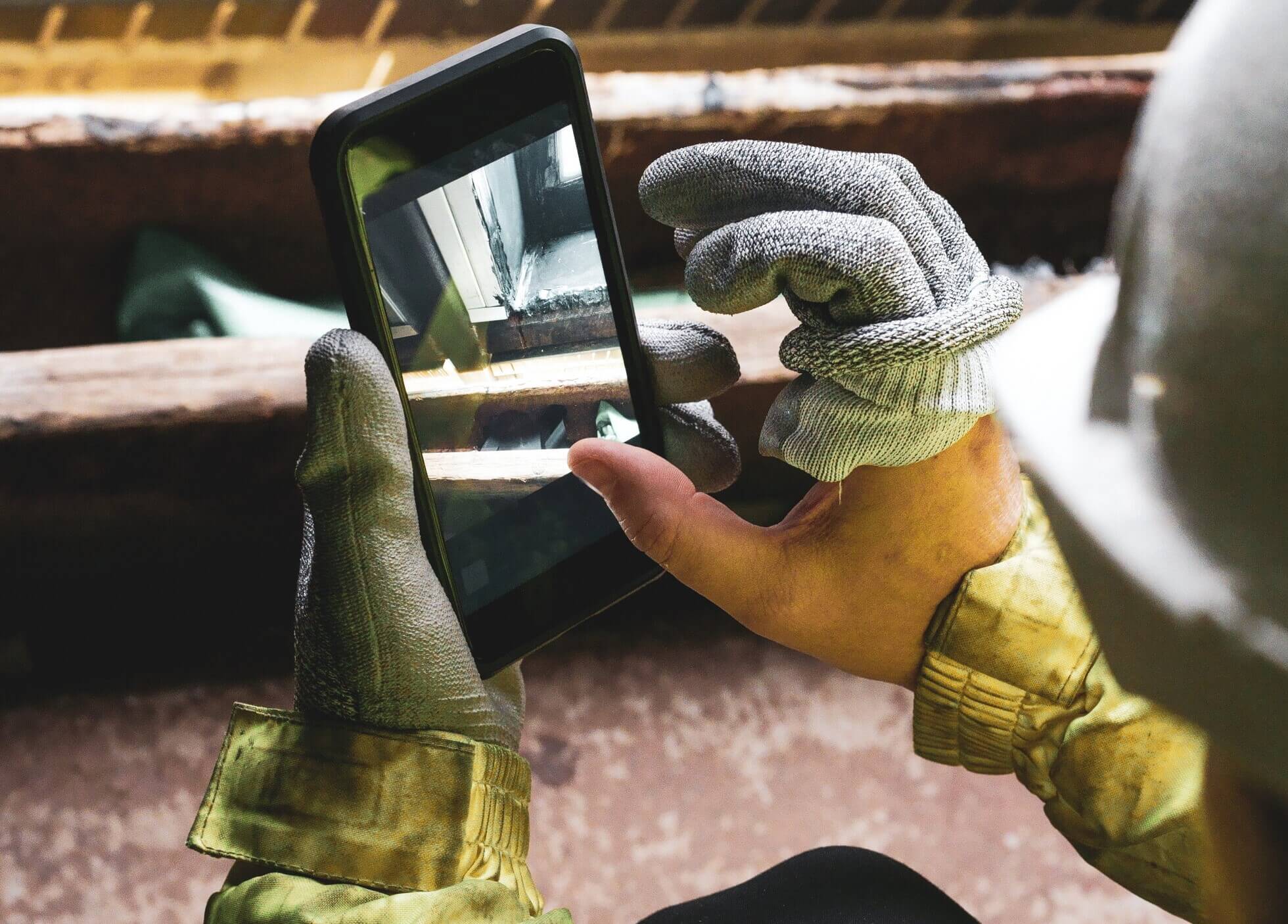
Maintenance management is a crucial aspect of keeping operations running smoothly, whether you're overseeing a manufacturing plant, a fleet of vehicles, or a network of facilities. It’s about way more than just fixing things when they break. Maintenance management is about your overall approach to maintenance, whether it's preventing breakdowns from taking place at all or preparing to handle them when they do. With effective maintenance management, you’ll be able to not only reduce downtime but also extend the useful life of your assets and optimize your spending.
With the rise of digital solutions, the market is now flooded with maintenance management software options, each promising to improve efficiency and reduce costs. However, not all software is created equal, and choosing the wrong one can lead to wasted resources, frustrated teams, and unresolved issues. Navigating this crowded market to find the right fit for your organization is key to achieving streamlined operations and a healthier bottom line.
Here, we explore the top maintenance management software options in the market and guide you through the steps to select the one that makes the most sense for you. You’ll be equipped with the knowledge you need to make a choice that helps you optimize your resources, keep your team running smoothly, and handle any issues.
What is maintenance management software?
Maintenance management software enables users to streamline their maintenance processes with functions like preventive maintenance scheduling, asset performance tracking, work order tracking, reporting, and more. When used properly, maintenance management software can help teams reduce downtime, maintain accurate records, and optimize maintenance schedules. By centralizing and automating these tasks, organizations can make more informed decisions, improve productivity, and save on maintenance costs.
Top 7 maintenance management & scheduling solutions
If you’re in the market for maintenance management software, you’ll find a plethora of options to choose from. Don’t be intimidated, though. Sure, it can be difficult to know where to begin, but we’ve put together a list of the top seven maintenance management solutions out there today. Let’s dive in.
1. MaintainX
Overview
MaintainX offers a mobile-first, user-friendly platform for managing maintenance operations. It includes features for digital work orders, asset management, inventory management, real-time reporting and analytics. It also offers the best technician experience, making it easier to record and complete work. With expert implementation services, MaintainX also offers the fastest time-to-value on the market.
Key strengths
- Ease of use
- Mobile-first functionality
- AI-powered workflows
- Real-time reporting and insights
- 24/7 support
- Seamless integration with other systems, like SAP
2. UpKeep
Overview
UpKeep is a mobile-first CMMS solution designed to help maintenance teams improve their efficiency. It offers work order management, preventive maintenance scheduling, asset management, and reporting features.
Key strengths
- Strong mobile capabilities
- Preventive maintenance scheduling
- Work order management
- User-friendly interface
3. Fiix
Overview
Fiix is a cloud-based CMMS that helps organizations manage their maintenance operations through work order management, preventive maintenance, asset management, and powerful analytics.
Key strengths
- Integration with IoT devices
- Preventive maintenance scheduling
- AI-powered insights
4. eMaint
Overview
eMaint, part of Fluke Corporation, provides a versatile CMMS platform that supports work order management, preventive maintenance, asset tracking, and inventory management.
Key strengths
- Customizable interface
- Reporting capabilities
- Strong integration options
5. Hippo CMMS
Overview
Hippo CMMS is known for its simple and intuitive interface. It offers features for work order management, preventive maintenance, asset management, and inventory control.
Key strengths
- Easy implementation
- Strong customer support
- Cost-effective for small to mid-sized businesses
6. Limble CMMS
Overview
Limble CMMS is designed to streamline maintenance operations with features such as work order management, preventive maintenance scheduling, asset management, and real-time reporting.
Key strengths
- User-friendly design
- Robust mobile app
- Strong customer support
7. ManagerPlus
Overview
ManagerPlus, part of iOFFICE, offers a comprehensive maintenance management solution with features for work order management, preventive maintenance, asset tracking, and analytics.
Key strengths
- Integration with other business systems
- Powerful reporting tools
- Scalability for large enterprises
Case Study: SanTan Brewing Co. uses MaintainX to open up maintenance management
How to choose the best maintenance management system for your needs
Even with the options narrowed down, it can be tricky to figure out which system makes the most sense for you. The important thing to note is that there’s no one-size-fits-all approach. The best option for you will depend on your unique situation and needs. With that in mind, we’ve put together a structured approach you can apply to evaluate the maintenance management software options on the market.
Understand your needs & objectives
Before anything else, you should get answers to some key questions. What problems are you looking to solve with maintenance management software? Do you want to reduce downtime? Or would you also like to facilitate remote collaboration between your team members? Do you need reporting features? Establishing your priorities beforehand will help you focus on the features that matter most.
Prioritize ease-of-use
Whatever you settle on, you want to ensure that your team can make a smooth transition. Difficult-to-use software will only extend your team’s learning curve and likely reduce user adoption, which goes against the whole point of acquiring the software to begin with.
Seek integration with existing systems
The best maintenance management software should seamlessly integrate with your current systems, such as enterprise resource planning (ERP) systems, inventory management, and production scheduling tools. This connectivity helps streamline operations and prevents data silos, giving you a complete view of your maintenance activities.
Consider the total cost of ownership
The initial purchase is one thing, but software solutions often come with long-term costs covering implementation, training, support, upgrades, and more. Understanding the total cost of ownership helps you avoid unexpected expenses and ensures the solution fits your budget over the long term.
Investigate vendor reputation and innovation
Choose a software provider with a strong track record in the industry and a commitment to continuous improvement. Seek out customer reviews on app marketplaces and third-party review sites like G2. Look for vendors that are known for reliability, customer support, and innovation, as these qualities will help ensure your system evolves with your needs.
Evaluate scalability and flexibility
As your business grows, you want to ensure that you don’t need to head back into the market looking for a new software to meet your needs. Make sure the software you choose can grow with your business and adapt to changing needs. A scalable and flexible solution will allow you to add new users, assets, or functionalities without a complete system overhaul, ensuring it remains relevant as your operations expand.
Maintenance management software done right with MaintainX’s CMMS
MaintainX is a CMMS that offers a range of features to streamline your operations and processes. Optimize your resources and streamline your maintenance management with:
Digital work orders
- Create and assign work orders in a centralized platform.
- Address one-off work requests.
- Track maintenance tasks and share real-time updates directly from the floor.
- Capture work order data more easily with pre-filled templates, time tracking, signatures, and required fields.
Maintenance scheduling
- Schedule preventive maintenance tasks in advance.
- Use automated reminders and recurring work orders to ensure technicians perform maintenance on time.
- Use workload-based scheduling with labor insights to assign work according to staff capacity.
- Schedule maintenance based on meter readings.
AI-powered workflows
- Create better SOPs faster with an AI-powered procedure generation.
- Minimize human error with AI-powered anomaly detection.
- Capture more work order data by recording voice memos and letting AI transcribe them.
Asset & equipment management
- Track asset performance, status, and history.
- Improve reliability across sites with data-driven asset insights.
- Access full maintenance logs for each asset.
- Scan barcodes and QR codes to pull up the right assets in the field and instantly see all their history.
Parts inventory management
- Get real-time visibility into inventory levels.
- Easily view and share parts inventory across your facilities.
- Create automated alerts for low stock and reorder on time.
- Manage vendor data in one centralized location.
- Keep track of parts with barcodes and QR codes.
- Reduce carrying costs by using data-driven insights to order only what you need.
Maintenance management software FAQs
What are the benefits of property maintenance management software?
Property maintenance management software helps streamline maintenance tasks, improve tenant satisfaction, reduce response times, and ensure regular upkeep, ultimately saving time and reducing costs for property managers.
Which is the best handyman scheduling software?
The best handyman scheduling software depends on your specific needs, but popular options include Jobber, Housecall Pro, and ServiceTitan, which offer features like scheduling, invoicing, and customer management.
What is the best aviation maintenance software?
The best aviation maintenance software varies by organization, but leading solutions include Aviation InterTec’s RAAS, WinAir, and AMOS, which provide robust tools for compliance, inventory management, and maintenance tracking.
How do I choose the right equipment maintenance software?
To choose the right equipment maintenance software, assess your specific maintenance needs, consider ease of use, ensure compatibility with existing systems, and evaluate the total cost of ownership and vendor support.
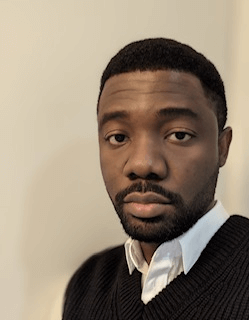
Lekan Olanrewaju is a content writer with years of experience in media and content creation. He has held positions at various media organizations, working with and leading teams at print magazines, digital publications, and television productions.