Lean manufacturing is a concept based on eliminating waste in all its forms and creating a cycle of continuous improvement. Often these days you may hear the phrase, “Shine, standardize, and sustain”–shorthand for the 5s Lean Process.
Many different Lean concepts have arisen over the past few years, as the popularity of this Japanese approach to efficiency spread through the manufacturing sector. The original core idea of 5s, however, centered on five improvement principles.
Robust CMMS software is designed to make it easy to centralize and disseminate maintenance and repair information and can easily be used as a Lean 5s management tool. Using a CMMS like MaintainX helps streamline process improvement by providing a centralized platform to digitize, assign, and manage standard operating procedures–including your very own 5s.
What Is the 5s Lean Process in Manufacturing?
5s is simply an abbreviation of the five standards for improvement:
- Sort
- Set in order
- Shine
- Standardize
- Sustain
Let’s look at each of the 5s standards in more detail.
What Are the 5s Standards?
1. Sort
The sorting step in the Lean manufacturing process ensures that unnecessary steps, items, or workflows are removed completely from the process so that only necessary elements remain.
The core of the sort technique is to “remove what is not needed and keep what is needed.”
In a typical manufacturing workflow, this could mean:
- throwing away unnecessary parts and offcuts cluttering the work area,
- eliminating complex multi-step labeling processes, or
- installing better racking to organize components at an assembly station.
The idea is to throw away unnecessary items and ensure everything left behind has a purpose or place. This creates a work environment that provides an overall sense of order and calm which makes workflows more efficient.
Once the work area has been cleared of unnecessary clutter, it’s time to organize what remains.
2. Set in Order
Step 2 of the Lean 5s process is to ensure that there is “a place for everything and everything is in its place.”
Neatly arranging essential items such as tools and equipment allows you to access them easily when you need them. You can go a step further and arrange the items you need to complete a task in the order you will use them.
This may seem to offer fractional efficiency gains at first, but when added up over many repetitions, strategically arranging your workstation can make a quantifiable difference to productivity and other KPIs.
Setting up a work area efficiently means designating the same spot for frequently used items like screws, welding rods, or packaging material. The most commonly used items will be easier to find and use. For shared items like power tools, this step becomes even more important. Having a specific place for a drill–and always putting it back–means anyone on the team can quickly find it when needed.
3. Shine
Successfully implementing the 5s methodology in the workplace requires workers to keep equipment, tools, and work areas clean and neat. The idea is to clean everything thoroughly. Use this step in the process to inspect and identify anything that needs replacing, low parts inventory, or other areas that need attention.
A great way to stay on top of agreed-upon standards for cleanliness is to use a cleaning checklist, especially if different workers use the same workstation.
Remember also that shining isn’t just about sweeping, wiping, and tidying up–although these tasks are critical to maintaining an efficient workspace. “Shine” also includes looking at your work area through the lens of preventive maintenance: ensuring all your equipment is in good working order and lubricating and maintaining machinery is key to a robust 5s approach.
4. Standardize
Standardizing work processes makes it clear when, where, and how to perform the first three S’s. It’s ineffective to sort, order, and clean up a work area only once, which is why a sound 5s system involves creating repeatable activities for this process.
From the Japanese seiketsu, meaning “to standardize,” this step involves using 5s checklists, instructions, signs, labels, and reminders to ensure everyone involved can easily understand and follow the cleaning and organizing processes.
Using a computerized maintenance management system (CMMS) is particularly useful. CMMS allows you to plan scheduled tasks at specific intervals. This could include daily straightening up and cleaning of workspaces, or weekly deep cleaning that includes quick preventive maintenance tasks and checks.
5. Sustain
As with all Lean approaches, 5s is cyclical, not linear. Once you have a working system, keep adjusting and improving each step of the process indefinitely.
Everyone from the management team to the employee completing the task should be involved in managing and maintaining the process to make it truly sustainable.
The entire 5s process should be smooth. Consider implementing 5s training or hanging posters around the shop floor with the 5s principles visible. Scheduling audits or reviews at intervals to identify when tasks or processes need to be updated and to ensure the processes laid out in the initial 5s steps remain relevant.
Benefits of the 5s Process
The goal of 5s activities is to make the workplace as neat and efficient as possible. Unnecessary items, steps, or clutter get cleared away, and the work area is always orderly and free of trash or mess.
Benefits of a 5s system include:
- Reducing waste resulting from poorly organized work areas
- Ensuring tools and parts are always in the right place and ready for use
- Keeping work areas free from clutter, rubbish, and debris that pose potential safety hazards
- Increasing efficiency of individual tasks and manufacturing process as a whole
- Increasing employee engagement–workers can take pride in their work area and can complete tasks without issues
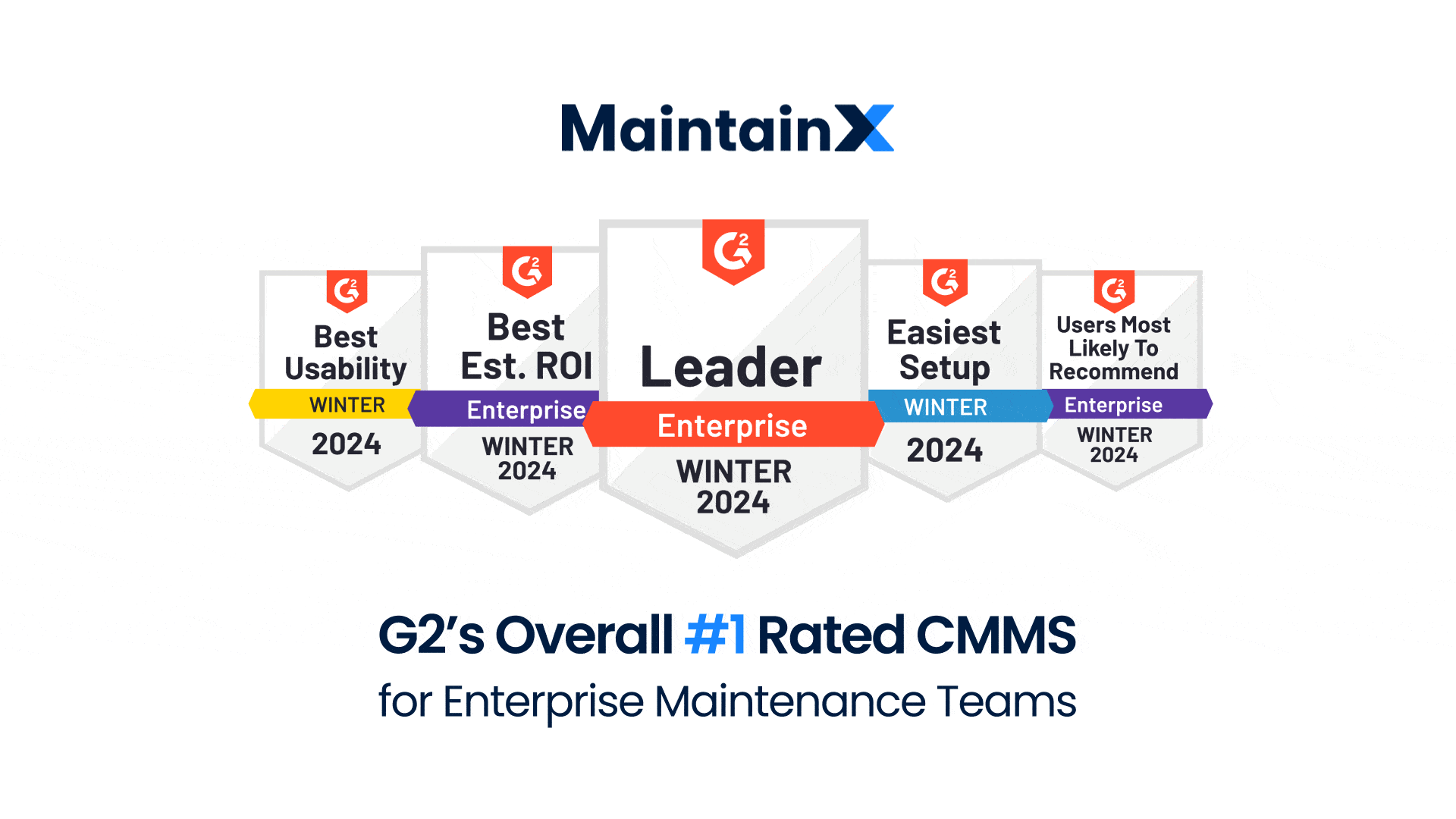
Integrating a 5s Program with a CMMS
While 5s can work as a standalone process, it is much more effective when used alongside other Lean methodologies like Kaizen, Lean Six Sigma, and Gemba.
View the 5s process as a cycle. Because 5s relies on recurring tasks, these tasks need to be documented so that all employees can follow the standard cyclical process. A computerized maintenance management system (CMMS) streamlines process-based tasks, making it ideal for managing 5s processes.
Want to get started with your 5s Lean Process? Check out MaintainX.
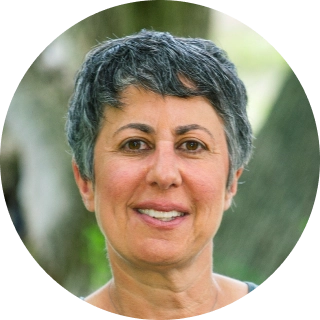
Caroline Eisner
Caroline Eisner is a writer and editor with experience across the profit and nonprofit sectors, government, education, and financial organizations. She has held leadership positions in K16 institutions and has led large-scale digital projects, interactive websites, and a business writing consultancy.
See MaintainX in action