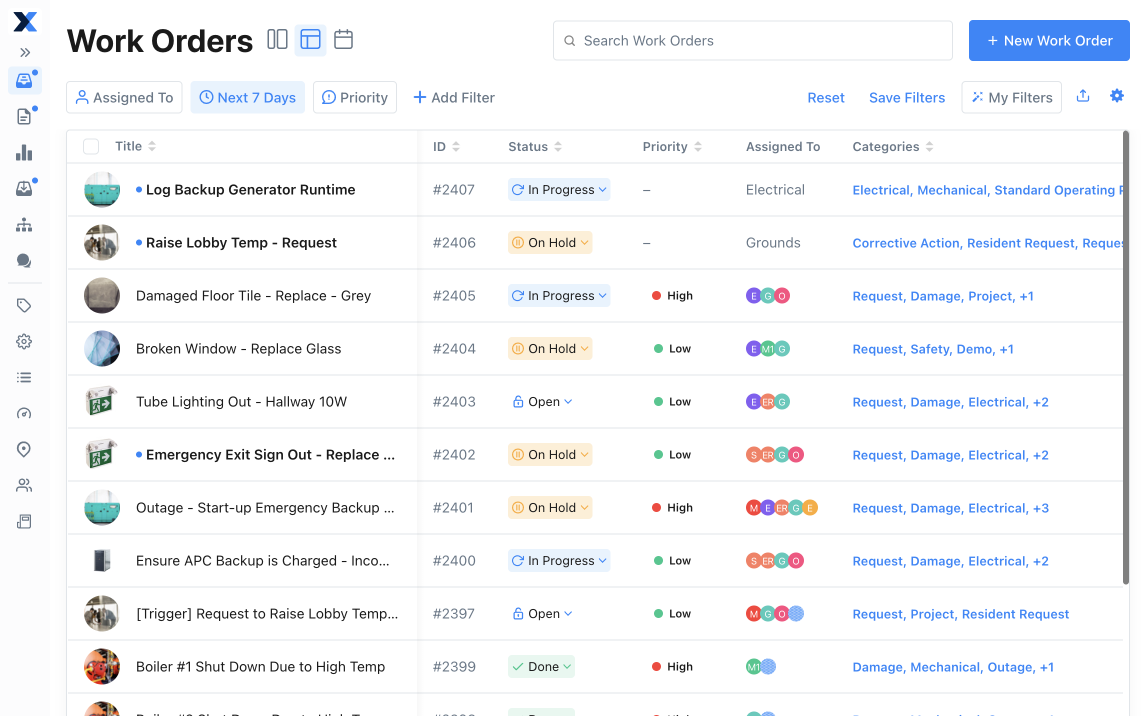
When your maintenance team struggles to keep up with a growing backlog of incomplete tasks, it can quickly lead to equipment downtime and rising costs. This is the reality when work orders aren't properly tracked. However, with effective work order tracking, your team can prioritize tasks, address urgent repairs faster, and streamline daily operations. Whether you’re just starting with work order management or fine-tuning your current processes, tracking work orders makes it easier to complete maintenance tasks on time and keeps your teams' priorities aligned.
This guide explains how a modern computerized maintenance management system (CMMS) system makes tracking work orders easier, increases efficiency, and improves visibility for maintenance activities. With the right CMMS solution, you can tighten up workflows, monitor work orders, and improve performance, all while maintaining compliance and lowering asset maintenance costs.
What is work order tracking?
Picture a technician trying to fix a broken HVAC system. The work order they received is missing a critical detail—the model number for a filter they're trying to replace. Now, they have to pause the job, call the office for clarification, and wait for the model number to continue. For businesses without proper tracking, this type of delay is fairly common.
Work order tracking is the process of monitoring and managing maintenance tasks from start to finish. It provides the necessary details—such as the air filter model number and task description—so they are easily accessible in one place. A good work order tracking system keeps operations running smoothly by centralizing information.
Why work order tracking software is crucial for maintenance
Imagine trying to track down an old work order during an audit, only to spend hours sifting through stacks of paper stored in boxes. Many managers and administrators have faced this kind of situation before switching to a digital work order tracking solution. It’s not unheard of for someone to spend an entire day locating the correct document for the fire marshal. But with a modern digital work order system, you can find what you need in minutes.
The right order-tracking software simplifies the process by centralizing everything on one platform, providing real-time updates, and improving communication across teams. With it, you can be confident that maintenance tasks are accurately tracked, completed on time, and easy to locate when needed. Here’s how work order tracking software can transform your maintenance operations:
Increase efficiency and accuracy
Stop wasting time on paperwork and manual tracking, and let your team focus on what really matters. Work order tracking software greatly reduces the risk of manual errors and streamlines maintenance practices, leading to fewer delays and better use of resources. With your digital standard operating procedures in one place, you can easily assign tasks, follow progress, and avoid overlooking critical steps. Put those procedures into action with powerful digital tools that automate workflows, reducing the time spent on administrative tasks.
Receive important updates in real-time
When an operator receives an urgent notification that a conveyor belt in your production facility is overheating, they can send a real-time update through the work order tracking system. This lets you quickly assign a technician to investigate the issue. An efficient work order management system with tracking tools lets you monitor equipment conditions in real-time and task statuses as they occur. Your team can respond quickly to any situation and make any necessary adjustments on the spot. Real-time visibility helps you make informed decisions and prevents minor issues from growing. By staying informed, your maintenance teams can work proactively and keep projects on track.
Enable swift communication & collaboration
Work order tracking software improves team communication by combining all maintenance tasks on one centralized platform. When managers and technicians can view the same information and message each other directly, they can work together more effectively and reduce miscommunication. The best platforms include built-in messaging tools and notification options that let everyone stay informed, helping to prevent delays and keeping maintenance teams aligned.
Key features of a work order tracking system
A powerful work order tracking platform offers many valuable tools to help keep maintenance operations moving along smoothly. From digital work order creation to real-time reporting, these tools let you see what's happening at all times and improve efficiency across the board. These five key features help make a work order system an effective asset to your maintenance efforts:
Digital work orders
Digital work orders make creating, assigning, and tracking maintenance activities easy with just a few clicks. They eliminate the need for paper forms, reduce manual input, and are accessible from anywhere. When you digitize forms like maintenance requests and work orders, these benefits will help your team stay productive and focused:
- Automatically create a maintenance request.
- Reduce the chance of mistakes.
- Improve response times for your team.
- Keep operations running efficiently.
- Streamline the tracking of tasks and progress.
Reporting and analytics
A good work order software suite provides reporting and analytics tools that monitor both equipment performance and team efficiency, helping you make data-driven decisions, such as adjusting preventive maintenance schedules or reallocating resources to high-priority tasks. You can empower your team to make smarter maintenance decisions with detailed breakdowns of completed tasks, downtime, and resource usage. These insights can help you:
- Track key performance indicators (KPIs) for team evaluations.
- Identify patterns and locate areas for improvement.
- Schedule preventive maintenance and inspections at optimal times.
- Optimize maintenance processes to make the best use of resources.
- Reduce unnecessary costs with better planning.
- Parts tracking (i.e., what's in stock)
Work order templates
Work order templates standardize the work order creation process, saving time and keeping maintenance operations consistent across departments. By using templates, you can quickly generate work orders without missing important details. Here are other benefits of using work order templates:
- Consistent formatting for all work orders
- Reduced time spent on repetitive tasks
- Minimizes the risk of overlooking crucial information.
- Easily customizable to create templates for your specific maintenance needs.
Work order history
Maintaining a detailed work order history is crucial to the work order management process, letting you track progress and stay compliant with industry standards. With a complete maintenance history, you can document processes to meet regulatory requirements. A work order tracking system allows you to:
- Keep a comprehensive record of completed tasks.
- Compare the frequency of preventive maintenance versus corrective maintenance work orders.
- Track recurring issues and spot patterns over time.
- Provide documentation for audits and compliance checks.
- Identify areas for improvement in your maintenance strategy.
- Track parts and inventory for asset management efforts.
One MaintainX client, Future Foam, struggled with missing work orders and had no historical data to track equipment disruptions. This led to significant periods of heavy downtime. With the help of MaintainX, the company adopted a data-driven approach that turned its operations around. — “MaintainX was the direction we needed to go. We’ve never looked back.”
Native mobile app
A mobile work order management system puts power in the hands of facility managers and maintenance teams alike. A native mobile app allows you to access work orders and update real-time progress from any location. This flexibility helps maintenance teams stay connected and responsive no matter where they are. With mobile access, you can:
- Quickly reprioritize corrective and preventive maintenance work orders.
- Monitor progress in real time.
- Provide updates and attach photos from anywhere.
- Improve communication across the maintenance department.
- Track and complete work orders on the go.
How to track work orders effectively with MaintainX
Effectively tracking work orders takes the right tools and strategies. With MaintainX, you can streamline processes from start to finish, making it easier to manage tasks, communicate with teams, and monitor real-time progress.
One case study shows how SanTan Brewing Co. closed over 450 work orders after just six months of using MaintainX. They've optimized work order processes across several locations using the platform. — “MaintainX was #1,” Soltis said. “When I landed on the MaintainX free trial, honestly, it was love at first sight for me.”
Here are five key ways that MaintainX can help your business optimize its work order flow:
Create digital work orders with ease
With MaintainX, creating digital work orders is fast and simple. You can quickly assign tasks to the right people and include all necessary details, such as priority levels, due dates, and SOPs. Digital work orders help ensure your team doesn’t miss anything and that they focus on what’s important. Benefits include:
- Instant task creation with full details.
- Auto-assign tasks to the right team members.
- Real-time updates for task progress and completion.
- Standardize work order creation with customizable templates.
- Include asset details, location, priority levels, and deadlines for clear communication.
- Use digital forms to attach photos and detailed information.
- Schedule preventive maintenance tasks in advance to reduce downtime.
Assign your work orders to the right staff
MaintainX simplifies the task of assigning work orders. Maintenance managers can easily delegate tasks to the right team members based on skill level, availability, or job priority. The platform gives you confidence that the right people are handling the right jobs. Other benefits include:
- Real-time notifications for assigned tasks.
- Automatic assignment based on predefined criteria.
- Improved task management for maintenance managers.
- Reduced risk of tasks slipping through the cracks.
Execute and immediately monitor work order progress
Technicians can efficiently execute work orders using the MaintainX mobile app, providing real-time updates to ensure accuracy. They can log updates, attach photos, and mark tasks as complete directly from the field, helping keep work organized and reducing downtime.
For managers and executives, MaintainX provides real-time visibility into the effectiveness and efficiency of maintenance processes, providing confidence that your team will complete work orders on time. Automated notifications and updates keep everyone in the loop, allowing for better oversight and quicker decision-making.
Learn from your work order data
MaintainX offers powerful reporting and analytics capabilities to accurately evaluate work order data and improve processes. EHS (Environment, Health and Safety) professionals and executives can benefit from real-time insights into task performance, equipment usage, and downtime, allowing for more informed decision-making. With detailed reports, you can:
- Identify trends and recurring issues.
- Improve resource allocation and preventive maintenance schedules.
- Track technician productivity with performance metrics.
- Forecast future maintenance needs based on historical data.
- Continuously improve overall maintenance strategies for long-term success.
Maintain compliance every step of the way
With MaintainX, your team follows regulations and industry standards by keeping detailed historical maintenance data. With this documentation, EHS professionals can track every step of the maintenance process, helping everyone abide by safety protocols. The platform provides:
- Complete audit trails for regulatory reviews.
- Instant access to work order history for inspections.
- Documented proof of compliance with safety standards.
- Streamlined reporting for easier recordkeeping.
With MaintainX, work order tracking is a game-changer for your maintenance operations. Whether you're tackling preventive maintenance, managing urgent repairs, or keeping your assets running smoothly, our streamlined approach will improve your team's efficiency. Say goodbye to paper trails, miscommunications, and unnecessary downtime. Take control of your work orders and transform your maintenance operations. Get started with MaintainX today and experience the difference.
Work Order Tracking FAQs
What is maintenance work order tracking software?
Maintenance work order tracking software is a digital tool that helps teams manage a variety of maintenance tasks from start to finish. It lets you create work orders and assign them to the right team members for the task. Work order software also enables you to monitor the progress of work orders in real time so you can be sure teams are staying on schedule. These platforms also offer valuable insights into resource use, worker performance, and maintenance history. You can use this information to tighten up workflows and improve team communication, leading to better asset management and reduced downtime.
What is the best work order tracking software?
The work order tracking software that works best for you depends entirely on your organization's needs. Top platforms like MaintainX stand out by offering features like mobile access, cloud-based data storage, and real-time tracking. These systems streamline task management and let you monitor operations. Look for a software solution that provides mobile access and combines well with other systems, allowing your team to stay connected and productive wherever they are.
What are the best practices for manufacturing work order tracking?
Manufacturing work order tracking relies on clear communication and streamlined processes to do its job well. To improve efficiency, consider using a digital work order tracking system that assigns tasks automatically, monitors real-time progress, and provides detailed reporting. Best practices include:
- Standardizing work order templates for consistency.
- Prioritizing preventive maintenance over reactive responses to reduce downtime.
- Regularly reviewing work order data to identify trends and areas for improvement.
- Integrating the system with inventory management tools for timely parts availability.
Following these practices keeps manufacturing operations running smoothly and helps manage resources more effectively.
Can I track work order progress with MaintainX’s mobile app?
Yes, MaintainX’s mobile app lets you track work order progress in real time from any location. Managers can create work orders and send them directly to specific team members. Technicians can update tasks, add photos, and log details directly in the app, providing instant updates to managers. The mobile app also sends notifications for task completion, delays, or changes, keeping everyone informed and on schedule. Whether in the field or the office, the app helps your team stay connected and productive, streamlining communication and task management.
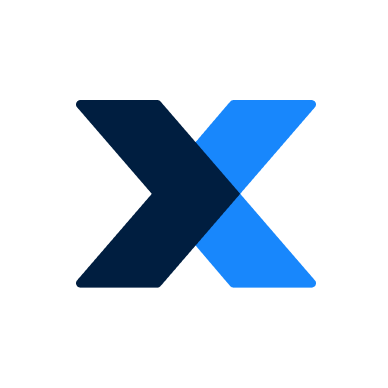
The MaintainX team is made up of maintenance and manufacturing experts. They’re here to share industry knowledge, explain product features, and help workers get more done with MaintainX!