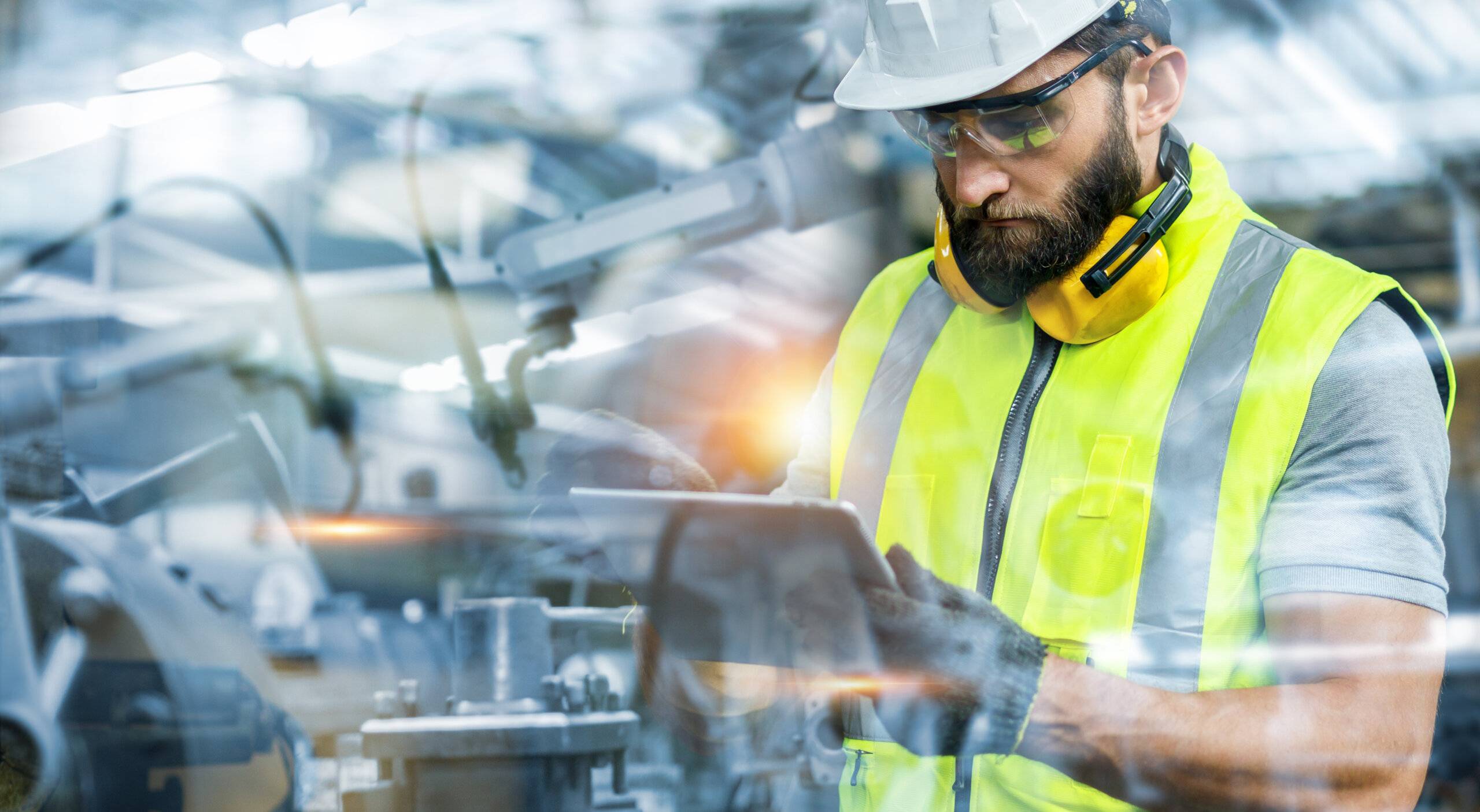
Trying to execute a maintenance strategy without a CMMS is like playing a game of darts while blindfolded. You know you have tasks to complete, but figuring out how many—or how to complete them—is like taking a shot in the dark.
A Computerized Maintenance Management System (CMMS) is a software solution that removes the proverbial blindfold and helps organizations efficiently and proactively manage and maintain their equipment. Maintenance, repair, and operations (MRO) professionals across a number of industries use CMMS software. From manufacturing to facilities management to property management—any industry that relies on equipment to operate can benefit from a CMMS.
A good CMMS helps MRO professionals organize their maintenance operations, streamline procedures, digitize their systems and processes, and reduce costs associated with unplanned downtime. The improvements made possible by digital tools like a CMMS are often referred to more broadly as digital transformation—the process of adopting and implementing digital technology to radically change operations.
By our count, there are 20 CMMS benefits that are transforming maintenance management today. Let’s take a look at each one.
1. Improved asset management and equipment reliability
At a high level, CMMS software modernizes the way teams manage their assets and increases equipment reliability. It does this in a few ways.
First, managing all assets in one place means they can be tracked and utilized more easily, rather than waiting until someone remembers to perform maintenance—or worse, until something breaks.
CMMS software also streamlines preventive maintenance scheduling, automating preventive work orders based on timing or usage. DeLong, for example, reached 100% preventive maintenance coverage on all its assets across all accounts in just three months after adopting a CMMS. Getting ahead of preventive maintenance tasks increases equipment uptime, extending asset lifecycles.
Finally, maintenance software allows MROs to monitor asset performance in real-time, allowing them to deal with problems before they impact production.
2. Increase operational efficiency and reduce downtime
CMMS software introduces a level of automation that both increases efficiency and reduces downtime. Automated work order processing makes it easy for maintenance managers to assign, complete, and track work orders, accelerating each step of the process and freeing up technicians’ time. Higher efficiency combined with less unplanned downtime leads to labor productivity, so workers can spend more time completing tasks that contribute to the bottom line.
Managing maintenance through a software solution also allows maintenance teams to optimize resource allocation so that the right people are assigned to the right tasks at the right time. Doing this digitally means that no time is wasted filling out paperwork—or missing it completely. The red tape of relying on pen and paper is instantly removed. Wasueon Machine experienced this first-hand when they adopted a CMMS and saw PM completion rates skyrocket from 60% to 100%.
3. Maintenance cost savings and financial benefits
In our 2024 State of Maintenance Report, we found that, despite most companies (85.2%) experiencing less unplanned downtime, a significant portion (29.4%) say unplanned downtime costs are rising. Thankfully, a CMMS enables substantial cost savings and financial benefits.
Being proactive about maintenance means being able to better control maintenance costs. Having fewer surprise breakdowns and an accurate read on asset health leads to long-term savings, both through better planning and asset lifespan extension.
Maintenance software also provides a holistic view of inventory management, meaning teams can order parts when they need them—and ensure nothing ever collects dust on a shelf. Finally, a CMMS allows MRO professionals to accurately track ROI by tightly tracking maintenance activities against costs.
4. Ensure compliance and safety standards
Staying compliant is immensely easier with a CMMS. Admins can create repeating schedules, set due dates, and get alerts when inspections are past due. Technicians can complete compliance documentation within the app, ensuring every detail is captured for compliance audits.
CMMS software also enhances safety protocols—and standardizes maintenance practices—by allowing maintenance teams to create digital checklists for technicians to follow. With these, procedures can be carried out the same way every time a task is completed.
5. Leverage CMMS data for proactive maintenance and informed decision-making
A proactive maintenance strategy needs data to run—data on asset health, past failures, parts inventory, staffing, and more. A CMMS centralizes this data and makes it easily accessible so that managers can keep their machinery—and their team’s workflows—running smoothly.
CMMS data also allows teams across organizations to work better together. When there’s a single source of truth to refer to, communication barriers are reduced, and teams can stay tuned into each other’s progress and needs. The net effect is better, data-based decision-making across the organization.
6. Access CMMS software on the go with mobile accessibility
A CMMS with a mobile app makes it easy to capture work order data and log updates from the field. When using an app, technicians can see work assigned to them, easily access asset information, and notify the team when their work is complete, no matter where they are.
7. Customized CMMS solutions for scalable maintenance management
CMMS software can help organizations of any size, from single-site operations to global enterprises. The right CMMS should have features any sized team can readily use, and be flexible enough to accommodate teams and organizations as they grow.
CMMS workflows should also be customizable so that when a team changes, the workflows associated with that team can also change.
8. Predictive maintenance and asset health monitoring
Predictive maintenance—the most sophisticated of all maintenance strategies—uses IoT sensors to predict and prevent failures before they occur. A CMMS can integrate with those sensors so that any potential issues feed directly into your team’s workflows as upcoming tasks.
A predictive strategy should also factor in asset health data, which is possible with a CMMS (and virtually impossible without it).
9. Streamlined inventory management and spare parts tracking
Inventory management can make or break any company’s efforts to reduce downtime. If something breaks and you don’t have a spare part to fix it, it can be disastrous. CMMS software digitizes inventory management so that MRO professionals always have an accurate read on what’s available, where parts are located, and what’s running low.
Having a CMMS that helps manage inventory data also helps reduce inventory costs by preventing emergency shipping, providing insight into stock across facilities, and providing one centralized place to purchase parts.
10. Effective vendor management and procurement tracking
Keeping track of vendor information is often a headache for MRO professionals. A CMMS offers instant relief from that pain, allowing admins to easily access vendor contact information as well as information related to parts and assets.
Admins can also keep external vendor conversations centralized with the right features. Some CMMS software includes external work orders, tracking vendor work progress within the app, and the ability to share files and emails centrally.
Finally, a CMMS can help teams stay on top of parts inventory and procurement tracking by creating and tracking purchase orders directly in the software.
11. Sustainable maintenance practices for environmental impact reduction
An efficient site doesn’t just mean that work is completed more quickly. It also means higher energy efficiency and less waste. A CMMS can help maintenance teams drastically improve inefficient processes to lessen the organization’s environmental impact and save money.
12. CMMS reporting capabilities and maintenance KPIs for better insights
Collecting and tracking data is great, but it’s only meaningful when that data is turned into actionable insights. CMMS reporting lets MRO professionals keep a close eye on the KPIs that matter—like Mean Time to Repair (MTTR), production capacity, and downtime—and improve them over time.
CMMS reports and dashboards should be easily customizable. This way, any team can get a quick read on the KPIs that keep operations running, and snap into action if anything’s amiss. Cox Machine, Inc. uses their CMMS dashboard to show a snapshot of work orders, organized by priority.
13. Increase stakeholder satisfaction with proactive maintenance and CMMS data transparency
Fewer breakdowns means greater efficiency, which leads to increased customer satisfaction. When you can prevent crises, you can keep delivering stellar results.
CMMS software also enables greater transparency with stakeholders, giving teams access to all the reports, checklists, and asset health data needed to paint a full picture for anyone outside the maintenance team.
14. Future-proof maintenance operations and advanced technologies
As artificial intelligence (AI) and machine learning continue to improve, their adoption across facilities will increase. A CMMS should integrate with these technologies to allow MRO teams to adapt to industry changes.
Many CMMS software options also have their own AI features, such as anomaly detection and AI-generated procedures using photos, files, or speech as a prompt.
15. Implementation and continuous improvement in maintenance processes
For maintenance teams coming from pen-and-paper systems, the idea of adopting a new software system may seem daunting. A good CMMS vendor will guide teams through their implementation, eliminating any guesswork. Onboarding training should give every worker the information they need to use the CMMS confidently.
Once each user is onboarded and the right systems are in place, a CMMS can also guide the continuous improvement of maintenance processes. Teams can easily track their maintenance programs over time to improve uptime and asset utilization.
16. Automated maintenance scheduling and task prioritization
Many maintenance teams have every intention of running a preventive maintenance strategy, only to fall back into reactive maintenance cycles when unplanned work appears and takes priority. Our 2024 State of Industrial Maintenance report found that 57% of facilities still rely on run-to-failure maintenance. A CMMS can help automate preventive task scheduling so that work orders are never abandoned.
Even with a preventive maintenance strategy that’s informed by real-time data and well-optimized, unexpected work will always find a way to derail plans. A CMMS can help prioritize critical preventive maintenance tasks so that an emergency doesn’t throw off the entire operation.
17. Reduce unplanned downtime and equipment failures
Equipment breakdowns are the number one cause of unplanned downtime, which has only gotten more costly over the years, according to the Unplanned Downtime Paradox. When assets are maintained regularly and tracked diligently, the number of failures—and the amount of unplanned downtime—go way down.
Less downtime and fewer equipment failures also leads to improved facility availability, meaning assets are available to produce at their full capacity rather than being shut down due to repairs or breakdowns. One large McDonald’s franchise recently reduced their equipment downtime by 85% after implementing a CMMS across 22 stores.
18. Improve labor management and maintenance team accountability
Without a system in place to plan, schedule, and track work, maintenance activities can be executed haphazardly (read: reactively) or relegated to best guesses regarding availability and work completed.
When workers can clearly see the work assigned to them—and when that work gets tracked automatically—efficiency and accountability both increase. Managing teams is exponentially easier when everyone knows who’s responsible for what, and which tasks are waiting to be completed.
19. Resource planning
Planning according to resources and capacity is one of the biggest drivers of operational efficiency. It’s also nearly impossible to do without a CMMS. Maintenance software lets managers see a full and accurate picture of their team’s workload and capacity at all times. This lets them make realistic resourcing plans according to what their team can actually achieve (and make adjustments if things change).
Maintenance teams that effectively use resource planning can get a lot more strategic work done, rather than waiting to see who’s available at any given time.
20. User-friendly CMMS interface for streamlined maintenance work
Teams will naturally default to using whichever system is easiest, so a CMMS that isn’t intuitive to use won’t be a hit. Great maintenance software is easy to adopt, use, and seamlessly integrates into existing workflows.
Most importantly, CMMS software shouldn’t just be easy for admins to use. Anyone who’s expected to interact with a CMMS should be able to do so easily, with as shallow a learning curve as possible. When software is easily adopted across teams, it can truly support maintenance strategies and workflows.
CMMS software helps today’s teams transform their maintenance management
There are many benefits to adopting CMMS software. But the bottom line is that it’s the only tool that helps maintenance teams truly transform their operations. Only a CMMS allows teams to move away from reactive maintenance, automate preventive tasks, and move towards a predictive maintenance strategy—all while reducing costs and increasing efficiency.
If you want to learn more about what a CMMS can do for your team, get in touch with us today.
FAQs about CMMS Benefits:
What specific maintenance challenges can a CMMS address?
A CMMS helps maintenance teams track, schedule, and improve their maintenance activities so that they can move away from reactive maintenance, reduce unplanned downtime, and tightly control maintenance costs. Without a CMMS, many teams struggle to complete work orders, adopt preventive maintenance strategies, and improve their overall operations.
How does CMMS enhance asset lifecycle management?
CMMS software allows teams to track the lifecycle of complex machinery, pinpoint failures, and control costs. It also allows MRO professionals to access maintenance logs for each asset, schedule preventive maintenance to keep assets running smoothly, and prevent unplanned breakdowns by tracking asset health.
How quickly can businesses see financial returns from CMMS?
Many businesses see a return on their CMMS investment quickly. ROI is greatly influenced by a team’s size, current maintenance practices, downtime costs, and the number of breakdowns that occur each month.
Which maintenance KPIs are most impacted by a CMMS?
The adoption of a CMMS greatly improves maintenance KPIs like Mean Time Between Failures (MTBF), Mean Time to Repair (MTTR), workforce productivity, unplanned downtime, and maintenance costs.
How does mobile accessibility in CMMS improve technician efficiency?
CMMS software that offers a mobile app skyrockets technician efficiency. When technicians can access work orders, operating instructions, and checklists on the floor, they can complete work faster and more accurately, without the headache of having to keep up with paperwork.
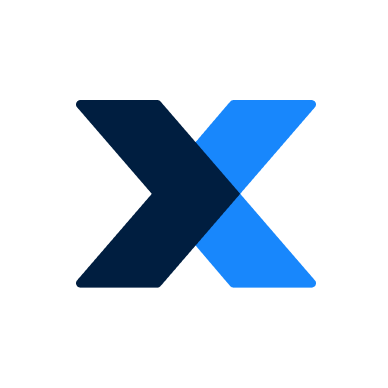
The MaintainX team is made up of maintenance and manufacturing experts. They’re here to share industry knowledge, explain product features, and help workers get more done with MaintainX!