Lockout tagout (LOTO) might not be the most glamorous part of your maintenance work, but it’s one of the most important. This protocol can be the difference between a safe repair and a potentially life-threatening mistake. Whether you’re managing a facility, running a line, or fixing equipment yourself, knowing how to lock out hazardous energy is one of the most important parts of the job.
Key Takeaways
- Lockout tagout is a legal and life-saving safety requirement.
- Every step in the LOTO process matters and must be followed precisely.
- Your team must be trained and clearly understand their role in the LOTO process.
- The right tools and documentation help ensure safe LOTO procedures.
- Regular audits prevent complacency and ensure compliance with energy control standards.
What is lockout tagout?
As a maintenance professional, you’re familiar with lockout tagout (LOTO)--a safety protocol designed to protect you and your team from injury when servicing machines or equipment. It prevents the unexpected startup or release of hazardous energy, which can happen even if a machine’s turned off.
Here’s how it works in practice:
- Lockout means placing a physical device (like a padlock) on an energy isolating device (such as line valves, disconnect switches, or circuit breakers) to stop the flow of power.
- Tagout adds a visible tag to the locked-out equipment. It tells others not to turn anything on and shows who’s responsible for the lockout.
Both steps matter. Lockout physically disables equipment; tagout communicates why it’s disabled and who’s working on it. When you combine these steps, you create a safer environment not just for the employee performing maintenance, but also for employees working nearby.
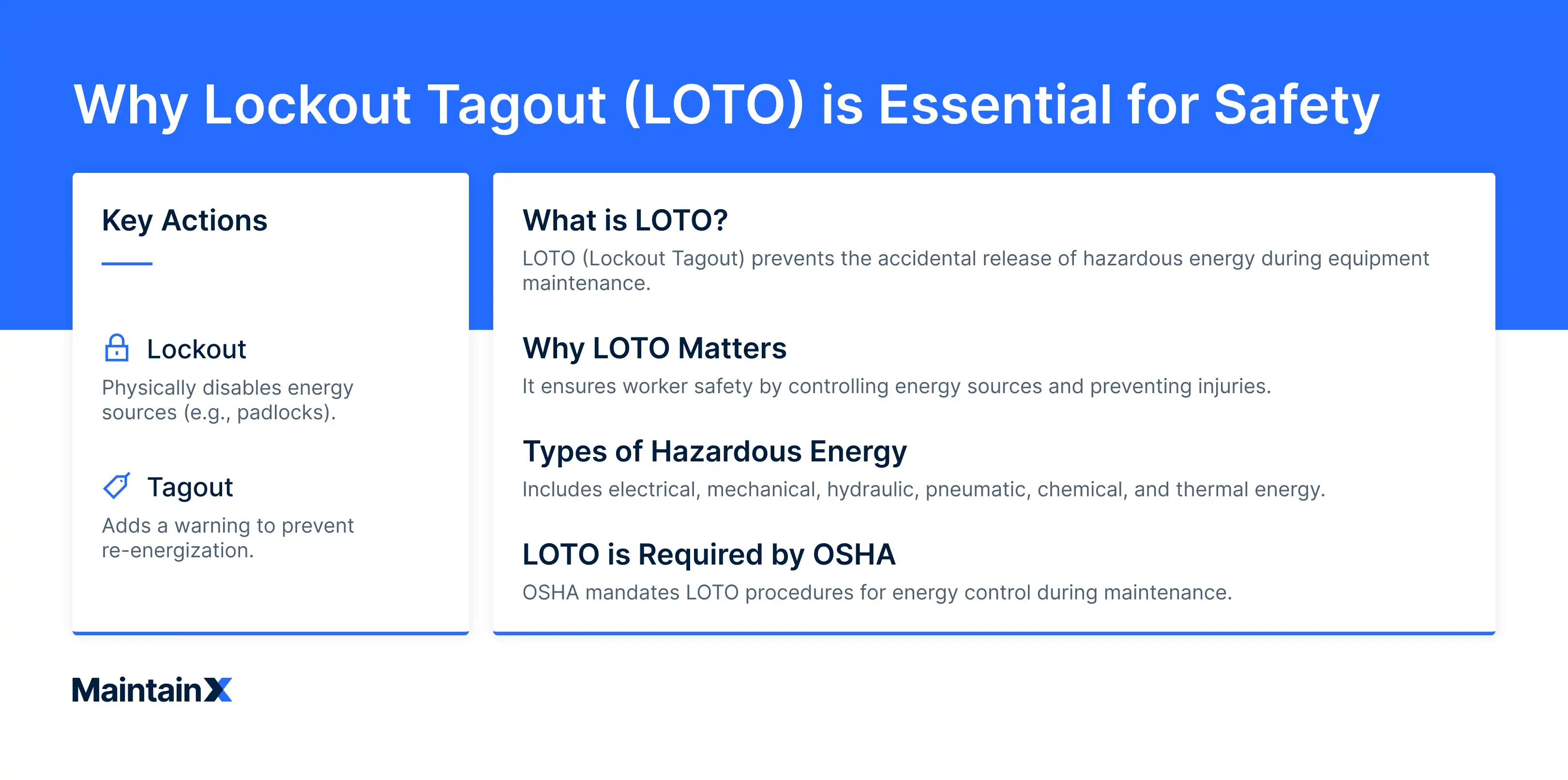
Lockout tagout standards
In the U.S., LOTO is required by OSHA Standard 1910.147, formally known as the Control of Hazardous Energy standard. It covers how facilities must develop and enforce LOTO procedures, train employees, and verify that energy has been properly isolated before work begins.
The standard applies to machines or equipment that could unexpectedly start up or release stored energy during servicing or maintenance. That includes everything from production equipment to HVAC systems, conveyor belts, robotic arms, and more.
It also outlines:
- When lockout is required versus tagout alone
- Who qualifies as an authorized employee
- What counts as an energy isolating device
- How to maintain exclusive control over locks and tags
Too often, facilities have a LOTO policy that exists only on paper, buried in a binder or rarely revisited. But the risks are real. Serious injuries can and do happen when procedures aren’t clearly documented, fully understood, or consistently followed.
Types of hazardous energy prevented by lockout tagout
You’re aware of the dangers of electrical energy. Most organizations, therefore, have adequate lockout tagout procedures to prevent the accidental release of electrical power.
Other types of equally dangerous energy include:
- Mechanical energy: You'll encounter mechanical energy created through the motion of moving objects, such as robotic arms, movable saw blades, and crushing parts. When someone accidentally bumps into a movable part, that moving component can become a danger if it picks up enough momentum.
- Hydraulic energy: Manufacturing facilities that rely on heavy machinery have a lot of hydraulic energy. You can accidentally release pressurized hydraulic fluid that is harmful while servicing equipment. Lockout tagout procedures for hydraulic power require maintenance personnel to release such pressure before starting their work.
- Pneumatic energy: This is similar to hydraulic energy but uses pressurized air instead of fluids. Equipment with pneumatic power should also have the pressure released before maintenance starts.
- Chemical energy: Facilities that handle chemicals must have safety procedures to prevent their accidental release into the air. One such approach is locking out diesel generators, which can release dangerous nitrogen and sulfur oxides, often used as backup power sources.
- Thermal energy: Heat sources such as natural gas, coal, nuclear, diesel, oil, and biomass release thermal energy. These elements are common in the mining and power generation industries.
The lockout tagout procedure: a step-by-step guide
Lockout tagout procedures differ from organization to organization. However, these are the general steps to follow regardless of your industry:
1. Get prepared
As the authorized employee, you start by identifying all energy sources connected to the machine or equipment. That includes not only the obvious electrical connections, but also less visible sources like hydraulic lines, compressed air, spring-loaded components, and gravitational forces. You’ll review the documented energy control procedure for that asset to ensure every potential hazard is accounted for.
2. Notify affected employees
Anyone working near the machine, including line operators, techs, and production staff, needs to be informed about the lockout, why it's happening, and how long the equipment will be offline. Communication helps prevent confusion and keeps people safe.
3. Shut it down
Using the machine’s normal operating controls, you power it off.
4. Isolate all energy sources
Use the appropriate energy isolating devices to disconnect or block energy sources. That could be a circuit breaker, line valve, or another mechanical device that prevents energy flow. The goal is complete energy isolation. Nothing should be able to energize unexpectedly.
5. Apply lockout and tagout devices
Now it’s time to physically secure each energy isolating device. That means placing a lockout device like a padlock or cable lock, so the equipment can’t be turned on. Then, you add a tagout device as a clear warning. Each tag should identify the authorized person who applied it. Only that person can remove it. This is what OSHA calls exclusive control.
6. Release stored energy
This step often gets overlooked. Even if you've turned the power off, machines can hold stored energy in springs, flywheels, air lines, or control circuits. You must drain, bleed, discharge, or restrain any residual energy before it can harm someone.
7. Verify energy isolation
With everything locked and tagged, you now attempt to operate the equipment (safely) to confirm that it won’t start. This test ensures you've successfully controlled all energy before work begins.
8. Perform servicing or maintenance
Once you've properly shut down, isolated, locked out, and verified the equipment, it's safe to begin the work. This could include preventive maintenance, repairs, or adjustments that require the machine to be off and safely de-energized. Even tasks that seem routine, like tool replacements or clearing jams, can pose serious risks if they require reaching into equipment or bypassing safety guards.
9. Remove devices and restart equipment
When you've finished the job, it’s time to remove the lockout/tagout devices. Only the employee performing the lockout can do this. After you’ve cleared the area, you restore energy and notify affected employees that the equipment is back in service.
Lockout tagout devices and equipment
A successful LOTO program depends not just on following the right steps, but also on having the right equipment.
Here’s what should be in every team’s LOTO toolkit:
- Lockout devices: These physically block the movement of switches, valves, or plugs. Options include padlocks, circuit breaker lockouts, cable lockouts, valve covers, and plug-connected electric equipment lockouts.
- Tagout devices: These are prominent warning devices that communicate why a machine is locked out, who applied the tag, and when.
- Group lock boxes: You use these for group lockout scenarios where multiple employees are working on the same equipment. Everyone applies their personal lock to the box holding the master key.
- Self-locking fasteners: These help ensure your lockout devices stay in place and can’t be removed accidentally.
Everything you use should be standardized across your site, easily identifiable, and able to withstand the environments you work in, whether that's high heat, moisture, or chemical exposure.
Components of an effective lockout tagout program
Your LOTO program should be more than a checklist. It should be a repeatable system backed by documentation, training, and regular review.
Here’s what to build into yours:
Documentation
- Create a documented procedure for each machine or piece of equipment in your facility.
- Include all energy sources, energy isolating devices, shutdown steps, and diagrams if necessary.
- Keep procedures updated and accessible digitally if possible.
Training
- Everyone on your site should understand the basics of LOTO, even if they’re not applying locks themselves.
- Authorized employees need hands-on training on how to identify energy sources, apply and remove devices, and verify isolation.
- Tagout-only procedures require additional tagout training, especially when lockout isn’t feasible (e.g., for connected electric equipment that can’t be locked out).
- Refresh your team’s training periodically and keep records to meet OSHA’s procedural and training requirements.
Audits and inspections
- OSHA requires at least one annual inspection of each energy control procedure. Use that time to confirm:
- The procedure is still accurate
- Your employees are following it correctly
- You address any gaps promptly
Reviews
- Update your lockout program whenever equipment you add, change, or remove equipment.
- Review your procedures after incidents, close calls, or any signs of confusion during shutdowns.
- Don’t wait for an audit to find issues. Make LOTO part of your culture of continuous improvement.
Get the right tools to document and refine your lockout tagout process
Running your lockout tagout program with clipboards and spreadsheets might work for a while, but it doesn’t scale. A computerized maintenance management system (CMMS) like MaintainX helps you make your process repeatable, trackable, and always audit-ready. To learn more about implementing effective LOTO procedures, check out our What are LOTO Procedures article, which provides a detailed step-by-step guide.
The bottom line: you get fewer errors, better documentation, and a safer, more consistent process. Try MaintainX for free.
Lockout involves physically disabling a machine using a lockout device. Tagout relies on visible warnings to prevent use. Lockout is always preferred when possible because it offers a stronger safeguard.
A lockout device prevents unexpected energizing of machinery by securing switches, plugs, or valves in an off position. It’s one of the most direct ways to control hazardous energy and protect workers during maintenance and servicing activities.
The basic steps are:
- Prepare
- Notify
- Shut down
- Isolate energy
- Apply lockout/tagout
- Release stored energy
- Verify isolation
- Perform service
- Remove devices and restart
Only the authorized employee who applied a lockout tag can remove it. This ensures exclusive control and keeps others from restarting equipment before it’s safe.
See MaintainX in action