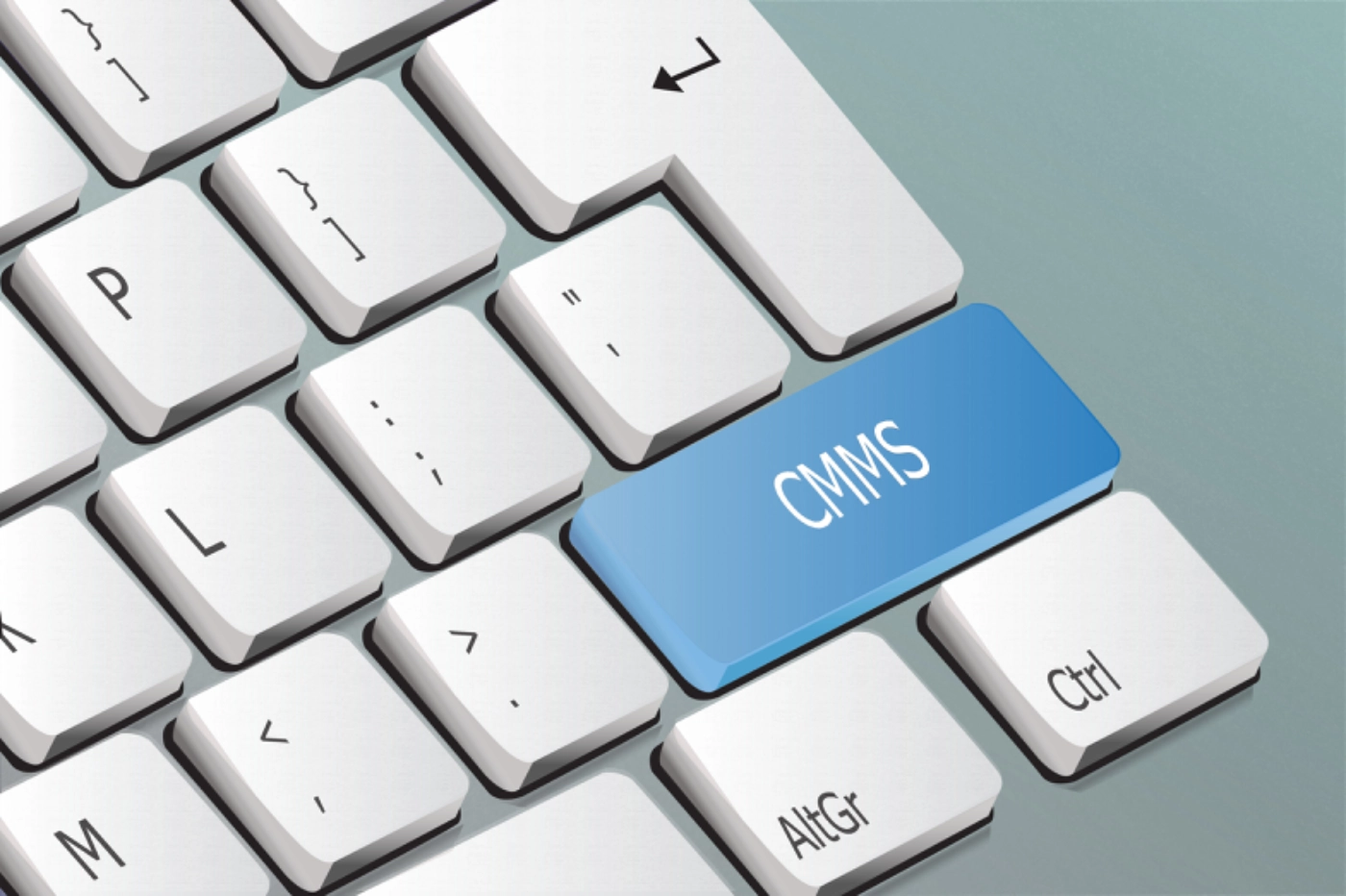
Asset performance monitoring is an essential part of the asset management strategy for any business using physical assets. Asset Performance Management (APM) involves balancing business, asset, and reliability goals when planning and operating assets.
APM combines digital transformation tools and software with traditional asset management practices to create a comprehensive and robust asset management approach. These digital transformation tools include artificial intelligence, machine learning, digital twins, and solutions supported by the Industrial Internet of Things (IIoT). While digitization isn’t entirely widespread right now, its adoption is only growing. A McKinsey survey found that 93 percent of manufacturing and supply chain professionals plan to focus on the resilience of their supply chain, and “90 percent plan to invest in talent for digitization.”
Used properly, these tools provide greater insight into assets, enabling deeper analytics to help with budgeting, risk management, supply chain management, and maintenance planning.
While asset performance monitoring is only one part of an overall asset performance management strategy, it is vital to a facility’s successful operations. Here are some reasons why.
“Implemented well, asset performance management (APM) can do more than improve maintenance. By connecting systems across an enterprise, it can deliver insights to optimize operations and safety, and drive financial results.”
Deloitte
What Is the Point of Asset Performance Monitoring?
Saves on Maintenance Costs
Asset performance monitoring is a critical factor in predictive maintenance. All proactive maintenance strategies work based on the idea that it’s better to fix minor problems before they’d develop into bigger ones, avoiding the risk of breakdowns and unplanned downtime.
Predictive and condition-based maintenance, however, go beyond a routine preventive maintenance approach and seek to prioritize maintenance work based on imminent failure or an asset’s physical condition.
Maintenance teams can only achieve this by paying close attention to assets, either by monitoring specific metrics or by using Internet of Things (IoT) sensor data. A robust sense of your asset performance will help you plan your maintenance correctly and increase the likelihood of detecting minor problems before they become bigger, more expensive ones. This approach can help reduce maintenance costs and operating costs as a whole.
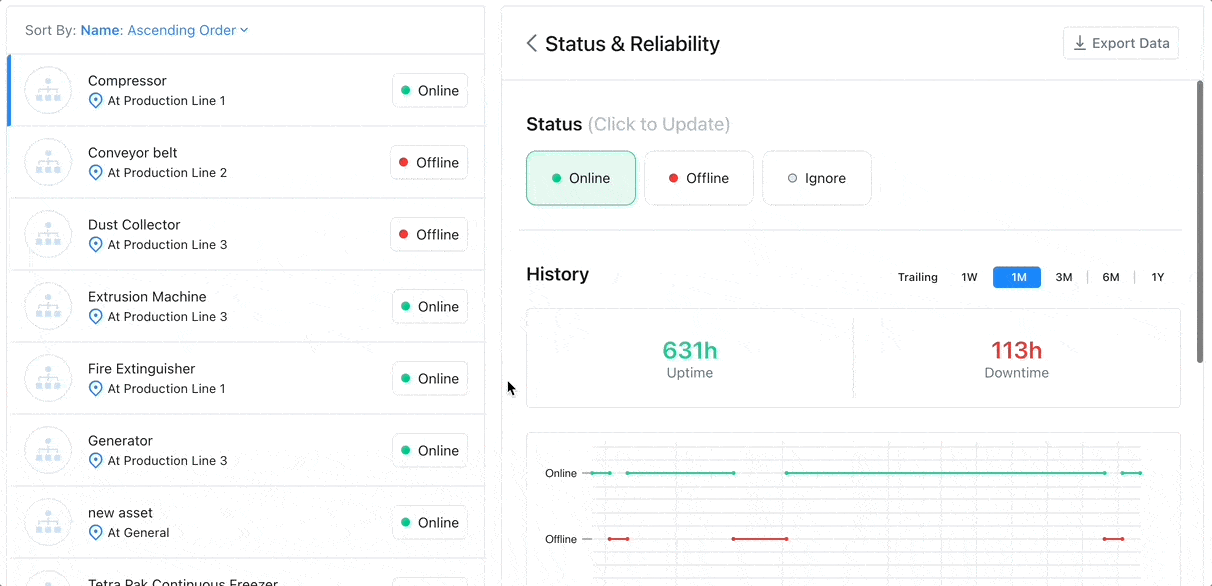
Optimizes Maintenance Work
Besides saving on maintenance costs by catching problems when they are still small, asset monitoring can help optimize your overall maintenance strategy. By paying close attention to asset performance, you can better understand what asset maintenance approaches are working and which are not.
You can then adjust your maintenance planning, ensuring you don’t waste valuable time and energy on activities that don’t provide the desired results. Imagine, for example, you carry out a routine maintenance activity every week. Monitoring specific asset metrics will help you see if this activity is making a difference.
On the one hand, you might realize you must act more frequently. On the other hand, you might learn that it makes no difference and that a monthly schedule would be more productive. Such knowledge would free up time and labor to work on actual critical assets.
Appropriate monitoring and management of maintenance can lead to overall improvements in business and operational efficiency.
Deloitte
Optimizes Decision Making
Beyond adjusting your maintenance strategies, you might also want to make decisions about your overall asset management. For example, when should you replace spare parts? At what point should you upgrade assets or continue repairing equipment to increase asset lifecycles?
You might have specific performance or usage thresholds already set. Whatever the case, proper condition monitoring helps you ensure you don’t miss this critical data so you can act when necessary.
In addition, making root cause analysis part of your asset strategy can help you identify the actual problems so you can direct your efforts there.
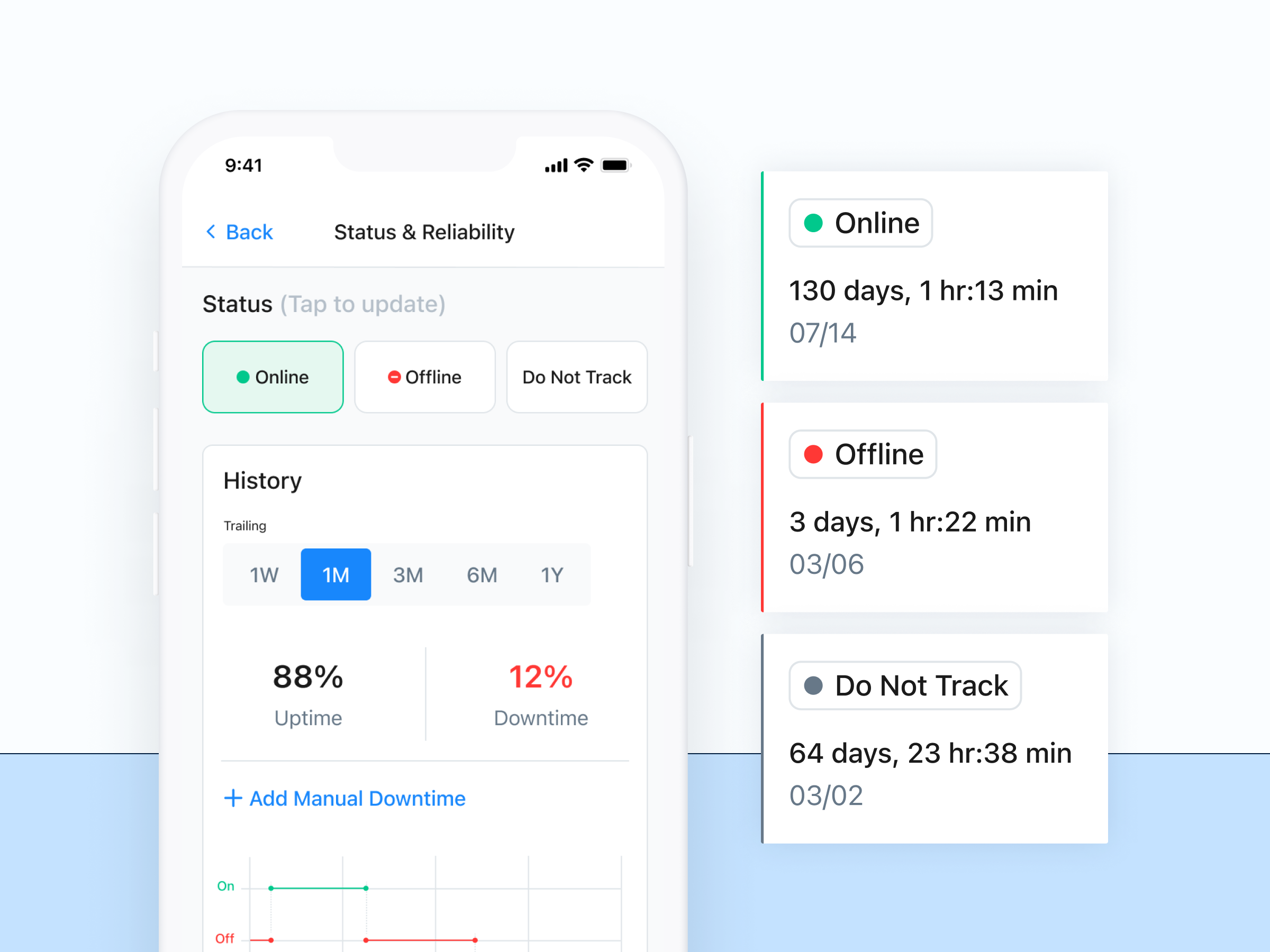
Prioritizes Asset Management
A criticality analysis is a tool used to prioritize asset management and maintenance. The tool is a quantitative way to approach your maintenance strategy, using numeric values to rate each piece of equipment on factors such as the seriousness of a potential failure.
As your business matures and increases in complexity, the number of assets and equipment to service and maintain grows exponentially. While obviously a good thing, this growth can also present several new challenges. How do you know what assets impact your ability to fulfill customer orders? What gets fixed first? And when budgets are tight, where can you safely reduce maintenance costs?
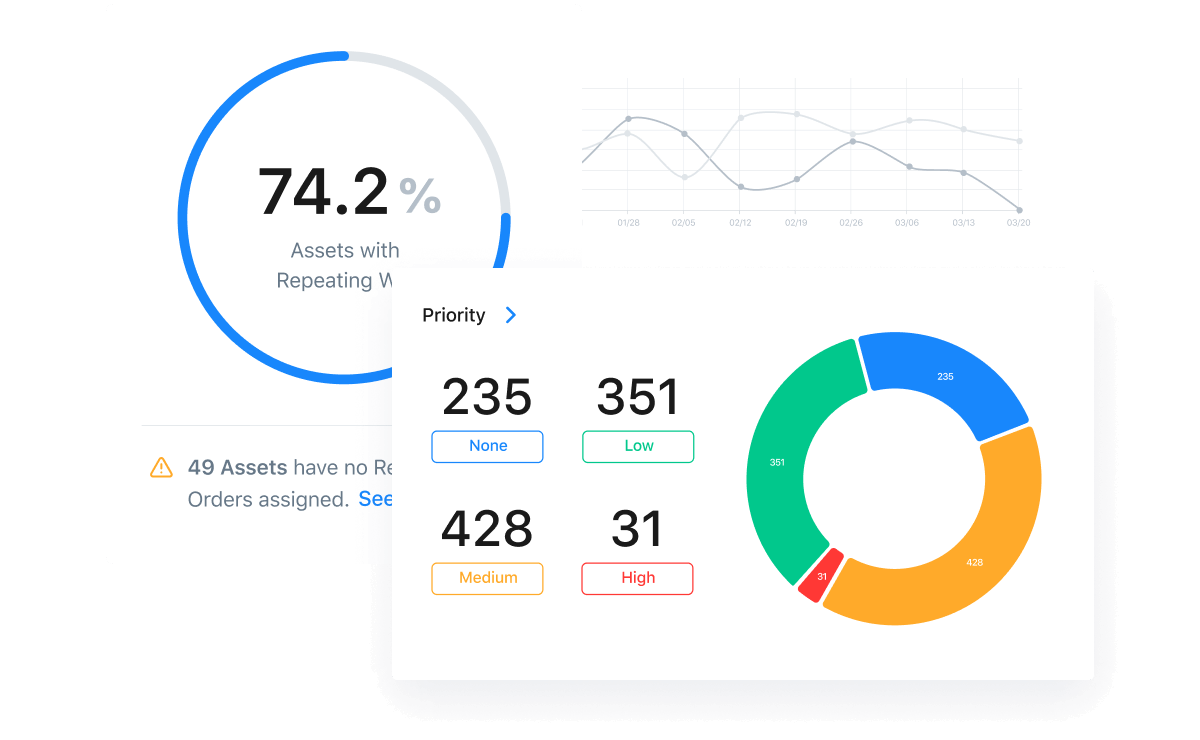
What Should I Be Monitoring?
Mean Time to Repair
Mean Time to Repair (MTTR) measures the average time a team spends on maintenance activities. What counts as a good MTTR depends on factors such as your industry, facility size, and asset types. However, aiming for an MTTR of below 5 hours is generally a good idea.
To find your MTTR, divide the total time your team spends on repairs within a period by the total number of repairs within that period.
MTTR = Total Maintenance Time / Number of Repairs
For example, if your team has spent 30 hours on maintenance for a particular machine, and this machine has had three breakdowns in one year, then the MTTR for that machine is 30 hours/3 breakdowns = 10.
Mean Time Between Failure
Mean Time Between Failure (MTBF) measures the amount of uptime assets have between failure states. It provides insight into the average time between breakdowns for repairable assets under normal operational usage.
MTBF provides an excellent way to gauge your asset reliability. For example, a low MTBF suggests that an asset is breaking down frequently, which might suggest you need to alter your maintenance approach. This might also suggest something deeper about the asset condition that you should investigate with a root cause analysis.
Calculate MTBF by summing up the time between failures and diligent that by the total number of asset failures.
MTBF = Total Uptime/Number of Failures
For example, if a piece of equipment runs for 10 hours and breaks down two times, your MTBF here would be 10 hours/2 breakdowns = 5.
Overall Equipment Effectiveness
Overall Equipment Effectiveness (OEE) measures the productivity of a facility’s assets/ OEE provides insight into your asset health, operational performance, and operational efficiency. It helps you understand if and how your operations use your assets best.
To calculate OEE, multiply three metrics: availability, asset performance, and product quality.
OEE = Availability x Asset Performance x Product Quality
Availability measures how much time assets are available for production. It is the percentage of planned production time for which an asset is uptime.
Availability = Uptime / Planned Production Time x 100
Asset performance measures production efficiency.
Asset performance = Planned Production Time / Actual Production Time x 100
Product Quality is the total number of good products expressed as a percentage of the total number of final products.
Product Quality = Number of Good Products/Total Number of Products x 100
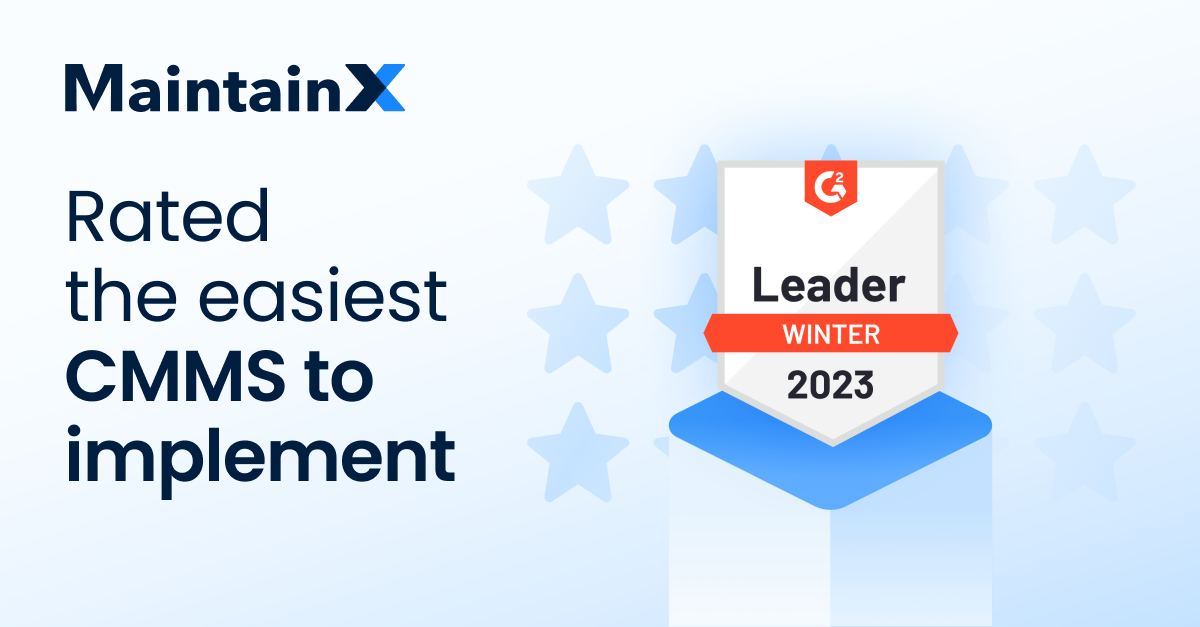
Optimize Your Asset Performance Monitoring with a CMMS
To get the best out of your asset monitoring processes, consider using a Computerized Maintenance Management System for:
Collecting and Managing Data
CMMS software can help you track your equipment and performance data. In-built storage functionality can help you maintain detailed records about everything concerning an asset: from purchase dates to service providers and maintenance history. In addition, you can calculate metrics like your MTTR or MTBF using robust CMMS software like MaintainX.
Automated Maintenance
Keep your assets in good shape using automated and repeatable work orders. Use predictive and prescriptive analytics to make your operations faster and more efficient on-premises or in the cloud. With a CMMS, you can assign work orders to staff who receive notifications via their mobile apps. This system also helps ensure that your maintenance technicians have detailed work instructions and follow standard operating procedures.
Streamlined Inventory Management
You can streamline managing and replacing parts using a CMMS. A CMMS can help you maintain an overview of your inventory, ensuring you know when levels are falling below set minimums. You can also trigger automatic purchase orders once your stock reaches a particular level.
Get the Best out of Your Assets with MaintainX
Ready to streamline your workflows and take your operations to the next level? MaintainX offers all the features described above: from work order automation to real-time shop floor updates.
For example, MaintainX’s Reporting module provides data visualization and analysis. You can use our predictive and prescriptive analytics to improve the speed and efficiency of your operations.
Generate actionable insights from your real-time MaintainX KPIs to make data-driven decisions to improve your asset management operations. If you want to know more, read a case study, check out one of our webinars, or get in touch today.
FAQs
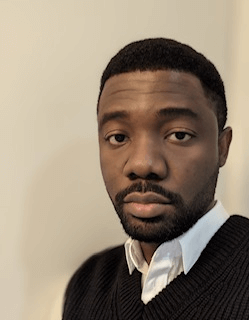
Lekan Olanrewaju is a content writer with years of experience in media and content creation. He has held positions at various media organizations, working with and leading teams at print magazines, digital publications, and television productions.