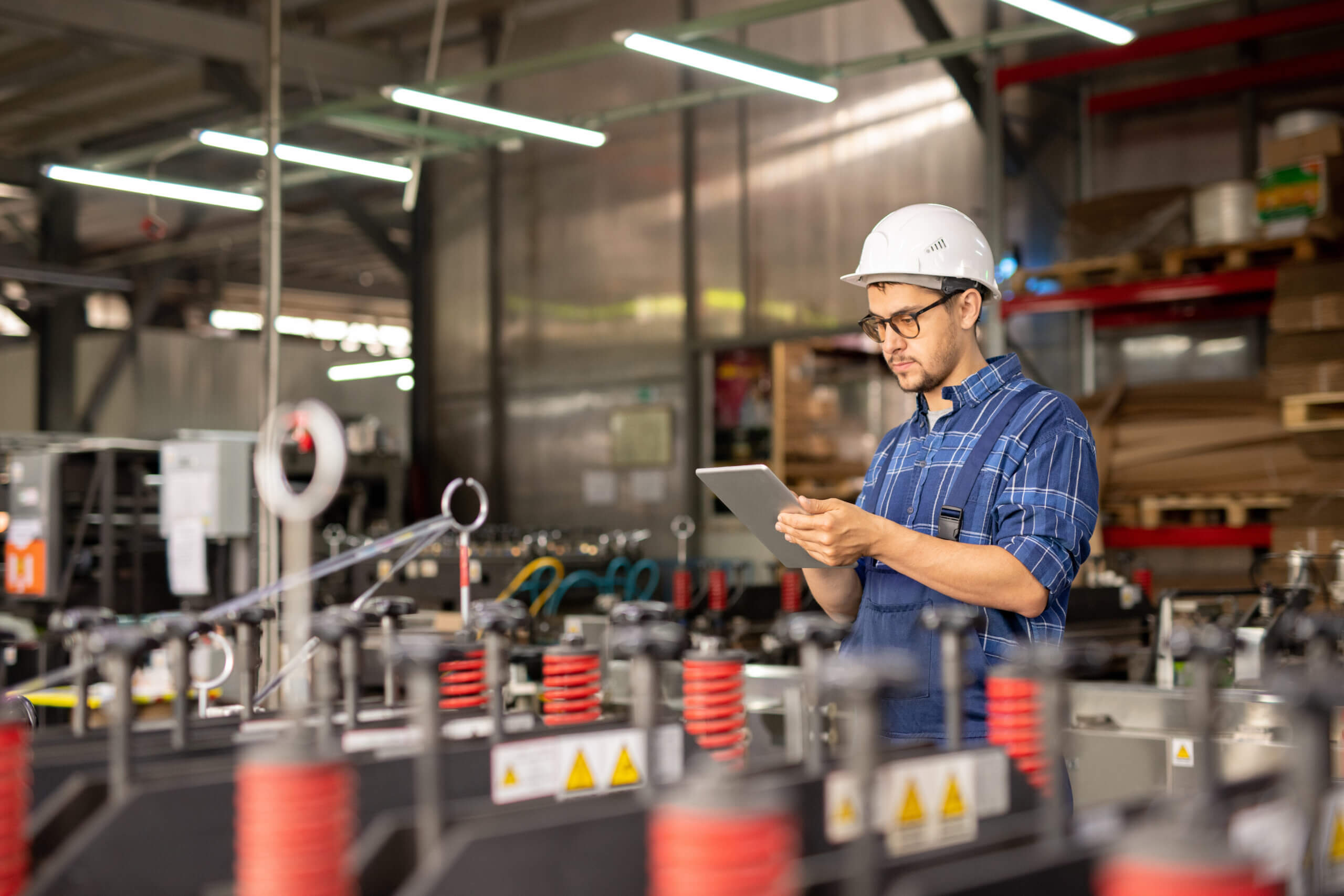
Questioning your current way of doing things is a great way to start identifying and removing the 8 wastes from your manufacturing business. In manufacturing and across industries, lean methodologies encompass a range of approaches and strategies that aim to increase efficiency, reduce operating costs, and eliminate waste.
From just-in-time production through kanban systems, one of the primary purposes of adopting a lean approach is to dramatically reduce the amount of waste your business produces.
In manufacturing, when we think of “waste,” we automatically think of things like excess packaging, steel offcuts, or defective production runs that get scrapped. However, in lean thinking, types of waste occur in many different forms.
We can address these 8 wastes in different ways, resulting in, as the name suggests, a leaner, more efficient, and more productive manufacturing operation. First, however, nothing beats using digital tools to take on the eight wastes.
“With digital lean, the manufacturer can build on its lean foundation and leverage new technologies, such as machine learning and predictive maintenance, to solve previously unsolvable business problems and unlock previously unreachable productivity frontiers.”
Deloitte
What Are the 8 Wastes of Lean?
- Overproduction: Manufacturing more than is required.
- Over-Processing: Spending additional time or work manufacturing at a higher quality than required.
- Defect Waste: Producing goods that fail to meet standards or customer requirements.
- Waiting: Waiting between steps in the production process.
- Transportation Waste: Moving raw materials or finished goods unnecessarily, resulting in lost time, energy, and costs.
- Inventory Waste: Holding excess raw materials on hand that aren’t needed for production.
- Motion Waste: Wasting time and effort caused by unnecessary movement of people.
- Underutilized Talent: Wasting your workforce’s talent, skills, and know-how.
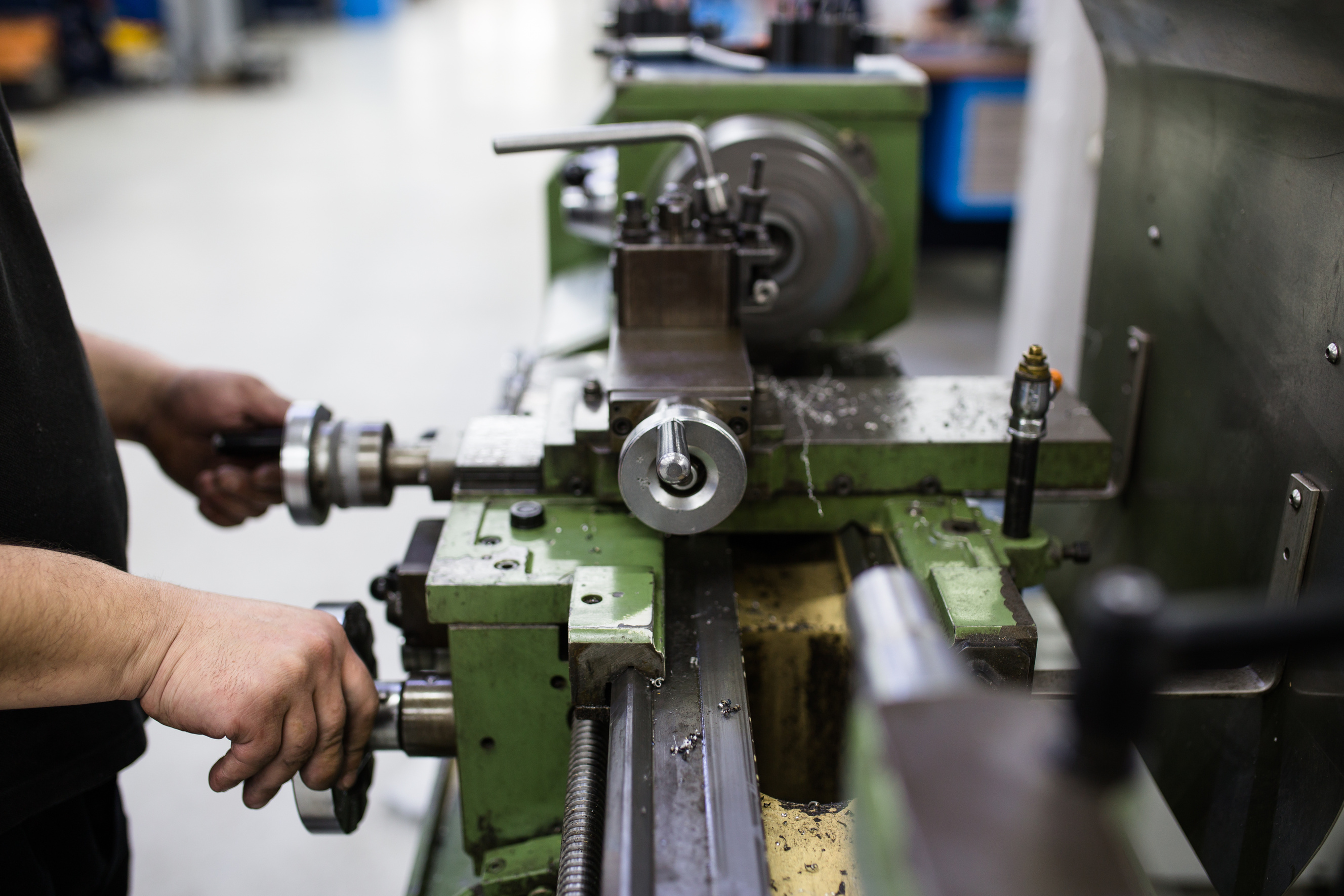
The Original 7 Wastes (and Where the 8th Waste Came From)
You may be aware of the origins of lean manufacturing. The Toyota Production System (TPS) is considered the benchmark of efficiency, precision, and continuous improvement. However, this didn’t happen overnight. Decades of refinement went into developing the various processes, including identifying and eliminating waste.
Toyota Chief Engineer Taiichi Ohno initially identified seven wastes. Named muda–a Japanese word meaning futility or uselessness–this methodology became an integral part of the TPS.
Breaking the identification of waste into sub-categories like transport, waiting, and inventory allowed Toyota employees to focus on one area at a time and fully understand how all manufacturing processes each carried wasteful elements.
Once broken down and identified, teams could then get to work eliminating waste in small steps, adding up to significant improvements over time.
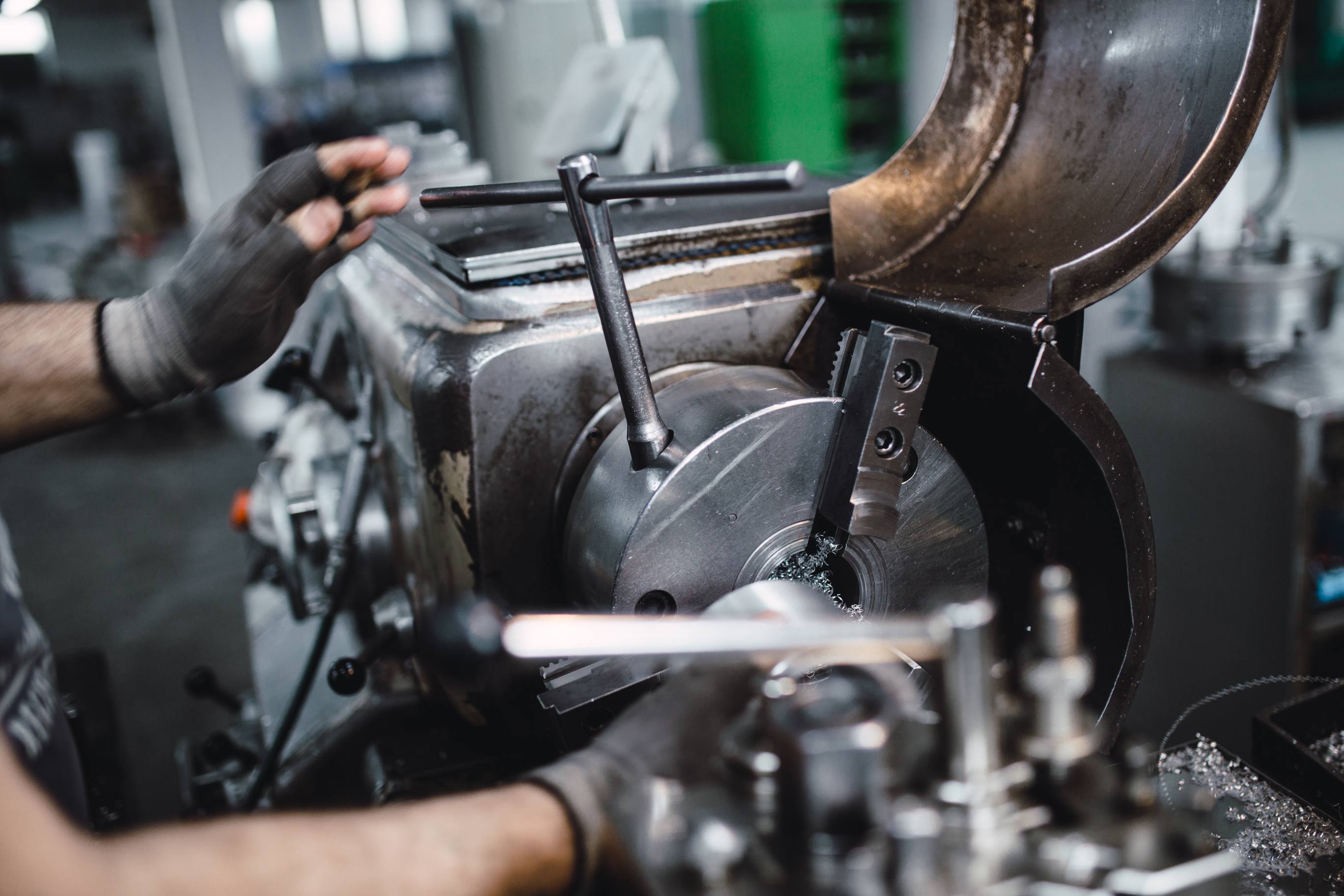
What Is the 8th Waste?
As the Toyota Production System was adopted by manufacturing plants in Western countries, an additional waste–Underutilized Talent–was identified. Although not technically part of the TPS, the 8th waste can have a marked impact on efficiency in your organization.
Training and encouraging employees to perform at their best can be a complex and nuanced task, but when done effectively, it can have an incredible impact on waste reduction.
If your staff is disengaged, overqualified, underqualified, or requires more training, they may unknowingly produce waste. By taking longer than is required, using an unnecessarily complicated process to get things done, or simply feeling underappreciated because they have skills far beyond their current role, having the right people in the right seats is an essential part of TIMWOODS.
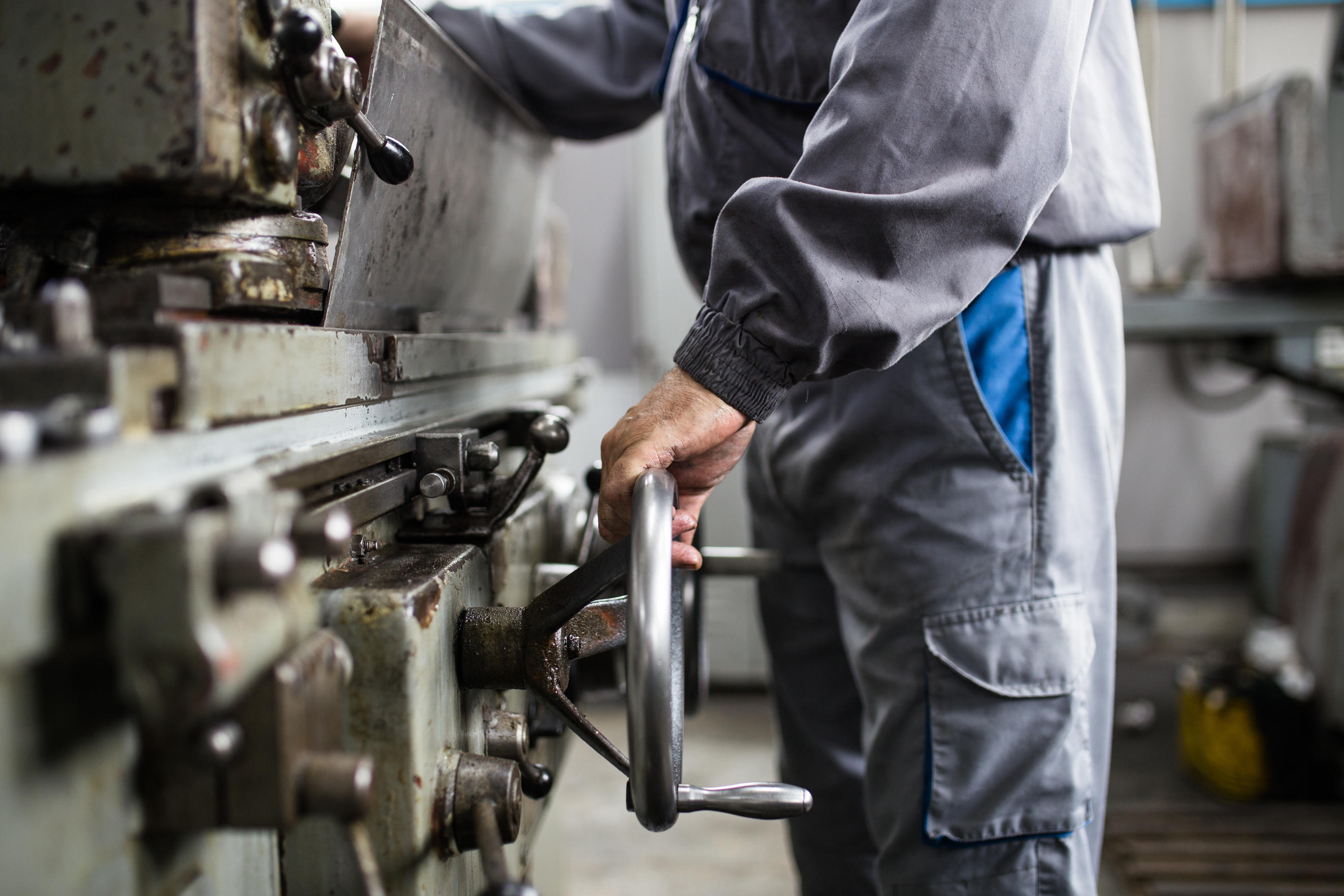
Wait! Who Is Tim Wood?
Tim Wood isn’t a person. Instead, the name is an acronym to help remember the seven wastes. TIMWOOD stands for Transportation, Inventory, Motion, Waiting, Overproduction, and Defects. With the addition of the eighth waste, the acronym became plural, and TIMWOODS worked its way into the lexicon.
Another handy acronym for remembering the eight wastes is DOWNTIME: Defects, Overproduction, Waiting, Non-Utilized Talent, Transportation, Inventory, Motion, and Extra Processing.
The 8 Wastes of Lean Manufacturing Explained
Overproduction
Overproduction relates to manufacturing more than is required. This occurs when work-in-progress (WIP) schedules don’t align with customer demand or production processes are geared towards manufacturing in bulk to save on costs.
While overproducing is effective in some instances, producing a massive volume of items and then needing to store them for 12 months is wasted production.
Take a close look at how much you manufacture each production run to see if this fits with customer consumption habits. Is your inventory way out of sync with your demand?
Over-Processing
Spending additional time or work manufacturing to a higher quality than is required is called over-processing. While creating the world’s highest quality product sounds positive, it’s worth investigating your customer needs in detail to see if this extra processing is noticed, appreciated, or, on the other hand, unnecessary.
Defect Waste
Producing goods that fail to meet standards or customer requirements creates waste. Defects, rework, and returns negatively impact your business.
There are no upsides to producing defective products, so this should be one of the first wastes to eliminate.
Waiting
Set-up times, changing tools or dies, heating up machines, and other similar processes create unnecessary wait time. This downtime between steps in the production process may seem insignificant but can add up, creating wasted time.
Combat this by looking at faster changeover processes and prepping for the next batch while the current batch is still in production. This minimizes waste and reduces your takt time (the rate you need to complete a product to meet customer demand).
Transportation Waste
The Lean Six Sigma approach asks us to map the value stream, identifying each part of the process from product development right through to transport and delivery to the customer.
Unnecessarily moving raw materials or finished goods around results in lost time, energy, and costs, so it is worth focusing on process improvement when it comes to transporting both raw and finished goods.
Inventory Waste
Holding excess raw materials on hand “just in case” can slow your business down and hamper cash flow by tying up funds in excess inventory.
If raw materials aren’t needed for production any time soon, consider how you can rearrange your purchasing and production processes to work in batches or take delivery of materials just in time.
Motion Waste
The unnecessary movement of people creates wasted time and effort. This is evident in impractical workspaces, messy workstations where employees have to hunt for the right tool, and workflow issues where the production floor layout doesn’t make sense, requiring people to walk to the other end of the factory to get things done.
Watch how items are handed off from person to person to eliminate bottlenecks and improve your workflow.
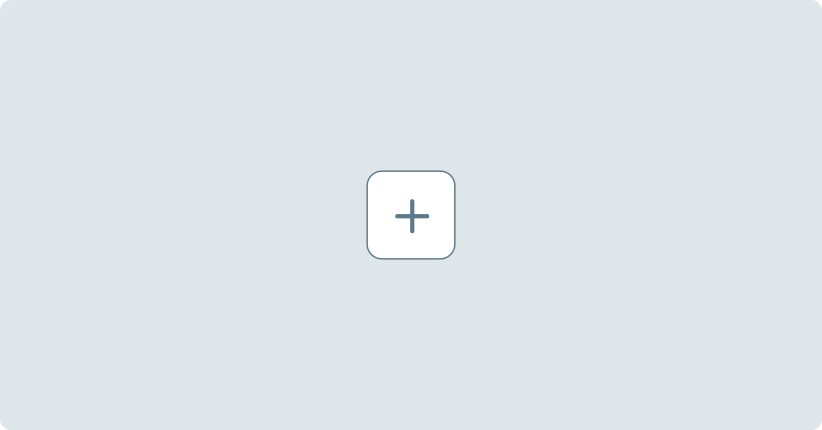
Underutilized Talent
The talent, skills, and knowledge of your workforce are an incredible asset, but if these skills aren’t being put to good use, your business is creating waste.
Both frontline workers and supervisors have their own talents that can propel your business forward, adding value and delivering a level of expertise that makes you highly competitive in the market. The trick is identifying and mapping these skills to ensure the right person is in the proper role to fully utilize the talent at your disposal.Obliterate Waste with MaintainX
Using Kaizen principles to question the current way of doing things is a great way to start identifying and removing the 8 wastes from your business. But going digital to become leaner makes all the sense these days.
MaintainX makes this process easy, allowing you to set up standard operating procedures, templates, and checklists so you can review what’s working and what’s not. In addition, our reporting feature provides real-time accounting of inventory, KPIs, and work orders to keep track of what is working and what is not.
Start eliminating the eight wastes and bring increased efficiency to your business when you create a free MaintainX account today.
FAQs
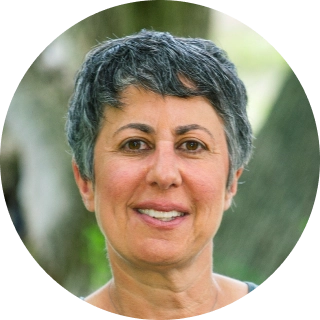
Caroline Eisner is a writer and editor with experience across the profit and nonprofit sectors, government, education, and financial organizations. She has held leadership positions in K16 institutions and has led large-scale digital projects, interactive websites, and a business writing consultancy.