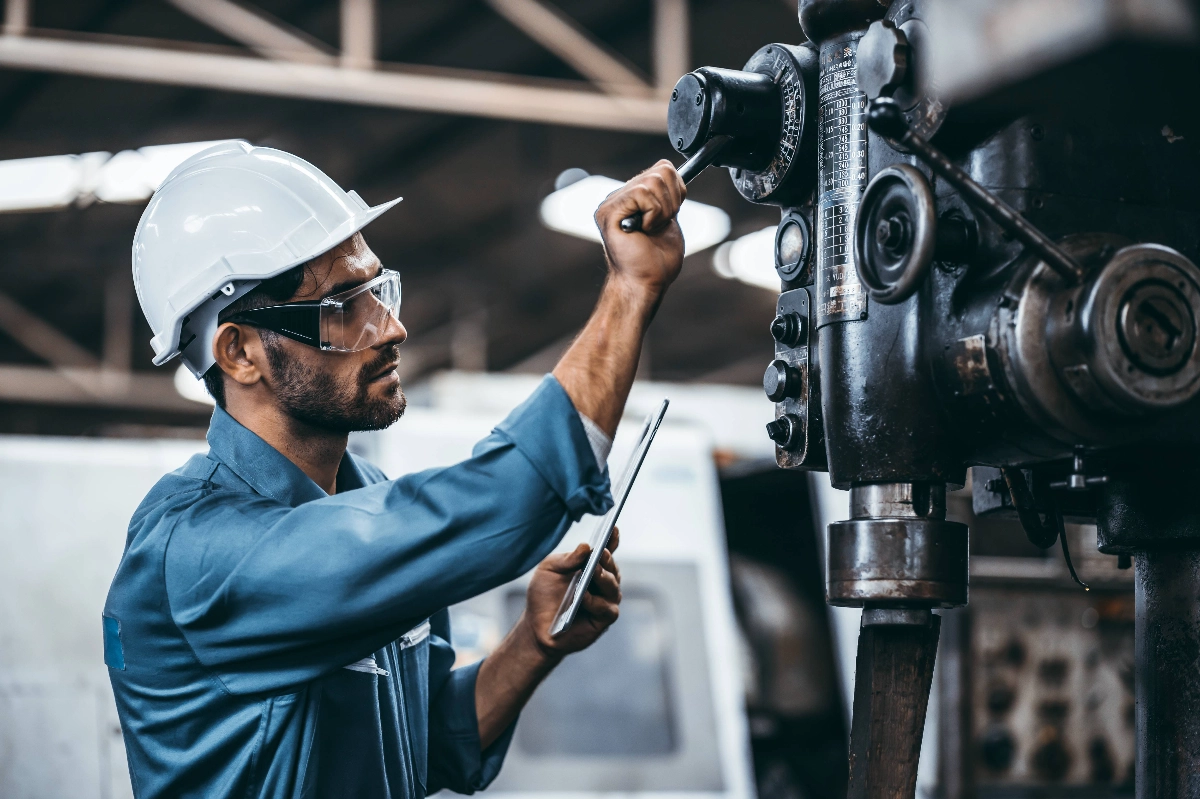
The work order management process is about more than just keeping track of tasks—it's about streamlining your entire operation. Whether you're managing a manufacturing plant or a small business, an effective work order management process helps you assign, track, and complete tasks efficiently, reducing downtime and costs along the way. But like any system, it comes with its own set of challenges. Choosing the right approach can make all the difference in optimizing your workflow and keeping your team on track.
In this article, we'll explore the key steps, common challenges, and best practices to help you fine-tune your work order management process. Let's dive in.
What is work order management?
Work order management is the process of creating, assigning, tracking, and completing maintenance tasks and repairs. It goes beyond simply getting tasks done—it’s about optimizing your entire workflow. By managing each step from start to finish, you can make the best use of your resources, minimize downtime, and boost overall efficiency.
The work order management process explained
The work order management process follows a structured cycle from start to finish. Every step is critical to ensure that maintenance operations run effectively and efficiently. While everyone can customize their process, each work order should include these seven key stages:
1. Work request submission
Team members submit maintenance requests when your equipment needs repairs. Work orders can also be triggered by preventive maintenance schedules, computerized maintenance management system (CMMS) alerts, or inspections. Simplifying submission processes and using triggers helps you prioritize. For example, the MaintainX work order management system lets you automate work order generation so you never miss critical work.
2. Work order creation
You need a clear, detailed work order to complete tasks accurately and on time. A well-structured work order should include everything from the task description and assigned personnel to the priority level and estimated completion time. With MaintainX, you can streamline this process by standardizing work orders and creating templates for recurring tasks. This saves you time, reduces errors, and keeps your maintenance operations running smoothly.
3. Work order planning & scheduling
A work order prioritization system helps see the swift completion of the most urgent tasks while keeping you up with routine maintenance activities. When setting priorities, keep in mind how important each asset is, the urgency of the task, and available resources. Effective scheduling strategies may involve assigning regular preventive maintenance work orders on a repeating schedule or grouping tasks to make the work more efficient. MaintainX offers a Workload view that simplifies work order scheduling and assignments by simply clicking and dragging key items, such as maintenance deadlines, to where you want them.
4. Executing work orders
Once assigned, technicians rely on work order details to perform their work better. A well-prepared work order includes the job description, an SOP, asset location, priority level, materials, and safety procedures. The assigned technician can give updates to maintenance managers as they work so you can be confident of well-documented issues and changes. With MaintainX, team members using the app can send and receive updates, keeping everyone informed from the start of a task to its completion.
5. Monitoring & tracking work orders
Tracking work order progress is important for maintaining efficiency. Digital tools give you real-time visibility to adjust priorities and track progress. For example, mobile apps allow your team to provide instant updates, making it easier for you to stay on top of issues. MaintainX's mobile capabilities let you oversee maintenance operations from any location, so you can be confident your team will do the job right no matter where you are.
6. Closing & documenting completed work orders
There's more to closing out work orders than just marking maintenance tasks as completed. Closing work requests involves providing thorough documentation, feedback from the assigned technician, and final supervisory approval to confirm the work was done correctly. Digital platforms like MaintainX enable your teams to easily document tasks, provide follow-up steps, and receive manager approval before moving forward, providing you with a complete maintenance history.
7. Tracking KPIs for continuous improvement
Improving your maintenance process doesn’t stop with a completed work order. Tracking key performance indicators (KPIs) over time—with the help of work order data—helps you spot areas for optimization. MaintainX generates detailed reports that give you the insights needed to make data-driven decisions for continuous improvement.
Overcoming common work order management challenges
Managing work orders can be complex, and ineffective work order management can often lead to slower completion rates and increased costs. Powerful work order management software helps facility managers overcome these obstacles through numerous features that boost efficiency. These tips will help you tackle common challenges and improve your work order management process.
Ensuring real-time insight and accurate updates
Keeping everyone updated can be challenging. Mistakes happen without immediate access to information, and miscommunication slows down work. A computerized maintenance management system (CMMS) that provides real-time insights can solve this problem. MaintainX lets parties easily access the latest information so you can tighten processes and improve efficiency.
Streamlining communication among teams
When restricted to one or two channels, information between teams handling a work order can move slowly, leading to delays and confusion. Streamlined communication is vital for keeping everyone on the same page. MaintainX offers integrated Chat, allowing your team members to communicate directly through the platform and keep everyone informed. This reduces miscommunication and improves your task coordination across maintenance teams.
Maintaining compliance standards
Following official standards such as OSHA regulations and industry-specific safety protocols is required for many maintenance tasks. Failure to follow standards can lead to rework, safety lapses, or even legal issues. Work orders usually provide checklists and procedure guides to direct technicians through each step and keep them compliant with requirements. By attaching instructions and reminders to work orders, MaintainX helps your team stay compliant while recording every action taken for easy auditing and reporting.
Managing a high volume of work orders across multiple locations
Larger organizations often struggle to manage a high volume of work orders, especially when using legacy systems that don’t scale well. Such inefficiencies can lead to delays and missed tasks. MaintainX solves this with centralized work order management that you can use across multiple locations. Centralized management provides real-time visibility and standardizes processes on a large scale. Multi-site dashboards and resource sharing enable your teams to easily coordinate tasks and keep workflows moving smoothly for any facility size or location.
Best practices to improve work order management
Effective work order management requires the right strategy and tools. Maintenance teams can boost efficiency and minimize equipment downtime by using features that streamline workflows and reduce manual effort. These best practices highlight how to improve work order management.
Automate work order triggers with meters
Setting up work orders to trigger based on conditions such as meter readings gives you prompt and precise scheduling of preventive maintenance activities and critical repairs. MaintainX works seamlessly with IoT devices allowing you to capture meter readings and automatically generate work orders when equipment meets preset conditions. This proactive approach optimizes asset performance and greatly reduces unexpected equipment failures.
Schedule recurring work orders
You can easily manage routine maintenance activities with automated triggers that prompt timely execution. MaintainX allows users to create preventive maintenance schedules that repeat automatically. This reduces the chance of overlooking vital tasks and prevents costly equipment downtime. Recurring scheduling enhances your team’s efficiency and keeps assets running smoothly by giving them the information they need ahead of time.
Attach detailed instructions and procedures to work orders
Clear step-by-step instructions help technicians perform repair and maintenance tasks accurately and efficiently. MaintainX enables you to attach detailed procedures to every work order, preventing workers from missing important steps. Attaching instructions reduces errors, boosts productivity, and gives every maintenance staff member the information they need to follow company and regulatory standards.
Use templates for faster work order creation
Manually creating each work order can be time-consuming and leaves room for errors. Customizable templates let your team members standardize recurring tasks and save significant time, promoting efficiency and saving time. MaintainX allows users to create and reuse customizable work order templates, keeping processes consistent and speeding up your work order creation.
Attach pictures to work orders from a mobile device
Attached images considerably enhance troubleshooting and repair efforts. Pictures and diagrams give technicians visual context to quickly resolve issues and perform accurate repairs. With MaintainX, users can attach images directly to work orders using a mobile device, significantly improving communications so that managers and technicians are aligned throughout every stage of the repair and maintenance processes.
Optimize your work order management with MaintainX
MaintainX offers powerful tools that simplify and enhance every aspect of work order management. From real-time communication to automated scheduling, these features enable swift and effective task completion and help your maintenance teams consistently produce successful results.
Digital work orders with mobile accessibility
MaintainX empowers users to leverage technology to create, view, and update work orders wherever they use a mobile device. This mobile accessibility provides efficient communication and real-time status updates, keeping your entire team aligned and letting everyone respond swiftly to changing priorities. Removing paperwork from the picture also streamlines operations and speeds up your task completion.
Reporting and analytics for informed decision-making
With MaintainX, managers can access real-time reporting and analytics to track work order progress, labor costs, and equipment performance. This data gives you a look into facility operations, helping you make informed decisions to optimize resource allocation and improve efficiency. MaintainX reporting tools let your teams monitor trends and provide information that helps your organization improve maintenance practices, whether you’re a small business or a large corporation.
Integrated asset management
MaintainX combines asset management capabilities that let you monitor equipment health, track usage, and proactively schedule maintenance tasks. By keeping a close eye on an asset's performance, you can prevent equipment failures and extend its life span. This streamlined approach improves facility maintenance by keeping assets on track for timely and effective upkeep.
Recurring work orders for preventive maintenance
With MaintainX, your teams can easily set up recurring work orders for preventive maintenance tasks so they’ll never miss routine upkeep. This proactive maintenance approach helps prevent breakdowns and extend asset lifespans. Automating these processes tightens up maintenance workflows and focuses on tracking progress to keep your operations running smoothly.
Work order templates and checklists
With MaintainX, you can utilize work order templates and attach detailed checklists for ongoing tasks, keeping practices consistent across maintenance activities. This reduces errors and saves time. By standardizing processes, teams continually improve job performance and never miss an important step.
Work order management FAQs
How does MaintainX support multi-location maintenance operations?
MaintainX simplifies maintenance for multiple locations by using a centralized platform. You can manage work orders, assets, and schedules across all sites from one dashboard, keeping your team consistent and compliant. The platform also allows you to share resources like templates and checklists so all locations follow the same best practices. This improves efficiency and reduces downtime, no matter how many sites you manage.
How does MaintainX ensure data security and compliance?
MaintainX uses advanced encryption to keep your data safe, whether it's stored or in transit. The platform meets compliance standards like SOC 2 and GDPR. You can control access by setting user roles and permissions, ensuring only authorized team members can make changes. MaintainX also tracks work orders and maintenance activities, making audits and compliance easier.
What is a work order management system?
A work order management system is a digital tool that helps you create, assign, track, and complete maintenance tasks. These systems streamline maintenance by organizing work orders, scheduling tasks, and tracking progress. MaintainX allows your team to access real-time updates, schedule work, and manage assets from one central place, helping you complete tasks efficiently and accurately.
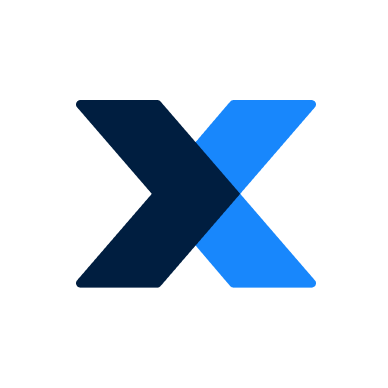
The MaintainX team is made up of maintenance and manufacturing experts. They’re here to share industry knowledge, explain product features, and help workers get more done with MaintainX!