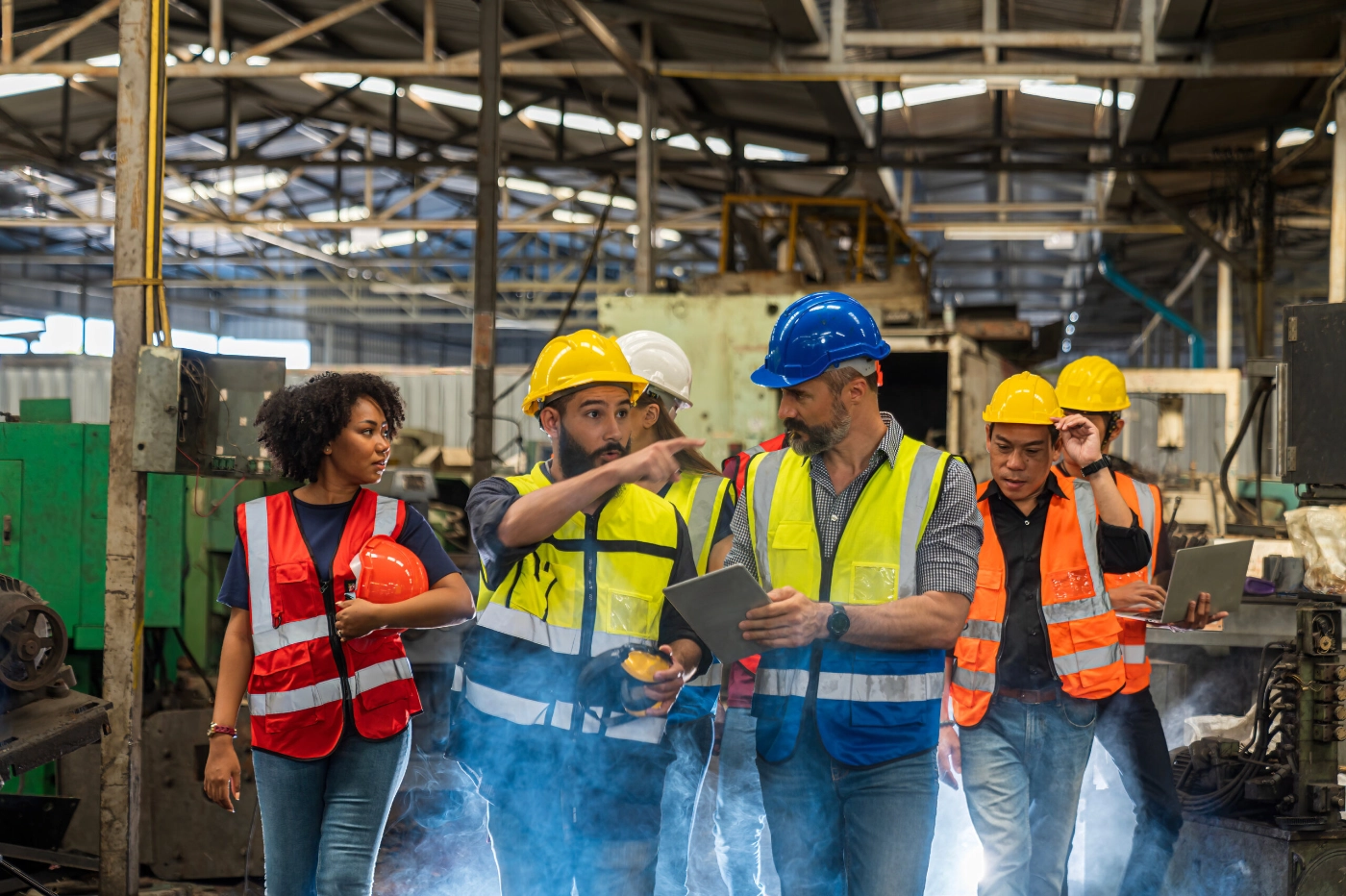
A Computerized Maintenance Management System, or a CMMS, is a software solution that helps manage maintenance operations. Many CMMS solutions on the market today have a wide range of applications. MaintainX CMMS, for example, offers many use cases, from facility management to inventory management.
However, if you’re running a manufacturing facility, you probably understand that maintenance underpins every aspect of your operations. Properly managing your maintenance will help you optimize everything from cost effectiveness to performance metrics. Let’s look at how to do that and how it all starts with preventive maintenance.
Why Preventive Maintenance Matters
Preventive maintenance refers to maintenance activities you carry out before breakdowns or downtime occur instead of after. It involves preemptive actions to keep assets and equipment in good working condition and streamline workflows.
Preventive maintenance takes many forms. It could be routine maintenance that follows a particular schedule according to the requirements of your assets or facility. Examples include monthly fire alarm testing, lubrication, HVAC cleaning, etc.
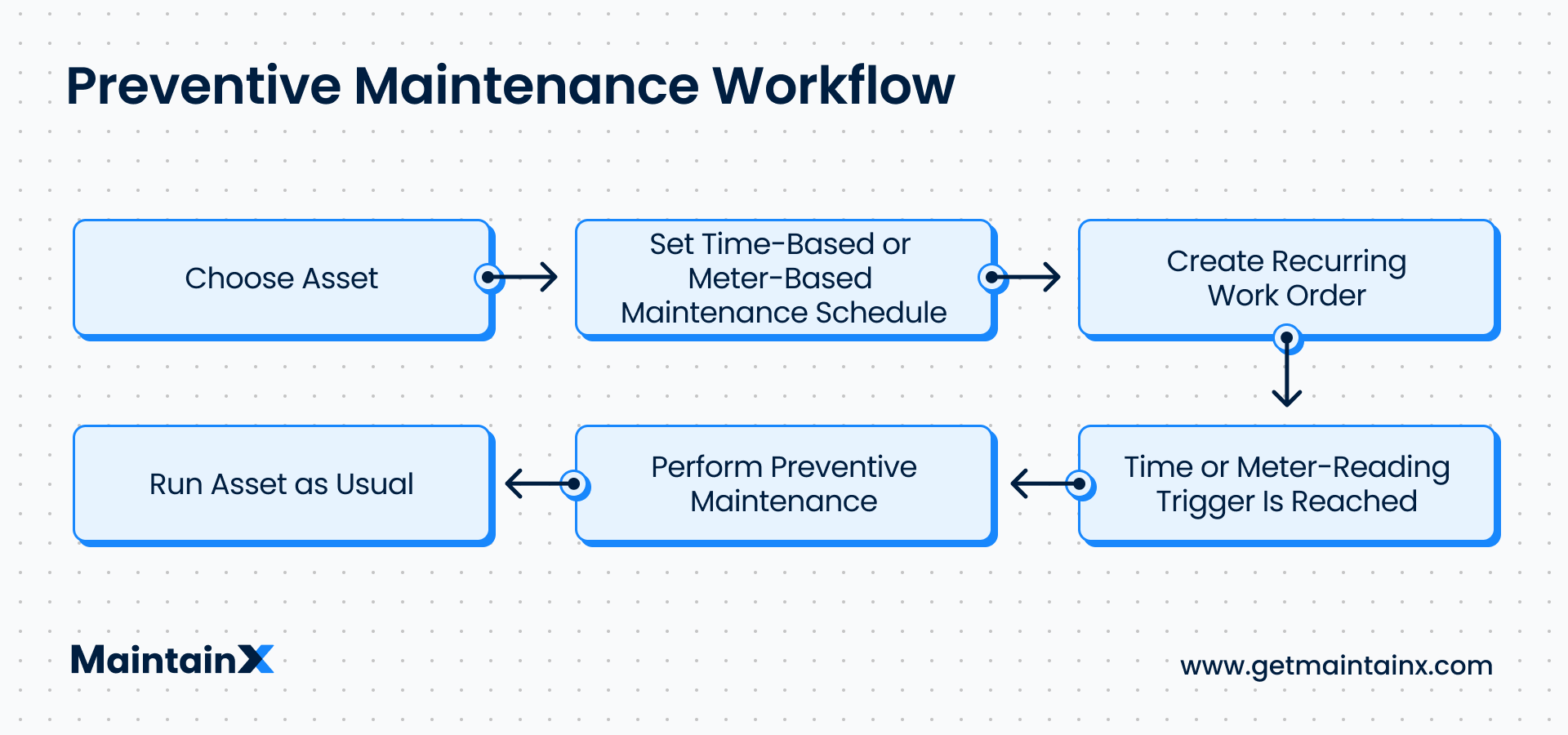
Another form of preventive maintenance is predictive maintenance, which takes multiple forms. Predictive maintenance focuses on identifying imminent breakdowns and timing maintenance activities to occur just before.
This approach helps teams direct maintenance efforts where they are most necessary and when. Predictive maintenance includes condition-based maintenance, reliability-based maintenance, and more. It uses sensors powered by Internet of Things (IoT) technology to monitor asset performance via methods like vibration analysis, sound analysis, and more.
Preventive Maintenance vs. Reactive Maintenance
The benefits of using preventive maintenance over reactive maintenance include:
Saves Time
On the one hand, preventive maintenance can seem like a waste of effort. If an asset is working fine or appears to be working fine, why bother trying to repair problems you can’t see? It might seem like it makes more sense to run the asset until it fails and develops a problem, at which point you can then use reactive maintenance to fix it.
The thing is, preventive maintenance, if done well, makes sure these problems don’t take place to begin with. Taking five minutes every week to regularly lubricate a particular asset can prevent something from breaking, which would require much more than all the time you would have spent on lubricating combined.
On top of this, you can’t exactly control when breakdowns happen. If they occur at inopportune times, you might prolong easily avoidable unplanned downtime.
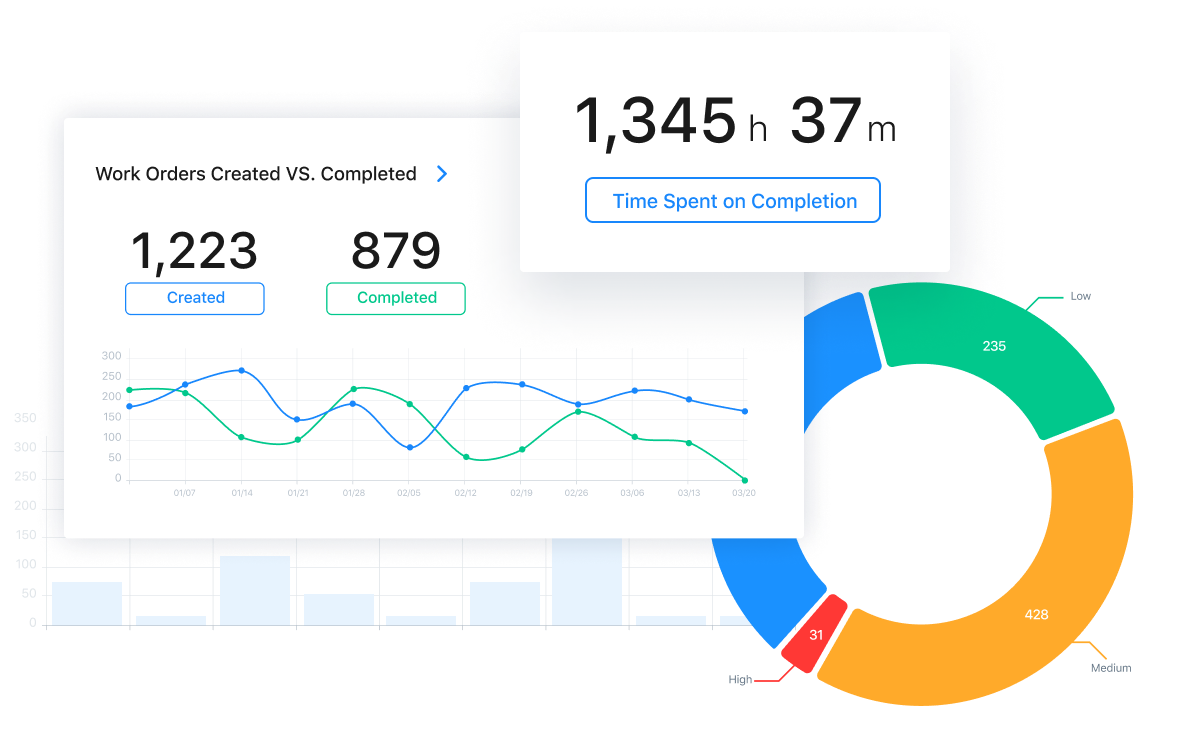
Saves Money
By extension, spending less time fixing a problem will likely mean less money spent on corrective maintenance efforts. However, the cost-effectiveness of preventive maintenance is also a function of increasing your uptime.
First of all, you’ll have fewer members of staff spending time trying to get assets back up and running, which means more staff available for the actual production work.
Second, proper equipment maintenance and asset management means they’re available longer to produce the goods they’re supposed to. In addition to this, regular maintenance activities make it more likely that you’ll identify problems when they are still small and might require much cheaper fixes than they would on developing into significant problems, thus reducing your maintenance costs. Preventive maintenance thus helps you spend less and bring in more money.
Prolongs Asset Life
By regularly maintaining your assets properly, you increase the likelihood that you can manage or prevent problems that might threaten their lifecycle. Increasing your asset life also means you’re less likely to spend money on replacing your assets or machines.
Optimizes Work Force
Preventive maintenance helps make the best use of your workforce as, instead of running around trying to fix emergency problems, reduced downtime means that your technicians can dedicate their best efforts toward the actual work of production and manufacturing. Your maintenance teams will also be able to plan better and use their time more effectively.
CMMS Software in Preventive Maintenance
Benefits of a CMMS in preventive maintenance include:
Optimizes Work Order Management
CMMS implementation allows you to manage your work order process by organizing everything in one place. Instead of dealing with spreadsheets or pen and paper work requests and instructions, you can manage these via the app. You create and assign maintenance work orders in one place.
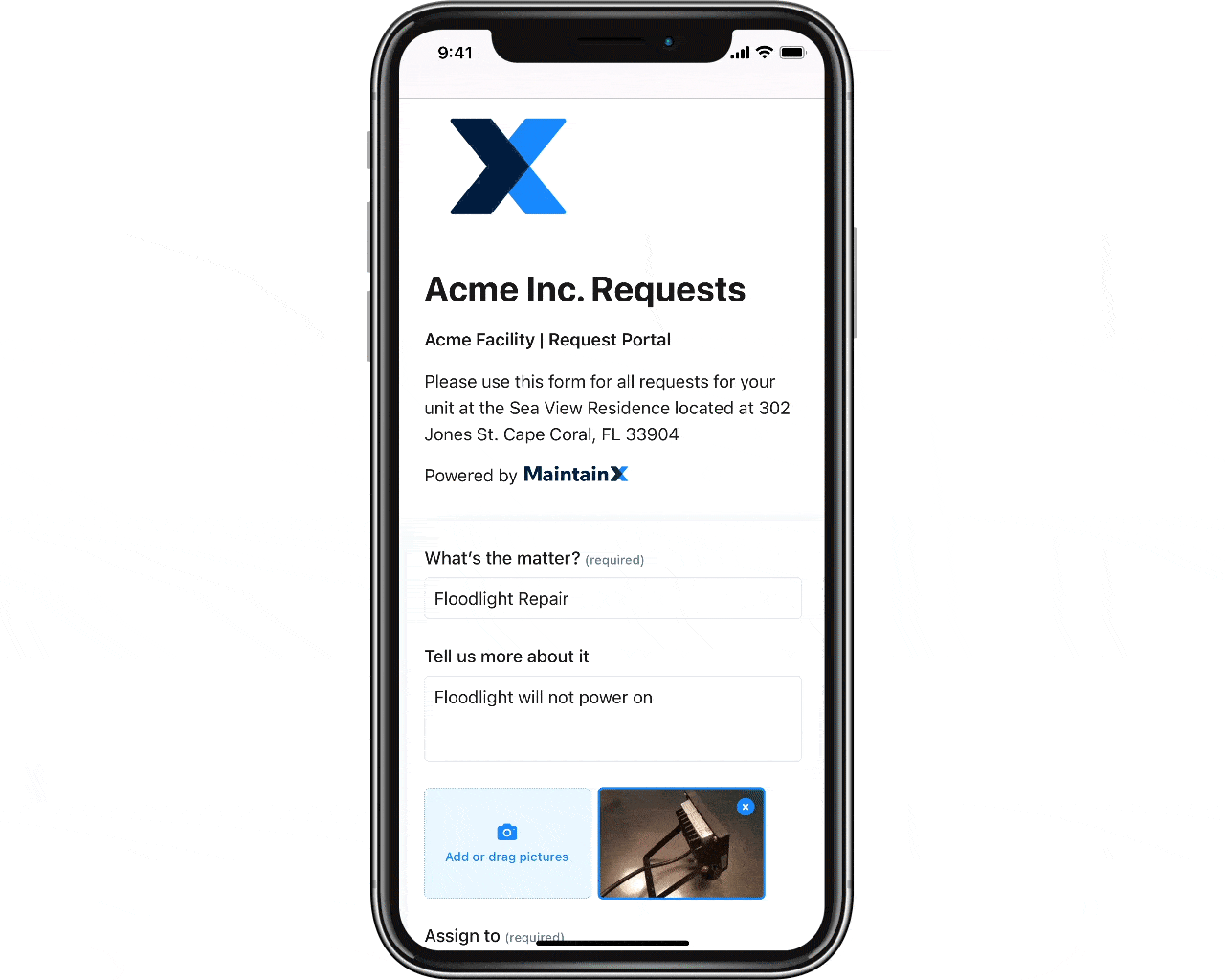
You can also track the work orders and get real-time updates from the shop floor. You can see when a technician gets started on a task, how far along they are, and communicate with them about any challenges they might face.
Simplifies Inventory Management
Computerized Maintenance Management Software can also help you monitor your parts inventory, ensuring you always have spare parts on hand for your maintenance activities. Tracking your inventory ensures that a lack of spare parts or equipment doesn’t disrupt your asset maintenance.
Doing this improves your equipment’s lifespan overall. CMMS apps on mobile devices also simplify data entry for inventory management. For example, instead of manually logging any piece of equipment they take out of inventory, maintenance department workers only need to scan barcodes with their mobile app and automatically update the central records.
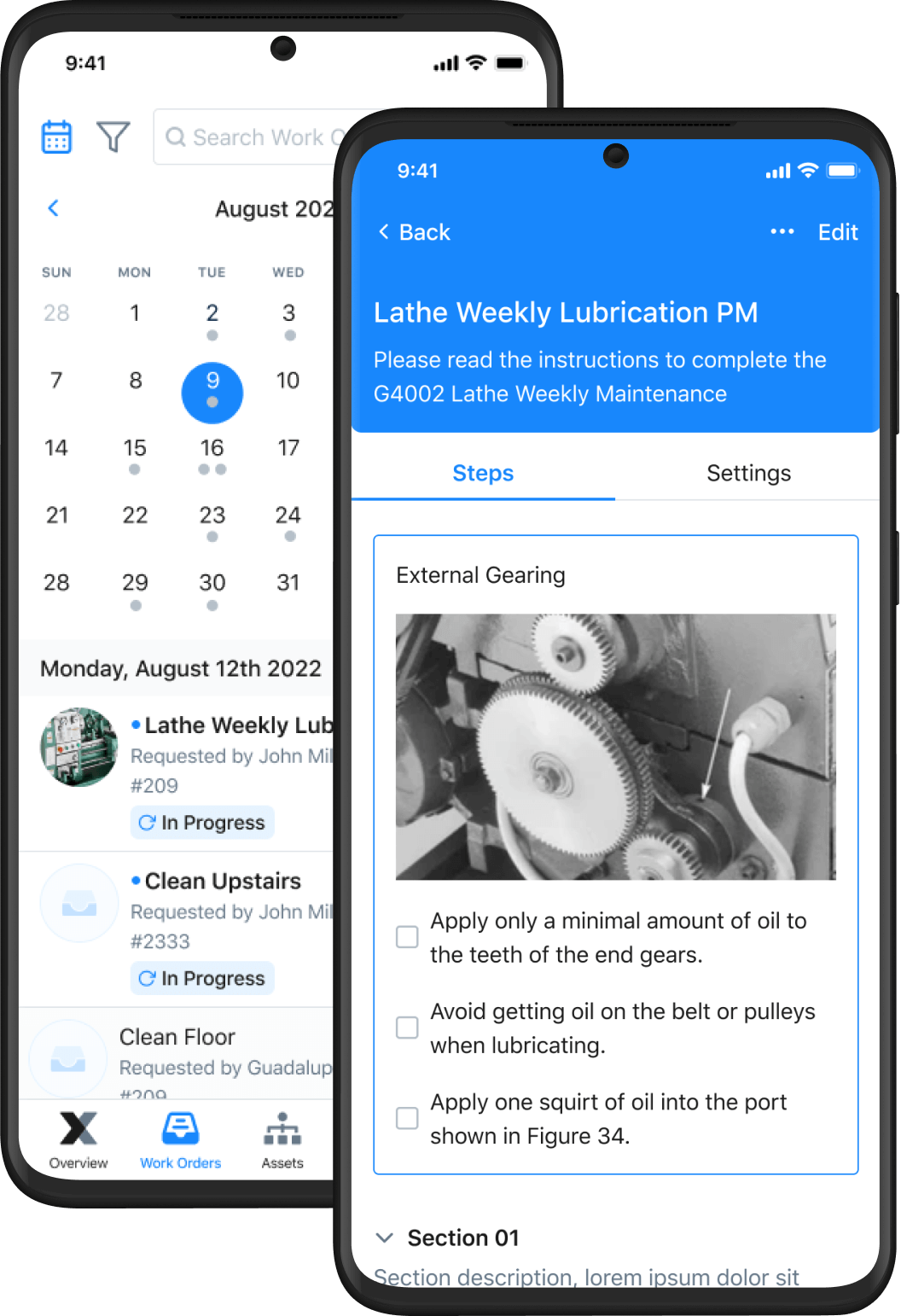
Enables Maintenance Automation
You can automate preventive maintenance schedules using good maintenance management software. MaintainX, for example, allows you to create repeatable work orders in advance. The assigned technician will receive notifications when the time for the preventive maintenance task comes. This system simplifies your maintenance workflows and eliminates the potential for error.
Maintains Audit Trails
Implementing A CMMS system also helps you maintain audit trails for all your activities. Instead of communicating your preventive maintenance plan verbally, doing this via a CMMS helps teams ensure they document all communication. Also, CMMS apps can allow you to create work orders as checklists.
MaintainX, for example, will enable you to develop detailed instructions, templates, and checklists for any activities. If anything goes wrong, you have your maintenance history stored, giving you a straightforward way of checking where the problem stems from. This maintenance process also helps ensure you stay in regulatory compliance.
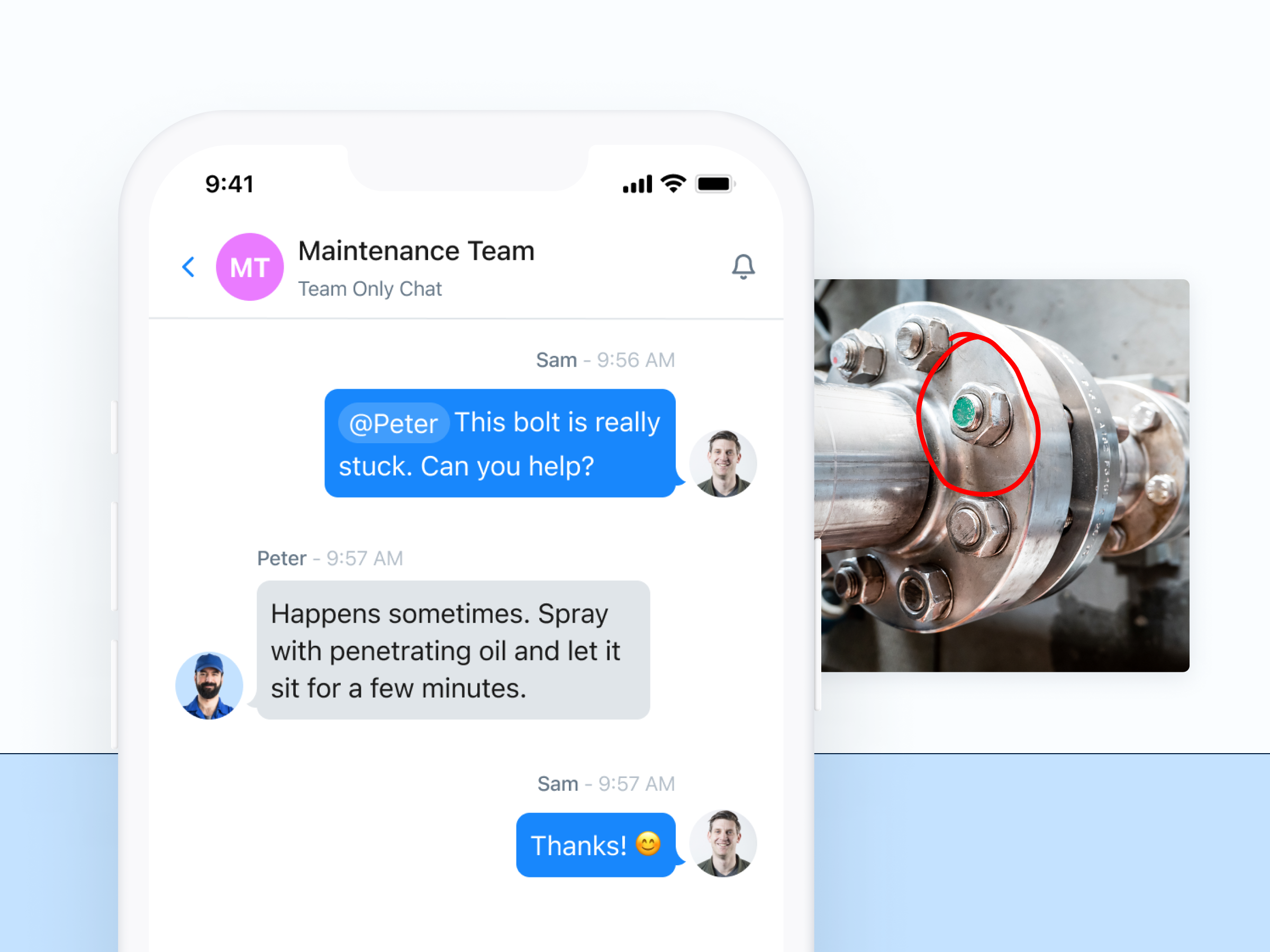
Facilitates Instant Communication
The best CMMS providers also offer instant chat functionality, allowing teams to communicate and share relevant information individually or within groups. Not only is this essential for ensuring team members can reach out when they want to, but it also ensures you have an information trail that exists if you ever need to verify communications.
Get Started with MaintainX Preventive Maintenance
MaintainX is a CMMS solution with functionality for preventive maintenance scheduling, automated work orders, cloud-based storage, real-time updates, and instant chat.
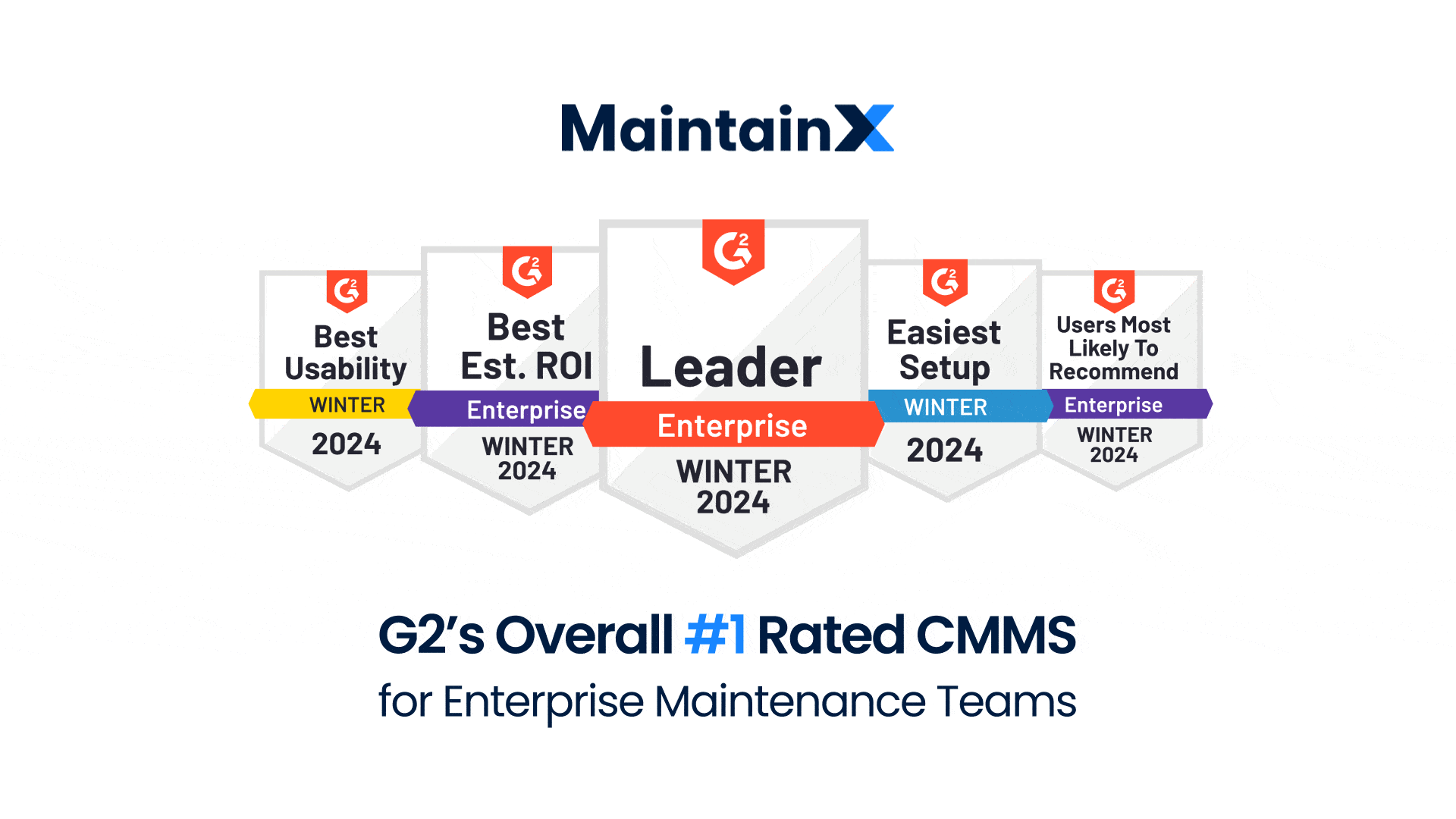
With MaintainX asset tracking features, you can track your KPIs and metrics, using the resulting data to optimize your maintenance planning. MaintainX also comes with reporting dashboards that generate actionable insights to inform your decision-making about your maintenance strategies.
Are you looking to take your preventive maintenance program to the next level? MaintainX is available as both a user-friendly web-based and mobile program, offering you support no matter your maintenance needs. Try MaintainX today!
FAQs
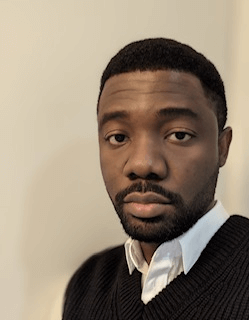
Lekan Olanrewaju is a content writer with years of experience in media and content creation. He has held positions at various media organizations, working with and leading teams at print magazines, digital publications, and television productions.