Schedule compliance is a maintenance performance metric that O&M managers use to determine the effectiveness of scheduled tasks. It measures the percentage of completed work orders before their given due dates over a given period.
What Is Schedule Compliance?
Schedule compliance is one way to illustrate how successful maintenance teams are in completing preventive maintenance (PM) tasks as planned. Maintenance experts consider the world-class standard for the measure to be 90 percent.
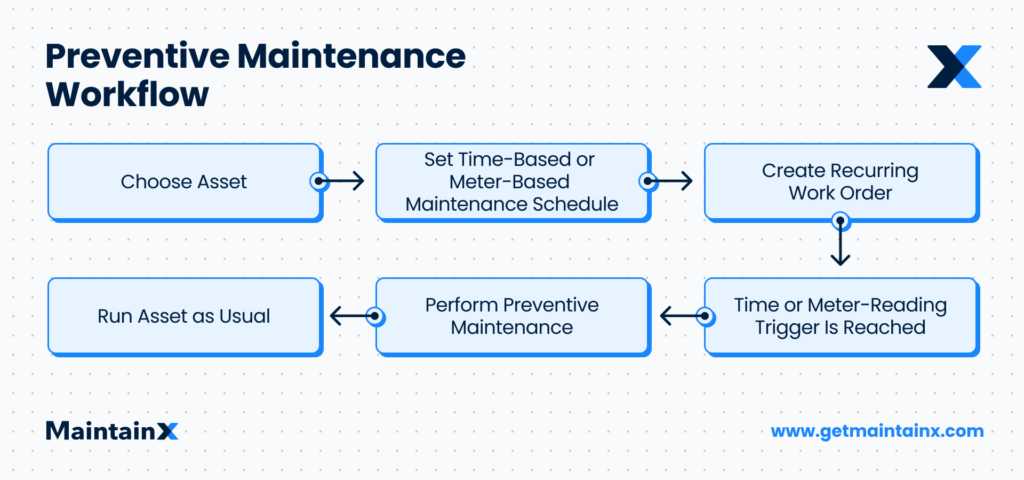
This key performance indicator (KPI), also referred to as PM compliance, compares actual work order completion dates to suggested completion dates. Periodically calculating schedule compliance is an excellent way to gauge overall maintenance productivity effectiveness.
Managers often schedule PM activities to be completed weekly, monthly, or annually. However, PM intervals can also vary according to the manufacturer’s recommendations, work environments, and equipment usage metrics. The key to running a successful PM program is to create a formal process to track, review, and investigate maintenance KPIs regularly.
This process can reveal fresh insights into workflow bottlenecks, opportunities for PM scheduling improvements, and O&M spending patterns. Meeting targets is especially crucial to maintain the reliability, functionality, and useful life of critical assets. Why?
Because extended downtimes can adversely impact company profits, brand reputations, and, in some cases, even employee safety. Critical assets include the pieces of equipment most integral to meeting goals and those most expensive to repair and replace.
How to Calculate Schedule Compliance
Divide your total number of completed PMs by your total number of PMs within a given period. Then, multiply the result by 100 to calculate your percentage.
Schedule Compliance Formula:
PM Compliance = (# of completed tasks ÷ number of scheduled tasks) × 100
Example:
You scheduled 200 maintenance tasks in the last three months. Your team completed 165 of them after factoring in the 10 percent rule (scroll down to learn about this important caveat):
Schedule compliance = (165 completed tasks ÷ 200 scheduled tasks)
= 0.825 x 100
= 82.5%
NOTE: Schedule compliance only takes note of PM assignments. Don’t include reactive or emergency maintenance tasks in your calculations.
Challenges Calculating Schedule Compliance
The goal of tracking schedule compliance is to ensure PM activities are completed on time. Delayed work orders are as bad as missed maintenance tasks because they defeat the purpose of practicing PM—to reduce the likelihood of unplanned downtime.
The more deadlines technicians miss, the higher the chance of emergency maintenance. One of the pitfalls for organizations that rely upon schedule compliance to measure overall PM program effectiveness is that the calculation doesn’t factor in late work order fulfillment.
Translation: uncounted delayed tasks may contribute to a false sense of confidence. For example, say a worker completes a PM 10 days after the 60th-day initial deadline. Let’s also assume management measures schedule compliance over a three-month period.
In this situation, the completed PM will contribute to a favorable score despite missing the original deadline. This is where the “10 Percent Rule” comes in.
The 10 Percent Rule
Maintenance experts recommend marking tasks “schedule compliant” if they have been completed within a 10 percent timeframe of their scheduled maintenance intervals.
For example, the task above would have been considered compliant were it completed within six days of its original due date. In other words, the maintenance technician would have completed the PM by the 66th day to be considered compliant.
The 10 Percent Rule is an effective method to avoid including late PMs in final schedule compliance calculations to ensure accurate program evaluations.
Schedule Compliance Red Flags
Most maintenance managers use schedule compliance as a KPI for their maintenance crews. But that doesn’t mean it isn’t routinely misinterpreted.
For example, managers sometimes assume that a low percentage means an essential unscheduled task interrupted their PM schedule. However, other factors such as employee absences and poorly planned maintenance tasks—that require significantly less or more time than anticipated—can also affect the KPI.
Common Schedule Compliance Misinterpretations, Misuses, and Abuses:
- Delayed Emergency Maintenance: Equipment problems that pose safety hazards or severely impact productivity should always be a top priority. Busy maintenance teams should always complete these work orders first, scheduled or not.
- Task Time Over-Estimation: This happens when maintenance schedulers purposefully overestimate time frames to raise rates. The practice causes teams to fall behind on PMs by overly focusing on schedule compliance.
- Lack of Strategy: Schedule compliance is sometimes reported as a single number without meaningful recommendations for remedying low results. Some maintenance departments end up scheduling less work to improve their rates.
Though unlikely, over-emphasizing schedule compliance can have negative consequences on maintenance efforts. For this reason, it’s important that team leaders thoroughly understand the scope of each work order, along with identifying process improvements.
Tips to Improve Schedule Compliance
Low rates are usually an indicator of underlying maintenance department issues. Here are a few tips to improve your program:
- Audit Unnecessary Maintenance Tasks: Regularly review PM processes to identify redundant tasks that waste resources. Eliminating unnecessary tasks will boost schedule compliance and save time, capital, and effort.
- Make PMs Easier to Complete: A common cause of low PM compliance is limited O&M resources. Improve schedule compliance by making PM tasks easier and faster to complete. Providing better training, access to resources, and improved troubleshooting procedures will help technicians complete their assignments faster.
- Address Backlogs: Track your organization’s scheduled maintenance critical percent (SMCP) to help prioritize and clear backlog assignments. This KPI helps determine which delayed tasks should be given priority.
- Analyze Results and Trends: Analyze KPI trends to identify the root causes of low schedule compliance. Involve your team in the discussion for more significant insights.
- Integrate a CMMS maintenance software: A CMMS like MaintainX helps automate maintenance preventive maintenance workflows and provides advanced key performance metrics to help analyze your results and trends.
Finally, you may want to assess your maintenance team’s culture, capabilities, and processes. Do you have standard operating procedures in place?
If so, are they clear, realistic, and accessible? Your entire team should feel confident approaching each assignment.
Get MaintainX for Your Schedule Compliance
We recommend implementing mobile-friendly work order software that your technicians will enjoy interacting with daily. Schedule compliance is a popular maintenance KPI that compares actual work order completion dates to suggested completion dates. The world-class standard is 90 percent, but such exemplary results aren’t achieved overnight. Aim to continually improve schedule compliance, and you will reduce equipment downtime, increase productivity, and enhance overall O&M program effectiveness.
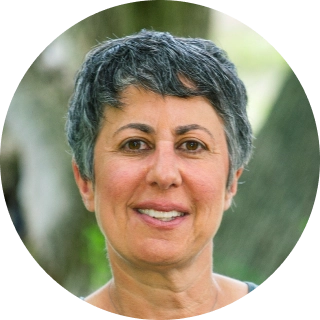
Caroline Eisner
Caroline Eisner is a writer and editor with experience across the profit and nonprofit sectors, government, education, and financial organizations. She has held leadership positions in K16 institutions and has led large-scale digital projects, interactive websites, and a business writing consultancy.
See MaintainX in action