Maintenance standards are established criteria for performing various maintenance tasks such as cleaning, repairs, parts replacement, lubrication, and maintenance data collection. Stakeholders in the maintenance industry establish standards for various reasons, including reduced safety risks, increased asset reliability, and enhanced efficiency.
What Are Maintenance Standards?
Companies of all sizes establish their own internal standard operating procedures (SOPs) to ensure smooth maintenance and operations. Additionally, industry institutions, such as the International Organization for Standardization (ISO), publish official maintenance standards as recommended best practices. Maintenance departments use these standards as guidelines when developing, implementing, and correcting maintenance team strategies.
The implementation of maintenance standards takes into account:
- Organizational operating plans and budgets
- Environmental laws, OSHA mandates, and other regulatory requirements
- Terms and conditions of facility and asset insurance policies
- Terms and conditions of operations and maintenance agreements
While organizations have no obligation to implement SOPs, most high-volume companies consider them crucial to their long-term success. The more complex pieces of equipment a company utilizes, the easier it becomes to overlook the many small tasks involved in maintaining equipment reliability and cost-efficiency.
The Benefits of Maintenance Standards
Maintenance standards serve the following primary purposes:
- Clarify Contractual Obligations: Ensure organizations and maintenance professionals understand responsibilities, liabilities, and important details.
- Simplify Daily Operations: Harmonize maintenance best practices among organizational key stakeholders so everyone knows exactly what, when, and how to execute preventive and corrective maintenance tasks without question.
- Keep Everyone Safe: Define criteria for reducing the risk of injury, minimizing environmental impact of processes, and upholding quality control.
Additionally, adhering to maintenance standards is crucial to passing audits, minimize unplanned downtimes, and reduce extraneous spending. Leading with agreed-upon protocols also can help build a positive work culture.
Who Produces Maintenance Standards?
While some departments implement unique SOPs according to their unique needs, most departments follow global maintenance industry standards. The two dominant international regulatory organizations are the International Organization for Standardization (ISO) and the International Electrotechnical Commission (IEC).
Maintenance standards developed by ISO include:
- Quality Management Standards
- Environmental Management Standards
- Health and Safety Standards
- Energy Management Standards
- Food Safety Standards
- IT Security Standards
ISO has technical committees that work on different aspects of maintenance. For instance, the TC108 and TC135 technical committees are responsible for developing condition monitoring, shocks, mechanical vibration, and non-destructive testing. Alternatively, the ISO/TC 251 is responsible for asset management standards.
The IEC also includes technical committees and subcommittees that develop standards for the management, maintenance, and logistics support that applies to many equipment types. This includes rotating machinery, hydraulic and steam turbines, switching devices, and fiber optics besides electrical equipment.
In the United States, the American National Standards Institute (ANSI) develops standards and oversees conformity assessment activities. It’s also a member of the two international standardization bodies mentioned above.
Lastly, private entities publish widely used maintenance standards. Though no one recognizes these documents as “official standards,” they provide reliable references for organizations in different industries. Examples of such entities include the Society of Automotive Engineers (SAE International), American Society of Heating, Refrigerating and Air-Conditioning Engineers (ASHRAE), MIMOSA, and the Society for Maintenance & Reliability Professionals (SMRP).
Classification of Maintenance Standards
ISO, IEC, and SAE International, among other institutions, develop standards that help organizations to improve their maintenance efforts. Some of the most common standards that maintenance personnel should be aware of include:
1. Asset Management Standards
Plant equipment and components are categorized under asset management. The goal of asset management standards is to coordinate and optimize an asset’s entire lifecycle from acquisition to disposal. ISO 55000 comprises three asset management standards:
- ISO 55000: It outlines the scope and merits of asset management. To be declared ISO 55000-compliant, organizations must have an asset management system that defines the policies, objectives, and processes to achieve organizational goals.
- ISO 55001: It elaborates the components of an asset management system, such as organizational context, planning, leadership, operation, performance evaluation, support, and improvement. The standard specifies the requirements organizations need to meet as an integrated and effective asset management system.
- ISO 55002: It provides guidelines for implementing asset management systems in line with the ISO 55000 family standards.
The ISO 55000 family also provides a practical framework for auditing and improving asset management systems.
2. Condition Monitoring and Machine Diagnostics
ISO 13374 outlines the standards for condition monitoring and machine diagnostics. It aims to ensure organizations have efficient data sharing and distribution for proactive asset maintenance. This standard includes condition-based, preventive, and predictive maintenance. Organizations should be able to exchange and integrate data across different systems easily.
The ISO 13374 family of standards provides ways to process, communicate, and present data in a unified and interoperable way across different systems without vendors’ reliance. It consists of the following four parts:
- Part 1: General guidelines for communicating and processing data
- Part 2: Requirements for processing data
- Part 3: Requirements for data communication
- Part 4: Requirements for data presentation
The components of ISO 13374 are widely used by organizations that conduct vibration analysis to determine asset health.
3. ANSI TAPPI TIP 0305-34:2008
The ANSI TAPPI TIP 0305-34:2008 standard provides a practical approach for developing and maintaining useful maintenance checklists. It outlines the guidelines for organizations and maintenance personnel to create daily, weekly, and monthly maintenance checklists. Maintenance engineers can customize the lists depending on organizational needs, types of assets, and physical configurations, among other characteristics.
4. MIMOSA Open Information Standards
MIMOSA, a not-for-profit trade association, develops Operations and Maintenance (O&M) standards used in facilities such as facility management, fleet management, and manufacturing. The standards cover different aspects of data exchange and O&M systems integration. Operational managers also use them for data sharing and interoperability across other maintenance datasets.
5. Industrial Internet Consortium Reference Architecture
The Industrial Internet Consortium Reference Architecture (IIRA) is at the forefront of digitizing the maintenance industry. It outlines the principles for structuring and integrating Industrial Internet applications in maintenance. Industrial Internet systems are used in sectors such as manufacturing, transportation, healthcare, and energy. The IIRA standard outlines guidelines for developing flexible, interoperable maintenance applications. It defines the requirement for connectivity and data representation and distribution.
6. SAE JA1011 Standard
The SAE JA1011 standard was initially developed to improve the reliability of assets and safety in the commercial aviation industry. It has been expanded and used in other sectors as well. Today, it’s referred to as the Reliability-Centered Maintenance (RCM) process.
Maintenance Standards and MaintainX
The maintenance industry employs several standards to maintain safe, efficient, and reliable operations. The above list of standards isn’t exhaustive but does include the most commonly utilized standards right now. However, maintenance standards are always evolving. As organizational maintenance needs and data mediums change, teams must continually adapt their approaches. Such flexibility enables maintenance departments to determine which standards are most applicable to their unique needs.
Modern computer-based management systems are sleek, intuitive, and affordable. With MaintainX, you don’t have to sacrifice features for simplicity—you can:
- Create reactive and preventive maintenance work orders.
- Assign recurring work orders to both teams and individuals.
- Monitor progress by maintenance category, priority level, downtime, etc.
- Analyze maintenance costs for greater efficiency and savings.
- Hold text conversations with team members in real time.
Anyone with a smartphone can download the app and get started with our basic plan, which includes unlimited work orders, right away.
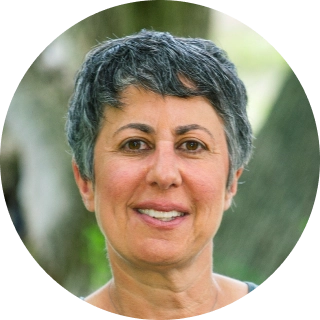
Caroline Eisner
Caroline Eisner is a writer and editor with experience across the profit and nonprofit sectors, government, education, and financial organizations. She has held leadership positions in K16 institutions and has led large-scale digital projects, interactive websites, and a business writing consultancy.
See MaintainX in action