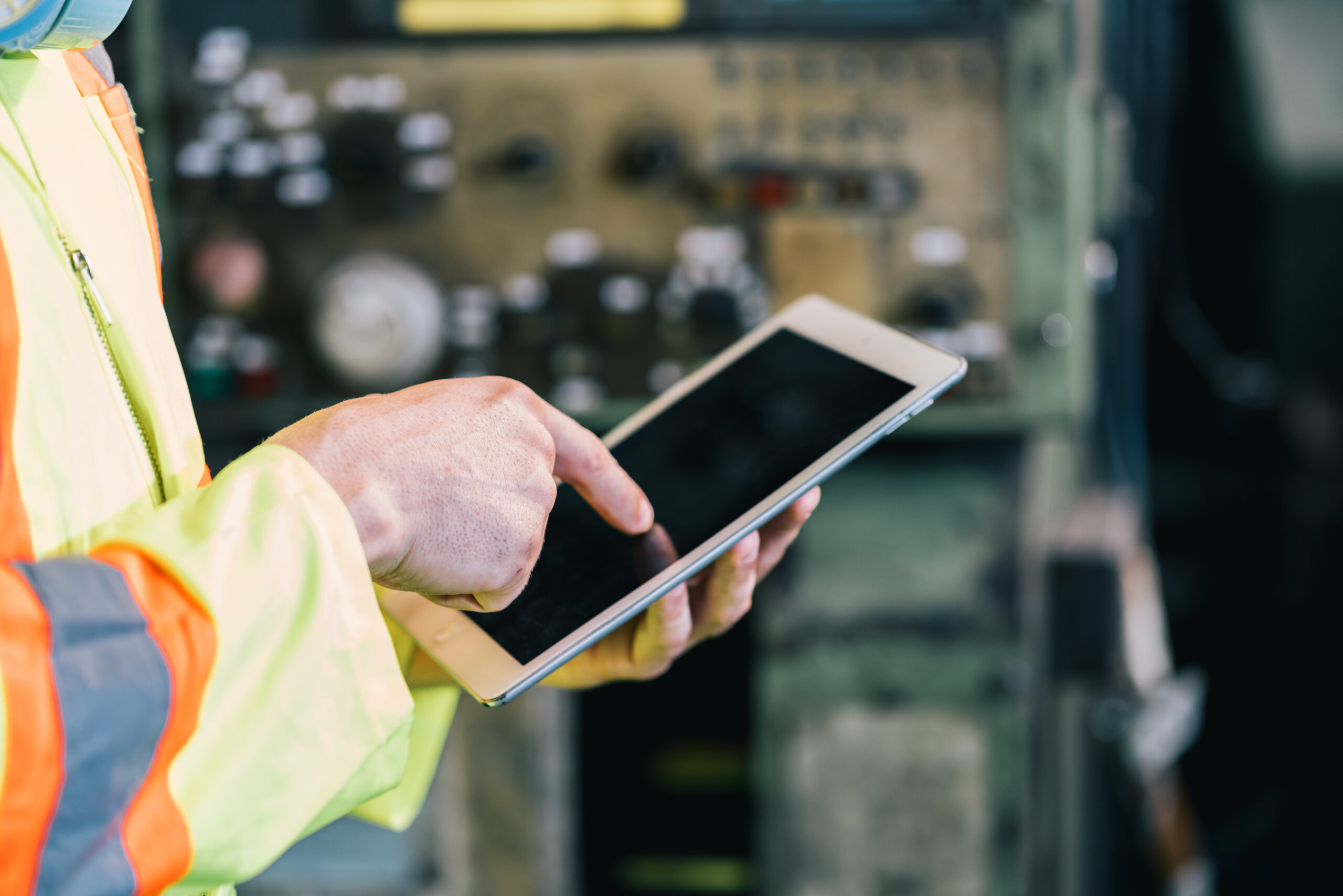
Still managing your quality control checklists, compliance audits, and safety procedures the old-fashioned way? Organizations within every industry are now benefiting from increased digitization in the workplace. In this post, we review how using standard operating procedure software and creating a centralized repository of SOPs will help you build a more agile workforce. In fact, Business Partner Magazine reported that data-driven organizations are 23 times more likely to acquire customers and six times as likely to retain consumers over time.
Digitization supports a more agile workforce in:
- Accomplishing more tasks in less time;
- Tracking, synthesizing, and illustrating large amounts of data; and
- Collaborating with team members via instant messaging.
Until recently, software developers mostly designed such productivity-boosting technology for desk workers. However, standard operating procedure (SOP) software and computerized maintenance management systems (CMMS) are quietly paving the way for a deskless digitization revolution. In this article, we’ll review the primary differences between CMMS and SOP software, the benefits they provide, and how to evaluate your options.
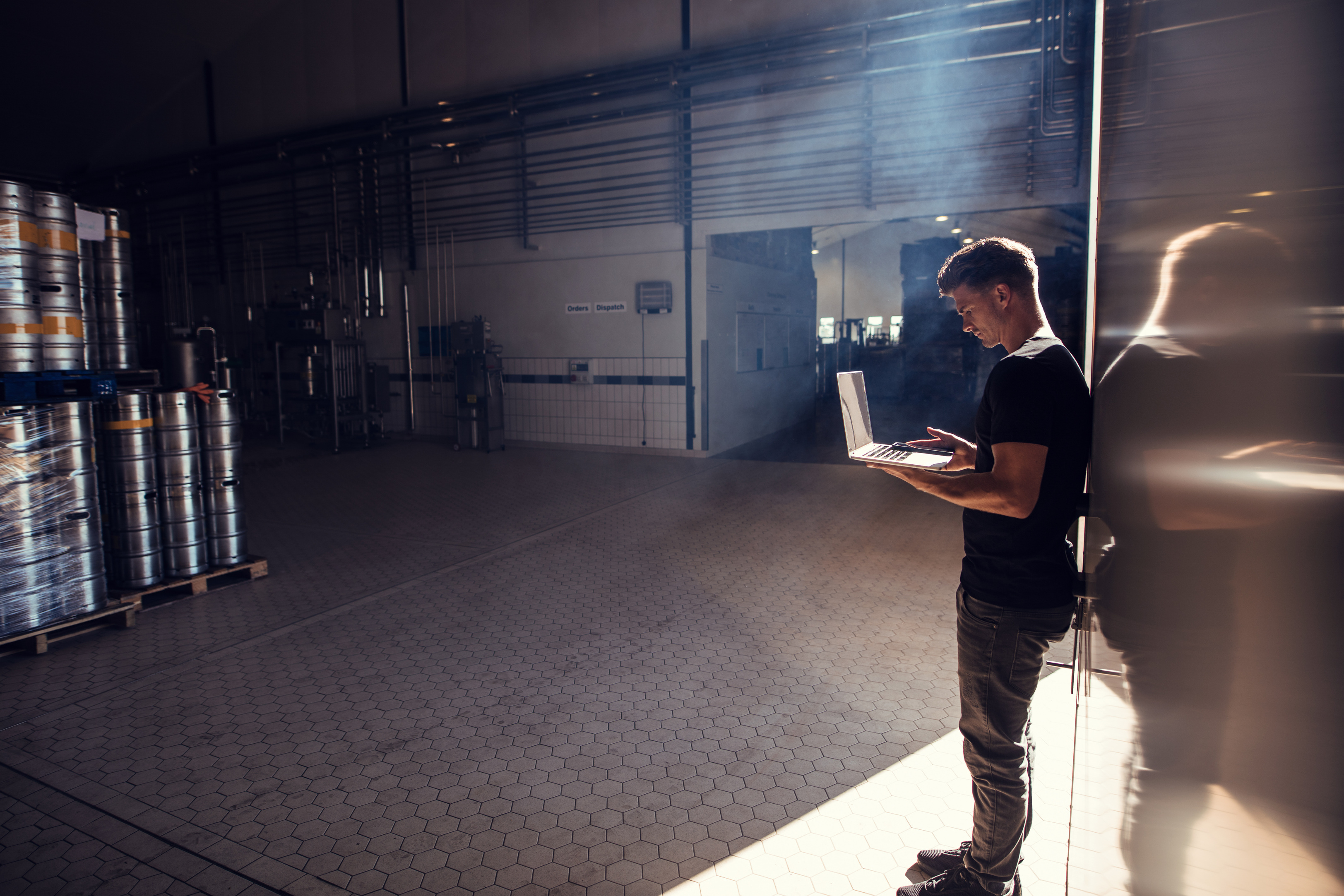
CMMS vs. Standard Operating Procedure Software
Whether you’re looking to improve quality control measures to ensure customer satisfaction, streamline employee onboarding processes, or implement safety and sanitation checklists, digital SOPS can make life easier for everyone. Before we explore the differences between the software types, it’s worth emphasizing that both options provide overlapping benefits, including:
- Preparedness: Create digital audit trails to prove compliance
- Efficiency: Streamline quality control management
- Peace of Mind: Know you’re following regulatory guidelines
- Collaboration: Share data and documentation on the spot
- Adaptability: Review and edit SOPs in real-time
However, the primary difference between standard operating procedure software and CMMS software is maintenance management capabilities. Let’s explore what that entails by delving into the history of CMMS.
“When companies get all of the requirements right, the results can be impressive. Leading players in a variety of heavy industries have used digital tools in dramatically reducing unplanned outages while boosting maintenance-labor productivity. Higher availability and a more-efficient workforce have increased profitability by 4 to 10 percent in some organizations.”
McKinsey
What Is CMMS Software?
What began as a collection of punch cards used on giant mainframes in manufacturing facilities has since evolved into smartphone-accessible CMMS. Modern CMMS software platforms allow operational managers to create, assign, and track work orders and SOPs from anywhere with a WiFi connection.
Additionally, mobile CMMS contains functionality for managing assets, parts, vendors, and inventory data in one digital location. Operations managers use CMMS to streamline maintenance management, automate task reminders, track OSHA requirements, and provide insights into O&M spending patterns.
In the beginning, enterprise manufacturing companies were the only organizations that could justify CMMS’s astronomical cost. The technology’s on-site hardware systems were expensive to set up, maintain, and scale.
However, starting around 2015, modern, cloud-based technology changed the game. Maintenance teams of all sizes could now access advanced CMMS features for affordable monthly fees—no onsite hardware installations required. Some platforms like MaintainX even provide free basic plans. Restaurants, hotels, schools, government municipalities, and businesses of all types now use CMMS to streamline work orders and SOP management.
Key Features of CMMS
- Reusable SOP templates
- Work order/SOP assigning, tracking, and fulfilling
- Asset management databases
- Parts, inventory, and vendor catalogs
- Advanced reporting statistics
- Work order commenting (with Maintainx)
MaintainX is the only CMMS provider that includes in-app team messaging, a free basic plan, and a native mobile design for an agile user experience.
What Is Standard Operating Procedure Software?
SOP software is exactly what it sounds like: software that includes tools for creating, editing, and assigning digital SOPs.
With that said, you can also use SOP software to electronically manage and distribute other types of documents, like company policies, training manuals, and announcements. Basically, it’s like CMMS in terms of functionality but without the bells and whistles. Here’s a screenshot of a typical SOP software dashboard:
Key Features of SOP Software
- SOP templates for onboarding, workflows, and quality control
- SOP- and manual-writing capabilities
- Centralized procedures and processes
- Sharing and permissions
Top SOP software providers include Process Street, Sapling, and SOP Express. Some of these programs provide standardized hierarchical checklists, while others allow for the inclusion of videos and advanced multimedia. Additionally, a few standard operating procedure software platforms even include advanced “conditional logic” for creating dynamic, if/then sequences that adapt to evolving worker needs.
While evaluating options, you’ll notice the existence of various niches. For example, some SOP programs are designed with employee onboarding in mind, while others are more focused on quality control. Determine which features you need and which ones you can do without while conducting your research.
CMMS vs. Standard Operating Procedure Software: Which Is Best?
As you may have already concluded, neither solution is better than the other. Organizations already using CMMS don’t typically invest in separate software for SOP digitization. Modern CMMS software already provides user-friendly templates for customizing, assigning, and tracking digital SOPs.
However, companies that mostly rely on reactive and outsourced maintenance services are great candidates for standalone SOP software. This includes small and medium-sized businesses that have yet to establish in-house maintenance teams.
Alternatively, organizations that heavily rely on preventive maintenance (PM) can save money by only investing in CMMS. If that sounds like your best option, keep reading. Below are five questions worth asking when evaluating providers.
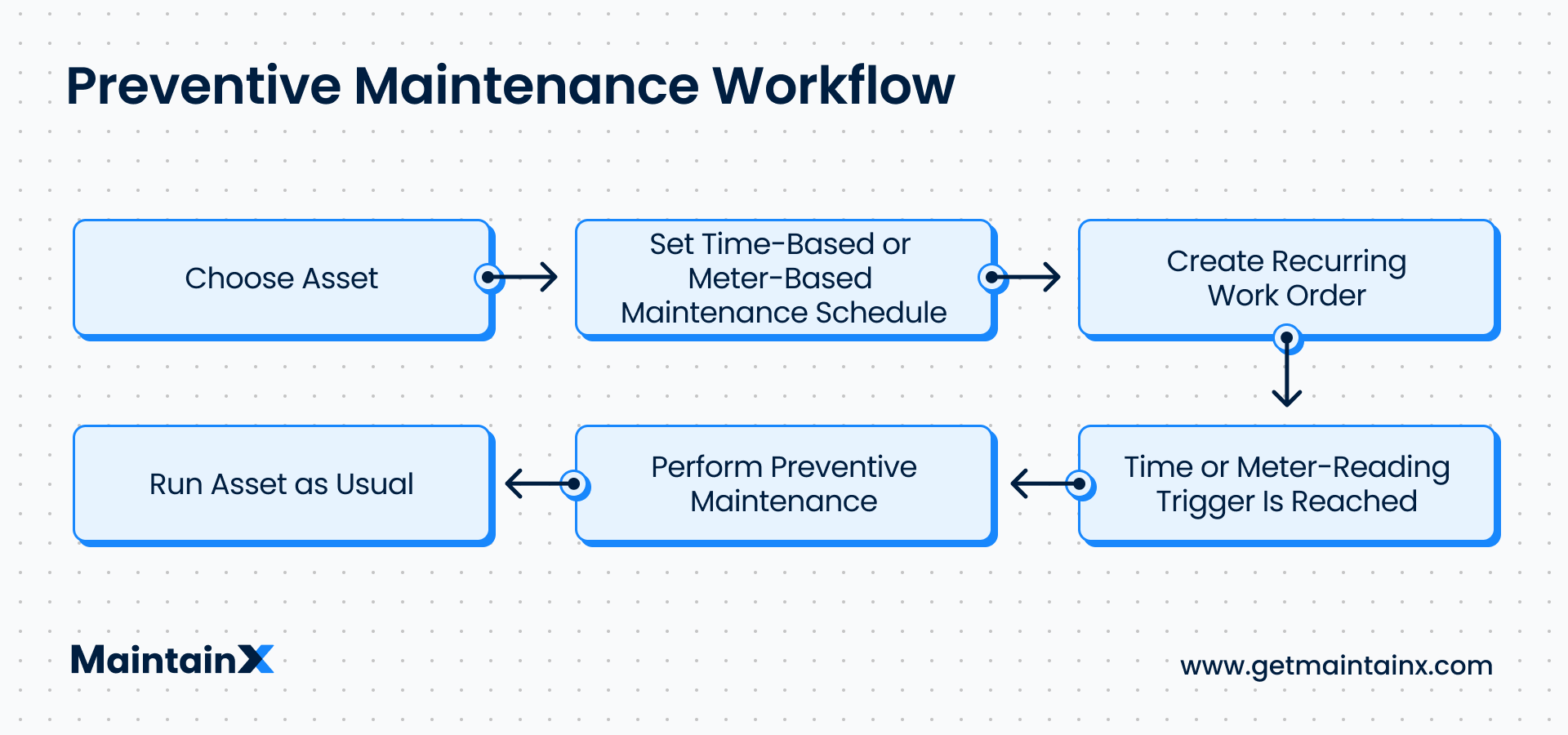
5 Questions for Evaluating CMMS for SOPs
1. What CMMS features do we really need?
A standard CMMS should provide a clear overview of upcoming work orders, safety inspections, and compliance procedures. As a manager, you should be able to quickly assign tasks, evaluate progress, and hold technicians accountable.
Identify your top priorities before shopping for CMMS solutions that address these needs. For instance, say team communication breakdowns are a constant source of stress. Poor communication leads to incomplete and poorly executed work orders that set the entire team back.
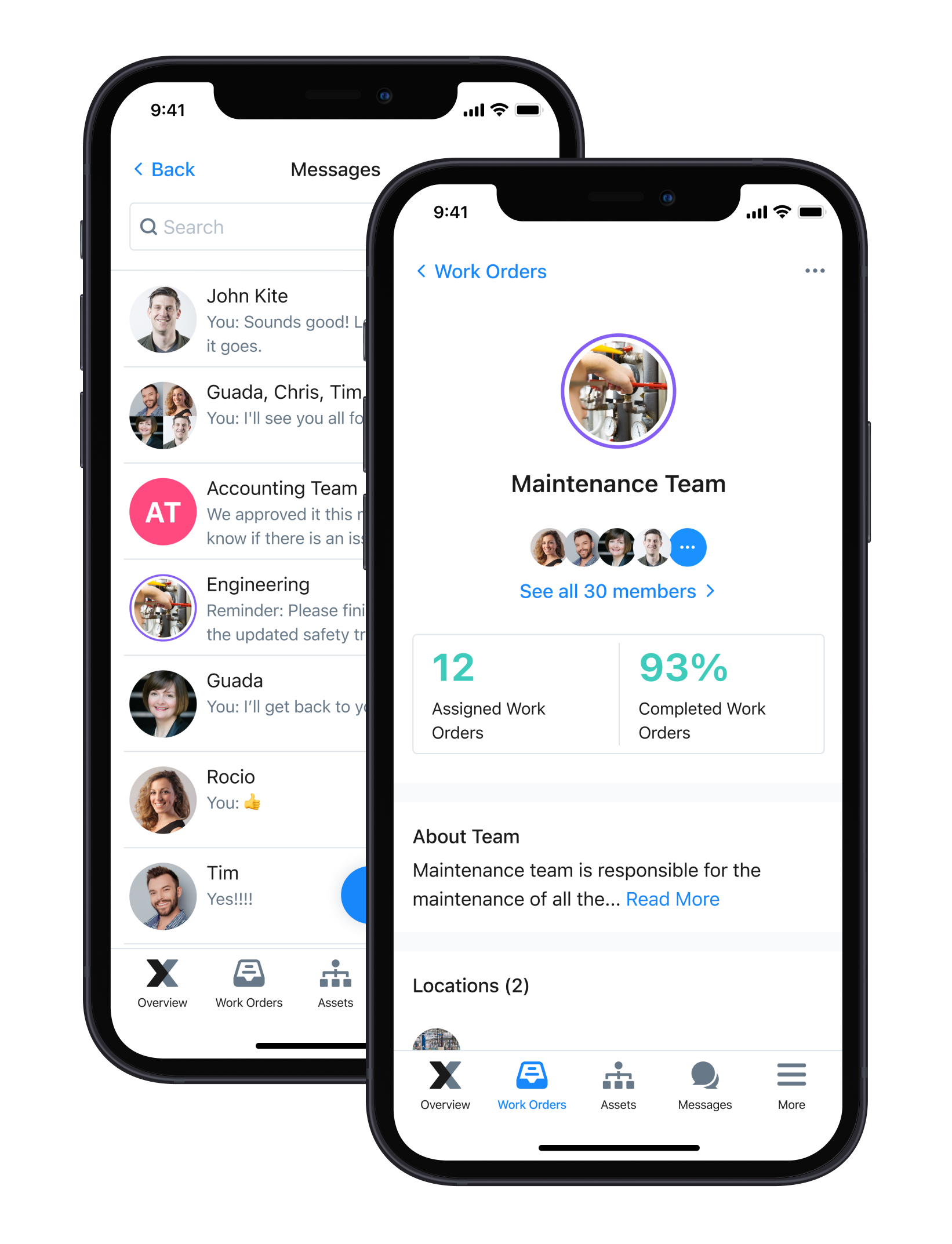
This issue is a high-priority problem to solve because it affects workplace safety, profitability, and morale. Prioritize trying out MaintainX, the only CMMS with chat functionality. Our chat feature allows team members to send instant messages, share photos of their progress, and troubleshoot issues in real time.
2. How user-friendly is the interface?
While most CMMS platforms share the same primary features, you’ll notice the user experience varies quite a bit from one platform to the next. Menu navigation styles, toggle options, and color schemes can differ substantially. If the platform you introduce is unattractive, confusing, and unintuitive, team members may revert to pen and paper out of frustration. So, invest in a CMMS your team can easily use.
Consider every member of your team who will interact with the software, what they will need in a CMMS, and how they will feel about adopting a new system. Consulting with actual future users while shopping will help avoid poor purchasing decisions. Definitely have everyone “try before you buy.” Key stakeholders who should be involved in testing the user-friendliness of the software include:
- Company executives
- System administrators and maintenance managers
- Inventory managers
- Reliability engineers
- IT team
- Health and safety personnel
- Operators
- Technicians
Your testers can indicate any challenges they may encounter in the future. Will it work for your field team? Will the IT team be able to easily integrate it into existing systems? Questions like these are crucial to ensure user compatibility.
3. Does the provider offer reliable customer support?
It’s not unusual for software shoppers to prioritize features at the expense of customer support.
Compare levels of customer support of different vendors by looking at customer reviews_. How difficult did their customers find it to contact the vendor for troubleshooting? What is the vendor’s average response time?_ Slow customer service can cancel out other CMMS benefits.
Besides phone and email support, prioritize the availability of online learning centers, video tutorials, and 1-on-1 training sessions. User-friendly resources help the entire team get on board, regardless of technical skill levels.
4. Is the CMMS on-premise or cloud-based?
As previously mentioned, CMMS can be deployed both on-site and in the cloud. In on-site deployment, CMMS software resides on your organization’s computer hardware systems. Alternatively, cloud-based deployment is accessible via smartphones, tablets, and desktops anywhere with WiFi.
Each method has its pros and cons. For example, the advantage of on-site deployment is that you don’t need an internet connection to access your database. You may also feel secure knowing your data is only accessible within your private network. With that said, modern CMMS software options are often data encrypted on third-party servers, so security shouldn’t be a concern—unless you’re the CIA.
Besides the high upfront costs, on-site CMMS burdens in-house IT teams for routine network configurations, updates, and backups. Put simply, the benefits of a cloud-based CMMS outweigh any cons: remote access, automatic updates, no need for new hardware, and minimal reliance on IT departments.
5. Does the software include cost analyses?
Lastly, CMMS should enable users to conduct cost analyses from both time and equipment standpoints. You should be able to determine how much time a team member spent on SOP checklists for any given period. The software should also reveal how much the organization has spent on parts, repairs, and time for given assets.
Streamline Operations with Digital SOPS
Modern solutions have made it easier than ever to write, assign, and organize SOPs. Digitizing SOPs helps organizations achieve greater efficiency in planning proactive maintenance, meeting regulatory compliance, and improving quality assurance.
If preventive maintenance is an integral part of your team's workload, consider streamlining SOP creation with mobile CMMS. However, if SOP digitization is your only need, invest in standard operating procedure software. Think CMMS may be right for your team?
FAQs
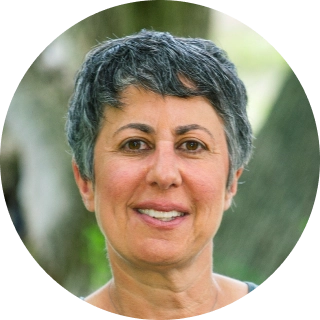
Caroline Eisner is a writer and editor with experience across the profit and nonprofit sectors, government, education, and financial organizations. She has held leadership positions in K16 institutions and has led large-scale digital projects, interactive websites, and a business writing consultancy.