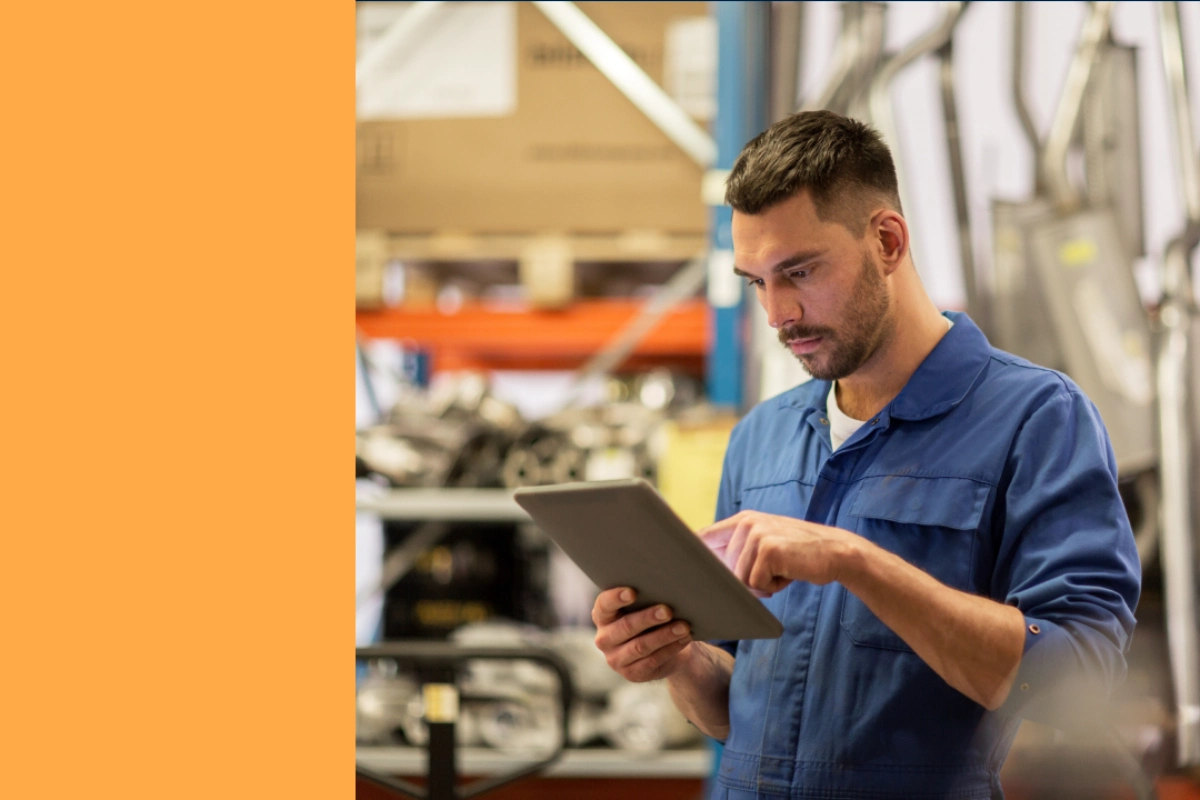
Unplanned equipment failures and poor maintenance can be expensive for businesses. The right maintenance software helps prevent these problems by allowing companies to plan ahead, work more efficiently, and save money.
This technology is often sold as part of a more comprehensive computerized maintenance management system (CMMS), which combines equipment maintenance features with asset tracking, financial tasks, and strong reporting capabilities.
Key Takeaways:
- Choosing the right equipment maintenance software minimizes downtime, extends asset lifespan, and streamlines maintenance.
- Essential features include preventive maintenance scheduling, work order management, real-time monitoring, AI-driven insights, and asset tracking.
- Cloud-based solutions enable remote access, allowing teams to manage maintenance from anywhere.
- A strong CMMS improves operational efficiency, automates routine tasks, and enhances decision-making with data analytics.
- Investing in the right system leads to significant cost savings and better resource utilization.
What makes great equipment maintenance software?
When choosing software, focus on features that are easy to use and can grow with your business.
Core features to look for:
- Preventive maintenance scheduling: A strong CMMS automates maintenance tasks to prevent unexpected breakdowns. It schedules routine servicing and ensures machines keep running without costly downtime.
- Work order management: An effective CMMS digitizes work order assignment and tracking, eliminating inefficient paper logs and scattered email chains. A central system allows teams to prioritize repairs, monitor progress, and complete work efficiently.
- Asset management and tracking: The right software provides real-time data on asset performance, usage, and history. It gives your managers the info they need to decide when to repair or replace equipment based on accurate insights.
- Inventory management: The software tracks spare parts and supplies, so there's no waiting for essential components. For example, hospitals use this technology to keep medical equipment stocked with necessary parts for quick repairs and manufacturing teams to manage their supply of electrical controls.
- AI and automation: Advanced maintenance software uses AI for predictive maintenance and automated reporting. It detects early signs of equipment failure and alerts teams before issues escalate. For instance, facility managers can receive notifications when HVAC systems show signs of failure, preventing costly breakdowns from happening in the first place.
ROI and business impact
A CMMS does more than just streamline work orders—it has a measurable impact on a company’s financial health. A strong maintenance strategy reduces downtime, lowers costs, and extends the life of assets, leading to more efficient and predictable operations.
- Reduce unplanned downtime: Facilities that shift from reactive to preventive maintenance experience 32% fewer unexpected shutdowns. Additionally, our data shows that 65% of organizations report proactive maintenance as the most effective way to prevent disruptions.
- Lowering downtime costs: Unplanned downtime costs businesses an average of $25,000 per hour. In larger companies, that number can exceed $500,000 per hour when operations are forced to stop.
- Cutting maintenance expenses: Organizations that implement a CMMS, such as MaintainX, typically see first-year returns on investment ranging from 25% to 300%, depending on their strategy and software utilization.
- Extending asset life: Companies that track and maintain equipment health with a CMMS improve overall equipment effectiveness (OEE) and decrease unexpected breakdowns, leading to longer-lasting assets.
The right CMMS allows businesses to shift from a reactive approach to a proactive strategy, resulting in greater efficiency, reliability, and cost savings.
Top equipment maintenance software solutions
Data analytics and automation have created new opportunities for CMMS providers, with the market expected to grow to $2,069.3 billion by 2031. This growth creates many options to choose from, but not all technologies are created equally. We have chosen the best maintenance management tools to help you prevent problems before they occur and save money on your operation.
MaintainX
MaintainX is a cloud-based maintenance and operations platform designed for businesses of all sizes. It stands out for its customization, advanced analytics, and strong integration capabilities, making it a flexible solution for various industries.
Key features:
- MaintainX CoPilot AI to pull information from OEM manuals and turn them into work order directions
- Mobile-first, full-featured experience that gives field technicians powerful insights while in the field
- Intuitive, user-friendly interface that requires no data experience to enjoy
- Digital workflow creation from uploaded PDFs, images, or handwritten notes
- Anomaly detection that flags unusual readings in work order data to prevent costly failures
- 20+ integrations plus API to connect with a wide range of business applications
- Learning library with certification for key roles in English, Spanish, French, and Italian
MaintainX promotes efficiency and reduces waste with automation, but also with its reporting features. Users can create tailored dashboards and schedule automated report exports via email so they can stay on top of repairs. It also supports CSV exports with scheduled data exports, and technicians can generate or access reports from the field through the simple-to-use mobile app. Reports are easy to read and understand, giving team members the information they need to improve operations and cut costs in organizations of any size.
Best for: Businesses seeking rapid efficiency gains through intuitive user experiences and AI-powered workflows. It provides some of the greatest flexibility and scalability for growing enterprises.
Upkeep
UpKeep is a mobile-first maintenance management software designed for small to medium-sized businesses. It simplifies asset management and work orders with an intuitive interface and strong mobile capabilities.
Key features:
- Mobile apps that let technicians create, track, and complete work orders from anywhere
- Automated schedules based on time or meter readings
- Competitive pricing compared to other solutions
- Frequent updates based on user feedback
- Highly rated assistance for onboarding and troubleshooting
Fiix
Fiix is a cloud-based maintenance management solution that streamlines preventive maintenance and asset management. It stands out for its ease of use, automation capabilities, and strong mobile accessibility.
Key features:
- No complex installations, automatic updates, and remote accessibility
- Automated scheduling based on time, meter readings, or events
- Customizable reports and real-time data dashboards
- Create work orders, receive notifications, and access data from anywhere
eMaint
eMaint is a highly configurable CMMS designed for businesses seeking powerful reporting, mobile accessibility, and seamless integration with Fluke tools. It’s designed to help organizations meet OSHA, FDA, and ISO compliance requirements.
Key features:
- Custom dashboards and automated report generation for data-driven decisions
- Offline-enabled mobile app to help technicians in the field
- Responsive service and extensive training resources
- Integration with Fluke IIoT sensors for condition monitoring
Facilio
Facilio is a cloud-based CMMS that unifies maintenance, operations, and sustainability into a single platform. It leverages AI and IoT integration to enhance predictive maintenance and workflow automation.
Key features:
- Combined maintenance, operations, and sustainability for real-time insights
- AI and machine learning (ML) to predict equipment failures and reduce downtime
- Highly configurable modules and workflows require no coding
- Mobile app that empowers technicians to update work orders offline
- IoT device, ERP, and building automation systems integration
- Intuitive design to support quick adoption
Limble CMMS
Limble CMMS is a highly customizable maintenance management system that simplifies part replacement and offers the most features when used on a desktop.
Key features:
- Custom asset fields to help tailor work request portals and support asset tags with barcodes or QR codes
- Specialized dashboard widgets and shortcuts to prioritize the most relevant KPI data
- Automation of repetitive tasks like work order generation, approval routing, and notifications
- Configuration of advanced task settings globally or at the individual task level
- Responsive service and training through Limble University
Asset Panda
Asset Panda is a cloud-based platform that helps organizations efficiently track and manage their assets. With a highly customizable interface and mobile-friendly design, it adapts to the needs of industries like IT, construction, education, and healthcare.
Key features:
- Real-time asset tracking with status, condition, and location
- Mobile-friendly full asset history to see maintenance schedule, warranties, and depreciation
- Barcode scanning built into the mobile app
- Unlimited users to give access to everyone in the field
- Smart permissions that offer role-based access to secure data without limiting collaboration
MPulse
MPulse is a CMMS focused on serving the manufacturing, healthcare, education, government, and hospitality industries.
Key features:
- Work order management to prioritize critical tasks over low-priority jobs
- Calendar view for a clear, visual timeline of upcoming maintenance tasks and better organization
- Inventory tracking to monitor supply usage and link items to work orders
- Graphical reporting with detailed reports and insights on maintenance performance
- Cross-platform access for a smooth experience with desktops, tablets, and smartphones
HippoCMMS
HippoCMMS, now part of Eptura, is a maintenance management system that streamlines work orders, tracks preventive maintenance, and manages inventory. It’s built for industries like manufacturing, healthcare, and education.
Key features:
- Cost optimization tools to monitor energy usage and right-size space planning
- Workplace automation for better safety compliance to avoid fines
- All-in-one portfolio to see every facility on one screen
- Inspection checklists aligned with compliance schedules
- Document uploads so technicians can document completed inspection orders
IBM Maximo
The IBM Maximo Application Suite offers asset lifecycle management to support equipment maintenance, inspection, and lifespan. It uses generative AI, analytics, and Internet of Things (IoT) technologies.
Key features:
- Enterprise asset management (EAM) to support assets from procurement to decommissioning
- Mobile app with remote access to necessary information and resources
- Advanced analytics to optimize maintenance planning and mitigate unnecessary and costly risks
- AI computer vision and mobile tools to monitor and analyze asset conditions in real time
Elevate your equipment maintenance strategy with MaintainX
Companies have many choices for the best equipment maintenance software, but only MaintainX combines powerful functionality with an intuitive, mobile-first design. Businesses can reduce unexpected downtime by 32% through automated preventive and predictive maintenance scheduling to keep equipment online and productive.
With MaintainX, companies can avoid regulatory fines by automating inspections and maintaining a digital audit trail for OSHA and EPA compliance. The platform also helps eliminate parts shortages by monitoring inventory levels and automating reorders, reducing emergency part costs by up to 34%.
Trusted by over 8,000 organizations worldwide, MaintainX is scalable for industries like manufacturing, food and beverage, automotive, and more. Take control of your operations today—try MaintainX to reduce downtime, improve productivity, and ensure your equipment runs at peak performance.
Frequently asked questions
What is asset operations management?
Asset operations management allows companies to keep their equipment, tools, and buildings running smoothly. It combines maintenance, planning, and tracking so teams can prevent breakdowns, reduce costs, and improve efficiency. With the right system, businesses can see all their assets in one place, schedule repairs easily, and make smarter decisions to keep everything working at its best.
What is enterprise asset management?
Enterprise asset management (EAM) is how businesses take care of their equipment, tools, and buildings over time. It helps track, maintain, and improve assets so they last longer and work better. With EAM, companies can schedule repairs, monitor performance, and reduce costs by preventing problems before they happen.
What is preventive maintenance?
Preventive maintenance is regular, planned upkeep to stop equipment from breaking down. Instead of waiting for something to fail, businesses check, clean, and fix things in advance. This helps prevent costly repairs, reduces downtime, and keeps everything running longer.
What is a work order?
A work order is a document that tells workers what job needs to be done. It includes details like the task, location, tools needed, and deadline. Businesses use work orders to track repairs, maintenance, and other tasks to improve efficiency and reduce costs.
What is CMMS software?
CMMS (Computerized Maintenance Management System) software helps businesses organize and track maintenance work. It stores information about equipment, schedules repairs, and keeps records of past work. With a CMMS, teams can prevent breakdowns, reduce downtime, and stay in compliance with safety regulations.
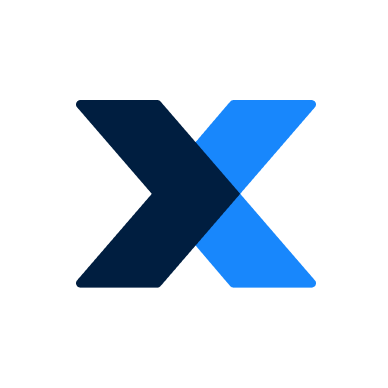
The MaintainX team is made up of maintenance and manufacturing experts. They’re here to share industry knowledge, explain product features, and help workers get more done with MaintainX!