.jpg)
What’s the difference between a computerized maintenance management system (CMMS) that gathers dust and one that has an impressive impact on your bottom line? The answer isn’t features alone—often, it comes down to how you prepare for implementation and who you involve from day one.
We’ve outlined three of the most important steps to take before you even select your software. By getting these fundamentals right, you'll set your organization up to see real value from your CMMS investment.
Three steps to take for a successful CMMS implementation
1. Build your implementation foundation
It’s smart to start your software search with a clear picture of what features and results are most important to your team.
- Define your CMMS requirements: Consult your frontline workers and your established goals to create a clear requirements list. Look beyond basic features to factors that will impact long-term success: How intuitive is the interface? What training resources are available? Read community reviews, request demos, and talk to others in your industry. Pay special attention to the vendor's implementation support and track record of customer success.
- Set the asset management groundwork: Good data is the foundation of an effective CMMS. So, before choosing your software, you should get your data ready. For example, decide how you'll organize equipment by location, type, or importance. This standardization helps streamline migration once you select a system.
2. Start on the frontlines
To ensure long-term success, involve the frontline workers who will actually use the software from the start. Here’s how:
- Get feedback on current pain points and needs: Work with your team to identify exactly where a CMMS would benefit them the most. For example, if your team is doing too much trial and error, prioritize digital Standard Operating Procedures (SOPs) that will eliminate the guesswork. If they’re struggling to capture data quickly on the floor, choose software that allows them to record voice memos instead of having to type. This way, you’ll be more likely to get software your team will use.
- Demonstrate "what's in it for me?" benefits: If your team wastes hours hunting down paper records, conduct live demos demonstrating how easy it is to pull up work histories in your CMMS. Are they spending too much time looking for coworkers on the factory floor? Show them your software’s instant chat features. By doing this, you’ll show your team that a CMMS will make their work easier, not harder.
3. Define clear goals and success metrics
Setting specific, measurable maintenance objectives will help you stay on track once you begin implementation. They’ll also help you measure the ROI of your CMMS. Here are the steps to take:
- Create a project charter that works: Include all the necessary information here—from budget to roles and responsibilities. Specify realistic timelines and resource requirements, like how many hours key team members will need to dedicate to implementation tasks. This way, you can quickly identify and get ahead of any potential issues.
- Connect CMMS goals to operational KPIs: Set specific targets, like reducing equipment downtime by 15% within six months. These clear milestones help you track progress and demonstrate the CMMS's impact on operations.
- Quantify cost savings: Build a clear business case by projecting and tracking how the software will benefit the company. Do you anticipate reduced downtime or lower inventory costs? For example, if your facility loses $1,000 per hour of downtime, show your team how a 15% downtime reduction will translate to significant savings. These numbers will help secure continued leadership support.
Set the stage for a successful implementation
When organizations take these steps before CMMS implementation, the results speak for themselves: higher adoption rates, improved maintenance efficiency, and significant cost savings. MaintainX customer Pharma NZ reports yearly cost savings of up to $70,000 and a 30% improvement in maintenance efficiency.
The bottom line? It pays to focus on these fundamentals before diving into technical details.
Learn from our implementation experiences
Our comprehensive CMMS Implementation Whitepaper combines insights from thousands of successful implementations to create your roadmap for success. Download it today to access:
- A detailed checklist of must-have CMMS features for manufacturing facilities.
- Common pitfalls and proven strategies to avoid them.
- Best practices for driving long-term adoption and ROI.
Ready to turn your CMMS investment into lasting value? Download the whitepaper now and get the advice you need to succeed.
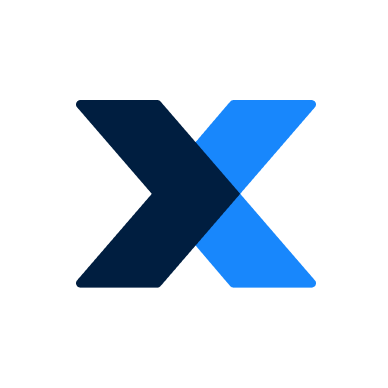
The MaintainX team is made up of maintenance and manufacturing experts. They’re here to share industry knowledge, explain product features, and help workers get more done with MaintainX!