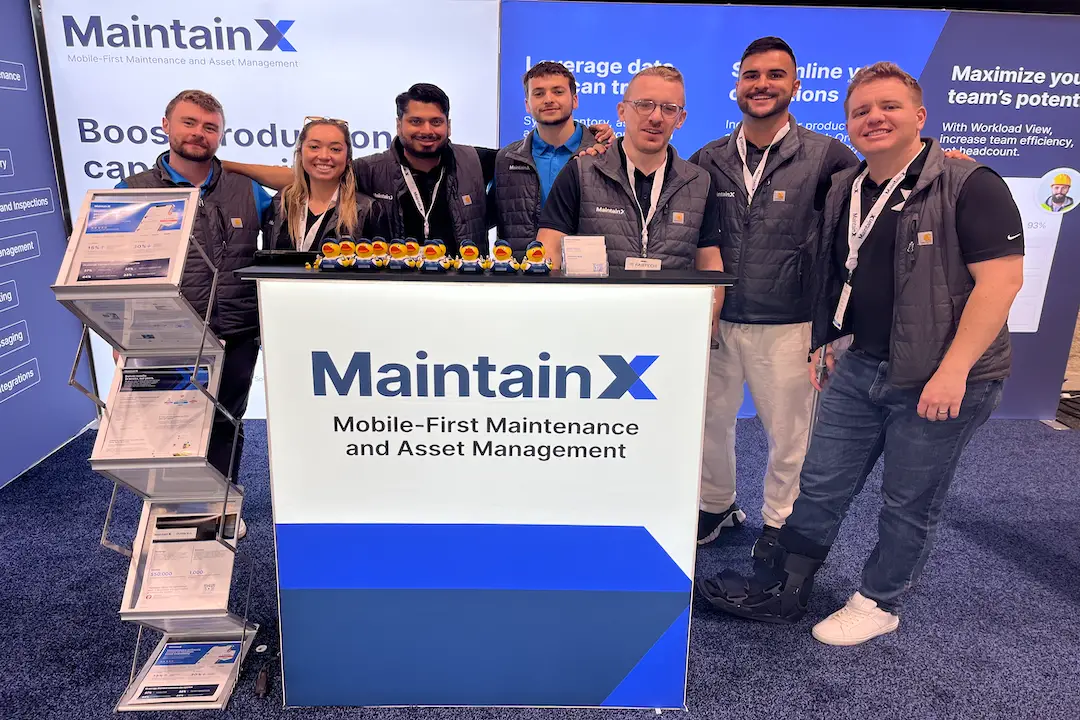
$8,000 a minute. That’s how much downtime can cost manufacturers in 2024. If nothing else, that number makes one thing clear: It’s time to get serious about cutting downtime.
Fabtech 2024 really brought this home for me: At the summit, I came across all kinds of industry leaders who are reimagining their digital transformation journeys. From seamless ERP integrations to predictive maintenance strategies, everyone’s trying to figure out how to move into the future of manufacturing.
It’s been a few weeks since the event, and I’ve identified five key themes that I think paint a picture of where the industry stands:
- Outdated manual systems and ERP integration
- Limited visibility and reporting
- Preventative and predictive maintenance
- Disconnected maintenance and operations teams
- Scalability and adoption challenges
In this post, I'll explore these themes and share strategies for manufacturing leaders to drive efficiency, innovation, and growth.
Key industry trends
Bridging the gap: Transitioning from outdated manual systems to integrated digital solutions
If you're still running your facility with paper work orders and Excel spreadsheets, you're fighting with one hand tied behind your back. I've seen countless manufacturers struggle with this. The story is always the same: data gets lost, duplicated, or entered incorrectly. Work orders pile up. Important maintenance gets delayed or missed entirely.
But here's what successful companies are doing differently:
- Implementing mobile-first platforms that put powerful tools in the hands of frontline workers. This way, your teams can capture data and execute work faster.
- Choosing solutions that integrate seamlessly with your existing systems so you can minimize disruptions during implementation and shorten your time-to-value.
- Prioritizing user-friendly interfaces that minimize training time and drive adoption.
The key is to start small but think big. Pick one critical process, digitize it, prove its value, and build from there.
Unlocking insights: Leveraging data for actionable decision-making
How much does downtime cost you? Which assets are eating up your maintenance budget? Where are your biggest efficiency gaps? If you can't answer these questions with hard numbers, you're missing out on opportunities to drive growth.
To change this dynamic, you need solutions that simplify data analysis. Seek out software with real-time analytics, custom dashboards, and KPI tracking. At MaintainX, we’ve prioritized customizable, out-of-the-box reports that can analyze your data and generate actionable insights with just a few clicks.
The result? Leaders can make decisions based on facts, not hunches. You can spot problems before they become crises and identify what’s working so you can double down on it.
Shifting gears: Embracing preventative and predictive maintenance strategies
Too many companies still spend too much time on reactive maintenance. From our own research, it’s clear that companies aren’t satisfied with this status quo. 86.8% of facilities implement some form of preventive maintenance despite spending most of their time on reactive work. Organizations want to embrace preventive and predictive maintenance—they’re just not sure how.
Here’s a quick three-step plan for beginning the shift to preventive maintenance:
- Implement the right preventive maintenance software. This step is crucial for multiple reasons, starting with maintenance scheduling. For example, MaintainX’s workload-based scheduling helps you create maintenance schedules that actually work by using labor insights to assign tasks. In addition, with the right software, you can integrate with IoT sensors to monitor equipment health and help you predict equipment failures.
- Analyze failure patterns to predict issues. By studying historical work order data, you can spot patterns like recurring breakdowns and problematic assets. This lets you identify where you need new or enhanced preventive maintenance work.
- Build a culture of proactive maintenance. This goes beyond simply checking maintenance tasks off a list. Leadership should actively champion preventive maintenance and demonstrate to their teams how it reduces downtime, improves safety, and makes work easier for everyone.
Breaking silos: Fostering collaboration between maintenance and operations teams
In too many facilities, maintenance teams are disconnected from operations teams. They use different systems, track different metrics, and have different priorities. The result? Miscommunication, delays, and missed opportunities for improvement.
The solution lies in unified digital platforms that create a single source of truth. Imagine this: A machine operator notices an unusual sound, creates a work order, and instantly chats with the maintenance team in the app. The maintenance tech asks clarifying questions, shares updates, and requests parts from the inventory team—all without switching systems.
This kind of seamless coordination isn't just convenient—it saves time, cuts costs, and drives efficiency.
Scaling for success: Overcoming adoption challenges and ensuring future-proof solutions
Here's the truth about digital transformation: purchasing technology is often easy. The real challenge is getting people to use new systems effectively.
Choose solutions that are genuinely intuitive and user-friendly. Involve frontline workers in the selection process and provide practical, comprehensive training. Start with pilot programs to prove value, and make sure to celebrate early wins. Most importantly, think about scalability from day one. Your solution needs to grow with you, accommodate new facilities, and adapt to changing business needs.
Looking ahead: Your path to digital transformation
Manufacturers who embrace digital transformation aren't just solving today's problems—they're positioning themselves for tomorrow's opportunities. The trends from Fabtech align with our vision here at MaintainX. From AI-powered solutions to empowering OEMs with Asset Connect, we're creating solutions to help teams step into the future of manufacturing, turning those $8,000-per-minute challenges into opportunities for growth.
The future of manufacturing is digital, connected, and data-driven. The question isn't whether to transform—it's how fast you can get there. Let's talk about how MaintainX can help you on that journey today.
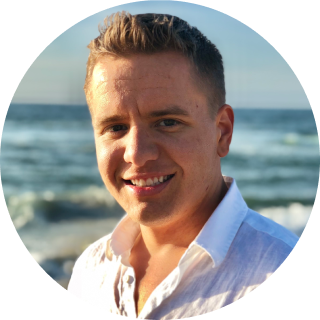
Nick Haase is a co-founder for MaintainX and is responsible for designing and leading the go-to-market strategies. He is a subject-matter expert in emerging CMMS technologies.