Mean Time Between Failure (MTBF) represents the average uptime between two failure states of a repairable system during its life period.
The MTBF calculation is only used in conjunction with repairable assets, not non-repairable components.
You calculate the metric under the assumption that equipment failure is inevitable. The question isn't if the machinery will break down, but when. The higher the MTBF value, the more likely the equipment operates uninterrupted for an extended period, improving overall equipment effectiveness.
The precise definition of Mean Time Between Failure depends on what gets categorized as a "failure." Most maintenance departments consider critical failures to be completely out-of-service equipment. Non-critical failures or minor malfunctions are not classified as system aborts.
Key takeaways
- MTBF is a foundational reliability metric for repairable systems that helps predict system breakdowns.
- Accurate data collection and well-defined scope are critical to meaningful reliability analysis.
- MTBF analysis helps minimize downtime, optimize maintenance schedules, and plan resources effectively.
- Modern asset management software tools can simplify and standardize tracking MTBF.
- Combine MTBF metrics with other failure metrics like failure rate and overall equipment effectiveness for a complete reliability picture.
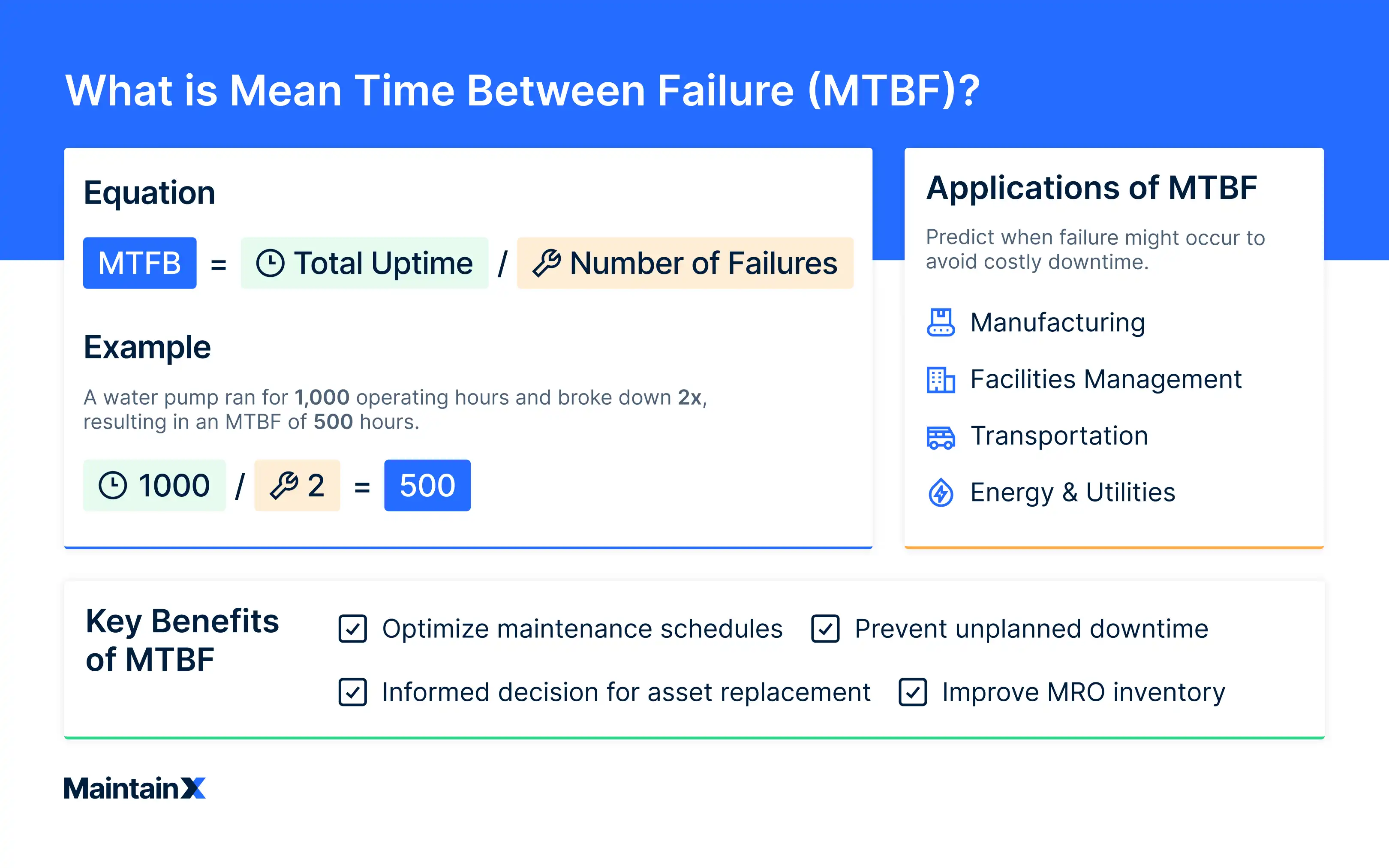
Why use Mean Time Between Failure?
MTBF rates help Operations and Maintenance (O&M) managers anticipate when failure occurs within given periods and transform reactive maintenance into proactive planning. It's often paired with other maintenance practices and key performance indicators (KPIs) like root cause analysis to remedy the original causes of repetitive equipment breakdowns. Instead of scrambling when equipment fails, you can schedule repairs during planned downtime, which saves money, reduces stress on your maintenance team, and keeps operations running smoothly.
Comprehensive preventive maintenance (PM) strategies enable you to implement a proactive maintenance strategy. This lets you reduce unplanned downtime and schedule routine upkeep within brief intervals. This is significantly better than the expensive hour-long shutdowns required during emergency maintenance activities.
Exactly how impactful are MTBF-informed maintenance processes? We're talking about the difference between spending a few hundred dollars in maintenance-related expenses versus hundreds of thousands of dollars in costly downtime and lost production! The cost of downtime for even small and medium-sized manufacturing can be as much as $150,000 per hour.
MTBF supports maintenance departments that execute several tasks, including:
- Optimizing maintenance schedules: MTBF provides a baseline for maximizing PM schedules. This allows leadership to schedule maintenance activities before a component fails so that technicians perform condition-based maintenance only when necessary.
- Improving MRO inventory: Tracking MTBF allows managers to fine-tune maintenance, repair, and operations (MRO) inventory purchasing to ensure the optimal number of parts is always available. Accurate parts forecasting results in lower costs, more liquid capital, and quicker repair times.
- Replacing assets: It's always tricky to decide whether to repair or replace a particular system. The MTBF formula helps inform the decision-making process by allowing managers to calculate expected repair costs over the same period. They can then weigh the data against the cost of purchasing new machinery to determine a cost-effective repurchasing date.
Additionally, MTBF is an essential KPI calculation for reliability engineering, especially when it comes to critical assets. Maintenance engineers often rely on MTBF calculations when designing safety, mechanical, and electronic systems to ensure optimal results.
Who uses Mean Time Between Failure?
Manufacturing MTBF is crucial for plants to keep production lines running. When your equipment runs 24/7 in manufacturing processes, you need to know when failures might happen. Food processors, automotive manufacturers, and pharmaceutical companies rely on MTBF data to schedule maintenance without disrupting production.
Facilities management teams use MTBF for critical building systems. Your HVAC, elevators, and backup generators can't fail without warning. Hotels, hospitals, and data centers track these reliability metrics to prevent costly emergencies and maintain comfortable environments.
Transportation and logistics companies monitor MTBF across their fleets. Whether you manage delivery trucks, forklifts, or conveyor systems in different systems, understanding failure patterns helps you avoid breakdowns that delay shipments and frustrate customers.
Energy and utilities depend on MTBF for infrastructure reliability. Power plants, water treatment facilities, and oil refineries use this data to prevent outages that affect thousands of customers. In these industries, equipment failure isn't just expensive but also a public safety concern with significant impact.
How to calculate MTBF
MTBF = total uptime of repairable asset ÷ number of failures of asset within given time period
To calculate MTBF, you need two pieces of information:
- Total operational hours (operating hours) for your asset
- Number of failures during that period
Here's a simple MTBF calculation example:
Your water pump ran for 1,000 operating hours and broke down twice.
- Water pump MTBF = 1,000 hours ÷ 2 repairs
- Water pump MTBF = 500 hours
This means you can expect the pump to run for about 500 hours between failures. This average value helps predict future performance.
Start with your most problematic equipment first. Calculate MTBF, fix the issues, then move to the next worst performer. Lower MTBF indicates more frequent failures requiring attention.
Important reminders:
- Only count unplanned failures, not scheduled maintenance.
- Define "failure" clearly (usually means equipment can't meet production requirements).
- Track data consistently using a CMMS for accuracy.
- MTBF assumes a constant failure rate during normal operating conditions.
How to conduct MTBF analysis
MTBF analysis goes beyond simple calculations. It's a systematic process for analyzing data that helps you understand why equipment fails and how to prevent future breakdowns. Here's how to conduct a thorough reliability analysis that drives real improvements in equipment effectiveness.
1. Define scope
Start by setting clear boundaries for your analysis. Choose one critical asset or a group of similar equipment. Don't try to analyze complex systems all at once. You'll get overwhelmed with data.
Define what counts as a failure for this equipment. Does the machine need to stop completely? Or does reduced performance count? Your maintenance team needs to agree on this definition before collecting any data.
Set your analysis timeframe. Six months gives you enough data to identify trends and usage patterns for most equipment. But equipment with infrequent failures, like backup generators that only run during power outages or seasonal equipment like heating boilers, might need a full year to capture enough failure events. Consider your equipment's typical usage when choosing the period.
2. Collect reliable data
Good analysis needs good data. Track every failure with these details:
- Date and time of failure
- Total runtime before failure occurs
- Failure description
- Repair actions taken
- Downtime duration
Use your CMMS to standardize how you collect data. When technicians log failures consistently, your MTBF metrics become more accurate. Train your team to record failures immediately because memories fade fast.
Avoid common data mistakes. Don't mix planned maintenance with failures. Don't guess at runtime hours. Non-critical failures might not count as true failures for MTBF, but small problems often reveal bigger issues in individual components.
3. Calculate MTBF
Now apply the MTBF formula to your collected data. If your compressor ran 2,000 hours with four failures:
- MTBF = 2,000 hours ÷ 4 failures = 500 hours
Calculate MTBF for different time periods to spot trends. Is the system's reliability improving or getting worse? Monthly calculations help you catch problems early.
For multiple identical assets, calculate individual and fleet-wide MTBF. This comparison reveals which specific units need attention and helps identify systemic issues.
4. Analyze results
Compare your MTBF to industry benchmarks and manufacturer specifications. A 500-hour MTBF might be excellent for one type of equipment but terrible for another.
Look for patterns in your data:
- Do failures cluster around certain runtime hours?
- Are failures more common during specific shifts?
- Does weather or workload affect failure rate?
Graph your results over time. Visual trends are easier to spot and share with management. A declining MTBF trend demands immediate attention from reliability engineers.
5. Identify root causes of failures
Don't stop at symptoms but dig deeper using root cause analysis. Use the “Five Whys” technique. If a bearing fails, ask “Why?” repeatedly until you identify the root cause:
- Why? Lack of lubrication
- Why? Missed PM schedule
- Why? No automated reminders
- Why? CMMS not properly configured
- Why? Insufficient training during implementation
Review maintenance histories for recurring issues. If the same component fails repeatedly, you've found a design flaw or procedural gap affecting equipment reliability.
Interview your operators and technicians. They often know why equipment fails but haven't been asked. Their insights can shortcut your investigation.
6. Take corrective actions
Turn your findings into specific actions. Common improvements include:
- Adjusting PM intervals based on actual failure data
- Upgrading components that fail frequently
- Improving operator training on proper equipment use
- Installing condition monitoring for early warning
Prioritize actions by impact and cost. Quick wins build momentum. Fix the easiest problems first—this proves your approach works and gets buy-in from management. Then, use these documented improvements to justify tackling bigger, more expensive fixes.
Document every change you make including what you changed, when, and why. Track your MTBF before and after each improvement. This before-and-after comparison proves which actions actually reduced failures and helps you repeat successful fixes on similar equipment.
7. Re-measure and monitor
MTBF analysis isn't a one-time project. Set up monthly or quarterly reviews to track progress. Did your corrective actions work? New failure patterns might emerge as you fix old ones.
Create dashboards that show MTBF trends for critical equipment. When everyone can see the numbers, accountability improves. Celebrate improvements and investigate declines quickly.
Adjust your analysis scope as needed. Once you've achieved high MTBF for your worst performers, expand to other equipment. Continuous improvement means always having the next target ready.
How to improve MTBF
Your MTBF analysis revealed the problems. Now, it's time to fix them. Improving MTBF isn't about one big change but rather making smart adjustments across your maintenance program. Here are proven strategies that extend equipment life and reduce failures while maintaining operational efficiency.
Improve your processes
An effective PM program can drastically increase MTBF. Ensure your maintenance technicians are well-trained, equipped with appropriate manufacturer manuals, and have adequate procedural checklists for PM activities.
Spend more time searching for root causes of equipment failures instead of engaging in temporary fixes. Engaging in investigative maintenance strategies like "The Five Whys" can help address the specific reasons certain assets fail more often than others.
Track PM compliance religiously. When MTBF drops, first check if PMs were missed. A single skipped lubrication can cascade into bearing failure, shaft damage, and weeks of costly downtime.
Create preventive maintenance schedules
Your PM schedule directly impacts MTBF and overall equipment effectiveness. Review your current intervals against actual failure data. Are you maintaining equipment too often or not enough? Data beats guesswork every time.
Start with manufacturer recommendations, then adjust based on your operating conditions. Equipment running in dusty environments needs more frequent filter changes. Machines under heavy loads require more frequent inspections.
Create detailed PM checklists that technicians can't skip or rush through. Include:
- Specific torque values for bolts
- Acceptable tolerance ranges for measurements
- Clear pass/fail criteria for inspections
- Required photos for verification
Use condition-based maintenance
This proactive maintenance strategy uses technology-based diagnostics like vibrations, temperature, pressure, speed, and voltage. These measurements are combined with problem-solving flowcharts to determine when maintenance is needed. Sensor devices monitor the actual conditions of assets in real time and indicate signs of decreasing performance or impending failure before something breaks.
Technology-aided data collection works particularly well because every asset operates under different circumstances. Human factors like how operators run equipment, how technicians assemble components, and how teams perform maintenance all affect reliability differently.
Understand aging assets
The industry’s assets average 24 years old—the oldest since 1947. Team leaders should educate themselves on how to best handle aging equipment and address avoidable recurring issues that have significant impact on production.
Streamline and standardize data collection
MTBF metrics are only as valuable as the data behind them. Use a cloud-based solution like MaintainX to reliably store PM repair dates, parts used, and maintenance costs accrued for work orders and work requests.
The right tools help improve MTBF
Manual tracking and spreadsheets won't cut it for serious MTBF improvement. You need tools that capture data automatically, calculate metrics instantly, and reveal patterns you might miss in complex systems.
Modern CMMS platforms transform MTBF analysis from a quarterly project into real-time intelligence. Your technicians log failures on mobile devices. The system calculates MTBF automatically. Dashboards show trends before they become problems, helping you maintain high system reliability.
The best tools integrate with your existing maintenance processes. They remind technicians about PM schedules, track parts usage, and document every repair. Consistent data collection makes your MTBF calculations accurate and actionable, leading to lower costs and better equipment reliability.
When you combine MTBF analysis with a comprehensive preventive maintenance strategy, equipment reliability improves dramatically. The right tools make both processes simpler and more effective.
Frequently Asked Questions
MTBF stands for Mean Time Between Failure. It measures the average time a repairable piece of equipment operates between breakdowns. For example, if your compressor runs for 1,000 hours and fails twice, its MTBF is 500 hours. This metric helps you predict when equipment might fail and schedule maintenance accordingly. It's a critical measure of reliability for any repairable system.
Review MTBF monthly for critical equipment and quarterly for everything else. After implementing improvements, check weekly for the first month to ensure changes are working. Annual reviews help with budget planning and equipment replacement decisions. The key is consistency. Pick a schedule and stick to it. Regular analysis helps you identify trends early and maintain optimal equipment effectiveness.
MTBF reveals your equipment's reliability and helps predict future performance. A declining MTBF warns that equipment is deteriorating. An improving MTBF confirms your maintenance strategy is working. Use MTBF to optimize PM schedules, justify equipment replacement, and benchmark performance against industry standards. It's your early warning system for equipment health and a key indicator of maintenance program effectiveness.
See MaintainX in action