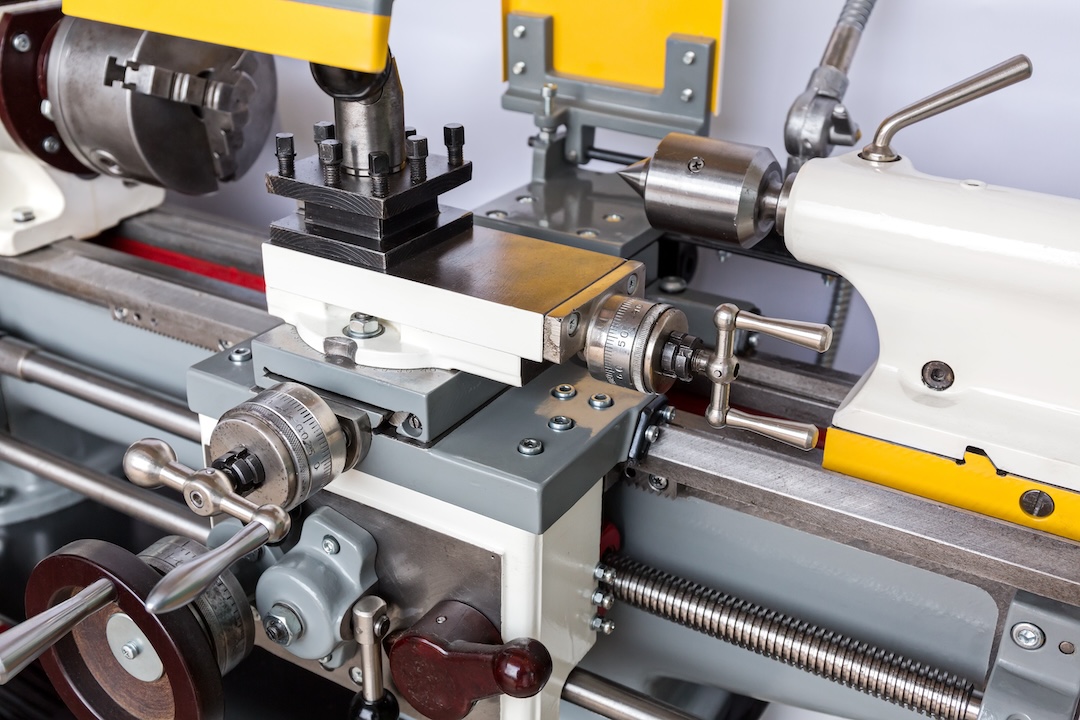
If you’ve been dealing with rising manufacturing costs, you’re not alone. But what if you’ve been looking in the wrong place this whole time? With labor costs and raw materials on everyone’s radar, there’s a problem many aren't seeing: poor asset management.
Inefficient asset management can reduce overall equipment effectiveness (OEE) by up to 13%, directly affecting profitability.
The good news? Enterprise Asset Management (EAM)—a powerful approach that can optimize operations and boost your bottom line. And while EAM implementation can be a bumpy ride for unprepared teams, the right approach will set you on the path to a more efficient, profitable future.
In this article, we'll share our roadmap for EAM success, with proven strategies to help you navigate the complexities, maximize its benefits, and accelerate your journey to improved ROI.
CMMS vs. EAM: What’s the difference, and why does it matter?
First, let’s get on the same page about the difference between EAM systems and Computerized Maintenance Management Systems (CMMS). While both types of software are important in properly executing asset management, they serve different purposes and offer unique benefits.
A CMMS primarily focuses on execution—like scheduling, tracking, and managing maintenance activities—and helps ensure that day-to-day operations run smoothly. It provides immediate value by optimizing maintenance processes and ensuring your team can complete tasks efficiently. For example, a maintenance technician might use a CMMS to view their daily work orders, record completed tasks, and request spare parts from inventory. A maintenance manager could use the CMMS to assign work, track team performance, and generate reports on maintenance costs and equipment reliability.
On the other hand, EAM systems take a broader approach, focusing on the entire lifecycle of assets. An EAM software integrates financial elements, compliance, and strategic planning. It provides a comprehensive view of asset management beyond just maintenance. A plant manager, for example, might leverage an EAM system to make data-driven decisions about asset investments, balancing capital costs against operating costs. A financial controller could rely on the EAM to accurately calculate asset depreciation and plan for replacements.
Three pillars of successful EAM implementation
Implementing EAM successfully is not just about choosing the right software; it's about strategically integrating it into your operations. To help you navigate this complex process, we've identified the following key pillars for maximizing the value of your EAM investment.
1. Start small, scale smart
One mistake companies make is trying to implement EAM across their entire operation at once. However, it’s not the best time to adopt the “go big or go home approach.” Starting small is the best way to avoid overwhelming your operations and overrunning your budget.
Our tip? Begin with a pilot project—whether it’s a single site or a specific asset class. Apply a phased approach that allows you to test the waters, identify issues, and refine your strategy without too much risk.
By starting small, you can also demonstrate quick wins and build momentum. Introducing any new system can lead to skepticism from some team members, but with initial successes, you can address that. You’ll be able to secure buy-in from your team and stakeholders, showing them the tangible benefits of EAM. Once you’ve ironed out the kinks and proven the value, you’ll be in a stronger position to expand EAM across your organization.
2. Prioritize interoperability
An EAM won’t work in isolation. To truly unlock its potential, you need to ensure it integrates seamlessly with your other systems—from your Enterprise Resource Planning (ERP) system to your Internet of Things (IoT) systems. When choosing an EAM solution, prioritize:
- Open architectures
- API capabilities
- ERP, Supervisory Control and Data Acquisition (SCADA), IoT, and Manufacturing Execution System (MES) integrations
Remember, the goal is to create a single source of truth for all your asset-related data. Interoperability isn't just a technical requirement—it's the key to making data-driven decisions across your entire operation.
3. Simplify user adoption
Ultimately, success with an EAM is not just about the software; it’s about embedding EAM into your maintenance culture. As such, if your team isn’t fully on board with the system, the EAM will have little to offer you. If they aren’t using it properly, you might make decisions based on inaccurate data, which might cause more harm than good.
Ensure you get buy-in from all levels, and make EAM a natural part of how your business operates, not just another tech project. Key strategies for boosting user adoption include:
- Involving end-users in the selection and implementation process
- Providing comprehensive, role-specific training
- Selecting solutions with intuitive user interfaces that match workflow
- Celebrating early wins to build momentum
Measuring EAM success
Implementing an Enterprise Asset Management (EAM) system is just the start. To keep things on track, you need to keep an eye on the right metrics to identify challenges, track success, and make data-driven decisions about how to improve. Here are some key metrics to watch:
- Overall Equipment Effectiveness (OEE): OEE tells you how well your equipment is performing by looking at availability, performance, and quality. A high OEE means your equipment is running smoothly and efficiently.
- Mean Time Between Failures (MTBF): MTBF measures how often repairable equipment breaks down on average. Longer MTBF means your maintenance functions properly and your equipment is reliable.
- Planned Maintenance Percentage (PMP): PMP tells you what fraction of your maintenance work is planned rather than reactive. A higher PMP means you're ahead of the game, avoiding surprise breakdowns.
- Asset Uptime: This tracks how much time your equipment runs versus being out of service. More uptime means more productivity and less downtime.
Consider the case of Titan America, a leading manufacturer of heavy building materials. By implementing a modern CMMS solution and integrating it with their ERP system, Titan America reduced unplanned maintenance by 30%. Titan’s strong CMMS foundation with MaintainX was crucial in enabling its EAM initiatives.
EAM: Your roadmap to ROI
Think of EAM as a marathon, not a sprint. It’s all about continuous improvement instead of a quick fix. To really make EAM work for you, start with the basics—take small, deliberate steps. Once you've got that down, focus on making sure everything works seamlessly together and that your team is fully on board.
Yes, implementing EAM will need some investment and a bit of a shake-up in how you do things, but the rewards are huge. With rising costs and tight competition, optimizing your assets isn’t just a nice-to-have—it’s essential. By taking the right steps today, you won’t just be able to survive today’s business challenges, you’ll be setting the stage to take your business to the next level and enjoy efficiency and ROI gains.
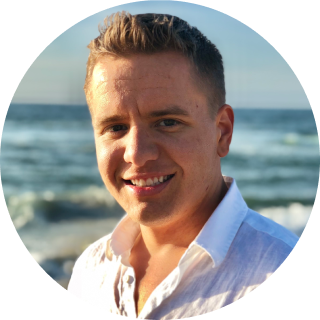
Nick Haase is a co-founder for MaintainX and is responsible for designing and leading the go-to-market strategies. He is a subject-matter expert in emerging CMMS technologies.